Achieve welding efficiency through robotic systems and automation
By Staff Report | August 13, 2024 3:51 pm SHARE
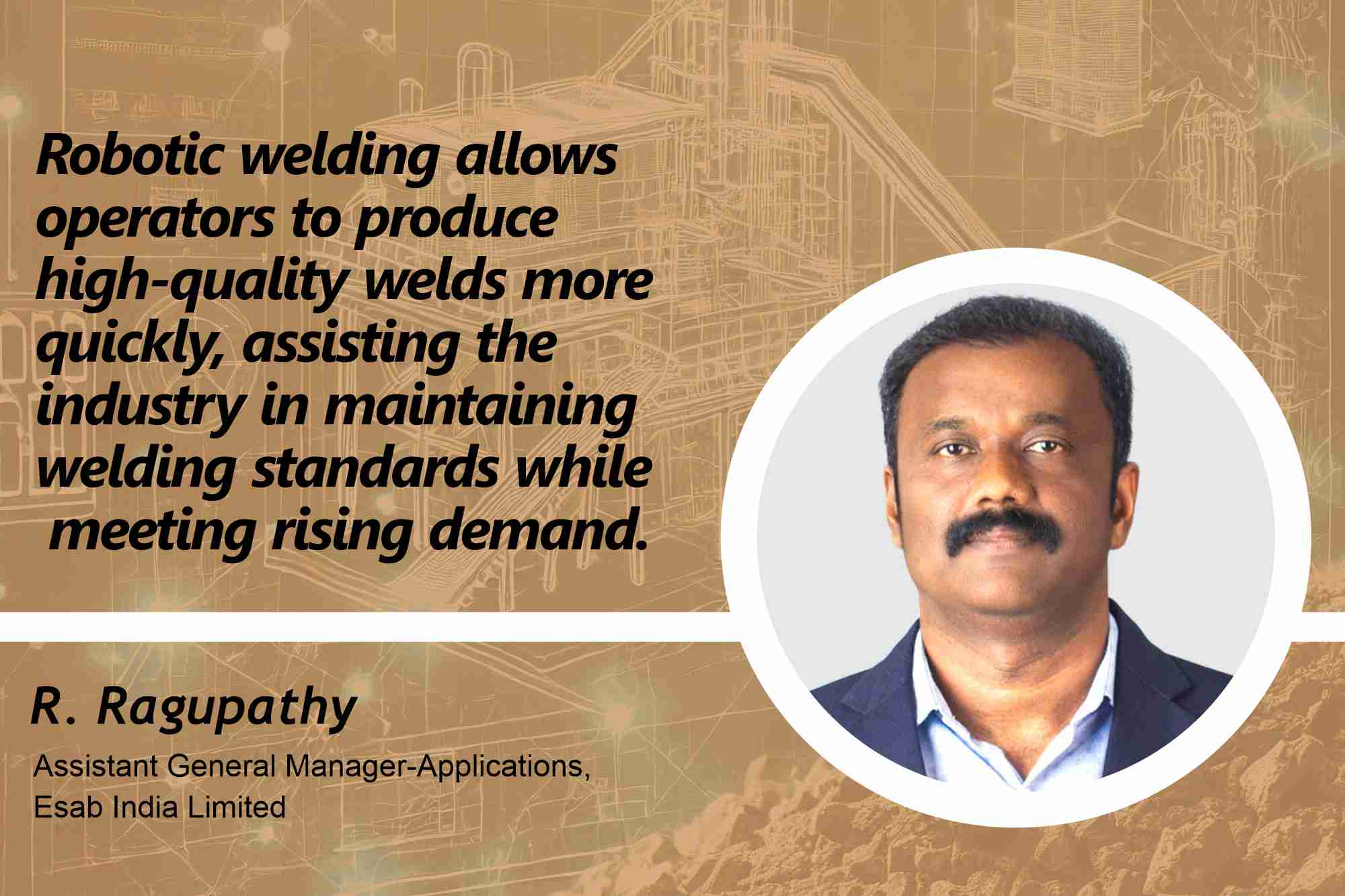
Integrating automation and robotic welding technologies into operations increases flexibility, productivity, and safety. These innovations assure precise welds, reduce downtime, satisfy growing demand, and improve welding quality.
What pre-treatment methods do you employ to optimise material properties before welding, and how do these methods vary across different metals?
Pre-treatment phases are crucial for getting the appropriate weld quality. The procedures used vary depending on the type of metal welded and its specific features and characteristics. For steel, rigorous pre-treatment entails degreasing and rust removal, often accomplished mechanically using sanding or wire brushes and grinding. Aluminium preparation eliminates oxide layers that build quickly when exposed to air due to its high thermal conductivity. Chemical cleaning and scraping away oxides with a stainless-steel brush or aluminium wire are common techniques. Stainless steel requires special care to prevent chromium depletion and maintain corrosion resistance. Mechanical cleaning removes iron impurities and restores the passive film on the surface while avoiding contamination.
How do you integrate automation or robotic welding systems into your workflow, and what benefits have you observed from their implementation?
Modern welding processes benefit from advanced automation and programming capabilities, which increase flexibility and productivity. Advancements in robotic welding have had a favourable impact on the industry, including improved workflow, increased safety, and material savings.
Manufacturers improve quality by eliminating human mistakes and ensuring weld precision. New programming abilities enable operators to optimise robots and weld parameters, allowing them to effectively complete a specific set of duties while being remotely monitored to ensure quality standards are fulfilled. Another advantage is increased safety since robotic technologies help prevent welding injuries and equipment damage, improving the overall safety of welding processes. Improved productivity is also realised, with precision and consistency being the key goals of programming technology in modern welding equipment, allowing enterprises to reduce downtime while increasing production dramatically.
Rather than addressing the constraints of hand welding, both large and small-scale industries profit from improved robots that automate regular welding activities. This enables operators to concentrate on weld programming and specialised applications.
In what ways do you minimise environmental impact during cutting and welding operations?
Welding and cutting processes are common in practically every sector. Several typical procedures are used to reduce their environmental impact, particularly concerning waste management and emissions. These include using environmentally friendly welding methods and high-quality equipment that maximises the use of heat and consumables. Welding electrodes and filler wires are now made from recycled and recyclable materials. Fume extraction systems remove toxic compounds from the air, safeguarding both the environment and workers, and the filtered dust must be disposed of properly to avoid environmental damage. Dust-collecting systems equipped with proper filters and protective mechanisms reduce the risk of fire or explosion. Furthermore, gas optimisation systems equipped with contemporary digital controllers improve the utilisation of shielding gases.
How do you identify and mitigate potential risks associated with cutting and welding activities on-site, especially in dynamic construction environments?
With the extensive use of welding in the construction industry, various hazards arise, necessitating a thorough grasp of safety precautions. Wear and tear are common causes of damage to electrical wires and joints. Taking appropriate precautions to prevent cable damage and replacing broken cables regularly helps reduce risks. The intense light from welding arcs emits hazardous UV and IR light that can cause eye injuries, but using welding helmets with the appropriate filter lens shade helps reduce this risk.
Overexposure to welding fumes and gases is a health risk, so construction sites need proper ventilation or exhaust systems. Powered Air Purifier Systems (PAPR) that provide filtered fresh air are crucial for welders’ safety in confined spaces. Welding spatter can occur in suboptimal settings, often due to productivity pressures or a lack of awareness. Advanced equipment with spatter-reducing technologies and digital controls, along with proper protective gear, can help prevent fires caused by spatter.
Emphasis on awareness training and regular safety audits can continuously help to improve safety measures for increased protection.
For more information, visit: https://esab.com/in/ind_en/
Cookie Consent
We use cookies to personalize your experience. By continuing to visit this website you agree to our Terms & Conditions, Privacy Policy and Cookie Policy.