Fuel efficiency and alternate energy to dominate the industrial applications
By Edit Team | November 2, 2022 6:57 pm SHARE
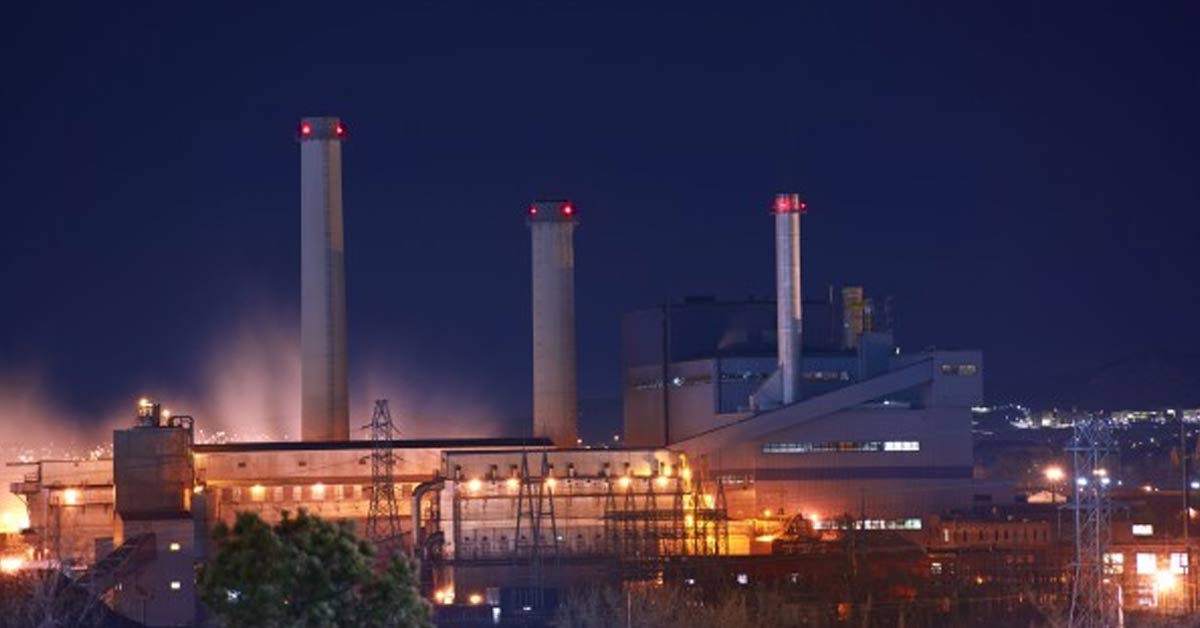
As per the recent reports the global welding market is projected to grow from $20.99 billion in 2021 to $28.66 billion in 2028 at a CAGR of 4.6 per cent in the forecast period, 2021-2028. In the past few years, the industry has evolved significantly as there is a widened application scope, driven by advanced technological tools used in manufacturing and production.
Sustainability in welding
Welding technologies can be sustainable because they contribute to the production of new components using 3D printing, metal additive manufacturing, or Directed Energy Deposition (DED-Arc). The wide range of transfer and technology like CMT-Cold Metal transfer welding technology is widely used for this AM process for manufacturing near-net shape components.
Talking about company’s initiative on sustainability and reducing waste V V Kamath, Managing Director, Fronius India Pvt. Ltd., says, “We have a carbon-neutral headquarters, and the following are the areas where we are reducing waste. In our company, reducing our green house gas emissions to a minimum is one of the main pillars of Fronius’ sustainability strategy. Decarbonisation at our Production sites in Austria will be achieved by 2023. On the one hand, we will achieve this ambitious goal on the other hand by switching from fossil fuels to clean energy such as solar energy, geothermal energy, and biomass, and on the other hand by reducing our energy consumption.”
Sharing notable technological advancement Amrityoga Mishra, Sr. Manager-Marketing at Panasonic Smart Factory Solutions India, says, “Panasonic Robots and Machines has many unique features that help customers achieve great productivity through high-speed, high-quality welding. Panasonic manufactures the full Arc welding robot, including the power source, controller, and manipulator. In the case of competition, the client needs three sources: one for power, another for the controller and manipulator, and a third for integration of these.”
Protection against corrosion and rust across industrial applications
Innovation, product development and continuous up-gradation of quality have been our constant endeavour and key strengths. Conventional metal piping products are associated with problems like poor resistance to corrosion and abrasion, chemical reactiveness, sedimentation, short and uncertain life spans, repeated maintenance requirements, etc.
G.S. Dikondawar, Sr. GM (Innovation & Technology), The Supreme Industries Ltd., suggesting solutions for corrosion and rusting, says, “On the other hand, all plastic piping products are free from these problems and offer many other advantages. Plastic piping is a sustainable and eco-friendly solution compared to conventional products. Being chemically inert and free from corrosion, plastic piping products are considered much safer than traditional metal pipes, especially for potable water applications and industrial usage.”
The growing emphasis is easing the shift of green, sustainable products and solutions across the industrial application, including welding, pipes and fitting, pump and valves, and all the allied segments in the industrial sector.
Cookie Consent
We use cookies to personalize your experience. By continuing to visit this website you agree to our Terms & Conditions, Privacy Policy and Cookie Policy.