Everest Industries builds a future-prooffacility for Pragati Infra
By Staff Report | November 23, 2024 4:18 pm SHARE
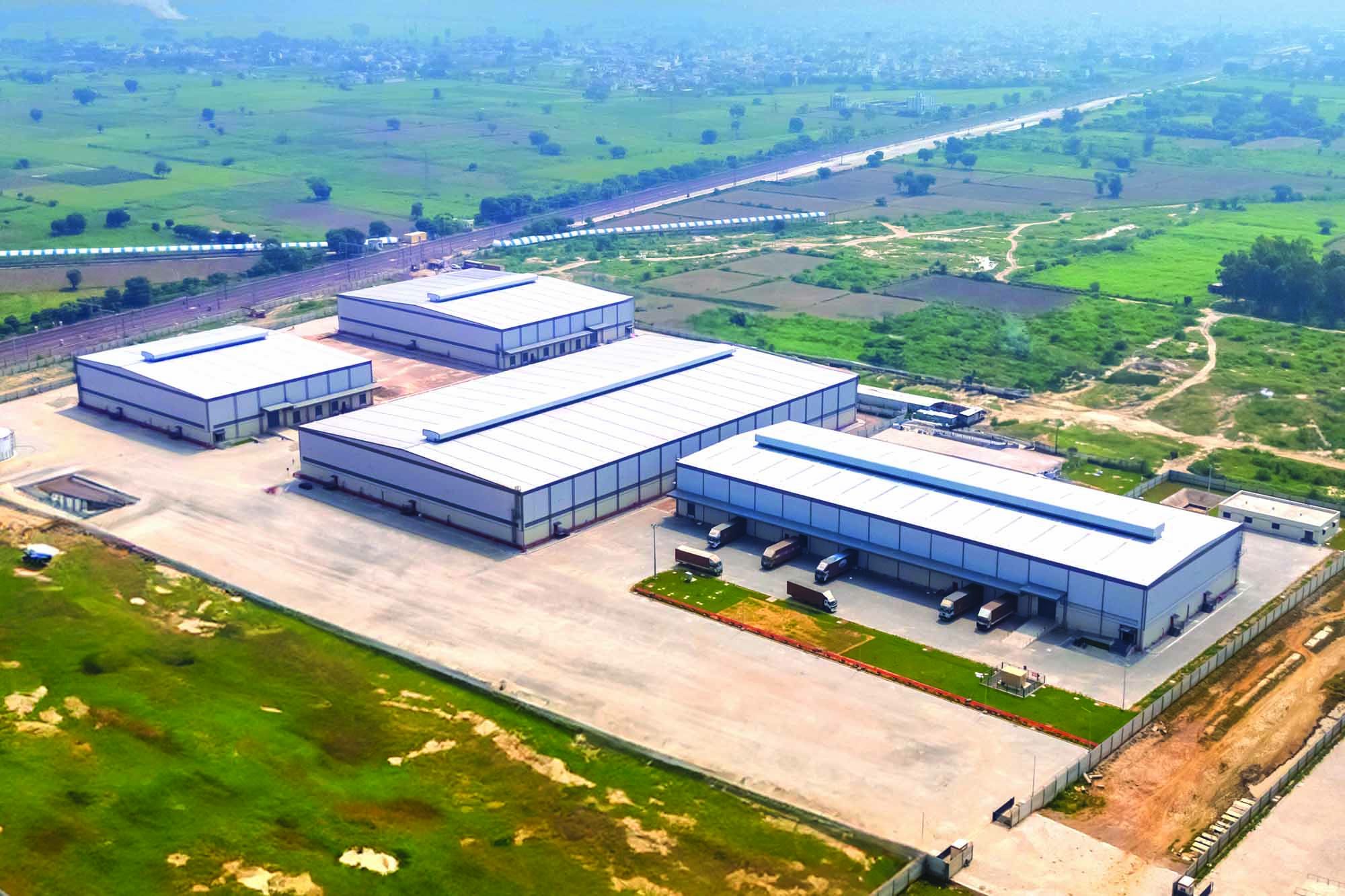
Everest Industries’ extension of Pragati Infra’s Palwal facility exemplifies sustainable industrial design by combining energy efficiency, natural lighting, and adaptable spaces to accommodate changing production requirements and enable long-term growth.
Pragati Infra, a renowned industrial manufacturing company, has tasked Everest Industries with expanding its Palwal, Haryana facilities to increase production capacity. The project included the construction of three unique buildings, each designed to fulfil the company’s evolving operational demands. This case study will examine the facility’s architectural, structural, and sustainable elements. We will focus on the novel engineering solutions, tonnage, and area specifications that make this industrial complex unique in modern architecture.
Overview of the project
The Pragati Infra Palwal extension project comprises three buildings, each built for a unique operational purpose but linked by cutting-edge engineering solutions offered by Everest Industries. The facility’s overall tonnage is 1,000 metric tonnes (MT), and each structure includes modern amenities, optimised workstations, and sustainable elements designed to fulfil the company’s growing needs.
Building specifications
Block A2
Block A2 is the complex’s largest structure and exemplifies modern industrial architecture. With a tonnage of 495 MT and a plinth area of 11,580 square metres, this structure is intended to handle a high operational capacity while ensuring energy efficiency and worker comfort.
·Daylight Polycarbonate: 647 square metres of daylight polycarbonate panels built into the roof help flood the room with natural light, eliminating the need for artificial lighting and improving the overall working environment.
·Insulation: The roof has 4 mm thick air bubble insulation and covers 11,700 sq m. This insulation helps to regulate internal temperatures by limiting heat loss in the winter and keeping a cool indoor climate during the hot summer months.
·Louvres: 278 square metres are strategically arranged to provide effective ventilation and improve air quality throughout the structure.
·Mezzanine Area: A 590 sqm mezzanine level improves the building’s storage and operations capacities while not increasing its overall footprint.
Block A1—Part 1
Block A1 is divided into two portions, each built for a specific function within the industrial complex. Part 1 has a plinth area of 3,980 square metres and a tonnage of 220 tonnes.
·Daylight Polycarbonate: 300 square metres of polycarbonate panels allow plenty of natural light, minimising the need for artificial lighting and increasing energy efficiency.
·Insulation: The roof is insulated with 4mm thick air bubble material that covers 4,203 square metres, delivering consistent thermal performance year-round.
·Louvres: 255 square metres of louvres are installed to improve ventilation and ensure excellent air circulation and comfort.
·Mezzanine Area: A 340 sqm mezzanine adds extra space for operational purposes, storage, or future expansion.
Block A1 – Part 2
Part 2 of Block A1 is the largest of the two pieces, weighing 285 tonnes and covering an area of 5,800 square metres.
·Daylight Polycarbonate: This part has 435 square metres of polycarbonate panels, which allow natural light to permeate the interior while reducing energy use.
·Insulation: The roof is insulated with 4mm thick air bubble material, which covers 6,067 square metres and ensures efficient temperature regulation.
·Louvres: 337 square metres are fitted to improve air circulation and eliminate the demand for mechanical cooling systems.
·Mezzanine Area: This section’s 481 sq m mezzanine provides additional storage or operational space and allows for future growth.
Sustainable features and efficiency
Sustainability was a top emphasis during the facility’s design and construction. The strategic use of daylight polycarbonate panels across all buildings reduces dependency on artificial lighting, lowering energy consumption and improving the internal environment for workers.
The air bubble insulation utilised in the roofing system considerably improves the facility’s energy efficiency by maintaining ideal inside temperatures all year. This minimises the demand for HVAC systems, resulting in cheaper energy bills and a more environmentally responsible operation.
Furthermore, the buildings have louvres that allow for natural ventilation, which minimises mechanical cooling and improves indoor air quality, critical for worker health and productivity.
Futureproofing through mezzanine spaces
Each block has a mezzanine area varying in size from 340 to 590 sqm, which provides flexible space for future storage, operations, or equipment. These mezzanine floors help to future-proof the building, allowing it to accommodate Pragati Infra’s rising needs as the firm grows.
Everest Industries’ Pragati Infra extension project in Palwal exemplifies modern industrial construction that integrates sustainability, energy efficiency, and functional design. Everest Industries has designed a facility that suits Pragati Infra’s current operational needs while providing long-term adaptability for future growth.
This project supports Pragati Infra’s expanding operations and establishes a new standard for industrial buildings in the region. It showcases Everest Industries’ ability to deliver high-performance, sustainable industrial facilities.
For more information, visit: https://www.everestind.com/
Cookie Consent
We use cookies to personalize your experience. By continuing to visit this website you agree to our Terms & Conditions, Privacy Policy and Cookie Policy.