A challenge: Safety integration of AGVs
By Edit Team | July 12, 2024 12:14 pm SHARE
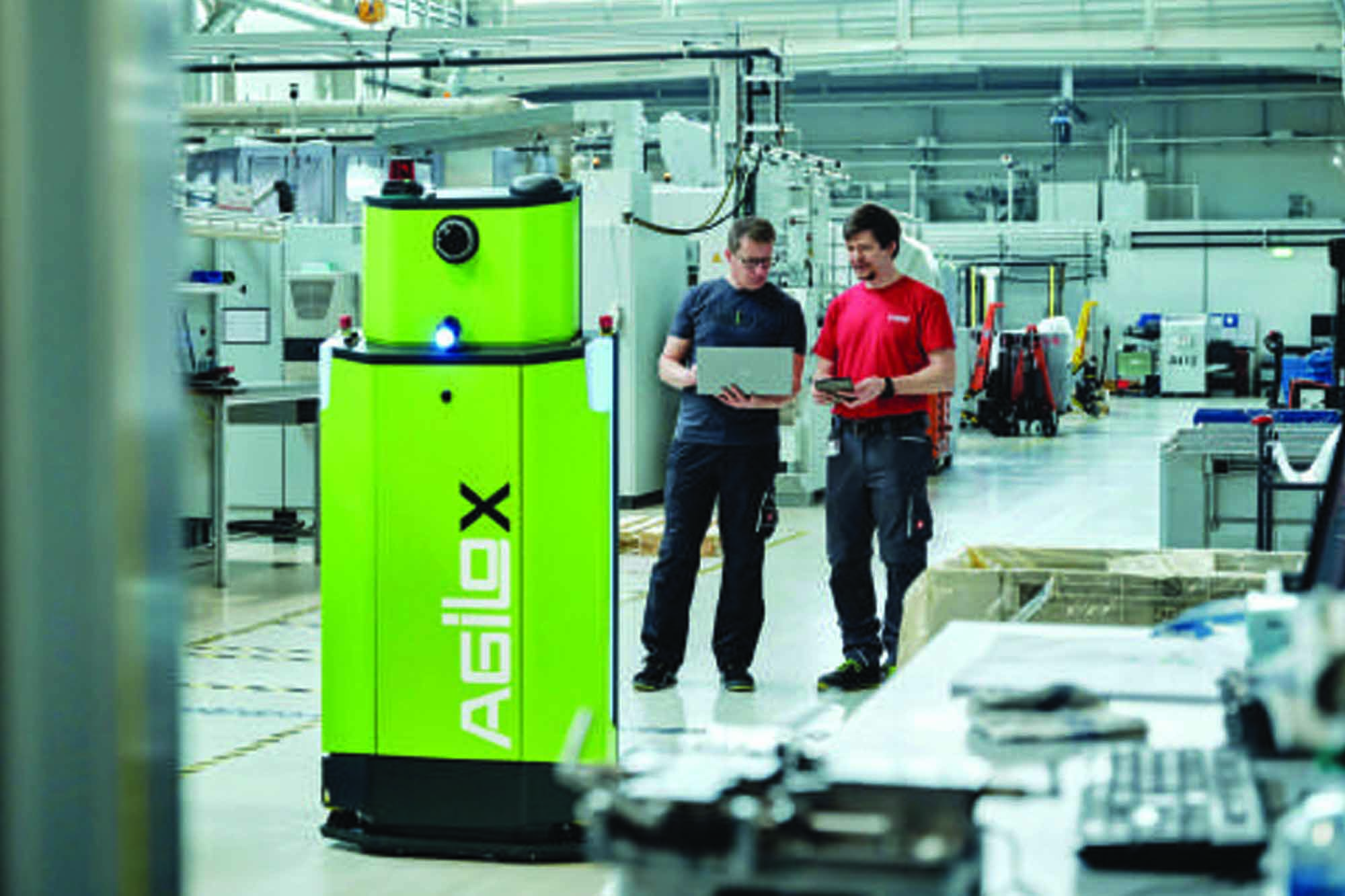
What must system integrators and users remember when planning and operating materials handling systems with Automated Guided Vehicles (AGVs)? It’s not a trivial question – different principles apply to the planning and operating of stationary automated conveyor systems and conventional industrial trucks/forklifts. It’s also a topical question, as AGVs are now frequently integrated into intralogistics processes.
AGVs and industrial service robots are solutions for autonomous, flexible materials transport. They have arrived at the very heart of intralogistics, and the trend is set to continue. Market research institute Mordor Intelligence has predicted that between 2023 and 2028, Europe’s AGV market will grow by around 19 percent each year.
This is also due to the high level of market differentiation. The spectrum ranges from mini-vehicles for smaller containers to heavy-duty AGVs with capacities of several hundred tonnes. There is also a proliferation of autonomous mobile robots (AMRs) with additional degrees of autonomy, used in a wide variety of areas, from the automotive industry to mechanical engineering, parcel logistics to heavy industry, and even hospitals.
The challenge
From an occupational health and safety perspective, this is an exciting and challenging development. AGVs often have to move in the same workspace as personnel, and because they are automated vehicles, special safety precautions need to be taken and certain requirements satisfied. This is often new territory for users, and it is undoubtedly challenging.
Many incomplete machines
The starting point is the definition of a ‘machine’ under the Machinery Directive. It’s no trivial question. By definition, AGVs are typically supplied as incomplete machines. At the same time, the complete system must be regarded as an ‘assembly of machinery’, which requires a certificate of conformity. The party responsible for ensuring this, whether the manufacturer or system integrator, must be determined early on.
Standards: Manufacturer’s perspective
The requirements for the safety of AGVs are more complex than those for other transport and conveyor systems as AGVs have to take both the Machinery Directive and its subordinate standards (i.e. the perspective of the manufacturer) as well as the occupational health and safety regulations of the respective facility (i.e. the perspective of the operator) into consideration.
For manufacturers of AGVs and complete systems, C-standard EN ISO 3691-4 Industrial trucks-Safety requirements and verification-Part 4: Driverless industrial trucks and their systems have been in effect since the end of 2020. The standard replaced EN 1525, which had been in effect since 1997 and had ceased to reflect the state of the art.
The new standard specifies the requirements for AGVs, transfer stations, and the system. It distinguishes four operating areas: operating area, operating hazard area, restricted area and closed area. Defined safety requirements must be satisfied for each of these four areas. These requirements include safety clearances, travel speeds, safety markings, and active and passive personnel detection equipment specifications.
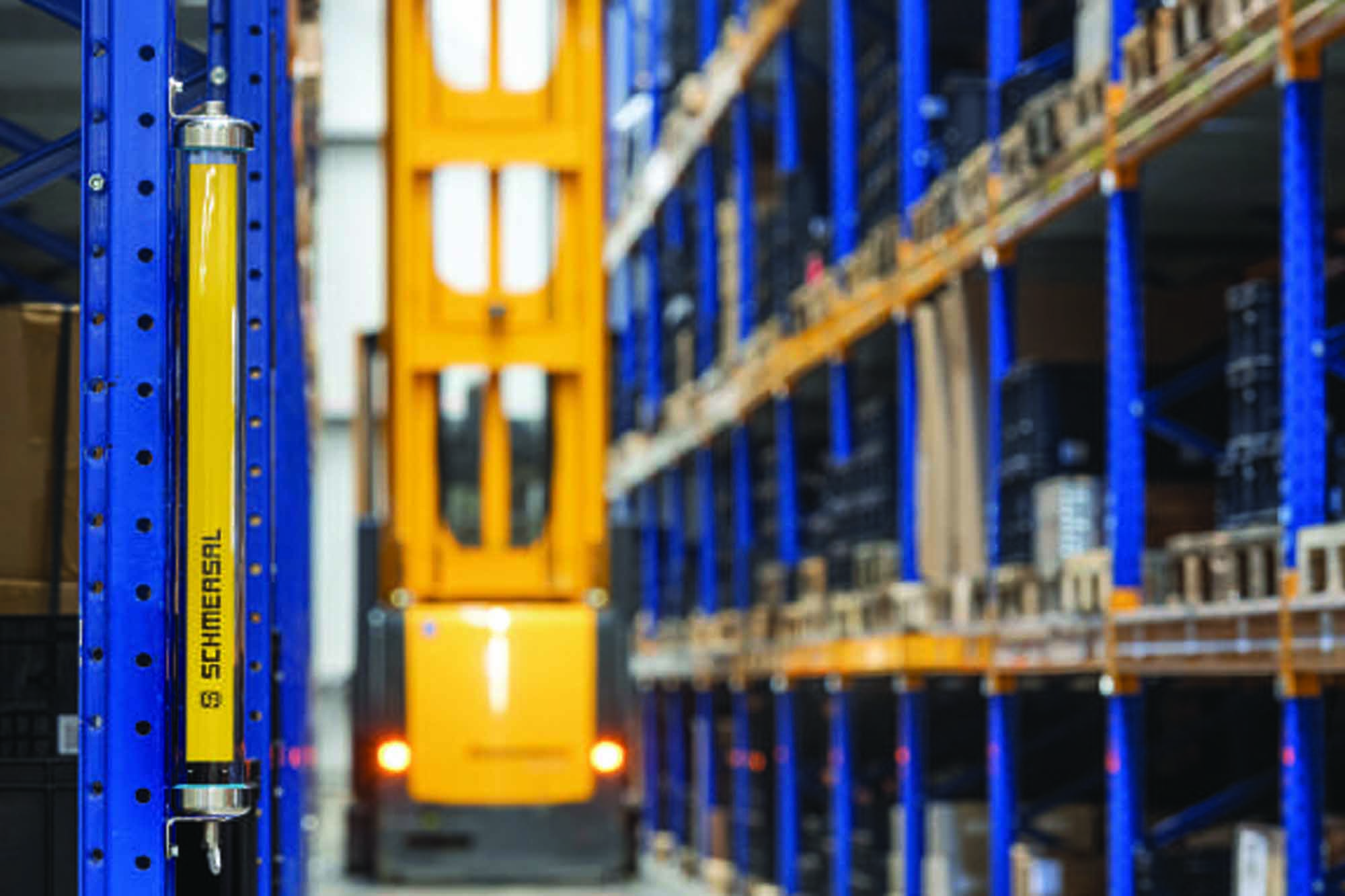
Requirements:
Operator’s perspective In contrast to other automated systems, AGVs work at the heart of production, with no safety fences or delineated working areas. This means that the occupational health and safety regulations of the production facility in which they are used apply to their integration into the production environment.
As an example, the Operational Safety Ordinance applies to AGV applications in Germany. Subordinate to these are the technical regulations (TRs) ‘ASR1-2 Room dimensions and movement areas’, ‘ASR-A1-8 Traffic routes’ and ‘ASR-A2-3-1 Escape routes and emergency exits, escape and rescue plan’. These TRs must be taken into consideration, as integration of an AGV could have an impact on their requirements.
Annex A, tables 1 and 2 of DIN EN ISO 3691-4 describe all relevant relationships with clearance dimensions, active/passive personnel detection equipment, permissible speeds, markings and restart procedures.
Central safety function: Personnel detection systems
Quite understandably, a central safety function of AGVs is personnel detection. This ultimately decides whether an AGV detects a person working in the area of the planned route and responds accordingly, e.g. by stopping or modifying its route. ISO 3691-4 (see above) requires.
Performance Level (PL) ‘d’ (PLR = d) for this particular function. The standard also specifies test requirements for upright and horizontal obstacles. It also imposes requirements on warning systems, emergency-stop devices, operating modes, load handlers, towing and trailer operation, and technical documentation and operating instructions.
Prioritise machinery and operational safety early in the process
The brief overview shows that from the perspective of machinery safety, the planning and commissioning of an AGV require a different approach than the planning of conventional conveying technology. The complete machine must be planned with all aspects of machinery safety and operational safety taken into account. The task is thus more complex than other internal conveyor and transport technology systems. Since planning often involves different partners (e.g., the AGV manufacturer and a system integrator), tasks must be distributed. An important aspect: Employee training It is also important to note that when planning AGV-supported intralogistics, the requirements for the operator organisation and awareness-raising amongst employees play a vital role in the safety of the complete system than is the case with other automated systems and machinery – precisely because the use of AGVs involves man and machine working alongside one another.
Employee training is thus becoming increasingly important. Practical experience shows that AGV cross-traffic with forklift trucks must also be considered. Due to the safety technology in place, AGVs are capable of avoiding accidents. Still, collisions between AGVs and forklift trucks are commonplace. Why? When a forklift truck operator is transporting goods on pallets, his ability to see flat-bodied AGVs ahead of the truck is limited. Training is an effective way to minimise this risk.
Author by Marcel Bogusch, Industry manager for intralogistics at K.A. Schmersal GmbH & Co. KG, Wuppertal.
For more information, visit: https://www.schmersal.com/en/home/
Cookie Consent
We use cookies to personalize your experience. By continuing to visit this website you agree to our Terms & Conditions, Privacy Policy and Cookie Policy.