An addressing system for long conveyors in heavy industries
By Edit Team | October 31, 2023 3:22 pm SHARE
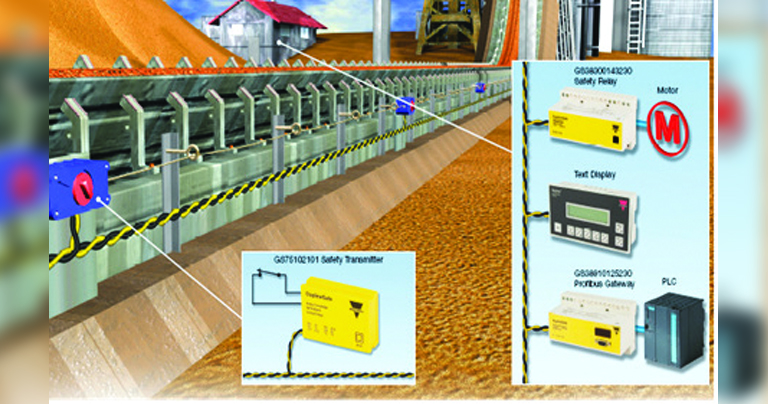
Long conveyors, necessary for heavy industries, can range from a few metres to many kilometres. Identifying problems or activated switches becomes more difficult as they grow longer. In an emergency, traditional procedures fall short. However, addressing systems that use a two-wire bus system are revolutionising extended conveyor management. This article investigates their relevance and real-world implications.
Locating defects or identifying the activity
Long-distance conveyors are outfitted with various instruments, including emergency stops at regular intervals, pairs of belt misalignment switches every fifty metres, zero-speed switches, belt speed sensors, encoders, and other components. As the conveyor length increases, so does the number of switches and instrumentation components. However, this can make it challenging to locate defects or identify the activity of a single switch along the long conveyor. As a result, implementing an addressing system in lengthy conveyors is critical to ensuring quick replies and optimal system functionality.
This article is divided into sections, explaining the significance of addressing systems. The second portion investigates the available addressing strategies, and the third section presents case studies of applications that use these systems, providing insights into their contributions to boosting efficiency and minimising downtime.
Conveyors are essential in heavy industries, facilitating material handling duties ranging from a few metres to several kilometres. We’ve completed projects in India, including conveyors as long as 22 kilometres. Finding defects in such large conveyor systems can take time and effort. Traditionally, operators wire groups of 5-6 switches together and treat them as a single digital input group. Even with this structure, finding defects remains difficult, especially in an emergency.
An addressing system
Adding an addressing system for the switches along these conveyors, linked into a two-wire bus system, substantially aids in finding defects from a centralised control room. This technology recognises the quantity and location of actuated switches and generates alarms, allowing for quick problem solutions.
Furthermore, installing addressing systems improves overall plant efficiency and output. Also, these systems can be readily connected with Industry 4.0 solutions, allowing for data logging from the switches. This data can be used for analytics, analysing the operational trends of specific switches, asset management, and maintaining a detailed history of switch activities.
In this context, an address is a standardised piece of information used to define a location, making identification easier and aiding in the precise location of defects.
Concept
Addressing is assigning a unique code or number to the location of a switch, which is then monitored by a specific operation. In the case of long conveyors, a sensor module assigns an address to each switch along the conveyor, and this information is sent to a controller through a two-wire bus system.
Technologies
Various addressing systems, classified as safe or standard addressing systems, are used globally for switches on lengthy conveyors. We are actively developing the following technology for addressing switches along long conveyors:
Safe Addressing System: In partnership with a global vendor, we created a safety addressing system for Industrial Applications that uses a versatile bus. This bus can transmit analogue and digital data across lengths of up to ten kilometres. Its modules are simple to configure and do not require any extra protocols. This system is widely utilised in mining to improve safety through ventilation, illumination, and conveyor control applications.
Standard Addressing System: Schmersal India has created a standard addressing system based on a two-wire bus system in collaboration with an Indian enterprise. This technology takes advantage of fluctuations in current inside sensors mounted in switches. It can handle conveyor distances of up to 9 kilometres.
AS-Interface (Actuator Sensor Interface): AS-Interface is a manufacturing and process networking solution that connects simple field I/O devices. Various automation equipment providers support it and use a single two-conductor cable. However, its working range is limited to 1.2 kilometres.
Benefits of addressing systems
Addressing systems are essential information technology solutions that support everyday operations in long conveyor systems, and they provide the following significant benefits:
Fault Location: Addressing systems allow for precisely identifying faults along the conveyor.
Enhanced Operator Safety: They help to make conveyor operators safer.
Reduced Errors: The systems reduce information errors, resulting in more reliable processes.
Increased Efficiency: Quicker access to information and more efficient system processes.
Increased Productivity: Increased staff productivity, which benefits the whole process.
Incorporating addressing systems into business and operations provides additional benefits such as correctness, standardisation, user-friendliness, rapid feedback, better efficiency, and profitability.
System implementation
Implementing an addressing system on a lengthy conveyor requires careful planning. The process involves calculating the number of switches to be addressed, designing the system, and determining the number of sensors to be incorporated into the loop. Some addressing systems require an end termination sensor, while others require harmonic filters and repeaters based on the conveyor’s length.
Results and findings
These systems can efficiently meet the most prevalent difficulties faced by industries, notably safety and fault location on lengthy conveyors. Additionally, these systems can be expanded to attain a higher level of automation, complying with Industry 4.0 concepts and easing asset and inventory management.
Conclusion
The integration of addressing systems represents a significant advancement in conveyor technology. This invention speeds up fault identification and improves safety, productivity, reporting, and traceability. Aside from these immediate advantages, addressing systems opens the door to the exciting world of the Internet of Things (IoT), promising even greater gains in efficiency and reliability for lengthy conveyor systems. In an era of rapid technological innovation, adopting modern technology is necessary to ensure a future of outstanding performance and operational excellence.
Cookie Consent
We use cookies to personalize your experience. By continuing to visit this website you agree to our Terms & Conditions, Privacy Policy and Cookie Policy.