Fire-resistant stone wool insulation is non-combustible and can withstand over 1,000°C
By Staff Report | November 18, 2024 6:14 pm SHARE
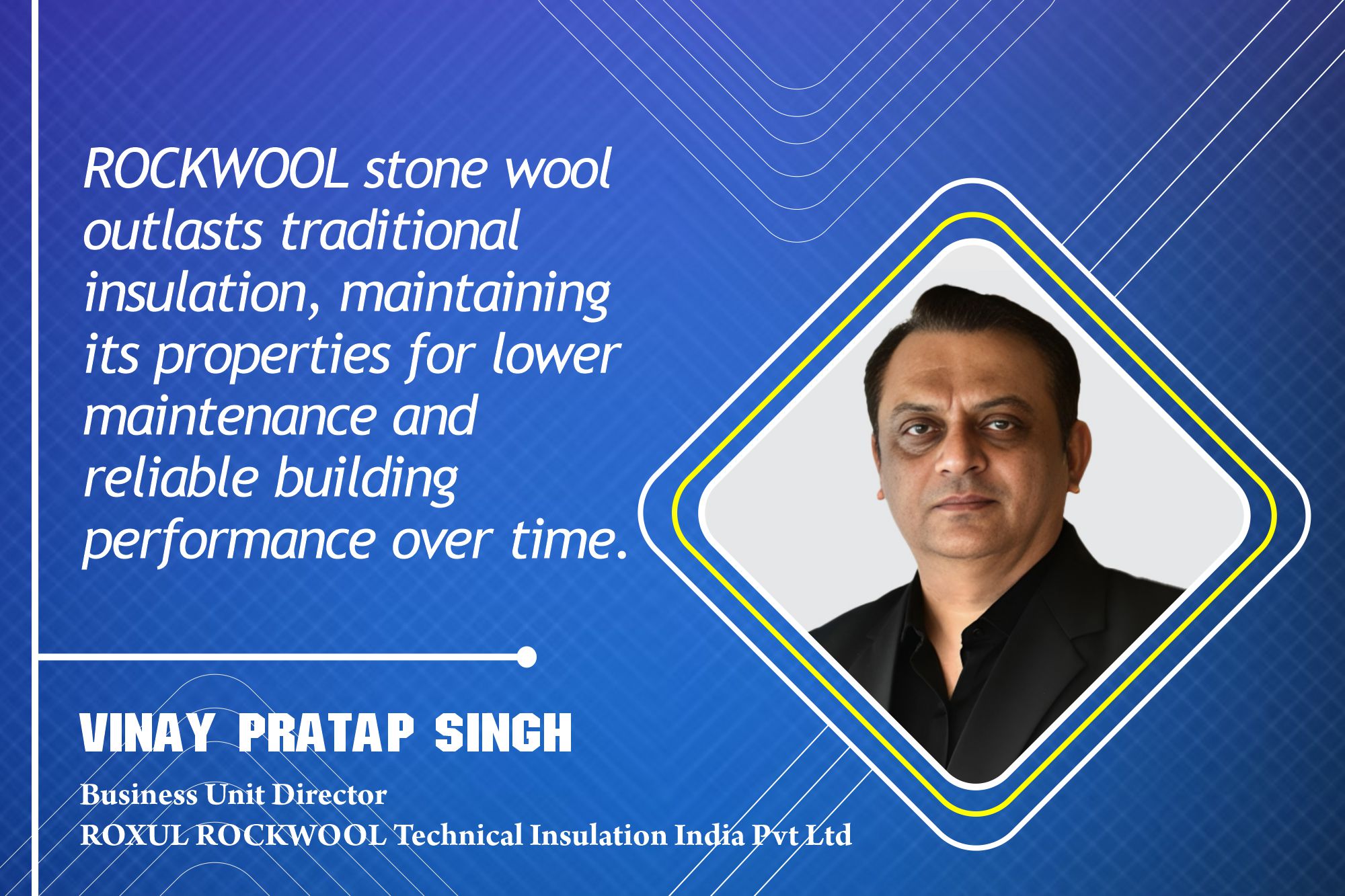
ROCKWOOL, a leader in sustainable insulation, is expanding its presence in India with a new plant in Tamil Nadu. The plant will provide energy-efficient, fire-safe construction solutions customised to India’s infrastructure requirements.
ROCKWOOL has been established in India for over a decade now. Can you tell us about ROCKWOOL’s growth trajectory and future expansions in India?
We have steadily developed our footprint in India, beginning with a production facility in Dahej, Gujarat, in 2011 and growing rapidly. To address increased demand and better service the Indian market, we are expanding operations by opening a new facility in Cheyyar, Tamil Nadu. This strategic location will allow us to increase manufacturing capacity, shorten lead times for southern regions, and more efficiently serve the rapidly expanding PEB and industrial insulation sectors. The Cheyyar factory demonstrates our commitment to India’s infrastructure growth, bringing innovative manufacturing closer to our southern clients and reaffirming our commitment to long-term, fire-safe insulation solutions nationally.
How do ROCKWOOL stone wool products contribute to energy efficiency and thermal heat regulations in buildings, especially given India’s diverse climatic conditions?
India’s many climate zones—from the heat of the plains to the cooler northern regions—require adaptive insulating methods. ROCKWOOL stone wool is excellent in temperature regulation because of its low thermal conductivity, which reduces heat transfer. This feature keeps buildings cool in the summer and warm in the winter, decreasing dependency on heating and cooling equipment. As a result, energy consumption is reduced, which affects greenhouse gas emissions. When used in PEB applications, our insulation provides excellent thermal comfort across all climates, supporting green building standards and improving operational efficiency in industries such as warehousing, manufacturing, and logistics.
What distinguishes ROCKWOOL stone wool-based sandwich panels from other materials regarding fire
resilience, and why is this particularly relevant in the Indian PEB sector?
ROCKWOOL stone wool insulation is intrinsically non-combustible and can sustain temperatures above 1,000 °C, making it an excellent choice for fire-resistant applications. This is critical in India’s PEB sector, where safety standards are tightening, and fire hazards are prevalent in industrial settings. Conrock / Lamrock panels’ recent 1-hour- and 2-hour fire ratings provide additional protection for buildings and occupants. Unlike traditional insulation, which can contribute to fire spread, our Conrock / Lamrock Sandwich panels act as a fire barrier, extending structural integrity and allowing for safer evacuation time — a significant advantage in industries with high fire loads, such as warehouses and manufacturing facilities.
Can you explain the significance of achieving EN 1364 Part 1 fire ratings for ROCKWOOL Conrock/Lamrock-based sandwich panels? What does this mean for safety standards in India?
EN 1364 Part 1 is a stringent European standard that evaluates the fire resistance of non-load-bearing wall components, which is critical for building safety. Our Conrock / Lamrock sandwich panels, newly certified with 1-hour and 2-hour fire ratings, provide longer fire protection, increasing safety in commercial and industrial situations where fire risk management is critical. Adopting such standards assures that buildings in India are fire-resistant and meet or exceed local regulatory requirements. This coincides with the country’s continuous efforts to improve fire safety standards and working conditions in high-risk industries.
Given the push to reduce plastic usage, how does ROCKWOOL stone wool insulation support India’s environmental goals in construction?
ROCKWOOL stone wool insulation is an environmentally beneficial alternative to plastic-based insulation. Stone wool is manufactured from naturally occurring basalt rock, a sustainable resource. The building industry may dramatically reduce plastic usage and waste by using stone wool. Our commitment to employing sustainable, recyclable materials is directly aligned with India’s ‘Beat Plastic Pollution’ project, which promotes environmentally conscious construction methods and helps reduce building operations’ environmental impact.
In terms of long-term performance, how does ROCKWOOL stone wool compare to traditional insulation materials used in sandwich panels?
ROCKWOOL Stone wool is well-known for its long-lasting performance. Unlike standard insulation materials, which decay, lose structural integrity, and absorb moisture with time, our stone wool retains its thermal, acoustic, and fire-resistant qualities. This long-term stability means fewer maintenance costs and continuous building performance. Our stone wool solutions provide a superb solution for the PEB industry, where rapid assembly and long-term durability are critical, making it a sensible investment for building owners.
What future insulation and building materials trends does ROCKWOOL anticipate, and how is it preparing to meet these evolving needs?
We anticipate increased demand for sustainable, high-performance insulation due to tougher building requirements, higher energy costs, and initiatives to combat climate change. Insulation technology advancements, such as increased fire ratings and acoustic performance, are also expected. We spend substantially on R&D to stay ahead, focusing on solutions that combine sustainability and high performance. As India pushes for green construction and energy efficiency, Our sophisticated insulation materials and production and distribution expansions ensure that we are well-positioned to serve the future of India’s building sector.
With growing attention to sustainable building materials, how does ROCKWOOL’s approach to manufacturing align with India’s sustainability objectives?
Our manufacturing process emphasises circular economy concepts using basalt rock, a naturally abundant resource, as its major raw material. Our stone wool offcuts and line waste are also recycled internally. In India, where the push for sustainable infrastructure is rising, our products minimise energy demand and pollutants over their lifetime. Our products directly support India’s green building initiatives, contributing to the country’s goal of lowering carbon emissions.
Do you run any programme that contributes to sustainability and environmental goals in India by reducing the use of scarce raw materials?
ROCKWOOL Rockcycle® is our flagship service which is pivotal in achieving our sustainability and environmental objectives by minimising the demand for scarce raw materials through an innovative closed-loop recycling system. This initiative allows us to recover and reuse stone wool from construction, renovation, and demolition sites, effectively channeling it back into our production process after cleaning and preparing it for recycling. By doing this, we significantly reduce our reliance on newly extracted resources, supporting India’s shift toward resource efficiency and a circular economy.
One of Rockcycle unique advantages is its ability to recycle stone wool infinitely without any degradation in performance, unlike materials such as plastics that tend to lose quality and get “downcycled” into lower-value products. For India, where the construction industry is growing rapidly, this aspect of Rockcycle offers a sustainable solution that not only conserves resources but also lessens the carbon footprint associated with raw material extraction and manufacturing. It’s an approach that directly aligns with the nation’s efforts to build a greener, low-carbon future, making Rockcycle a strategic, sustainable choice for India’s evolving building and insulation needs.
What are the key benefits and challenges associated with implementing the ROCKWOOL Rockcycle® service in India’s construction sector?
ROCKWOOL Rockcycle® service offers substantial benefits for India’s construction industry, especially with the growing demand for sustainable and high-performance building materials. The closed-loop recycling system ensures that waste stone wool collected from construction sites doesn’t end up in landfills but instead returns to our manufacturing process. This reduces waste, conserves valuable resources, and lowers the environmental impact of our operations. With Rockcycle, we offer a fully circular recycling solution that uniquely retains stone wool’s insulating properties even after multiple cycles of reuse, which sets us apart in an industry where downcycling is often the norm.
However, implementing Rockcycle in India does present operational challenges. For one, it’s crucial to maintain a supply of clean, uncontaminated stone wool for effective recycling, which requires close collaboration with clients to ensure materials are free from mixed waste. Additionally, handling fluctuating volumes of reclaimed material can create storage demands at our facilities, which we need to manage by optimising capacity planning. Overcoming these challenges is key to scaling Rockcycle in India, and we’re committed to adapting the program to meet local needs as we expand its reach.
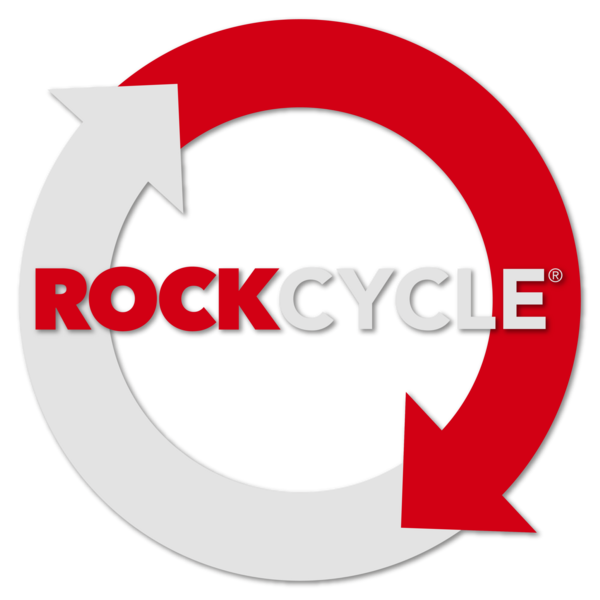
For more information, visit: https://www.rockwool.com/in
Cookie Consent
We use cookies to personalize your experience. By continuing to visit this website you agree to our Terms & Conditions, Privacy Policy and Cookie Policy.