FAQ on cold galvanising procedures
By Edit Team | May 17, 2016 11:37 am SHARE
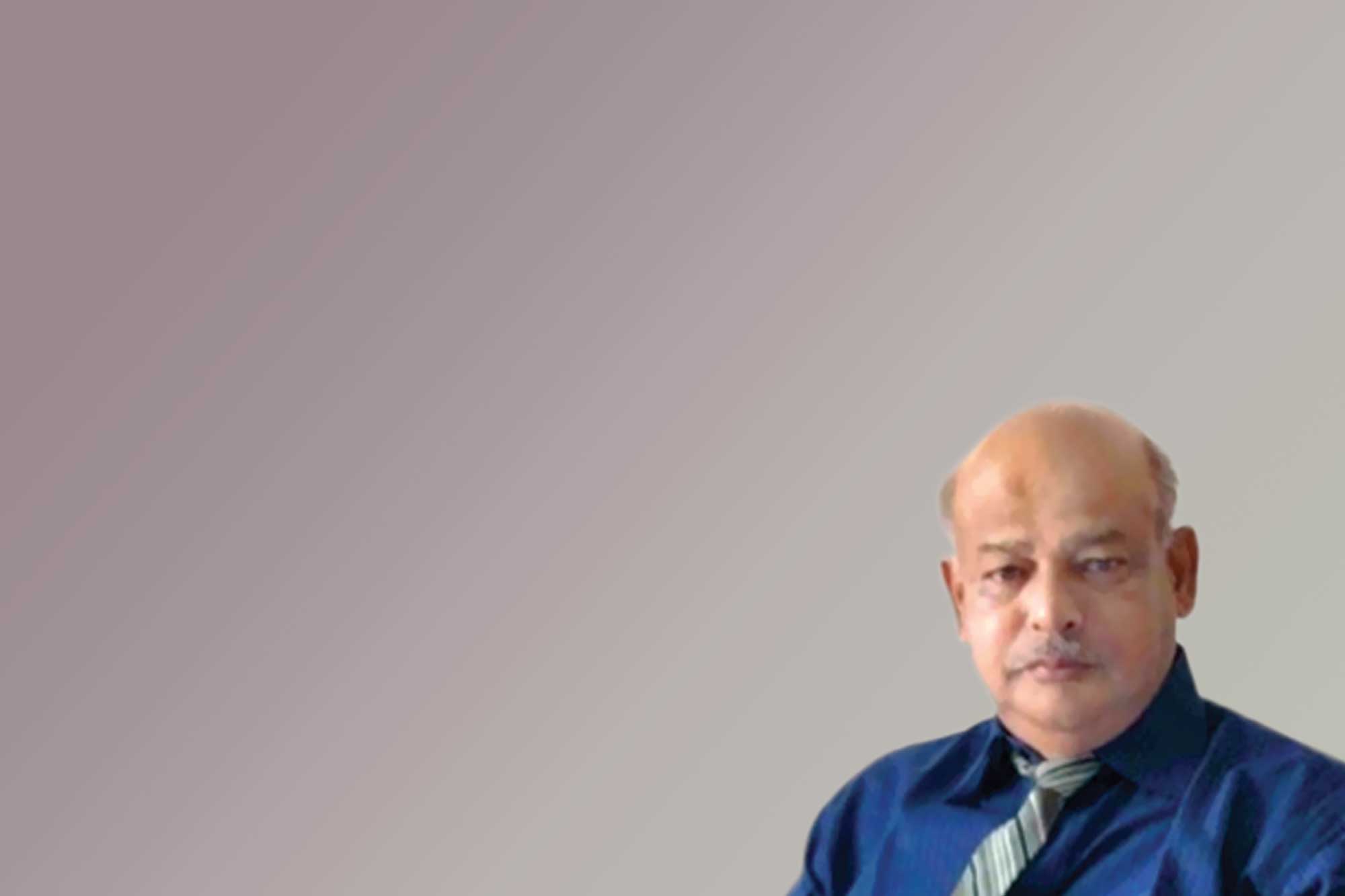
Pradeep Vaidya, Technical and Marketing Director at Promtech Consultancy Group explains the process of cold galvanising and its advantages
How does galvanising protect steel from corrosion?
Zinc metal used in the galvanising process provides an impervious barrier between the steel substrate and corrosive elements in the atmosphere. It does not allow moisture and corrosive chlorides and sulphides to attack the steel.
How long the galvanised steel fabrication lasts?
It is not uncommon for galvanised steel to last more than 70 years under certain conditions. Under very severe conditions zinc rich paints will prove to be the best option.
Does the galvanised steel coating of zinc resist abrasion?
The three inter-metallic layers that formed by fusion bonding between iron and zinc metals during the hot dip galvanising process are all harder than the substrate steel and have excellent abrasion resistance.
Why do galvanised steel appearances differ from project to project and galvaniser to galvaniser? Is there any difference in the corrosion protection offered by the different appearing coatings?
The steel chemistry is the primary determinant of galvanised coating thickness and appearance. Continuously cast steel produced by the steel companies has a wide variety of chemistries thus the different coating appearances. There are several different additives galvanisers may put in their zinc kettle viz aluminium, flux additives etc. to enhance the coating appearance by making it shiny, bright or matte gray. The external appearance of the galvanised coating does nothing to change the corrosion protection of the zinc coating. Zinc rich paints, used for touch up are polymerised paints based on QD, special resins (modified acrylics or epoxy) completely seal off the surface and offer best Rust protection.
Is galvanising more expensive than paint?
Depending on the product mix, square feet per tonne, and condition of the steel surface, galvanising is often less expensive on an initial cost basis. However the lifetime costs should be considered when making a project decision on the corrosion prevention system to utilise. With galvanising, the life-cycle cost, i.e. the cost per year to maintain, is almost always less than any conventional painting system. Paint systems require maintenance, partial repainting and full repainting several times over a 30-year project life.
How long will hot-dip galvanising protect steel from corrosion?
The corrosion rate of zinc and how long it will provide protection is a function of the coating thickness and the amount of corrosive elements in the atmosphere. For example, in rural settings where there is less automotive/truck exhaust and plant emissions, galvanised steel can easily last for 100 – 150 years without maintenance. Industrial and marine locations contain significantly more aggressive corrosion elements such as chlorides and sulphides and galvanised steel may last for 50 – 100 years in those cases.
Where are galvanised steel products used?
Mild steel used in all kinds of structural fabrications including angles, channels, wide-flange beams, I-beams, H-beams, grating, expanded metal, corrugated sheets, wire, cables, plate, castings, tubing, pipe, bolts and nuts.
The industries that utilise hot-dip galvanised steel range from infrastructure projects, water and wastewater treatment plants, architectural steel structures (like canopies, facades, exposed structural steel, lentils, reinforcing steel for concrete decks, exposed structural steel columns and barriers), pulp and paper plants (structural steel, walkways, handrail), motor housings, electrical cabinets, frames, heat exchanger coils, transmission towers, distribution poles, substations, wind turbine poles, signal antennas, and towers, rail transportation (like poles, switchgear, miscellaneous hardware), chemical and petrochemical plants, off-shore constructions, pipeline hardware steel buildings, storage tanks, walkways) silos, tank farms, chemical and steam pipelines, fence poles, boats, trailers, stadiums, arenas, road crash guards, racetrack fences, pre-engineered metal buildings and almost every mild steel fabrications.
Contact
Pradeep Vaidya, CEO,
Innovative Coating Industries,
MIDC, Pune
Thane: B-7 / 701, Vedant Complex, Vartak Nagar Naka,
Thane (West) – 400 606
Mobile: +91-9820181738
Email: puvpromtech@gmail.com
Sonia Vaidya, Tech Mktg Executive, Thane
Tele: +91-22-25883265, 9819813015
Email: soniavaidya30@gmail.com
Cookie Consent
We use cookies to personalize your experience. By continuing to visit this website you agree to our Terms & Conditions, Privacy Policy and Cookie Policy.