A game-changer for remote construction challenges
By Edit Team | April 12, 2024 12:49 pm SHARE
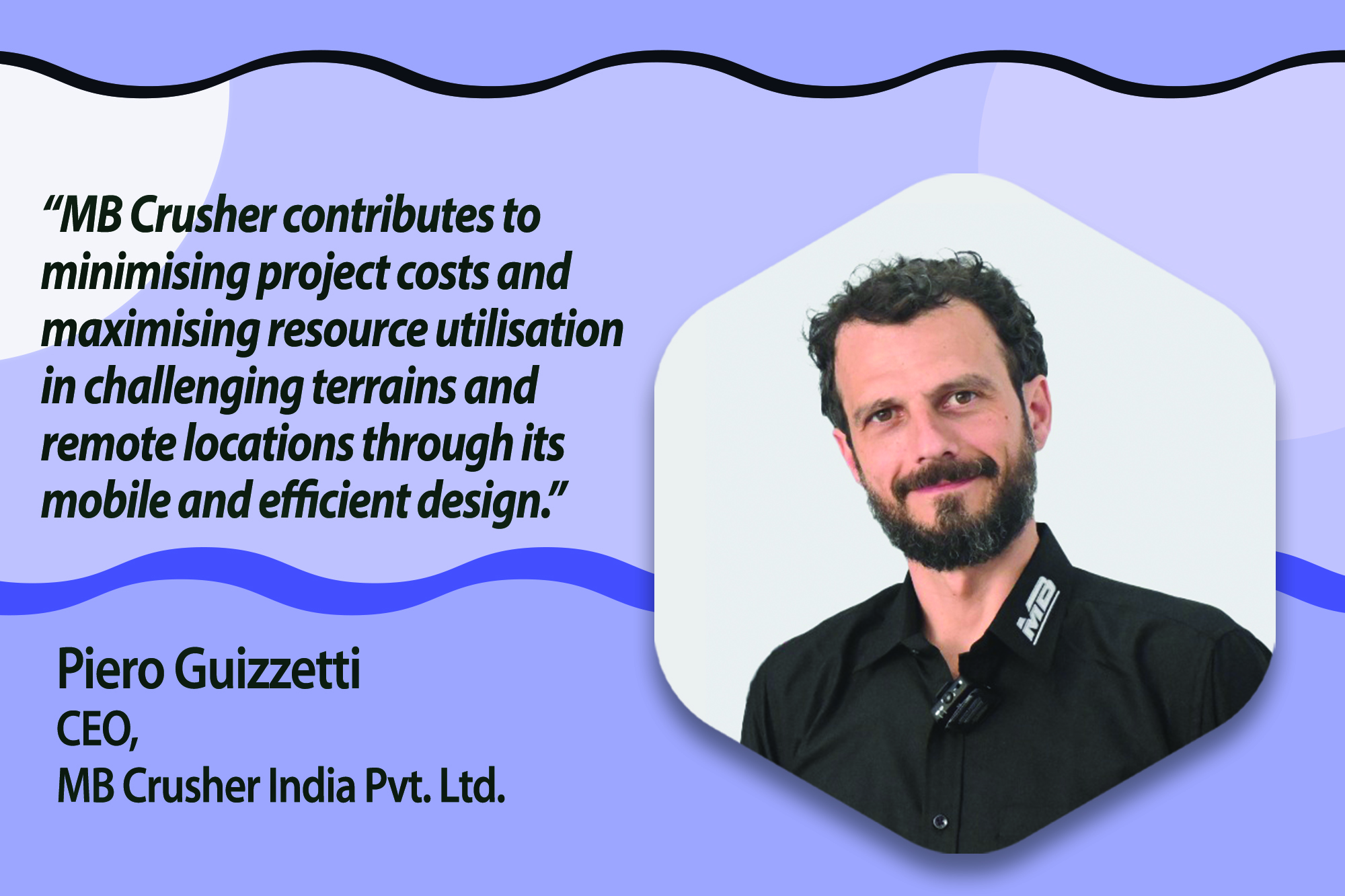
In this interview, MB Crusher unveils its pioneering solutions tailored for remote and rugged construction challenges. It showcases how its innovative approach is reshaping project dynamics in extreme environments.
Can you provide insights into how MB Crusher is uniquely suited to address the challenges posed by rugged terrains and high altitudes, as evidenced in the ground-breaking project in Kaza, Himachal Pradesh?
MB Crusher’s crusher buckets are uniquely tailored to excel in rugged terrains and high altitudes, as demonstrated in the ground-breaking project in Kaza, Himachal Pradesh. The value of MB products exponentially increases as the degree of remoteness or difficulty of reaching a site increases. That is because the alternate solutions become increasingly non-feasible from a technical perspective, and transportation costs increase accordingly. On the other hand, MB crushers can crush, screen, and trench trench any material directly at the site, thereby being completely independent of all aggregate requirements. Furthermore, MB machines are designed with robustness and adaptability, allowing them to operate efficiently even in the most challenging conditions. Their compact and agile construction enables easy manoeuvrability, crucial for navigating rough terrain. Moreover, MB Crusher boasts advanced crushing technologies that optimise performance while minimising downtime, ensuring continuous material production despite environmental obstacles. This versatility and resilience make MB Crusher the ideal solution for addressing the challenges of remote and demanding construction sites like Kaza.
How does MB Crusher ensure precision and efficiency in material production for concrete and GSB work, particularly in remote locations with limited access to traditional crusher plants?
MB Crusher ensures precision and efficiency in concrete material production, and GSB (Granular Sub Base) works through its innovative design and cutting-edge technology. Our patented elliptical motion jaw crusher technology optimises the precision of the output material, both in terms of consistency and quality. In remote locations where traditional crusher plants may not be accessible, MB Crusher offers a mobile and versatile solution that can work independently at the site with no additional cost or resources. Their ability to directly process materials on-site eliminates the need to transport materials to stationary plants, reducing logistical challenges and costs. All that is required in the excavator and the operator would be necessary for any other alternate solution.
Additionally, MB Crushers are equipped with features such as adjustable jaws and screening capabilities, allowing for precise control over the size and quality of output materials. Hence, MB products can also adapt to the customer’s varying and changing requirements. This ensures that construction projects in remote areas receive high-quality materials tailored to their specific requirements, enhancing overall efficiency and productivity.
Could you elaborate on the advantages of utilising MB Crusher over static crusher plants regarding project completion timelines and resource optimisation, as demonstrated in the Kaza project?
Unlike traditional static plants that require large capex spending, significant setup time and infrastructure, MB Crusher can commence operations from the project’s outset. There is no grid connectivity, generator, or added machines or resources. Just a base machine and an operator are genuinely it. This early initiation accelerates the production of essential materials, shortening project timelines and reducing overall costs. Additionally, MB Crusher are highly mobile and versatile, requiring minimal space and infrastructure, which translates to lower operational expenses and enhanced resource utilisation. Last, whereas static crushers require transportation to and from MB, the crushing unit moves in tandem with all other operations. MB Crusher offers a more efficient and cost-effective solution for completing construction projects in remote locations like Kaza by streamlining the crushing process and eliminating the need for extensive setup.
How does MB Crusher ensure seamless integration and compatibility with various heavy machinery, such as excavators, loaders, and backhoe loaders, to meet the diverse needs of construction projects?
These crushers are designed to be easily attached to a wide range of heavy machinery, including any brand and model excavator, loader, and backhoe loader, which offers versatility and flexibility in construction applications. The integration process is streamlined and straightforward, allowing quick setup and operation. Furthermore, MB Crusher’s crusher buckets are equipped with adjustable jaws and attachments, enabling them to adapt to different machinery and construction tasks. This compatibility ensures that MB Crusher can meet the diverse needs of construction projects, regardless of the equipment available on-site, thereby maximising efficiency and productivity.
Can you discuss the specific features and capabilities of MB Crusher’s BF90.3 Jaw Crusher and MB-S18 Screening Bucket that contributed to the success of the Kaza project, particularly in terms of material processing efficiency and cost optimisation?
The BF90.3 Jaw Crusher and MB-S18 Screening Bucket offered by MB Crusher played pivotal roles in the success of the Kaza project, particularly in terms of material processing efficiency and cost optimisation. The BF90.3 Jaw Crusher is renowned for its high productivity and versatility, which makes it capable of quickly crushing various materials. Its adjustable jaws allow for precise control over the size of output materials, ensuring uniformity and consistency in production. On the other hand, the MB-S18 Screening Bucket efficiently separates and screens materials, eliminating debris and contaminants to produce clean, high-quality aggregates. Together, these two components of MB Crusher’s equipment lineup contributed to the efficient processing of materials for concrete, and GSB work in the Kaza project, resulting in improved productivity and cost savings.
In what ways does MB Crusher contribute to minimising project costs and maximising resource utilisation, especially in challenging terrains and remote locations where traditional crushing methods may not be feasible?
MB Crusher contributes to minimising project costs and maximising resource utilisation in challenging terrains and remote locations through its mobile and efficient design. By eliminating the need to transport materials to stationary crusher plants, MB Crusher reduces logistical costs and downtime associated with transportation. Moreover, their ability to directly process materials on-site ensures a continuous and reliable supply of materials, reducing dependency on external suppliers and mitigating delays. Additionally, MB Crusher are designed for durability and longevity, minimising maintenance and operational costs over the lifespan of the equipment. This efficient use of resources and streamlined operation makes MB Crusher an ideal choice for construction projects in remote and demanding environments where traditional crushing methods may not be feasible or cost-effective.
Cookie Consent
We use cookies to personalize your experience. By continuing to visit this website you agree to our Terms & Conditions, Privacy Policy and Cookie Policy.