Anticorrosive treatment from STP
By Edit Team | December 18, 2014 6:53 am SHARE
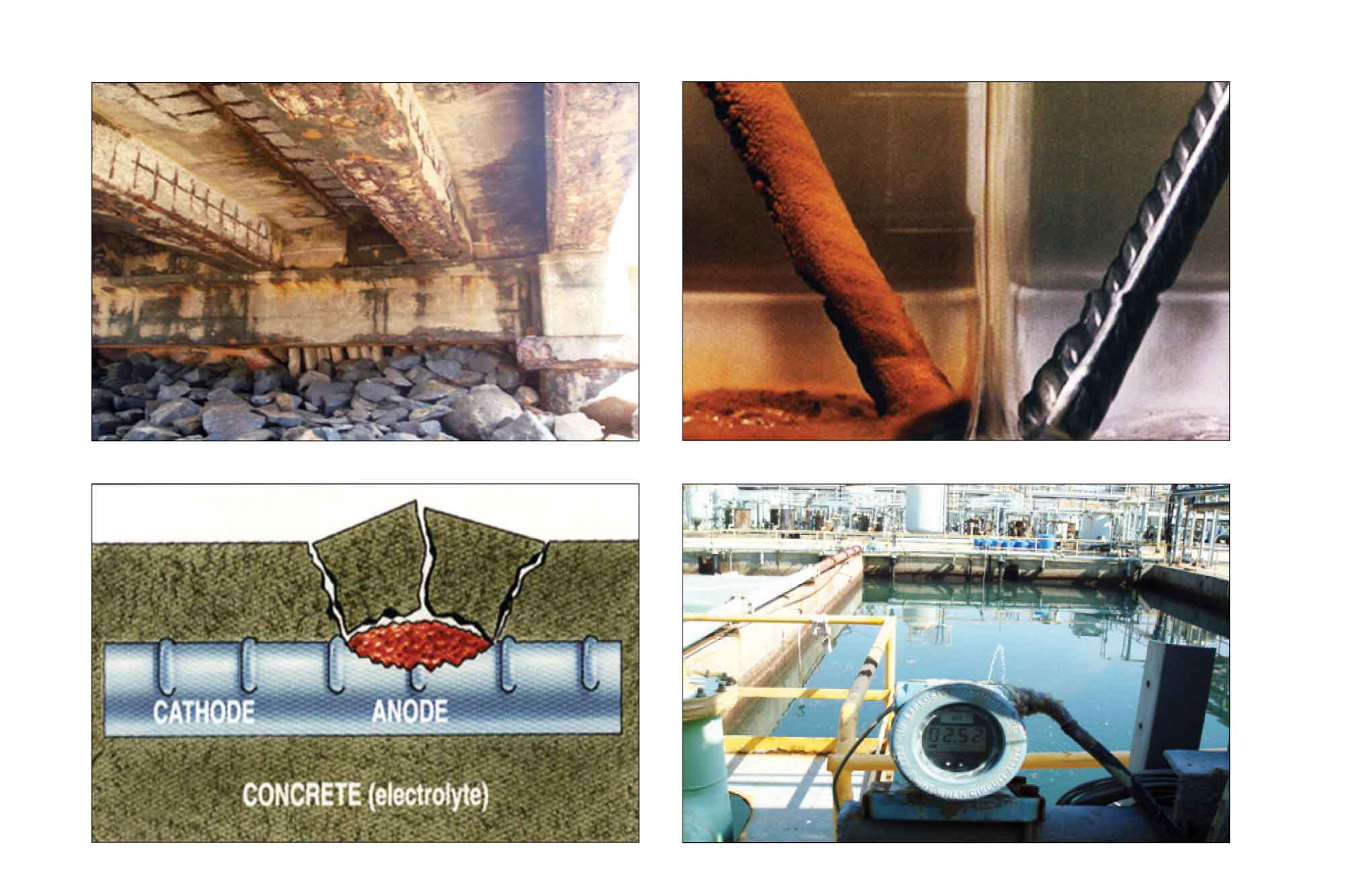
A metallic material or reinforced concrete, exposed to corrosive environments, tends to have chemical reactions with the air/water. The effects of corrosion become evident on the surfaces of these materials. For example, after putting the iron into a corrosive atmosphere for an extended period, the iron starts rusting due to oxygen interaction with water on the iron’s surface. Therefore, metal equipment lacking any preventive (anti-corrosive) measures, may become rusted.
There are a number of methods for preventing corrosion, especially in marine applications. Anti-corrosion measures are of particular importance in environments where high humidity, mist, and salt are factors. The loss due to corrosion in India is to the tune of $40 billion every year, which is about 4 per ecnt of the GDP.
The water penetration helps corrosion of the steel reinforcement. As the rust has more volume then the original steel bar, the rust causes tension in the surrounding concrete. As the cover of concrete is limited on the outer side, the resultant tensile force causes cracks formation and the crack permit more easier entry of water and oxygen to form more rusting that results in more increase in volume and the cracks in concrete get wider and wider. The surrounding concrete becomes partly disintegrated which finally causes spalling.
Corrosion resistant coatings
Corrosion resistant coatings ensure metal components have a longer life. Metal coatings are ideally used coatings in the industry. The function of the coating is to act as a barrier that inhibits contact between chemical compounds or corrosive materials with the metal housing.
STP Ltd. was established in 1935 as a bitumen and Tar based company and diversified into construction chemicals, anticorrosive treatment and many other products, STP Ltd. brings decades of experience to the application of corrosion resistant coatings, along with the advantage of six mega factories and highly experienced staff.
A wide variety of anti-corrosion coatings are available to match the performance requirements of a specific application.
Anticorrosive categories
• Rust remover : ShaliRustoff
• Rust Converter : ShaliPrime RC
• Zinc Rich Primer : ShaliPrime ZnR
• Zinc Phosphate Primer : ShaliPrime Zn Ph
• Micacious iron Oxide : ShaliPoxy MIO
• Novolac based epoxy: ShaliKote NES
• Bituminous coatings : Tank Mastic HB
• Asphalt based coating for automobiles (under body) : SuperKarGard BT
• Coal Tar Epoxy coatings : ShliPrime CTE HB LB
Rusting of reinforcement bars lead to spalling of concrete. Corrosion control of metals is technically, economically, environmentally, and aesthetically important. The good option is to use inhibitors for protecting metals and alloys against corrosion. Lot of people are using migratory corrosion inhibitor (ShaliPlast RCI) in concrete at the time of pouring concrete to prevent rusting of reinforcement bars in the future. These are generally Amine based bipolar migratory corrosion inhibitors
Effect of addition of ShaliPlast RCI, migratory corrosion Inhibitor in concrete block would result in corrosion free rebars.
Protection of concrete from highly corrosive environment in chemical plant can be done by using ShaliKote NES. To protect the reinforced concrete in the neutralisation pit.
Coal Tar Epoxy (ShaliPoxy CTE LB /HB) are quite often used in marine structures like Jetties. Whereas PU coatings (ShaliUrethane PC) are used for metal structures.
Conclusion
When it comes to corrosion protection, different kinds of materials are available. The usage depends on the kind of environment the structure is exposed. Choosing the right methodology for the treatment is very important.
Authored by-
Hasan Rizvi,
Vice President,
STP Ltd.
Cookie Consent
We use cookies to personalize your experience. By continuing to visit this website you agree to our Terms & Conditions, Privacy Policy and Cookie Policy.