Advanced Welding in Shipbuilding
By Edit Team | March 20, 2017 7:01 am SHARE
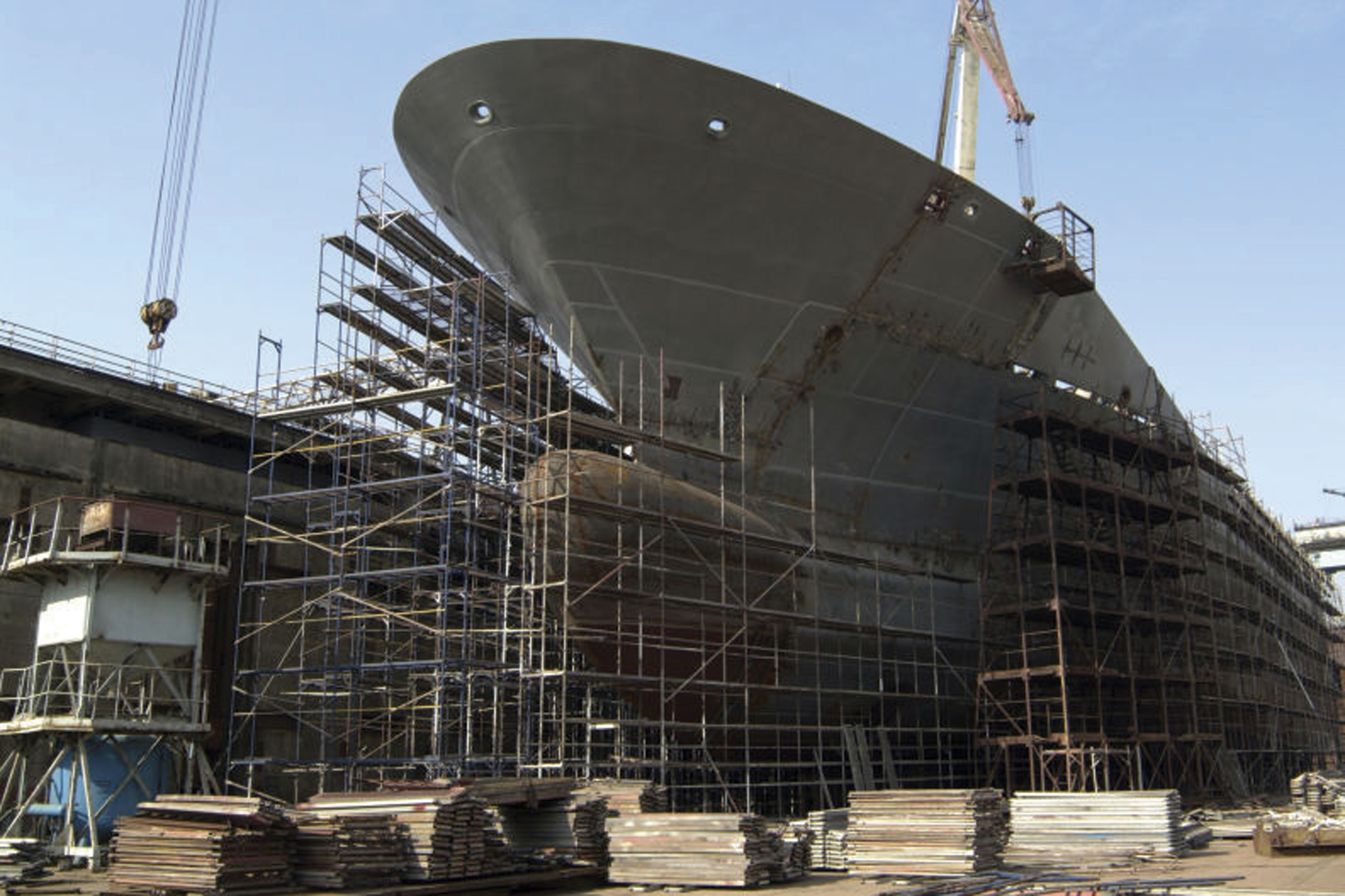
Shipbuilding industry is witnessing sea-change in terms of technological development. Mrugesh V Sutaria, National Sales Manager, Kemppi India Pvt Ltd explains about the advanced welding technologies for this sector.
With the Indian government initiative of “Make in India” and thrust to modernise the defence sector, the Naval and the shipyard sector has opened up to new opportunities. To mitigate new challenges of the sector new high strength material, alloys of aluminium, corrosion resistant steel etc. are constantly being developed.
To weld these materials and to improve productivity, welding industry has taken the challenge and Kemppi is leading from the front in developing sustainable solutions.
Reduced Gap Technology (RGT)
RGT Challenges the conventional joint design principles enabling reliable narrow gap welding of material with thickness upto 30 mm, without need for special equipment or accessories. With welding software WiseFusion and WisePenetration, not only the HAZ is kept to the minimal but also reducing the number of passes resulting in material saving and arc time saving.
WiseFusion welding software keeps the arc stable, improves the control of the weld pool and reduces the magnetic arc blow. This decreases the risk of welding defects, and it results in lower repair costs.
WisePenetration Welding Software keeps the arc power consistent, regardless of variations in the contact-tip-to-work distance. This enables a higher welding speed and deposition rate, and it results in lower labour costs.
Total Welding Management System – Weld Eye
TWMS is a universal solution to manage welding production, improve quality and streamline documentation. It is a complete software application covering welding documentation and quality requirements for welding procedures, welding certificates, Non Destructive Testing (NDT) and process control of your production. It provides value right across the production process. It is a tailored IT solution that simplifies, documents and tracks all your welding related processes. Improving efficiency, documenting quality and driving value creation for all concerned.
• Every weld is 100 per cent traceable afterwards
• Every contractor and all their welders follow the welding procedure
• All standards are followed and all regulations met
• Control over total welding production and quality
• Data collection, data analysis, reporting and documentation are automatised
• WPSs, deviations, and NDT inspections are all in one system
• Multisite managing saves costs and improves total quality
• All the welders have correct and up-to-date qualifications
• Each welder follows the welding procedure
• Risks for welding defects are minimal.
SuperSnake
If distance and access are your problem, then SuperSnake is the answer. The SuperSnake extends the reach of standard Euro MIG welding guns, providing simple distance wire feeding for a variety of filler wires up to 25 m from the wire feed unit. The SuperSnake removes the need to carry large and heavy wire feed units, reducing personnel fatigue, improving safety, and increasing productivity. Negotiating all terrain with ease.
• Suitable for Fe/SS/Al/FMC/MCW filler wire
• Includes voltage and wire speed adjustment
• Large, clear meter display
• Brights LED cabinet lighting
• 10-, 15-, 20-, 25-metre air- and water-cooled models
• Visible safety with tough, bright orange casing
• Gun remote control option.
Mechanised Welding Rail system Mig
A5 MIG Rail System 2500 is the most cost efficient way to improve productivity in mechanised MIG/MAG welding. The system has an inbuilt weaving and rail fastening mechanism with magnets or with vacuum suction cups. With the system one can achieve significant savings for all applications where the weld lengths exceed 2 m or in case of multi-layer welds. In mechanised welding, the welding carriage carries the gun (instead of being held in the operator’s hand), making the arc movement accurate and steady. With unique WISE welding application software and the smart WISE processes provide significant improvements in welding production efficiency.
Authored by_
Mrugesh V Sutaria
National Sales Manager,
Kemppi India Pvt Ltd
www.kemppi.com
Cookie Consent
We use cookies to personalize your experience. By continuing to visit this website you agree to our Terms & Conditions, Privacy Policy and Cookie Policy.