10 ways Volvo Trucks achieving leadership through innovation
By Edit Team | March 1, 2016 12:16 pm SHARE
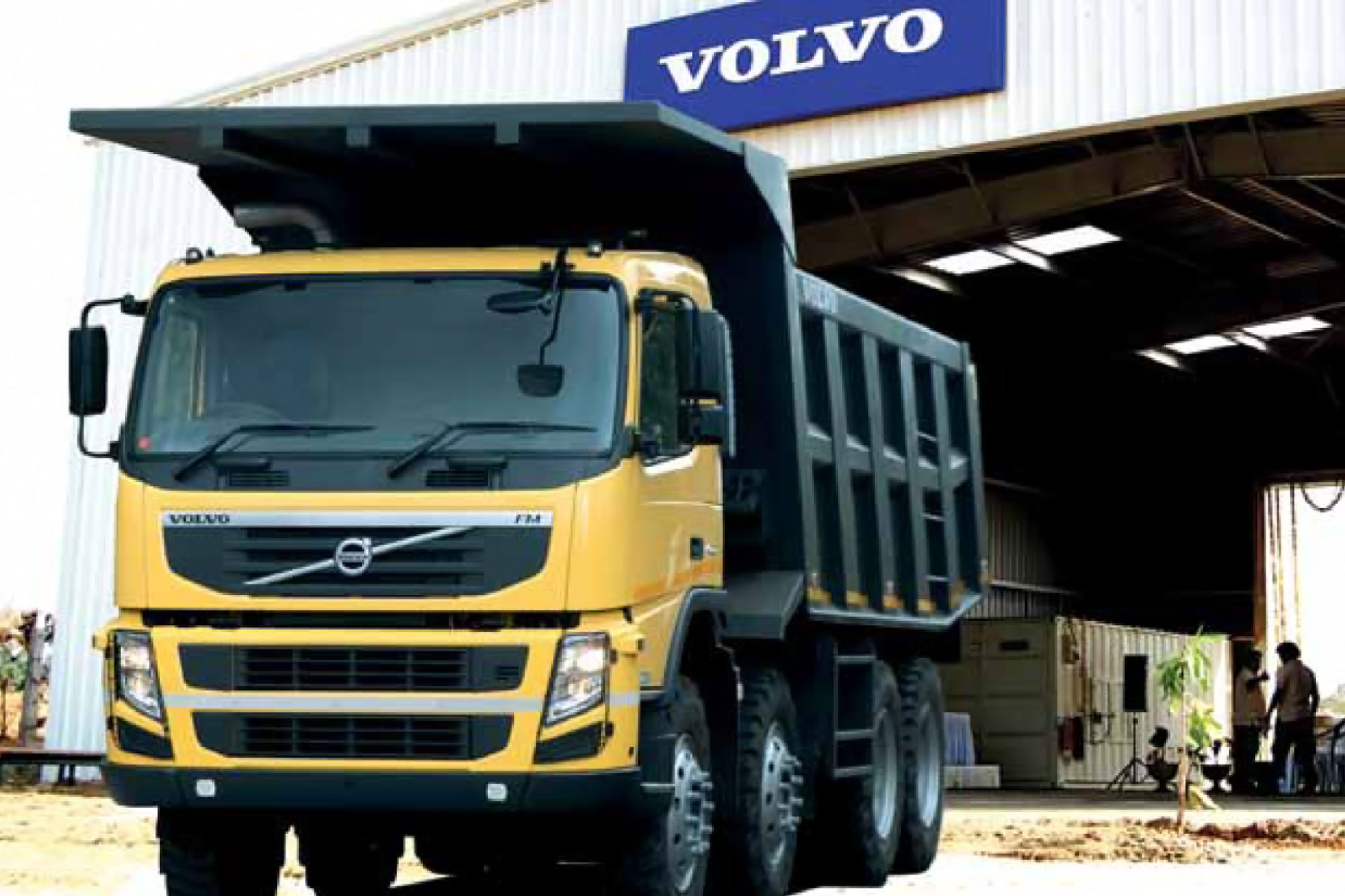
A walk through the journey of Volvo Trucks’ splendid journey in Indian mining transportation market
The year 1997, it was the time when India was changing fast – the economy was surging ahead. The doors opened to global companies to set shop with the next generation technologies, products and solutions for India’s core sectors. With a growing economy, huge domestic market and abundant skilled manpower, the world was focusing on India. Volvo Trucks envisioned the market potential and became the first European truck company to setup a state-of-the-art truck manufacturing plant and make high performance trucks in India for Indian customers. The company embarked on an epic journey in the Indian mining transportation industry.
1. It all started with the 8×4 tipper concept
When Volvo Trucks came to India, the mining transportation industry was using the conventional inefficient 6X4, low capacity tippers, primarily designed for construction work or depended on large, gas guzzling dumpers. They were difficult to operate efficiently in most of the Indian mines with deep coal pits, narrow roads and faraway dump sites. The need of the hour was a mining truck that was flexible, easy and comfortable to operate in Indian mines with bigger capacity, combined with fuel efficiency and a reliable technology to deliver high uptime. The 8X4 tipper concept was just the right solution for India. The Volvo FM7 created a new segment in the industry.
2. Also focused on the drivers
One more significant change that Volvo Trucks brought to the industry was the much needed safe, comfortable and driver friendly cabin that just didn’t exist then. The Volvo tipper cabin was a true revolution for mining trucks. The cabs were tested with Swedish impact tests, the toughest safety norms across the globe. The ergonomic driver seat was designed for long working hours on the uneven roads of the mines. Above all, the high performance air-conditioning system introduced for the first time in India as a standard fitment changed the life of the Indian drivers forever.
3. Innovation that set new benchmarks in uptime
To meet even better performance for higher returns on investments, Volvo introduced the Container Workshop – a complete service solution at the site to reduce the downtime, so that customers could have their trucks rolling when and where they needed. The container workshop came with Volvo trained technicians, complete service infrastructure and ready availability of genuine spare parts and lubricants, to get the trucks back on road in the shortest possible time.
4. Volvo answered the call for competent drivers
As more and more operators made Volvo tippers their choice, there was a huge demand for the drivers who had the competence to use the high performance technologically advanced Volvo tippers and deliver productivity. Anticipating this well ahead of time, Volvo Competence Development Centre was developed. The programs are designed to not only train drivers, but also technicians and fleet managers and help customers create a complete team of well trained manpower to bring in professionalism in operation. Till date, Volvo has trained over 35,000 truck drivers making them better and competent to deliver higher driver productivity with Volvo trucks.
5. FMX platform: The next big step in mining transportation
By 2010 Volvo had established itself as one of the market leaders in mining transportation industry that had fully adapted to the FM series of 8X4 tippers. It was once again time to set the clock for the next innovation. Volvo launched a next generation mining tipper based on the new FMX platform. It was designed with a much stronger chassis, axle, more powerful driveline, powerful brakes, large body and the advanced and safe cabs. FMX set new benchmarks in productivity performance, uptime and efficiency.
By 2012 there were more than 5,000 Volvo tippers delivered in India, a big number in the high performance truck industry.
6. Taking productivity to the next level
The launch of an innovative dump truck built on the first-of-its-kind 10X4 platform with a 5-axle chassis was a unique solution. It integrated the flexibility and fuel efficiency of a tipper with capacity closer to a dump truck and at an attractive price tag. Its large body offered the capacity of 43 tonne. For the customer it was a solution where three dump trucks could now do the work of 5 tippers, making it an economic option for their fleet as well as overall operations.
With FM 10X4 dump truck, Volvo created a new segment in mining trucks. This was followed by two new products for coal transport – the 33 cu.m. coal body tipper for crushed coal and 29 cu.m. coal body tipper for raw coal. Being a customer centric organisation, the aim was to provide a range of technologically advanced solutions to the industry.
7. The next-gen tipper that stretched the limits of performance
Towards the end of 2014, Volvo took a major leap in product design by introducing the advanced FMX mining tipper built on the new global technology platform, optimised further for tough and hilly terrains of Indian mining operations. They came with features that made a world of difference to mining trucks, with even bigger body capacity for higher productivity and improved cabin for better driver productivity.
8. The choice of manual and I-Shift
The challenge of getting that extra distance with every drop of fuel was answered with I-Shift for mining. An automated transmission system specially configured and optimised for mining applications. Now customer’s had the choice of both manual and I-Shift transmission on FMX tippers.
9. Smart information solution for smarter operations
Along with hard products, came yet another innovation called Dynafleet Online, a telematic system gateway developed to improve fleet management through real time data analysis of vehicles and drivers to make the right and wise decisions for improving operational efficiency. It’s a solution that takes advantage of the intelligent electronic architecture of a truck and allows the access of information through the internet to generate smart reports on performance.
10. The widest range of mining transport solutions
At EXCON 2015, Volvo Trucks introduced three innovative solutions based on the new FMX platform – FMX 520 26.1 cu.m. Dump Truck, FMX 480 24 cu.m. Dump Truck, and FMX 440 33 cu.m. Coal Tipper. Both the dump trucks and the tipper feature the new FMX cabin. While 24 cu.m. dump truck is built on a chassis with a pusher axle, the 26.1 cu.m. dump truck is built on a 10X4 chassis with a tag axle. This offers much more flexibility while carrying larger loads in mines with fuel efficiency far better compared to conventional dumpers currently available.
Volvo’s approach to leadership through innovation has resulted in the widest range of mining transport solution from a single source. Today, it offers the FMX 440 19.5 cu.m. tipper with the choice of manual and I-Shift transmission, FMX 440 33 cu.m. coal tipper and FMX 24 cu.m. and 26.1 cu.m. dump trucks.
Volvo has so far delivered over 7,500 tippers of which over 5,000 are currently operational. It has also trained over 35,000 truck drivers. Some of its tippers have clocked over 50,000 hours of operation.
Cookie Consent
We use cookies to personalize your experience. By continuing to visit this website you agree to our Terms & Conditions, Privacy Policy and Cookie Policy.