Airless spray painting unit with automatic pipe coating system
By Staff Report | October 25, 2024 7:43 pm SHARE
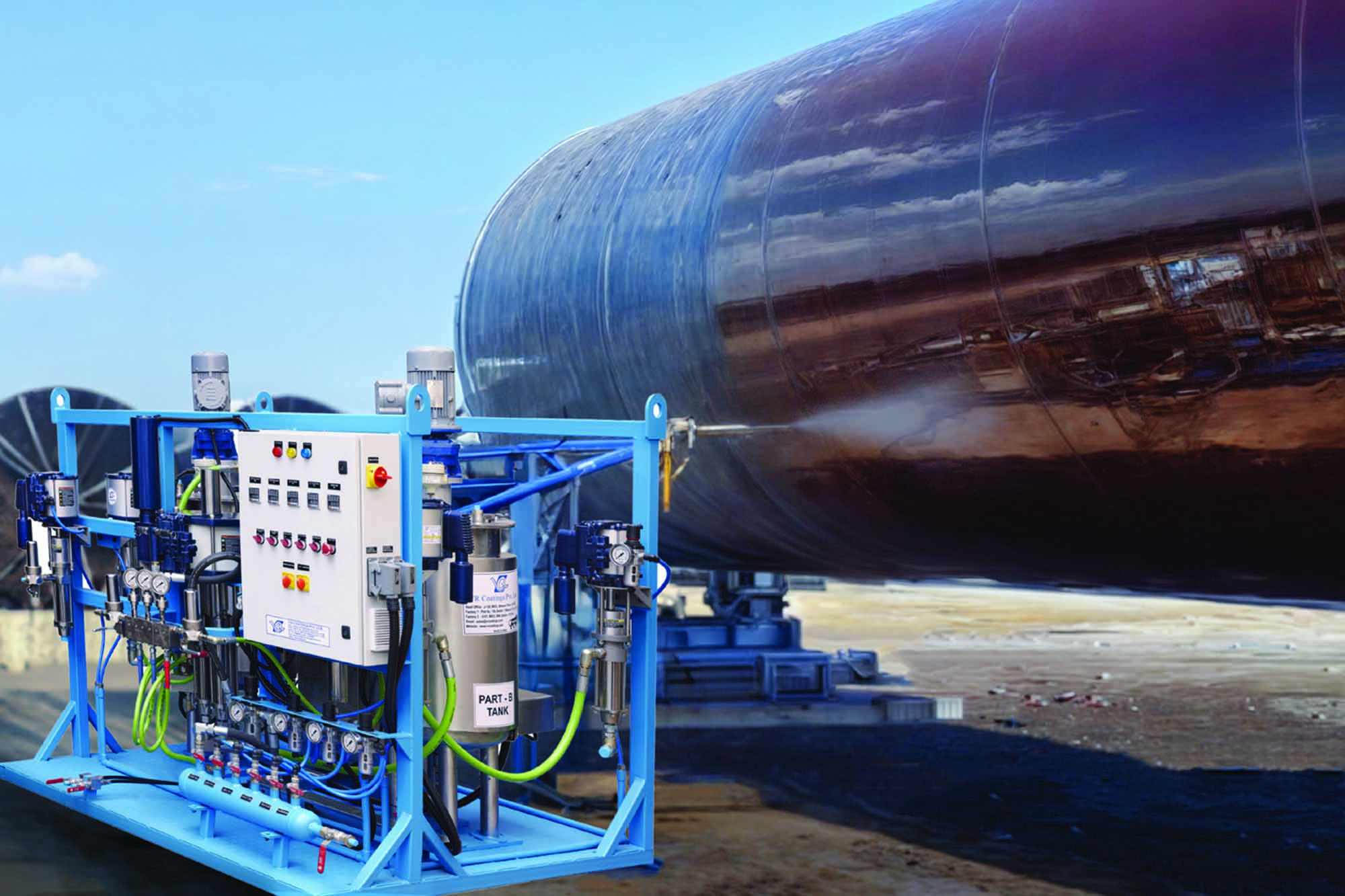
VR Coatings introduces a cutting-edge plural component spray painting system with automated pipe coating technology, ensuring precise thickness control and unmatched durability for industrial pipelines.
In the industrial world, maintaining the durability and longevity of pipelines is paramount. Protective coatings play a crucial role in this, and applying them efficiently and accurately remains a significant challenge. VR Coatings, a leader in surface finishing technologies, has developed an advanced plural component hot, airless spray painting unit integrated with an automatic pipe coating system featuring pipe rotators and a boom. This solution is engineered to achieve precise coating thickness, ensuring enhanced protection and performance.
The power of plural component technology
Plural component coatings, formed by combining two or more chemical substances like epoxy and polyurethane, offer superior corrosion resistance and durability. However, these coatings have a limited pot life, meaning they must be applied quickly after mixing to prevent waste and ensure proper adhesion.
VR Coatings’ hot, airless spray painting unit is designed to handle plural component coatings precisely. The unit mixes the components near the spray gun nozzle, eliminating the need for premixing. This reduces waste, ensures consistent coating quality, and allows quick, efficient application, even in harsh environments. The hot, airless spray feature uses high pressure to atomize the coating, reducing the overspray and achieving an even, smooth finish.
Automatic pipe coating system: Precision at its core
A standout feature of this solution is its automatic pipe coating system. Automating the coating process ensures every pipe receives an even and accurate layer of coating, regardless of size or shape. The system accommodates various pipe diameters and lengths, making it versatile across various industries, including oil and gas, water treatment, and industrial piping systems.
The combination of the boom and pipe rotators ensures seamless operation. The pipe rotators hold the pipe in place and rotate it at a controlled speed, guaranteeing uniform application across the entire surface. Meanwhile, the boom, adjustable in height and angle, allows the spray gun to reach every part of the pipe precisely. This setup eliminates manual handling errors, reduces inconsistencies, and ensures uniform coating thickness.
Achieving precise coating thickness
One of the key benefits of VR Coatings’ system is its ability to achieve precise coating thickness. In industries like oil and gas, maintaining the correct thickness of protective coatings is critical to prevent corrosion and extend the lifespan of the pipes. The automatic system continuously monitors and controls the flow rate of the coating material, ensuring consistent thickness throughout the process. This precision enhances coating quality while reducing material waste, making it a highly cost-effective solution.
Achievement
VR Coatings’ plural-component hot, airless spray painting unit with an automatic pipe coating system sets a new benchmark in industrial pipe protection. Its combination of advanced automation, precision, and efficiency makes it an essential tool for industries requiring reliable and durable coatings. With integrated features like pipe rotators and an adjustable boom, the system delivers consistent, high-quality results, reduces operational costs, and ensures the longevity of pipelines through precise control of coating thickness.
For more information, visit: https://www.vrcoatings.com/
Cookie Consent
We use cookies to personalize your experience. By continuing to visit this website you agree to our Terms & Conditions, Privacy Policy and Cookie Policy.