JCB unveils CEV stage 5-ready machines
By Staff Report | February 11, 2025 6:17 pm SHARE
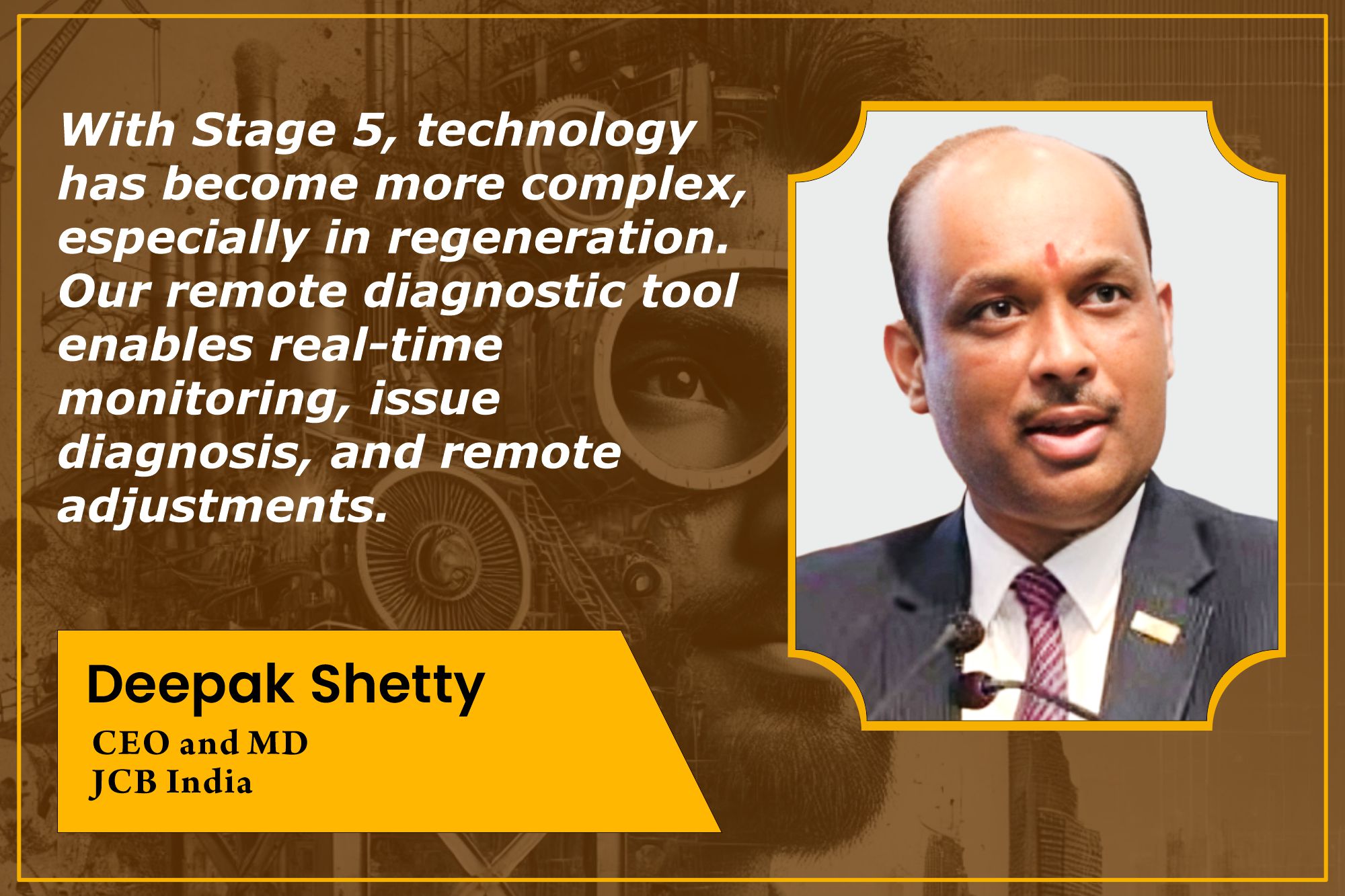
The launch of JCB’s CEV Stage 5-ready machines marks a pivotal shift towards greener, more efficient construction equipment. Designed with both cost-effectiveness and sustainability in mind, these machines deliver reduced maintenance costs, enhanced fuel economy, and adherence to stringent emission standards, making them a smart investment for today’s eco-conscious businesses.
How do your new CEV Stage 5-ready machines balance fuel efficiency, cost-effectiveness, and sustainability while meeting stringent emission standards?
We are excited to introduce our new range of CEV Stage 5-ready machines, engineered to align with the government’s vision of reducing pollution and fossil fuel consumption. Our team of dedicated engineers has enhanced fuel efficiency by 10-15% compared to previous models, boosting productivity and lowering maintenance costs. This makes the machines more cost-effective for our customers in the long run.
With a significantly reduced total cost of ownership, these machines offer outstanding value. Despite meeting strict emission standards, we’ve kept price increases minimal, ensuring competitive pricing that gives our customers more for their investment. Every hour these machines operate will deliver greater financial returns.
Operator safety and comfort have also been top priorities. We’ve incorporated a ROPS (Roll-Over Protective Structure) cab for enhanced protection and designed quieter, more comfortable cabins. This is especially vital for operators who spend long hours in the field, as we’ve focused on ease of use and reduced noise levels to improve the overall experience.
On the sustainability front, the 10-15 percent fuel efficiency improvement plays a crucial role in lowering fossil fuel consumption, which reduces emissions and helps shrink the machines’ carbon footprint. These advancements contribute to conserving natural resources and minimising environmental impact. We proudly offer a solution that benefits our customers and the planet.
Have customers played a role in the development or refinement of these machines?
We highly value customer feedback. During the testing phase, we placed these machines in the hands of our customers and actively sought their input. This feedback has been invaluable, enabling our engineers to refine and enhance the machines. This collaborative approach makes us confident that these machines perfectly align with market needs.
Are these machines already available for delivery?
We have already sold many of these machines ready for use in the field. Before launching, we conducted over 200,000 hours of rigorous testing across various conditions in India over the past two years to ensure the machines are reliable and optimised for our customers’ needs.
How does your remote diagnostic tool enhance machine uptime and reduce customer operational costs?
With the transition to Stage 5, technology has become more complex, particularly with regeneration processes. To tackle potential challenges, we’ve introduced a remote diagnostic tool that allows us to monitor machines in real time, diagnose issues, and even make adjustments remotely, eliminating the need to send a service engineer on-site. This innovation significantly boosts machine uptime, ensuring smooth operations with minimal disruptions.
For our A455 wheel loader, customers can expect approximately 18.5 lakh rupees in savings over its lifecycle – about 30 percent of the machine’s cost. These savings are driven by enhanced fuel efficiency and lower maintenance costs. The advanced technology has also improved the machine’s resale value, offering even greater financial returns for our customers.
How do your comprehensive training programmes for service engineers and machine operators enhance customer experience and minimise downtime?
Training is a cornerstone of our offering. We’ve trained over 5,000 service engineers across our dealerships, ensuring they’re equipped to deliver top-tier service and resolve machine issues swiftly, minimising customer downtime. In addition, we’ve trained thousands of machine operators, empowering them to operate the machines safely and effectively, which enhances the overall customer experience.
Our commitment to training extends through regular programmes for machine operators. For instance, last year, we trained over 5,000 operators to ensure they could handle the machines expertly. We also focus on training service engineers at our dealerships, enabling them to provide exceptional support. With the industry’s largest dealership and service network, our customers enjoy fast, efficient service that keeps their operations running smoothly.
What are your thoughts on some companies stocking older technology machines?
Stocking older technology machines is not in the customer’s best interest. Our customers deserve the latest technology with better fuel efficiency, lower costs, and improved environmental standards. By delivering these Stage 5 machines, we ensure they get the best technology available. It’s our responsibility as OEMs to provide machines that are not only better for the customer but also align with broader national goals like reducing pollution and conserving energy.
The future of our machines lies in continuous improvement. We’ll keep pushing the boundaries of innovation, ensuring that our machines are not only technologically advanced but also more sustainable and cost-effective. We’re committed to offering solutions that benefit our customers, industry, and the environment. This latest range is a big step in that direction, and we’re excited to see how it positively impacts our customers’ businesses.
For more information, visit: https://www.jcb.com/
Cookie Consent
We use cookies to personalize your experience. By continuing to visit this website you agree to our Terms & Conditions, Privacy Policy and Cookie Policy.