Cementing longevity in construction projects
By Edit Team | February 8, 2024 3:25 pm SHARE
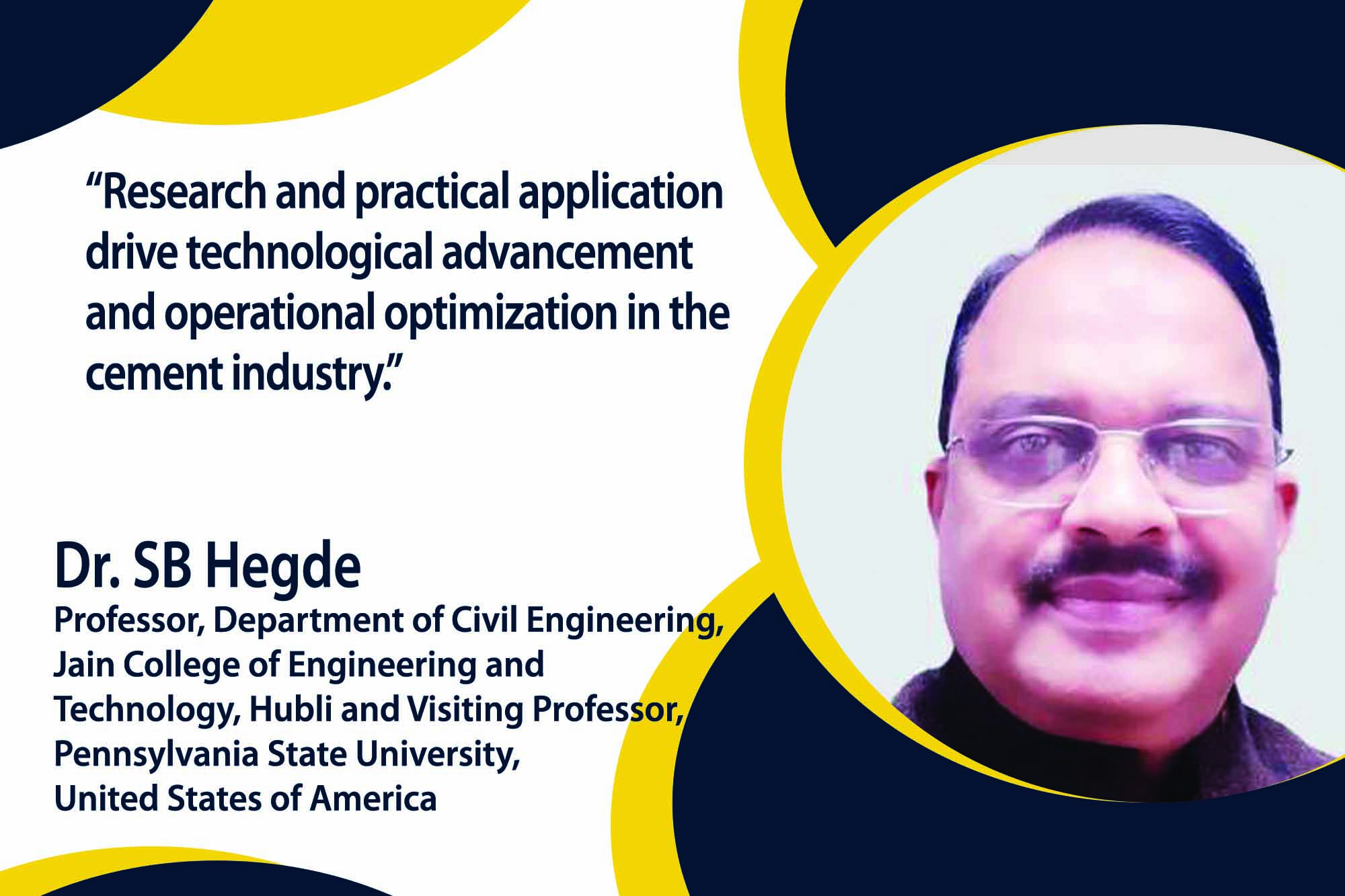
The cement industry, a crucial component of global infrastructure development, faces many challenges and opportunities. In an exclusive interview with Dr. SB Hegde, a distinguished expert in the field and a Professor at Jain College of Engineering and Technology, we delve into the key challenges and innovations shaping the future of cement manufacturing. Dr. Hegde’s extensive experience, with over 182 research papers and six patents to his credit, provides valuable insights into pivotal research findings and technological advancements in cement technology.
Challenges and innovations in the cement industry
The Indian Cement Industry, ranking second globally with an installed capacity of 580 million tons per annum, grapples with environmental and operational challenges. Dr. Hegde highlights the significant contribution of cement manufacturing to carbon dioxide (CO2) emissions and the industry’s proactive measures to address this issue. Initiatives include the adoption of alternative fuels like biomass and waste-derived fuels, advancements in energy-efficient kiln technologies, and integration of renewable energy sources.
Raw material extraction poses another challenge: resource depletion and environmental degradation. Dr. Hegde emphasises the industry’s exploration of recycling and the use of alternative raw materials, such as industrial by-products and wastes, to mitigate these concerns.
On the innovation front, Dr. Hegde discusses breakthroughs such as developing alternative binders requiring lower production temperatures, carbon capture and utilisation (CCU) technologies, and the exploration of clinker substitutes like supplementary cementitious materials (SCMs). These innovations, coupled with the integration of digital technologies, showcase the industry’s commitment to sustainability and efficiency.
Pivotal research findings and innovations
Dr. Hegde’s prolific research career has yielded impactful results in various aspects of cement technology. Noteworthy advancements include cement formulation with reduced clinker content, resulting in a tangible reduction in carbon emissions. Research in kiln technologies has led to patented approaches that significantly improve energy efficiency, reducing overall energy consumption during cement manufacturing by up to 15%.
The commitment to CCU research has resulted in efficient technologies that capture and utilise carbon emissions, substantially reducing net CO2 emissions. Additionally, incorporating industrial by-products such as fly ash and slag as supplementary materials in cement production enhances sustainability and improves performance characteristics.
In line with Industry 4.0 principles, Dr. Hegde’s research explores integrating digital technologies within cement plants, leading to the development of smart systems for real-time monitoring, predictive maintenance, and process optimisation.
The intersection of research and practical application
The synergy between research and practical application is crucial for driving technological advancements and operational optimisation in the cement industry. Dr. Hegde emphasises the role of material science research in discovering alternative binders and supplementary materials to reduce clinker content. Research in data analytics and process modelling identifies key parameters affecting cement production, leading to the implementation of advanced control systems for real-time monitoring and precise control.
Efforts focused on energy efficiency explore novel kiln technologies and alternative fuel sources, with practical applications involving retrofitting existing plants and transitioning to alternative fuels. Research initiatives also identify opportunities to utilise industrial by-products and waste materials in cement production, contributing to circular economy practices.
Circular economy in cement manufacturing
Implementing a circular economy in the cement industry is vital for reducing waste and promoting sustainable practices. Dr. Hegde highlights using industrial by-products as alternative raw materials, potentially significantly reducing traditional raw material extraction. Incorporating recycled concrete aggregates into the production process contributes to waste reduction, with circular economy practices aiming for 30% or more recycling rates.
Furthermore, co-processing waste-derived fuels diverts waste from landfills and reduces reliance on traditional fossil fuels, aligning with circular economy principles. Utilising by-products from other industries as supplementary cementitious materials can result in a 25% reduction in the carbon footprint associated with clinker production.
Procurement strategies for longevity
Strategic procurement strategies are pivotal in prolonging the lifespan of construction projects and materials in the cement industry. Dr. Hegde outlines key approaches, including emphasising high-quality raw materials, collaborating with suppliers for specialised formulations, and prioritising lifecycle cost analysis over initial costs. Incorporating sustainability criteria into procurement decisions and maintaining robust quality control measures throughout the process contribute to consistent and reliable cement properties.
Evolution of industry standards
As a participant in technical committees for standards organisations, Dr. Hegde sheds light on the evolving landscape of industry standards and their impact on cement manufacturing in India. The shift towards performance-based standards allows for a dynamic approach, fostering innovation and continual improvement. Including environmental sustainability metrics within standards reflects a global emphasis on reducing environmental impact, aligning with efforts to mitigate climate change.
Evolving standards accommodate advanced technologies like digitalisation and Industry 4.0 practices, enhancing global competitiveness. The swift standardisation of emerging technologies, such as carbon capture and utilisation, ensures the industry can adopt innovative solutions efficiently.
Cookie Consent
We use cookies to personalize your experience. By continuing to visit this website you agree to our Terms & Conditions, Privacy Policy and Cookie Policy.