Achieving hydraulic safety standards with Atos
By Staff Report | April 17, 2025 5:40 pm SHARE
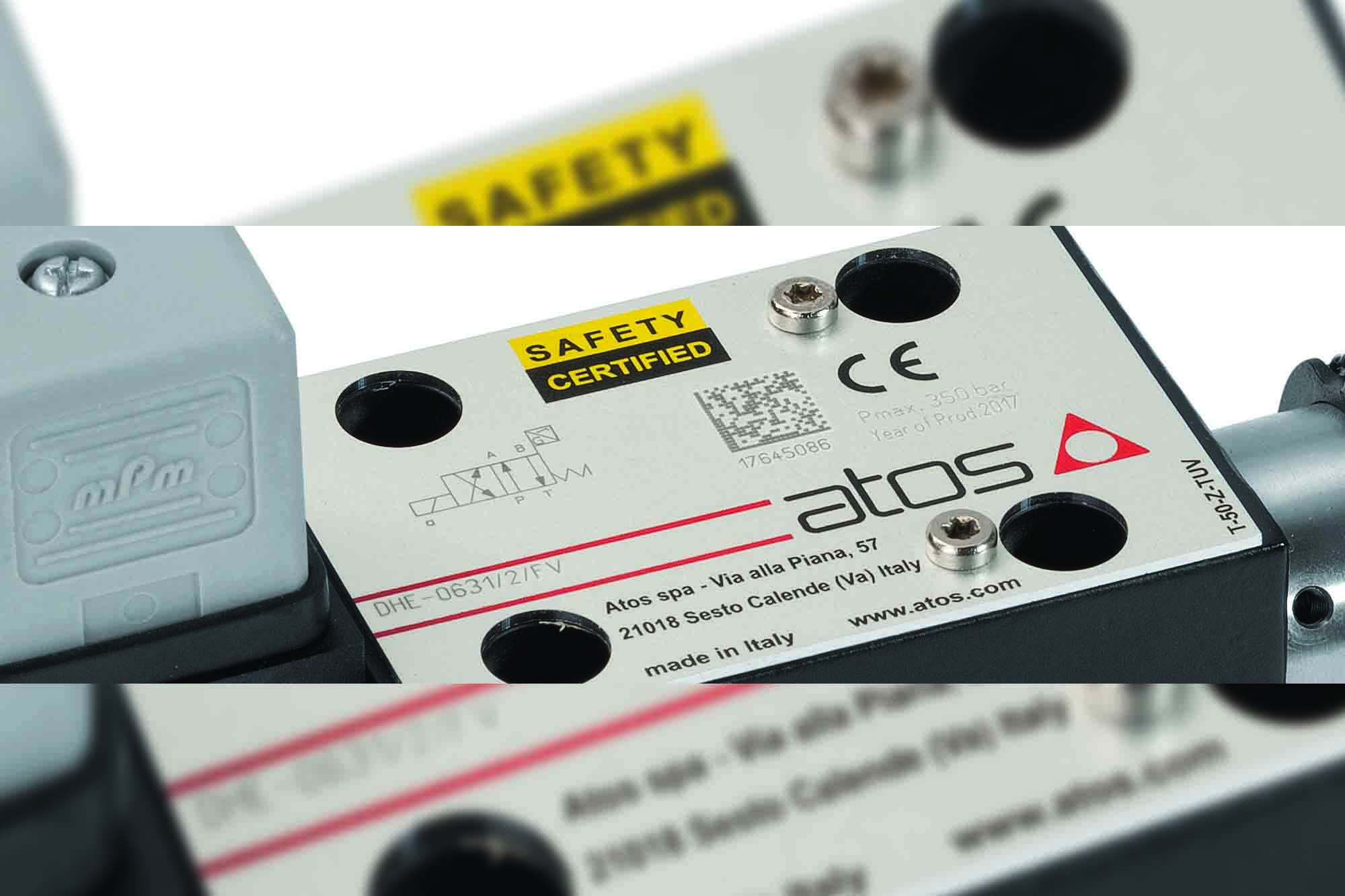
Ensuring safety in hydraulic machinery through compliance with the Machinery Directive 2006/42/EC.
The Machinery Directive 2006/42/EC is a critical piece of legislation that establishes the safety standards for machinery and equipment in the European Union. The directive establishes specific safety measures and guidelines that manufacturers must follow when designing, manufacturing, and commissioning hydraulic equipment. These measures include using safety valves to promote a safer working environment and maintaining machinery operational efficiency.
Understanding machinery directive 2006/42/EC
The Machinery Directive 2006/42/EC and the relevant harmonised standards IEC 61508 Safety Integrity Level (SIL) and ISO 13849 Performance Level (PL) define the general principles of machine safety that manufacturers must consider to reduce risks associated with machine operation.
Established by the European Union, the Machinery Directive 2006/42/EC is a cornerstone of equipment safety in its member countries. This directive establishes critical guidelines for operators’ health and safety requirements for machinery throughout its entire lifecycle, from initial installation and ongoing maintenance to eventual disposal. By meticulously addressing different safety aspects, the directive ensures that machinery is designed and manufactured with the operator’s well-being as the top priority.
ISO 13849 and IEC 62061 are crucial harmonised standards ensuring hydraulic system safety. These standards provide manufacturers with a framework for assessing and mitigating risks by considering factors such as component reliability, control system architecture, and the severity of potential hazards.

When evaluating the effectiveness of hydraulic system safety measures, two key concepts to consider are Performance Level (PL) and Safety Integrity Level (SIL). These levels assess the ability of safety functions to carry out their intended tasks under specific conditions. By assessing these factors, manufacturers can determine the appropriate PL/SIL for their specific hydraulic system, ensuring the safety measures are adequate for the intended application.
Understanding the Machinery Directive 2006/42/EC provides industrial engineers with the knowledge and insights required to revolutionise the functional safety of hydraulic systems. This will result in increased reliability, improved performance, and, ultimately, a safer industrial environment for operators.
The role of safety valves in hydraulic systems
As functional safety becomes more important across industries, a thorough understanding of safety valves’ critical role and contribution to ISO 13849 and IEC 62061 compliance becomes even more important.
Safety valves are designed and tested to meet stringent safety standards and regulations, ensuring hydraulic systems’ overall safety and dependability. They are designed with advanced features like monitoring systems and fail-safe mechanisms to ensure the highest level of safety. In practice, safety valves aid in limiting potential hazards to equipment or operators by preventing dangerous movements of electrohydraulic axes during production cycles or in emergencies.
However, it should be noted that the overall SIL and PL assessment is not solely based on the characteristics of a single component. SIL and PL assessments consider the entire chain of safety-related components that perform the desired safety function.

Hydraulic system architecture plays a fundamental role.
Safety valves can be integrated into redundant double-channel systems to improve safety while increasing system complexity.
Incorporating safety mechanisms into the system architecture can increase the number and type of faults detected, thereby increasing overall diagnostic coverage.
Atos safety valves
Atos has created a line of safety valves specifically intended for functional safety. They undergo rigorous testing to ensure their quality, dependability, and compliance with industrial safety standards. Atos safety valves come with notified body certification, simplifying machine design and system certification processes.
Atos provides a complete line of on-off valves and cartridges equipped with inductive safety sensors. These sensors monitor the spool or poppet position and are used by the machine’s central unit to confirm the valve’s safe status.
Atos has developed a line of digital proportional valves with onboard electronics designed and certified for functional safety.
Atos proportional safety valves meet safety standards by inhibiting the regulation of proportional valves via on-off enabled signals. The valve sends on-off digital signals to the machine’s central unit to confirm when the safe spool position has been reached.
By understanding and adhering to the Machinery Directive 2006/42/EC, Atos ensures that its safety valves meet the stringent requirements to prevent accidents and protect machinery and personnel. This commitment to safety standards demonstrates Atos’s focus on continuous improvement and innovation, ultimately providing the highest level of hydraulic protection.
For more information, visit: https://www.atos.com/en-in/
Cookie Consent
We use cookies to personalize your experience. By continuing to visit this website you agree to our Terms & Conditions, Privacy Policy and Cookie Policy.