AI innovates welding with precision and reliability
By Staff Report | August 17, 2024 11:32 am SHARE
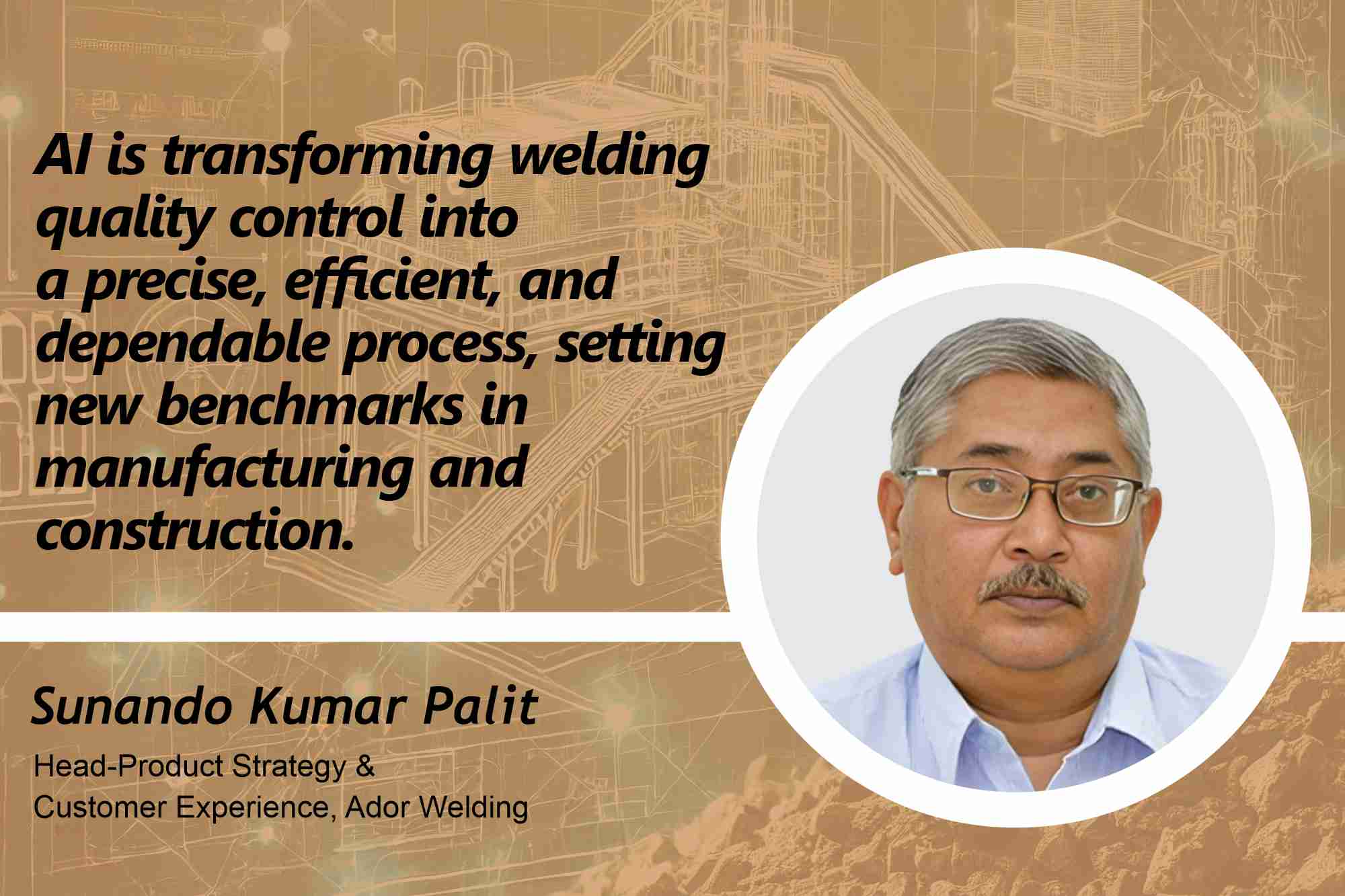
AI integration into welding processes is revolutionising, ensuring that quality, safety, and performance are never compromised. Discover how advanced technologies are transforming welding practices.
Welding is increasingly gaining importance in many industries, such as automotive, aerospace & manufacturing, and construction. With its increasing relevance and use, it is imperative to ensure the quality of weld as it directly impacts the final product’s durability, safety and performance.
The adoption of advanced technologies and artificial intelligence (AI) in welding has been a game changer, offering never-before-seen solutions that enhance precision, competency, and trustworthiness.
Automated visual inspection systems
Until recently, time-consuming manual inspection methods that were prone to human error were used. However, with the advent of AI-powered visual inspection systems, there has been a progressive transformation in the way welding defects are identified. AI-driven systems analyse high-resolution images of welds in real time, identifying imperfections such as cracks, porosity and misalignments with accuracy. These use the power of machine learning algorithms and continuously learn and improve, performing with precision.
Predictive maintenance and monitoring
AI is also being used to reduce downtime and achieve higher-quality welds by effectively using predictive maintenance and monitoring of welding equipment. The machine-embedded sensors have data that can be analysed to predict potential issues, thus allowing time to schedule maintenance before an actual breakdown. The AI system also analyses data that detect wear and tear, leading to repair/ maintenance before machine failure.
Robotic welding assistants
Robotic welders can be programmed to handle a variety of simple and complex joints. Together with AI, the robots ensure precision on each weld as they adapt to variations in materials and joint configurations. This results in quality welds, increased productivity, and reduced need for manual intervention.
Adaptive welding control systems
AI-driven adaptive control systems are designed to modify welding parameters dynamically to compensate for variations in materials, thickness, and joint configurations. These systems use real-time feedback to maintain optimal welding conditions, resulting in higher-quality welds with fewer defects. Adaptive control systems ensure that each weld meets stringent quality standards by continuously adjusting parameters such as voltage, current, and travel speed.
Data-driven quality assurance
AI plays a big role in data analysis, identifying patterns and correlations. This helps pinpoint the root cause of defects and recommend process improvements. This data-driven approach allows for continuous improvement, hence reducing the occurrence of defects over time.
Non-destructive testing (NDT) enhancements
AI is also revolutionising non-destructive testing methods used to inspect welds without causing damage. Techniques such as ultrasonic testing, radiography, and thermography are enhanced with AI algorithms that improve defect detection accuracy and reduce inspection times. AI-driven NDT methods ensure that welds meet quality standards without compromising the integrity of the welded structures.
Smart welding helmets
Smart welding helmets (equipped with AI) provide welders with real-time feedback and guidance, enhancing the weld’s quality. These helmets monitor the welding process using sensors and cameras and display information directly to the welder. This is useful in avoiding errors and maintaining proper technique.
AI applications in welding for quality control are transforming the industry by increasing accuracy, efficiency, and safety. AI enables more precise and reliable welding processes, from automated visual inspections to smart welding helmets. As AI technology evolves, its integration into welding quality control will only grow, leading to further advancements and innovations. The adoption of AI-driven solutions enhances weld quality and contributes to overall operational efficiency, ensuring that industries can meet the high demands of modern manufacturing and construction.
For more information, visit: https://www.adorwelding.com/
Cookie Consent
We use cookies to personalize your experience. By continuing to visit this website you agree to our Terms & Conditions, Privacy Policy and Cookie Policy.