Vermeer HDD is setting newstandards in directional drilling
By Staff Report | October 21, 2024 5:43 pm SHARE
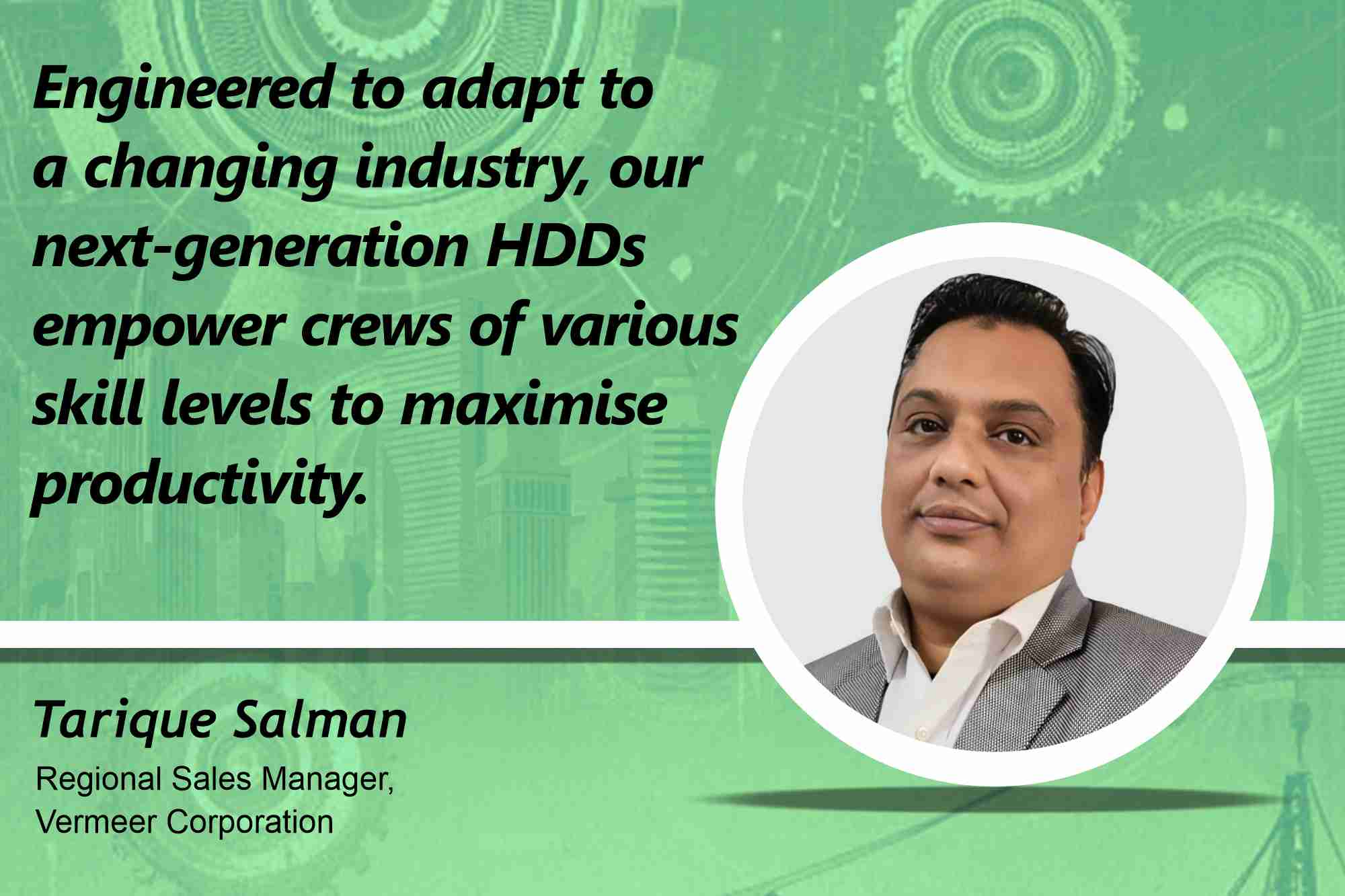
Discover how Vermeer is leading the charge in HDD technology, integrating advanced features that streamline operations and empower crews across various skill levels.
What unique features do Vermeer’s Horizontal Directional Drills (HDD) offer compared to competitors in the market?
As a trailblazer in the horizontal directional drill (HDD) sector, we take great pride in our capacity to consistently create cutting-edge machinery and technology that improve dependability and propel HDD forward. Our next generation of HDDs is built on everything that has established us as the market leader, such as delivering durability, reliability, and ease of use right at the job site.
Engineered to adapt to a changing industry, our next-generation HDDs empower crews of various skill levels to maximise productivity. Equipped with telematics and advanced onboard technology, our designs incorporate your feedback to ensure we meet your needs.
We are committed to providing increased dependability through enhanced hydraulics, electrical design, and powertrain systems. Intelligent on-rig diagnostics enable crews to troubleshoot equipment effectively, with specific diagnostic information and troubleshooting steps that help get you back to drilling without needing a dealer service tool.
Our next-generation HDDs are loaded with cutting-edge features designed to ease your crew’s workload while boosting your business confidence. Notable innovations include Automated Rod Exchange (ARE), a sliding open-side vise, and an optional larger rod box, all designed to streamline operations.
With Automated Rod Exchange, operators can automate the rod change-out process with a single button push, eliminating up to 13 steps for each rod exchange. This decreases training time and simplifies the rod exchange process, providing consistency in drilling.
The patented sliding open-side vise enhances visibility to the rod joint, maximising efficiency by minimising the steps in the rod change-out process while allowing easier access to clean or replace vise dies. Our class-leading rod capacity option allows you to bore farther without needing to dismount the machine to add a rod or change out boxes. This capability can significantly increase the total footage installed daily, potentially reducing operational costs by minimising time spent loading rod boxes.
Grounded in a strong foundation built on our past, we are excited to move into the future with our next generation of horizontal directional drills. Our added technology and machine refinements are designed to relieve job site frustrations and support your business growth.
How do your vacuum excavators adapt to various project requirements, and what specific technologies enhance their efficiency?
We have seen vacuum excavation gaining popularity as the benefits of soft dig solutions move into the mainstream. This method exposes existing infrastructure using pressurised water or air to break up the ground, followed by a vacuum that collects the debris. One of the significant advantages of our vacuum excavators is their ability to access areas that traditional excavators cannot. They are particularly useful in cold climate conditions where the ground might be frozen and can also be utilised to clean out pits.
Our vacuum excavators feature heavy-duty I-beam construction trailers and a high CFM blower configuration, making them ideal for pipeline right-of-way projects. We offer models equipped with a combination of air compressor and water pump, providing the flexibility to choose between air or hydro excavation on demand, based on job site needs. This series can be configured in either trailer or skid packages, with spoil tank capacities ranging from 500 to 1200 gallons to meet specific job site requirements. Additionally, our cam-over hydraulic rear door features a 360-degree positive seal that operates effectively even under reverse pressure, eliminating the need for additional clamping.
We also incorporate a three-stage cyclonic filtration system for wet and dry vacuum excavation. This design helps prolong filter life and keeps maintenance costs low. Another exclusive feature is our telescoping boom, which maintains hose length during extension and includes a remote-controlled hydraulic valve for easy vacuum shut-off. This combination of features enhances the efficiency and effectiveness of our vacuum excavation solutions, helping us meet the diverse needs of our customers.

Can you elaborate on any advanced technologies integrated into your trenchers and cable ploughs that improve operational precision?
We have designed our track trencher to be ideal for pipeline projects that demand high horsepower and deep digging depths. The rotary power trencher drive motor and splined head-shaft operate at low speed with high torque, allowing for effective rock excavation while minimising chain wear. This efficient ground penetration ensures optimal production results for our operators. To enhance versatility, operators can adjust trench depths using an optional sectionalise trencher boom, giving them the flexibility to meet various project requirements.
Our elevated rollover protective module (ROPM) cab is equipped with filtered and pressurised air, heating, and air conditioning, ensuring operator comfort. The cab’s elevation provides a great vantage point, allowing operators to easily view the boom, trench, and conveyor.
For added convenience, we also offer an optional wireless remote control, allowing full operators to function remotely. This feature enhances safety and operational efficiency, allowing us to effectively meet the demands of modern pipeline projects.
What measures are in place to ensure that your equipment, such as tub grinders and chippers are user-friendly and safe for operators?
We have taken the lead in new industries with our organic recycling equipment, which processes organic waste quickly and efficiently, enabling it to be transformed into useful end products. Our innovations are designed to improve productivity, streamline maintenance, and protect operators, ensuring that our compost turners, horizontal grinders, tub grinders, and trommel screens are built to last.
Specifically, our tub grinders are designed to handle stumps, regrind, and high-volume wood recycling and mulch operations. They come loaded with innovative features that enhance efficiency and job site safety. For instance, our patented duplex drum cutting system optimises cutting performance while simplifying maintenance. Additionally, our Thrown Object Restraint System (TORS) significantly reduces both the quantity and distance of thrown objects, increasing safety for operators and bystanders alike.
We also offer an optional grapple loader and a unique bio-screen kit that allows non-woody biomass materials, such as hay or agricultural residue, to pass efficiently through the grinder without compromising the quality of the end product.
Our brush chippers are engineered to withstand the daily grind for those looking to clear wood debris and logs or limbs with small to medium diameters. They feature exclusive attributes that promote easy operation, high efficiency, and operator safety. Our SmartFeed feed-sensing control optimises hardwood processing productivity. In contrast, the Ecoldle™ engine control system is adjustable to save fuel and reduce noise by automatically lowering engine speed after one or five minutes of inactivity. These advancements reflect our commitment to supporting our customers and maximising their operational efficiency and safety in the field.
What emerging trends do you see shaping the construction industry in India, particularly in the areas of utility installation and waste management?
The construction industry in India is experiencing several emerging trends, especially in utility installation and waste management. There is a growing adoption of smart technologies for utility management. IoT devices are being integrated to monitor water supply, electricity usage, and other utilities, leading to more efficient resource management.
We are increasingly emphasising green building practices, driving the installation of renewable energy sources like solar panels and energy-efficient systems. As building codes evolve, they now include more stringent sustainability requirements, pushing us to adapt and innovate.
The modular construction method has become a key strategy, allowing for the prefabrication of utility systems off-site. This approach speeds up installation, reduces on-site waste, improves quality control, and significantly shortens construction time. Innovative materials, such as self-healing concrete and energy-efficient insulation, are gaining traction. These materials can enhance the durability and efficiency of utility installations.
Innovative methods for converting waste into energy are being explored. These technologies are becoming more economically viable, reducing landfill dependence while generating power. There is a strong push towards recycling and reusing construction waste. The industry is actively participating in initiatives to convert waste into useful products, like aggregates sourced from demolished structures, which are gaining momentum.
For more information, visit: https://www.vermeer.com/ap
Cookie Consent
We use cookies to personalize your experience. By continuing to visit this website you agree to our Terms & Conditions, Privacy Policy and Cookie Policy.