How to achieve cost-effectivecrushing & screening
By Edit Team | April 14, 2018 6:39 am SHARE
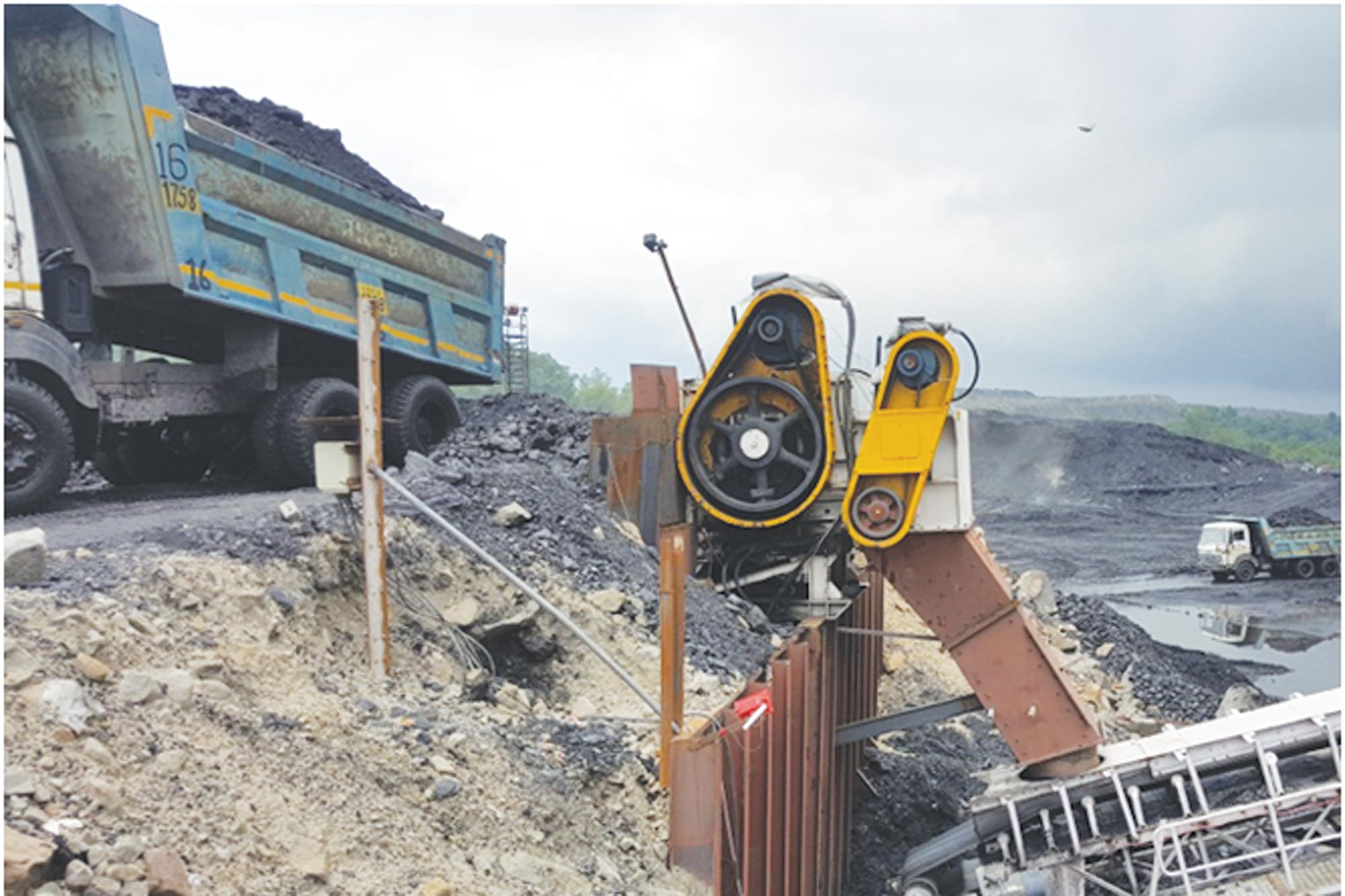
Buoyed by the growing demand of aggregates for infrastructure projects, the demand for crushing and screening equipment is witnessing tremendous growth in India. However, in this competitive age, it is essential to have proper strategies in place apart from having high-efficient machines to achieve best value for money in crushing and screening operations. Here, we present you some of the key points to consider in achieving cost-effective crushing and screening.
Analyse the problem areas
Ajay Varma, Director, Marsman India Ltd said, “Detailed analysis of the problems should be discussed with customers before finalising the machinery. Fuel cost and tyre wear of dumpers and loaders are the most important factors in crushing industry and cannot be overlooked. Transport cost should be accountable to check the feasibility of fuel cost.”
Right synchronisation of equipment is essential
Varma of Marsman adds, “Right synchronisation of crusher, feeder, vibrating screen and conveyors is an important factor in achieving cost effectiveness. One cannot expect a low capacity feeder to sync well high output crusher or similarly lower carrying capacity of conveyor belt will harm the viability of the project. Likewise, a 1,000 mm conveyor will be an overkill for a crusher with capacity of only 150 TPH.”
Marsman’s crushing and screening equipment produce high productivity at low power, claims Varma. He adds, “We offer crushers with low capacity motors still delivering desired production capacity thereby reducing electricity costs. Also, we provide tailor-made solutions to customers to suit their requirement while also suggesting various ways to lower their cost of production.”
Wear and tear is again involved a major cost and Marsman’s service team makes sure that all customers are kept up-to-date regarding the service of their crushing plant. The company has ready stock inventory of spares which are deployed at once wherever there is a requirement from customer. “Our jaw plates are a mix of manganese & chromium which lasts long and offer high output capacity while producing supreme quality stone,” claims Varma.
Maximise utility
Utility is a common denominator to solutions aimed at enhancing cost-efficiency, avers Piero Guizzetti, CEO, MB India. He adds, “We offer products that have an application spectrum that goes from optimal solution for primary crushing at the quarry to at site crushing for road construction.”
MB Crusher is one the pioneers in manufacturing crushing and screening buckets. MB has 12 models of crusher and 7 models of screening buckets in its range, catering to virtually every possible earthmoving machine, besides other products like drum cutter and grapple bucket. MB India subsidiary has supplied crusher and screening buckets in various parts of India among road, quarry and demolition sectors.
MB Crusher bucket is powered by the hydraulic plant of excavators and loaders; can crush aggregates to various sizes typically for GSB at the site itself. Such on-site crushing, saves the road contractor transportation cost of crushed material and multiple handing of raw or crusher material at the source quarry. Hence, according to Piero, “Compared to traditional crushing of similar capacity, cost of production or procurement of GSB by a road contractor is reduced by manifold with MB buckets.”
As a quarry owner, MB crusher bucket can be used as a primary crusher to produce optimum feed size for the secondary crusher plant. This process eliminates dependency on costly manual labour at the quarry and frequent bearing breakdown of secondary crusher plant due to over-sized feed material.
MB Screening bucket with its options of various mesh size may be used in large quarry to recycle the waste material or over burden material. Screened out material may be sold as GSB to road contractors and rest of the material can be processed at their crusher plant. It also creates additional space inside the quarry for further mining operation. This adds to the profit of the quarry operation with minimal investment.
Adhere to basic parameters
To achieve cost-effective crushing and screening, according to V. Venkataramana, Vice President – Marketing, Puzzolana Machinery Fabricators (Hyderabad), some of the basic parameters to be considered including:
• Aggregate requirement and time period of the project.
• Availability of quarrying and aggregates decides the type of plant, mobile/skid/stationary, capacity of plant 200/300/450/600 TPH etc.
• Number of stages i.e. 2- or 3-stage plants. If sand requirement is there, then 4-stage plant should be considered with sander. (Jaw + Cone + VSI + Sander) for concrete sand and plaster sand.
• Cost-effective or quality sand and (green) protective solutions in classification for both dry and wet classification through:
u Through improved design and materials of wear parts.
u Better utilisation of connected load (power).
u Reduce the re-crushing in each stage and add another stage.
u Ensure that minimum wastage of crushed material.
• To ensure cost effective production
u Through improved design and materials of wear parts.
u Better utilisation of connected load (power).
u Reduce the re-crushing in each stage and add another stage.
u Ensure that minimum wastage of crushed material.
• Ensure a continuous improvement in the design of equipment and add higher capacity machines to ensure production of 450 or 600 TPH capacity plants through 3- or 4-stage plants.
Ensure availability of equipment
“To achieve cost-effective crushing and screening production, the most important point is the availability of the equipment for production since many supporting equipment also become idle once the crusher is not available,” said Viraj Parthi, Country Manager, Terex India Pvt Ltd.
Terex Finlay offers reversible operation of jaw moving plate for clearing blockages, fully hydraulically adjustable closed side setting, advanced PLC for ease in control during operation and diagnosis of problems during downtime. The cone crusher comes with unique feature of metal purge system which helps in removing the metal contaminants from belt very quickly. These feature helps in improving the availability of the plant.
Another important feature of Terex Finlay Cone crusher C1540 which helps in cost effective production is the option for pre-screen on cone crusher. According to Parthi, this gives 10-20 per cent extra production without any extra operating cost. He further observes, “The feeding arrangement for the crusher i.e. the size of excavator is also a major factor in achieving cost-effective production.”
Skill level of operators
Parthi further adds, “The most important factor that plays very vital role in cost effective production is the skill level of operator team. And that is the reason, Terex Finlay puts a lot of emphasis on operator training as getting a trained manpower is a big issue for all the crushing plant owners. We arrange trainings at site as well as in our Hosur factory round the year free of cost.”
Onkar Sapre, Country Head – Sales & Marketing, Taurian Engineering compiled some of the steps to be followed in achieving cost effective crushing and screening as:
Proper sizing of boulders: User needs to put boulders of proper size in the primary crusher, oversize boulders get stuck and cause hindrance. User needs to take them out manually which causes time loss, energy loss and production loss all at the same time.
Proper maintenance: User must have proper scheduled maintenance carried out judiciously at his crushing plant. Negligence in the same would cause unexpected breakdowns and under-utilisation of the crushers. Also, improper maintenance leads to reduced life of the equipment and early breakdowns.
Operation: It is imperative for cost effective crushing and screening that the user has well-trained operator who understand the limits of the equipment to optimise them during operation.
Uninterrupted power supply: For a crusher to run freely at an optimised capacity it is important to have uninterrupted power supply so the cycle of crushing is not frequently broken.
Parts stocking: For maximum utilisation of crusher, it is important that the user stocks some critical or frequently used wear and spare parts at the site to reduce the downtime of the crusher.
Mining planning: The most important aspect to achieve cost effective crushing and screening is having proper planning of mining activity. If the user has managed his feed, then there won’t be intermittent losses in capacity due to non-availability of feed. If the feed is not regular, then it is important for the user to use stockpile so that the intermittent feed issue can be tackled.
Selection of correct equipment: It is important for the user to use the correct combination of equipment for the application.
Hazemag has been offering advanced crushing solutions
Hazemag has been offering advanced crushing solutions over the years. The German engineered products have been successfully crushing from 250 TPH to 2,000 TPH in different mines and/or plants across the globe.
HAZEMAG designed machines are features around the following perquisites:
Further, to handle higher output demand, Hazemag provides a combination of chain conveyor, roller screen and crusher to increase the capacity of the new circuit to almost double, claims Sandipan Majumdar, Sr. Manager- Marketing, Hazemag India.
Utility is a common denominator to solutions aimed at enhancing cost-efficiency.
Piero Guizzetti, CEO, MB Crusher India
Ensure a continuous improvement in the design of equipment and add higher capacity machines to ensure production of 450 or 600 TPH capacity plants through 3- or 4-stage plant.
V. Venkataramana,Vice President – Marketing, Puzzolana Machinery Fabricators (Hyderabad) LLP
Most important point is the availability of the equipment for production since many supporting equipment also become idle once the crusher is not available.
Viraj Parthi, Country Manager,Terex India Pvt Ltd
The most important aspect to achieve cost effective crushing and screening is having proper planning of mining activity.
Onkar Sapre, Country Head – Sales and Marketing, Taurian Engineering Pvt Ltd.
Hazemag provides a combination of chain conveyor, roller screen and crusher to increase the capacity of the new circuit to almost double.
Sandipan Majumdar, Sr. Manager- Marketing, Hazemag India
Cookie Consent
We use cookies to personalize your experience. By continuing to visit this website you agree to our Terms & Conditions, Privacy Policy and Cookie Policy.