New wet press and green innovations are reforming concrete production
By Staff Report | December 19, 2024 5:51 pm SHARE
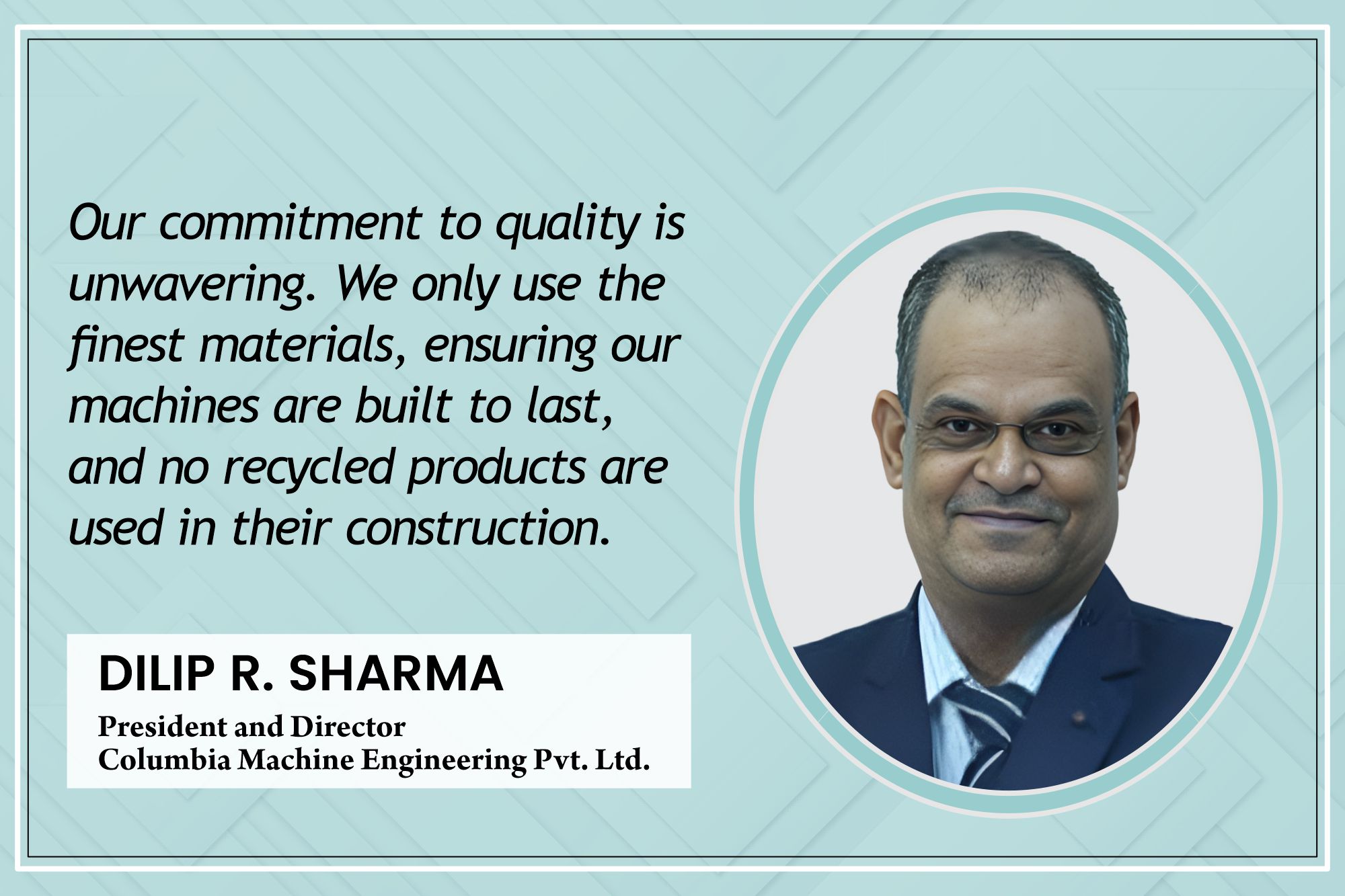
Columbia Machinery will showcase its latest innovations in concrete block production, energy-efficient technologies, and the Made-in-India Columbia Wil-El-Mil Wet Press, which has revolutionised the industry with cutting-edge sustainability practices and digital integration.
How important is an event like bauma CONEXPO INDIA in fostering relationships between manufacturers, project procurement professionals, and government stakeholders?
At major exhibitions worldwide, we consistently receive much attention from our large client base. Our huge number of visitors in India keeps us active most of the time. Beyond strengthening connections with existing clients, we are broadening our reach to include key stakeholders in infrastructure and construction. Our focus includes infrastructure firms, subcontractors, building material suppliers, and companies specialising in soil stabilisation.
Can you walk us through the latest innovations showcased in your product line at bauma CONEXPO INDIA 2024?
We use the Vertical Mould Vibration method, which benefits our customers by allowing them to produce concrete blocks with outstanding strength and perfect dimensional precision. This improved method minimises the quantity of cement used and decreases water absorption in the blocks, resulting in higher quality and economic efficiency.
In addition, we have started manufacturing the Columbia Wil-El-Mil Wet Press at our Columbia Machine India factories. This development is a game changer for the factories, particularly for prominent Wet cast manufacturers, because it gives them access to the world’s best-wet press technology at a reasonable cost. By manufacturing this cutting-edge technology in India, we enable our customers to attain outstanding product quality while supporting sustainable practices.
At the exhibition, we will debut our Made-in-India Concrete Wet Press. Given the large amount of concrete and space required for its functioning, a live demonstration of this plant on the exhibition floor is impossible. However, attendees will be able to delve further into this powerful technology’s advanced features and benefits, emphasising its potential for efficient and high-quality concrete production. We are also asking potential purchasers to visit our existing client sites and factory to see the plant in operation and conduct production demonstrations.
How is your company integrating eco-friendly practices in areas like emissions control and energy consumption in your equipment?
We began employing energy-efficient motors because we are devoted to minimising our clients’ environmental footprint and operational costs. This unique technique significantly reduces energy use and greenhouse gas emissions, helping to create a more sustainable future.
Our proprietary Vertical Mould Vibration Technology maximises energy efficiency when combined with modern hydraulic and pneumatic systems. By reducing electric power use, we help our customers lower their carbon footprint while saving money.
Digital transformation, including AI, IoT, telematics, and automation, is a driving force in the industry. How are these technologies integrated into your products? We have integrated IOT into the panels of Concrete Block Plants and Batching Mixing Plants. This will enable our clients to access input on raw material usage, production, and plant efficiency. This will also allow us, as equipment producers, to access them with online support.
What training or skill development programs does your company offer to ensure operators can fully utilise your product’s capabilities?
To ensure the best performance and longevity of our equipment, we recommend that our customers use professional personnel with ITI or diploma certificates in electrical and mechanical engineering to run the block and batching mixing plants. Furthermore, we recommend appointing civil engineering diploma or BE graduates as plant managers or quality control engineers.
We welcome this team to our facility for a comprehensive 3-5-day training program that will cover the theoretical and practical elements of our equipment. This training provides operators with a solid understanding of technology and equipment.
Our experienced Service Engineers impart training on assembly, erection and commissioning. Finally, customer operators receive on-site training covering production processes, machine settings, mould changes, mix design, and machine parameter optimisation.
The equipment market is growing rapidly, but this brings challenges in building a robust component supplier and service provider ecosystem. How are you addressing these challenges? Our cutting-edge manufacturing facility in Vadodara allows us to manufacture a wide range of equipment in-house, including batching and mixing facilities, handling systems, and moulds.
We get our outsourced components from reputable vendors with long-term connections, resulting in a strong and dependable supply chain. This strategic approach creates a robust supplier ecosystem.
Can you describe your approach to sustainability across your product’s lifecycle, including any material developments, recycling, or circular economy initiatives?
We adhere to the patented design of Columbia Machine Inc., USA, a firm known for its unique designs. Our machines rely on their tried-and-true procedures, which have been used since 1937. We improved our tried-and-true designs, ensuring machines endure longer and offer higher-quality results. We are committed to quality and only utilise the best materials; no recycled products here!
What can attendees expect from your company’s presence regarding live demos or conference participation? Are there any specific highlights you would like to share with those attending?
Our strategic acquisition of Wil El Mil, the global pioneer in Wil El Mil technology, in October 2022 has strengthened our position as a leading provider of sophisticated production solutions for concrete wet press technology. Building on our two years of excellent experience providing Columbia Wil El Mil technology from our UK facility, we are pleased to announce the start of domestic manufacturing of the Columbia Wil El Mil Wet Press in Baroda.
This critical milestone allows us to provide cost-effective and innovative solutions to our valued customers. We are excited to display our ‘Made in India’ machinery at baumaConexpo, where we will provide detailed insights into the technology and manufacturing process. We are not conducting a live demo due to space constraints and the large quantity of concrete required.
With India’s changing regulatory framework in construction, infrastructure, and mining sectors, how is your company adapting to ensure compliance while innovating? Do you foresee any regulatory shifts that could further accelerate growth in these sectors?
The Indian government’s infrastructure programs, particularly statewide highway construction, have greatly raised the demand for high-quality concrete block machines to manufacture retaining wall blocks and high-strength concrete pavers. This rise has resulted in our company’s highest-ever order book.
Furthermore, government mandates to use fly ash bricks near thermal power stations to reduce environmental effects have increased demand for high-quality fly ash bricks. We are happy to be fulfilling orders from quality-conscious customers who use our cutting-edge concrete block equipment to create these eco-friendly bricks.
Cookie Consent
We use cookies to personalize your experience. By continuing to visit this website you agree to our Terms & Conditions, Privacy Policy and Cookie Policy.