5 steps to select right roofing materials for warehouse
By Edit Team | May 28, 2014 9:22 am SHARE
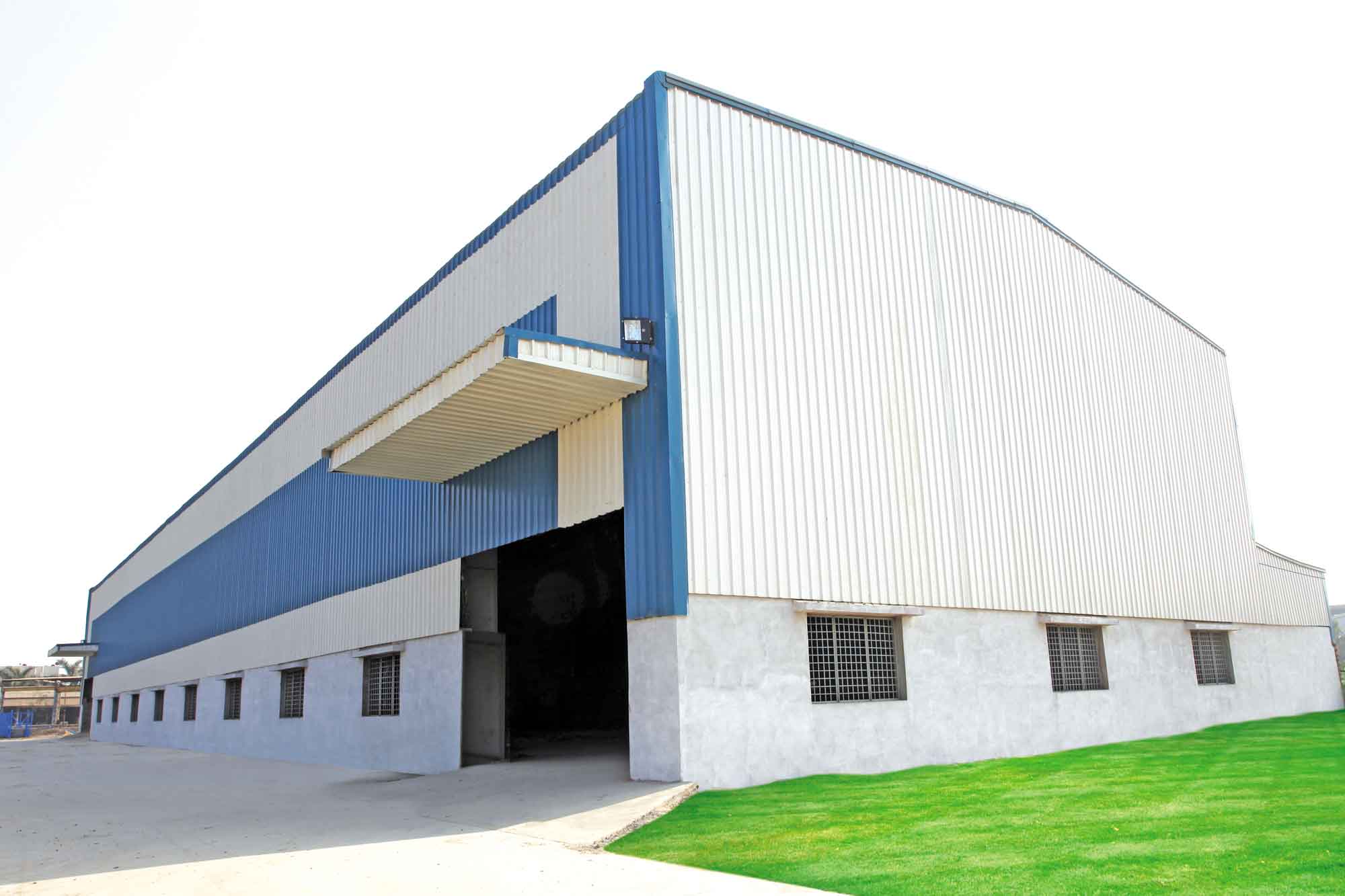
Selecting the right roofing material for warehouse application is an important task to perform before making a decision on investment. Any deviation in product specification may lead to paying a high cost on building maintenance or for early replacement of products. This article summarises the key parameters one must consider before procuring roofing materials.
Warehouse buildings are made by either conventional method or pre-engineered steel building method (modern technology). In both cases steel roofing and wall cladding arepreferred over the conventional cement or asbestos roofing sheets. This is because asbestos sheeting may cause health issues, it radiates more heat inside the building, water leakage could occur from sheet joining and hook locations, high maintenance cost on replacement of damaged sheets, high cost on steel structure and its heavy foundation cost.
The metal roofing or wall cladding is one of the principle building components that act like an envelope. They help to transfer the load to secondary member, restraining the secondarysteelwork and also provide thermal as well as acoustic insulation. Considering all these parameters, the building designer or specifier understand the cladding material for its steelproperties (thickness and grade), type of corrosion resistance metallic coating, its coating mass, type of paint system and its performance, shape of profile and its wind load capability, its water tightness. Section of right material would help to get increased building life, low maintenance, thermal comfort on heat and cold, flexibility on design and aesthetics that last longer.
To have proper understanding of material, the following steps can be followed while drafting the product specification for any project. These steps may help protect your company’s position in the market and end-client will have 100 per cent satisfaction. Any deviation in product specification may lead to paying a high cost on building maintenance or for early replacement of products. In each stage, a recommendation has been given on right product specifications:
Step 1: Base steel selection
Steel determines the strength of the roofing and for various roof curves, steel of different yield strength is required. Available yield strength includes min 550 MPa, min 340MPa/ 300 MPa and 250 MPa. Steel thickness should be selected as per design requirements. High strength (G550) steel – 0.42 mm BMT to 0.45 mm BMT. G340/G300 – 0.50 mm BMT to 1.4 mm. G250 grade – 0.60 mm to 0.80 mm BMT
Recommended thickness and grade for roofing and walling: 0.45 mm BMT Trapezoidal or concealed clip fixed profile typically for straight plane roofs (minimal curvature allowed subject to profile shape) recommended grade is G550. For concave or convex shapes use standing seam type profile, recommended grade is G300 material in 0.55 mm BMT – 0.60 mm BMT. Truss-less seam profile roofing, recommended thickness (subjected to design criteria) is 0.80- 1.4 mm BMT G340/ G300.
Step 2: Corrosion resistant coating selection
The corrosion resistance is maximised using critical coating composition.
• Galvanised coating is available in the market with Z275, Z180, Z120, Z90 as per IS 277. Z275 =275 g/m2 coating mass on both side should be alright for building construction typically for secondary structural i.e. purlin and structural decking and cold room applications in case of sandwich panels.
• 55 per cent aluminium-zinc alloy coating (55 per cent Al, 43.5 per cent Zn, 1.5 per cent Si) is invented by BIEC International Inc., a BlueScope Steel subsidiary. Products available in market with AZ150 and AZ200 as per IS 15961/ AS1397. AZ150 =150 g/m2 coating mass on both side is best suited for roofing and walling application as its life is upto four times more than Z275 galvanised steel in similar environmental conditions. Since 1993, the ZINCALUME brand has been imported from BlueScope steel mills and since 2011 it is being produced in India by Tata BlueScope steel. ZINCALUME steel has separate passivation layer and acrylic resin coating on surface for better thermal reflectivity and has anti-darkening property over other products.
Recommended metallic coating for roofing and walling: ZINCALUME AZ150 for general applications. AZ200 is recommended for harsh conditions (marine, air with high pollution levels etc.). Products comply with AS 1397/ ASTM A792M / IS15961.
Step 3: paint system selection
The paint system is to be selected according to its application (internal/ external exposure conditions) and aesthetic requirements.
Generally available paint systems are:
Resin system: Durable polyester for exterior applications type 4 (COLORBOND XRW, ULTRA) for durability and aesthetic property, Polyvinyl-di-fluoride (PVdF) with minimum 70 percent, Kynar+30 per cent Acrylic (COLORBOND XPD) type 3 category where colour retention is important. Silicon modified polyester (SMP-min 30-50 per cent Si content) is not preferred due to high film hardness and its lower flexibility. Regular modified polyester– type 2 category i.e. basic resin only suitable for internal applications.
Pigment type: Inorganic (naturally occurring) v/s organic (synthetic) and its composition percentage. Organic pigments deteriorate quickly when exposed to UV giving a patchy overallappearance. Cost-effective pigments. Hence it’s only recommended for internal application.100 per cent inorganic pigments have very high colour fading resistance used for exteriorapplication as it exposed to UV radiations. Mica /Metal flakes used in paint system for metallic appearance. Lead pigments are carcinogenic hence it’s not recommended in any paint system.
Selection of colour: Very dark and bright colours fade fast and allow more heat radiated inside the building. Always go with standard earthy colours that will keep the building newer for longer.
Gloss: For exterior application. It is always recommended to use semi-gloss paint system for exterior application.
Thermal performance: Recently innovation has been done in paint system, paint systems also provide thermal comfort (heat reflectivity due to Thermatech technology introduced inCOLORBOND steel paint system). It helps reduce temperature by 6 C (average), and enables 15 per cent lower electricity consumption per annum.
Product complying standards: AS/NZS 2728 type 3-4 type or IS15965 – class 3 for exterior roofing and walling application for buildings.
Water harvesting: Paint system used for cladding should not have heavy metal in coating such as lead.
Green product: Cladding products should comply with Green building criteria (100 per cent recycle, reusable, optimum usage of steel, high reflectivity (SRI value >78 in low slope and SRI value >29 in steep slope building), long-life.
Recommended paint system for roofing and walling: COLORBOND XRW (super durable polyester) is a complete system developed for exterior durability and long-term aesthetics forgeneral applications. COLORBOND ultra steel is developed for harsh environmental conditions.
Step 4: Sheet profile selection
In the market various types of profile shapes are available and selection of right shape is critical. It is suggested that the profile shape and its design criteria on serviceability andstrength is checked when selecting the profile.
Recommended: Suggest to always go for a reputed manufacturer who can provide profile wind pressure table data and also provide technical or detailing support.
Step 5: Fastener selection
The performance of the fasteners used must have the same or superior service life than the roof and wall cladding material and shall comply with Australian Standard 3566 class 3 or class 4. The washers containing significant levels of conductive carbon black fillers are not suitable for use with Tata BlueScope products.
Conclusion
In continuation of product selection, the design and structural details of a building are critical factors that determine its expected service life. A better understanding of the design issuesincluding roof slope, sheet laps, crevices, fastening techniques and the areas conducive to the build-up of dirt or contaminations, are to be addressed appropriately. The areas with build-up of dirt or contaminations need cleaning at regular intervals. It is to be noted that the components must be free of any ponding issue and there are least numbers of crevices. It is because accumulation of water at these locations for long periods is not good for coated steel components. Maintenance is a very important factor in getting the maximum life and cleaning by water hose is good enough.
Different environments affect the life of coated steel differently. Therefore, selection of coated steel material would require an understanding of the external and internal environment to which it is going to be subjected to. Particular attention must be paid to coastal, aggressive industrial situations and intensive farming applications. To get maximum life, the important factor is selection of the appropriate coated steel at the specification stage of the building. The new Indian standards will facilitate more uses of high corrosion resistant coated steel in buildings,
with a view to provide long life and aesthetic durability.
Authored by__
Mahendra Pingle
Dy. General Manager – Market Development
Tata BlueScope Steel Ltd.
Cookie Consent
We use cookies to personalize your experience. By continuing to visit this website you agree to our Terms & Conditions, Privacy Policy and Cookie Policy.