Nanotechnology – versatile tool to enhance the paint coating properties
By Edit Team | January 15, 2022 5:47 pm SHARE
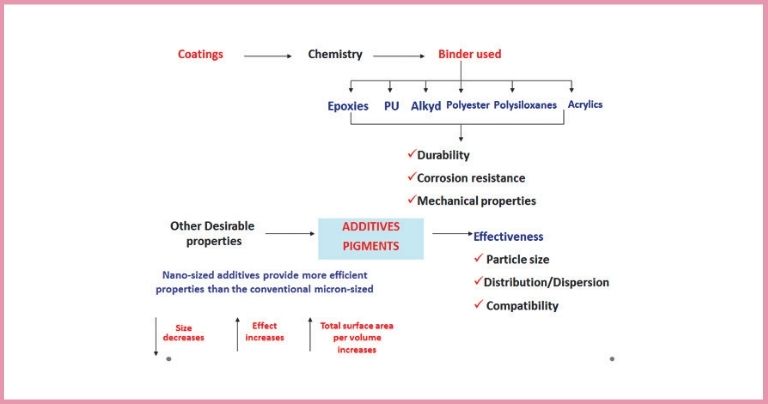
One can formulate a smart, protective and high-performance functional coating using a variety of nano additives and pigments.
Paints and coatings are being considered as an essential requirement in our daily life, since the first cave painting carried out around 40000 years ago. Since then, this field has been developed quite broadly, covering a range of applications like decoration, protection against corrosion and abrasion, fire retardant, anti-fungal and microbial, water repellent and so on. Modern applications demand coatings with additional functional properties. This has led to innovative technologies in the field of surface modification, nanocomposites, smart coatings etc. However, there are still certain areas in paints and coatings which need additional focus. For example, photo degradation due to the sun, the presence of micro defects, and damage due to abrasion can lead to localised corrosion of the metal components which is more dangerous than the uniform corrosion. Hence, the coating should have good corrosion protection and mechanical properties such as adequate strength, resistance to impact wear and abrasion and must be able to resist weathering and must have low water permeability. Addition of pigments, extenders, fillers and additives, generally used in conventional paint coatings has a size in the range of 50-200 µm. But loading levels for these micro sized pigments is rather high i.e. from 10 to 30 vol. % w.r.t to coating volume. Also, the micro sized pigments always bring side effects like reduction in flexibility, adhesion, unwanted changes in optical properties etc. Improvement of one functional property occurs at the compensation of the other. For example, improvement of mar resistance occurs at the cost of weathering resistance and flexibility. One of the effective ways to face these challenges is to use nano size pigments. Due to the large surface area of nano particles, the amount of pigment requirement is very low. Thus, one can formulate a smart, protective and high performance functional coating using a variety of nano additives and pigments.
Application of nano particles for paints & coatings
Nano-particles are engineered structures at nano scale whose size ranges between 1 to 100 nm at least in one direction. These are used in coatings as filler materials, opacifiers and semiconductors. Nano technology has led to break through advancements in coating industries because nano-materials have the potential to overcome several challenges faced by the coating industries.
With relevance to the coating industries, nano-particles have shown significant potential for much stronger, tougher and durable coatings. They offer unique contributions when dispersed in coatings. For example, they can be used for formulating functional smart coatings like Super hydrophobicity, anti-icing, anti-fogging, antireflective, anti-fouling, self-healing, anti-bacterial, anticorrosion and corrosion detecting, anti-graffiti etc., These unique properties are the outcome of outstanding aspect ratio, excellent surface interaction and high modulus. Numerous papers have been published on the enhancement of performance properties of polymer coatings by the addition of nano-materials. Due to the high surface area of the particles, even a small amount of addition can bring a big change in the performance of the coating. One can create magic using nano technology in the field of coatings. This needs an understanding of material selection, size effect and importance of morphology of the nano-particles. Also, the processing of polymernano composite is critical. If the synthesis process is not proper, we may end up with agglomerates in the coatings which is undesirable. Perfect distribution of nano-particles in the polymer matrix reflects the best possible outcomes. This problem can be overcome by using dispersing agents and methods like ultra-sonication or functionalisation with silanes and fluoro-compounds.
Among all the pigments, nano inorganic materials are considered to be most advanced to improve mechanical and performance properties. Nano TiO2, ZnO, (silica) SiO2, (alumina) Al2O3, carbon black etc., are commonly used for serving different purposes. Each kind can perform more than one function. For example, nano ZnO can be used as UV blocker but it can also improve the scratch and abrasion resistance. Hence, classification of nano-particles based on function is difficult.
Distribution of nano particles in coatings
Figure 1, summarises the effect of nano particles on the performance of coatings. The first selection criteria of coating is the chemistry of resin, which helps us to choose macro or bulk properties such as durability, strength etc. However, several micro-level properties are modified by pigments and additives. Here the size and shape and its loading is the main factor. If we go on size factor alone, then it is observed that smaller the size of pigments and/or additives more is its effect on the performance of coatings.
The dispersion of nano-particles in the coating matrix reflects its final properties. Hence optimisation of the synthesis method plays a major role. Due to the high surface energy of nano particles, they tend to agglomerate. As per continuum theory, the effect of each nano-particle distributed in coating matrix has its range of influence. In case nano-particle is overcrowded or non-uniformly distributed, the range of influence gets disturbed and the optimum property will be lost as shown in the figure 2. This is called continuum theory which explains, proper distribution where the effect of one neon-particle is taken over by the other is the best distribution. At lower level of loading it will not be possible and at higher level, agglomeration will occur. The acceptable distribution of nano-particles is therefore as given in 2(a).
Effect of size, shape and concentration of nano particles on the coatings
Second important factor required in making a nano-composite coating is proper selection of size and shape of nano particle. Fig. 3 and 4 show the SEM images and corresponding DLS data of spherical and rod shaped iron oxide nano particles, respectively. The average size of spherical Fe2O3 is 75nm and rod shaped particles is 180nm. The aspect ratio of rod shaped iron oxide is 18.
Now let us look how the mechanical properties such as tensile stress and modulus of bare epoxy and nano Fe2O3 modified epoxy, as presented in the figure 5. The tensile strength of the coatings increased with the addition of nano spherical and rod shaped Fe2O3 particles. The rod shaped particles showed significant improvement in the tensile strength compared to the spherical particles. The tensile strength increased with the increase in the concentration of nano-particles. For, the rod shaped nano-particles, the tensile strength decreased after an optimum concentration i.e. 1 W% due to aggregation. The most likely mechanism involved in toughening by nano-particles is plastic void growth and particle debonding. Since, the aspect ratio of rod shaped particles is very high, the energy required for debonding is more. Hence, the tensile strength offered by the rod shaped particles is more pronounced. There is a lack of literature on the behaviour of epoxy based coatings modified with various shapes of Fe2O3particles. But the results obtained are in a similar trend to that of the data published on epoxy modified with other nano particles.
Tabor abrasion index of nano Fe2O3 modified epoxy coatings
Figure 5 shows the tabor abrasion index of epoxy coatings modified with spherical and rod shaped Fe2O3 nanoparticles at various concentrations. There is a significant increase in the abrasion resistance with addition of these particles in the coating. The size, shape, distribution of nanoparticles in the coating, hardness of the nano particles, and compatibility of nanoparticles with the matrix affects the abrasion resistance of the coating. At 1 W % loading, the values start to become constant. The nano particles start to agglomerate at this point and a further increase in the concentration of nano particles will lead to detrimental effects.
Effect of Iron Oxide on UV weathering epoxy coatings
The percentage loss in gloss and yellowing index of the coatings exposed to UV A radiation are presented in figure 7 and 8 respectively. The percentage improvement factor for spherical and rod shaped Fe2O3 at various levels of loading is presented in table 2. The results clearly show that modification of epoxy with iron(III) oxide shows reduction in gloss loss and yellowing. The coating with 1 W% Rod shaped Fe2O3 Showed maximum resistance to UV degradation. For both shapes of particles, 1 W% concentration was the optimum concentration The decrease in the UV resistance with further increase in concentration of nano particles can be due to agglomeration. Fe2O3 is reported to scavenge OH˙ radicals. Fe3+ ions, when exposed to UV light in presence of OH radicals reduces to Fe2+. This Fe2+ ion is unstable. It gets oxidises back to Fe3+. By this cyclic reductionoxidation process, the iron oxide particles stay stable while scavenging OH radicals.
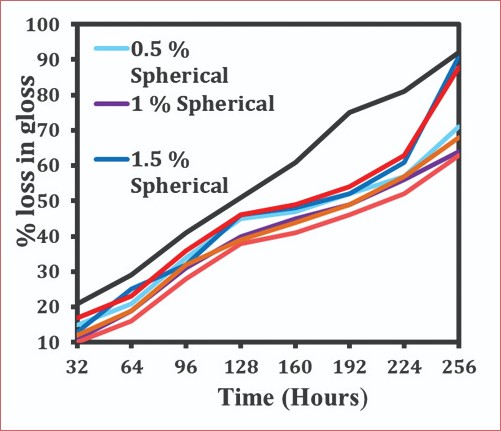
Figure 6. Percentage loss in gloss of the coatings modified with various concentrations of rod and spherical shaped nano Fe2O3 particles w.r.t accelerated UV weathering
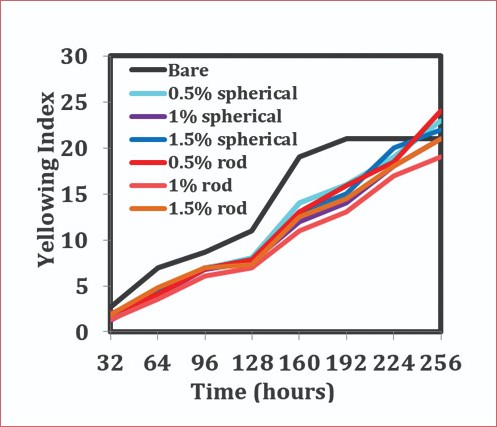
Figure 7. Yellowing index of the coatings modified with various concentrations of rod
and spherical shaped nano Fe2O3 particles wr.t time of accelerated UV weathering
Nano-modified waterproofing compound
Waterproofing is one of the severe problems in the old buildings. Lots of water proofing formulations available in the market are based upon the selection of resin with some additives in micro sizes. This results in leaving enough matrix space in the resin where micropores can form and water may start leaking. A simple solution was to find out a nano additive which distributes nicely leaving very little space or matrix to be attacked by environment as shown in Figure 8 (b) comparing it with Figure 9 (a).
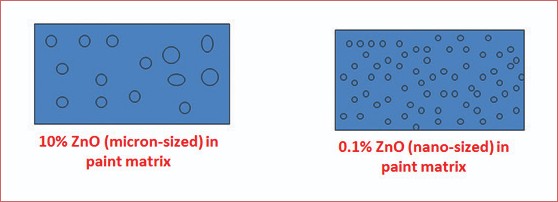
Figure 8; a) Schematic showing how large concentration of micro-sized additives still leave enough space for environmental attack while b)
nano-sized particles fill larger area in the matrix
This nano-modified compound is now available with a name called Thermacool WP-1. Its application works in three steps:
- Find out all leaking visible cracks or sides. Make small grooving in that. Apply a paste made from 50% mixture of Thermacool WP1 and white cement and some water to fill all these cracks.
- After drying of these cracks, apply using brush the Thermogreen WP-1 using brush on the whole surface area to be protected. This is called absorption coat which helps to seal all micro-pores in the concrete.
- Finally, 1mm thick paste of 50percent mixture of Thermacool WP1 and white cement is uniformly applied on the whole surfaces to fully seal it.
Fire retardant nano coating
A transparent nano-modified fire retardant coating was developed to either extinguish the fire or retard its rate of burning, on any substrate, such as wood, plastics, or metal. As shown in Figure 9, that after 7 minutes of burning the coated surface, there was no burning on the part. In the same way a PE floor mat uncoated burned immediately compared to the same, coated with nano-modified fire retardant coating DLFR-26. The TDS for this is given below in table.
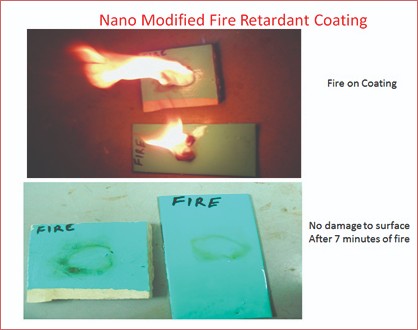
Figure 9. Showing that even after 7 minutes of burning, there is no effect on the coated wood surface.
Acid Resistant nano-modified Epoxy coating
A highly corrosion resistant, brushable epoxy based coating DLFR 300 was developed for such applications where very strong corrosion resistance from acids, alkalies or other strong mixed media is required. This is especially made for battery rooms in Ships and submarines, pickling side walls which constantly get acid vapours from acid tanks in 7 tank process, sewage treatment plants and refineries and chemical plants where SO2 , H2 S vapours keep coming. The epoxy is modified with nano PVDF particles. Coated panels resistance attack at any pH ranging from 1to14 and in various organic solvents.
SUMMARY
To summarise, it can be said that use of nano-particles, nanopigments, nano-additives and filler in paint coatings can enhance several properties of the coating such as corroiosn resistance, maechnical properties, UV blocking etc. The important requirement is to choose a suitable size and shape of the particles and optimise their concentration. This has been shown using Fe2O3 as o eof the examples which farms flakes and rod type nano-particles. It is possible to make very effective nano coatings as confirmed by examples of water-proofing, fire resistant and acid-resistant paints.
Expertise shared by:
Prof. A.S.Khanna,
Retd. IIT Bombay, Chairman SSPC India
He has 27 years of rich experience in teaching and
research, and has guided 27 Ph.D’s, 125 Masters.
He has also created research expertise in High
Temperature Corrosion, Coatings, Surface Engineering,
Corrosion of concrete structures and nano-coatings.
Cookie Consent
We use cookies to personalize your experience. By continuing to visit this website you agree to our Terms & Conditions, Privacy Policy and Cookie Policy.