Advanced techniques and practices in welding & cutting
By Edit Team | November 10, 2022 1:55 pm SHARE
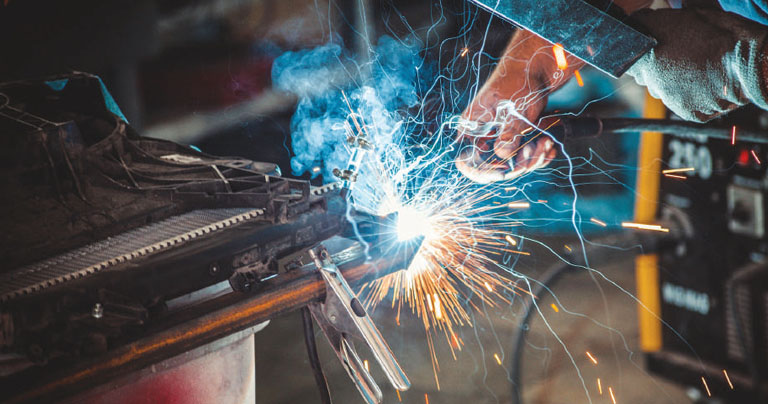
Experts across the welding and cutting industry, solution providers, and training experts discussed transformations happening in the welding and cutting sector. They further stressed upon the need to enhance training and skill development to increase quality welders across the industry.
Cutting and welding are essential components of infrastructure construction. With several new projects for buildings, bridges, dams, industrial structures, and other structures, the Indian construction and infrastructure industry has recently experienced rapid growth. In these projects, metals—particularly structural steel—are employed more frequently, and structural frames are created mostly through welding and cutting. By cutting and fusing various metal components, welding and cutting technologies are routinely used to create structurally sound metal frameworks.
Technological advancement
One of the most crucial goals for the welding business is cost reduction due to its rapid growth and technological development. With real-time data, one can use technology to decrease rework and rejections. Keep an eye on what is happening in the plant daily and identify any shortcomings. In order to increase productivity and eventually reduce costs, the gaps can be filled. Sharing notable innovations in the industry, Nimish Chinoy, Marketing Director, Electronic Devices Worldwide Pvt Ltd., says, “We are into manufacturing of building parts based on IoT. We also have a dedicated product which can be used with any welding power source, which connects to our data monitoring systems to get the online data of current-voltage on time and TPM requirements. Also, induction heating, compared to traditional gas-based ovens, has efficiency improvement, and can produce faster, better and more reliable.”
Whereas throwing the light on technological trends, Amrityoga Mishra, Sr. Manager Marketing, Panasonic Smart Factory Solutions India, says, “Robotic laser welding uses future technology which is under consideration in industry, and we are organising many awareness and training programs, to customers. Currently, the equipment cost is very high. It will be three crores like that single system. So customers become aware of this product and understand its benefits. More installations will start in the coming five years after sufficient awareness has been done to the customers.”
Low carbon Products
The most recent example of effectively manufacturing low-carbon steel products is MIG welding. Arc welding already exists, and MIG welding improves upon it. Arc welding still accounts for over 60 percent of all welding in India, while the country is slowly transitioning to MIG and flux-cored arc welding. As a result, we have a spool that provides continuous welding in place of using a single rod. It resembles a semi-automated welding process. In the manual mode alone, the operator’s deposition rate can reach one and a half to two kgs per arc. Although the code bans it, it is nevertheless permitted to use MIG welding directly for root jobs, good welding works, and short-pressure vessels.
Downtime Issues
Downtime is one of the main concerns in the welding industry. Most companies are trying innovative ways to implement these processes. Explaining the company initiative, Chinoy says, “We have come up with something called Sigma World Pro Series, these are high-end power sources, and they are modular. In welding equipment, we have made a modular technology that means 200- ampere modules can be inserted to make multiple machine capacities. So if there is a 400-ampere machine, then 200-ampere modules are inserted. The advantage is that if something is wrong in one of the modules, my entire machine does not need to stop when the other installed module is used. So this is how we are ensuring downtime is minimised. And even spares are optimised. So even if you have 100 machines, you can store only two or three modules as a pair. If something goes bad, remove the module, put it back, bring that module to the service station, repair it, and get it back online. It doesn’t stop the overall process. Being an Indian manufacturer, we have our service station spanning India. So, our engineers can come on-site to repair the PCBs also.”
Meanwhile, Mishra addresses the downtime issue, saying, “We have our patented design, wherein, inside the machine, there are a few hermetically sealed boxes. Inside each box is a separate hermetically sealed box for PCB, then another box to house the different electronic parts like the IGBT bridge separator. The machine’s unique design is that our fan is installed on the top side for better cooling of the machine. All other competition machines will have the fan on the rear side.”
“It has been designed in Japan to have a better cooling efficiency of the machine. That is how our machine is getting protected from outside dust or metal dust inside the factory, resulting in a longer machine life. These machines are used in hilly regions and sand areas, and because of the protection feature, the machine has a higher life. The machine has been designed for uncertain voltage fluctuations in India. So, machines are designed aptly for Indian conditions.”
Skill Development
Nowadays, all the advanced technologies and equipment require a lot of skill development. So for welders to take appropriate measures like training and development activities, electronic devices to upskill themselves are the need of the hour. Focusing on these skills, Chiinoy says, “One is that the equipment itself must make it easier for the operator to weld. So, the latest technology bar sources have a lot of artificial intelligence, which helps a person get trained faster than before. So, this is all a part of any of the top brands you take today that are given to them. So, the objective is to rescale the welder.”
“Secondly, to upskill the welder is to take him towards becoming an operator of the non-automation or SPM. Now he can sit back in a cabin. You can sit on the chair, observe the arc while the automation is working and take corrective actions. So, we are trying to upskill the welder to an operator by training them in automation and robotics and SPM, thereby reducing the load on the welder. But, no matter how smart we make, the machine still needs to know where to weld, and the operator still needs to see whether it is doing what it was supposed to do. So upskilling for me is allowing them to use better technology to reduce their effort.”
Certifications
Regarding the various welder certification available in the market, Antree K A, Project Manager, Don Bosco Vocational Training Institute, says, “Technical skills need to be certified and approved before its application. Technical skills certification is essential to match up to international standards. Generally, after high school studies in India, eight standard welding learning is allowed. The standard certification available in the country is ITI welder industrial training institute, provided by the Labour and Employment Department by National Council for vocational training. After this, the welders can enrol for a one-year apprenticeship training program.”
“For international certifications, if there is a unifying international body in the welding sector known as the International Institute of welding, they might have in India a franchisee as the Indian Institute of welding that offers all international programs. Don Bosco Tech Cochin is the main activity centre in India wherein every year we have around 50 to 60 welders coming out as international welders.”
“We are trying to upskill the welder to an operator by training them in automation and robotics and SPM.” – Nimish Chinoy, Marketing Director, Electronic Devices Worldwide Pvt Ltd.
“Robotic laser welding uses future technology under consideration in industry.” – Amrityoga Mishra, Sr. Manager Marketing, Panasonic Smart Factory Solutions India.
“Technical skills need to be certified and approved before application.” – Antree K A, Project Manager, Don Bosco Vocational Training Institute.
Cookie Consent
We use cookies to personalize your experience. By continuing to visit this website you agree to our Terms & Conditions, Privacy Policy and Cookie Policy.