Construction industry is adopting integration of embedded sensors
By Edit Team | May 8, 2021 5:54 pm SHARE
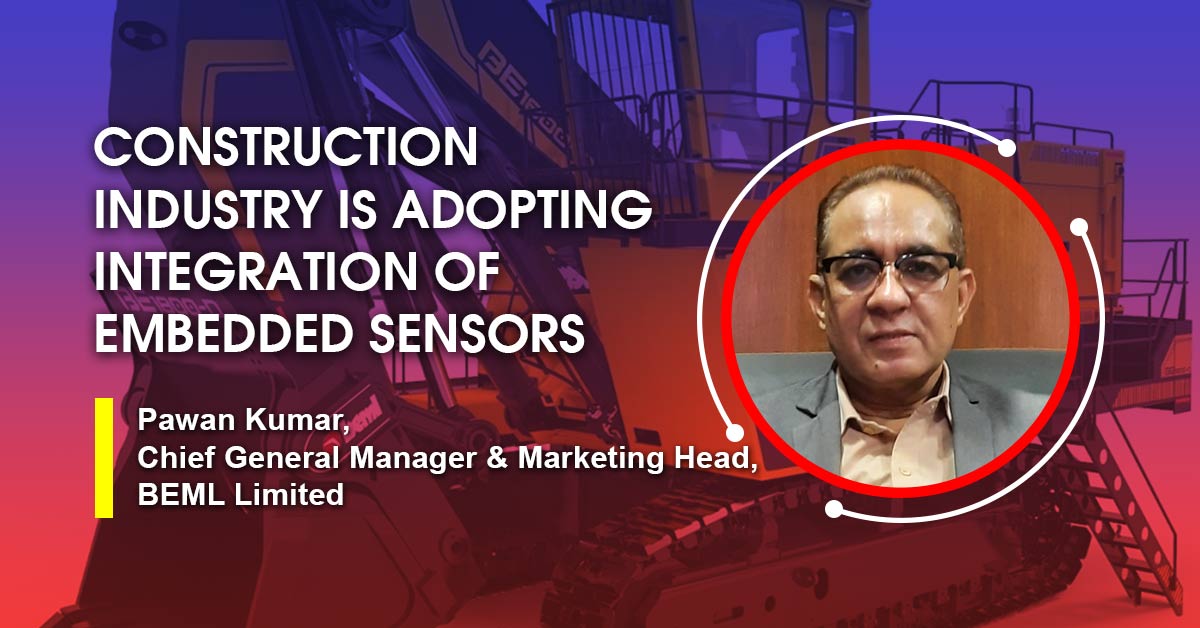
Proper timely maintenance of construction equipment will enhance the life of the sub-assemblies which reduces the operating cost of equipment, says Pawan Kumar, Chief General Manager & Marketing Head, BEML Limited.
How does maintenance play an important role in construction equipment?
Most of the construction equipment maintenance that happens today is reactive, machines are only repaired or checked if they break down or seem to be on the verge of breaking down. So, an optimised maintenance system needs to be maintained to allow planned and predictive maintenance to avoid downtime, delays, and incidents that ultimately lead to significant financial losses. Proper maintenance of machines is the first step to attaining that goal.
Preventive maintenance is the regular and routine maintenance of equipment and assets to keep them running and prevent any costly unplanned downtime from unexpected equipment failure. Proper timely maintenance of construction equipment will enhance the life of the sub-assemblies which reduces the operating cost of equipment.
What are the maintenance practices followed for the upkeep of construction equipment?
The following maintenance practices are generally adopted for the upkeep of construction equipment:
• Periodic maintenance as per manufacturer’s recommendations.
• Reactive maintenance based on trouble and breakdown.
• Preventive maintenance based on analysis and finding during periodical maintenance.
• Predictive maintenance based on previous experience and data to reduce breakdowns and cost.
How is predictive maintenance gaining importance in construction equipment and plants?
The nature of component failure in any construction equipment varies from project to project based on application and operating conditions. Based on the manufacturer’s recommendations for various types of application, past data, vibrations, oil analysis etc., will give the indication, and timely predictive action will reduce the major failures and overall cost of operations.
With predictive maintenance, the expected time of failure of critical aggregates and components can be reasonably estimated well in advance. This helps in obtaining such items just in-time. This helps in reduced inventory costs and ensuring timely availability of such critical long-lead items, thereby minimising equipment breakdown hours.
What is the role of digital technology in plant/equipment operation and maintenance?
The advanced digital technologies allow equipment operators and owners to work more productively, efficiently and safely. Owners and operators can save money by decreasing downtime and maintenance costs and via data to make better decisions when it comes to equipment operation and project management.
The construction industry is now adopting the practice of integrating embedded sensors in physical assets. These sensors are internet-enabled and with the current state of IoT, they can capture considerable volumes of data, analyse it, and communicate with other machines. These sensors greatly improve the anticipation of failures by generating alerts when a potential problem is noticed.
BEML has adopted the latest digital technologies towards effective operation and maintenance of equipment; which include:
• Operator fatigue monitoring system
• Warning system for critical parameters monitoring of major aggregates
• Rearview camera
• Automatic transmission, auto lube and auto fire suppression system
• Telematics which allows for remote monitoring and remote machine diagnostics
What is the importance of skill development in machine operation and maintenance? How will this help improve the machine uptime?
Skilled operators will improve the productivity of the equipment, take care of the safety of equipment and inform the maintenance crew well in time regarding abnormality in operation, if any. Further, following benefits are envisaged through skill upgradation.
• Skilled operators will operate the equipment in the recommended manner, thereby minimising fuel consumption and component wear and failure.
• Proper operation will enhance productivity and hence the ROI.
• Proper operation will ensure the safety of the personnel and machines and other property in and around the equipment in addition to the safety of the operator and the equipment he is operating.
Skilled maintenance staff adopts the proper maintenance practices and minimise equipment failures; which in turn increase the availability of equipment and reduce the overall operating cost of equipment. BEML’s factory-trained service teams are posted all over the country, who in turn are training the customer operators and maintenance staff.
BEML is also providing product-wise training at manufacturing plants to operators and maintenance staff of customers. To develop the skill of operators, BEML has adopted the latest simulator-based training technology, both at the selected project and at the manufacturing plant.
What are the challenges faced in equipment maintenance? What are the measures needed for better maintenance practices?
Challenges faced in equipment maintenance:
• Adverse weather conditions – Dusty environment, high temperature, cold conditions, windy, heavy rain and poor visibility. This will affect timely preventive maintenance action in avoiding failures.
• Some of the construction equipment are deployed in remote areas where the approach is difficult and lack maintenance facilities.
• One of the biggest challenges in maintenance is an advanced prediction of failures of critical and long lead items.
BEML has 12 regional offices, 15 district offices, six activity centres and five service centres spread across the country; to provide total product support to customers. Further, the company has deployed service engineers at pit heads to monitor the equipment closely.
Measures needed for better maintenance practices:
• Strictly adherence to maintenance schedules prescribed by Original Equipment Manufacturers (OEMs)
• To impart training to the maintenance staff of customers
• Spontaneous corrective action for the signals/indications given by the warning alarms
• To adopt GPS-based preventive maintenance solutions
• Smart wear to guide technician with step-by-step instructions during repair work
• Adopting AI-based predictive maintenance tool
BEML is offering maintenance contracts, recon exchange of aggregates, rehabilitation of used equipment, technical audit, upgradation of equipment, service centre repair facility and condition-based monitoring system; as overall product support to improve the availability of equipment increase productivity and reduce the operating cost.
Cookie Consent
We use cookies to personalize your experience. By continuing to visit this website you agree to our Terms & Conditions, Privacy Policy and Cookie Policy.