Ashok Leyland Gensets: Leading the way with top fuel efficiency and high-demand application excellence
By Staff Report | October 21, 2024 2:31 pm SHARE
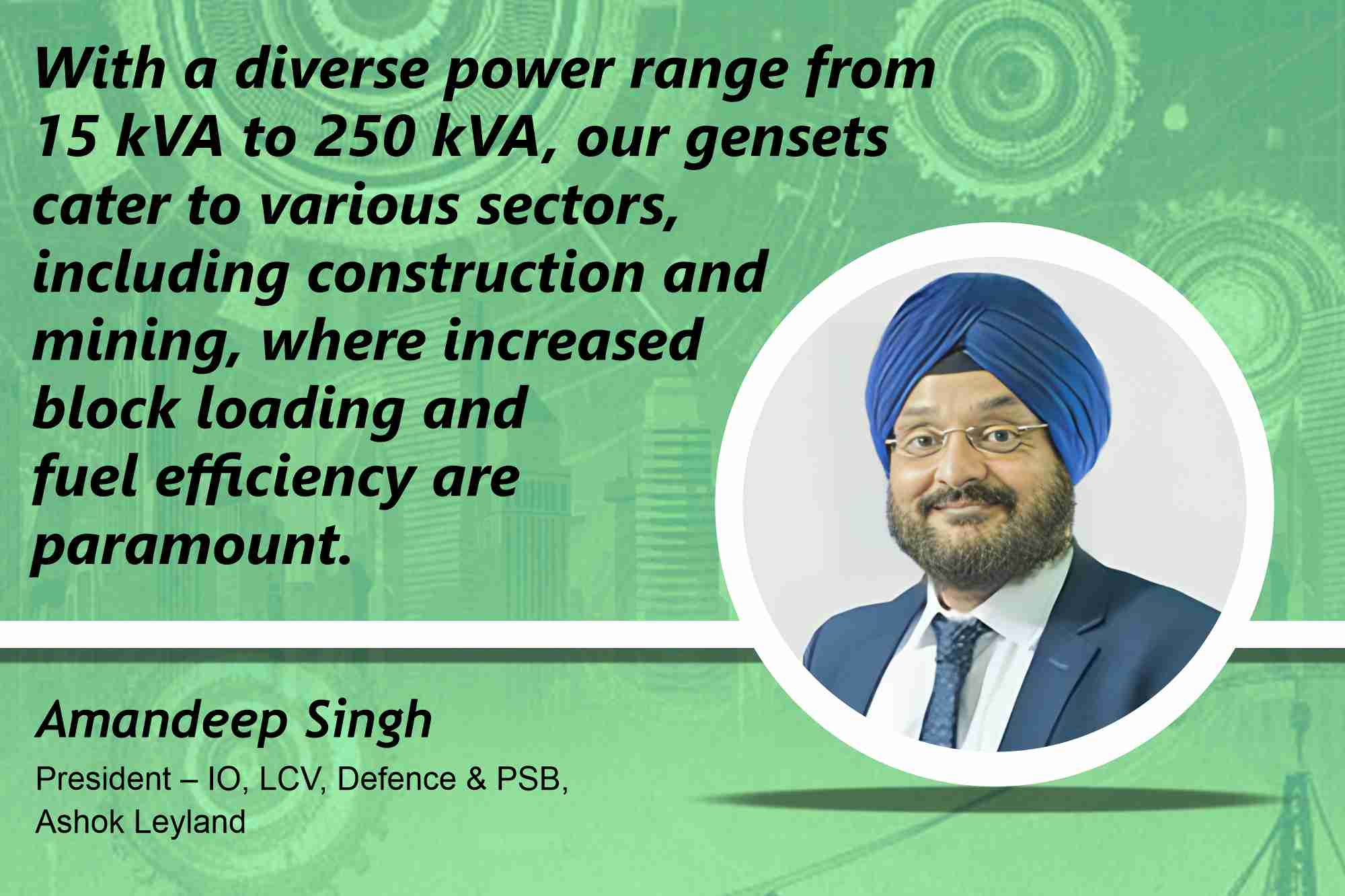
Ashok Leyland provides fuel-efficient, dependable gensets designed specifically for construction and mining. These provide cost-effective performance, CPCB4+ emission compliance, and comprehensive digital monitoring for maximum uptime and sustainability in demanding industrial applications.
Could you discuss the importance of fuel efficiency and long-term reliability in Ashok Leyland’s gensets and how your solutions address cost-effectiveness for large-scale projects like mining and construction?
As an automotive company, Ashok Leyland considers fuel efficiency basic hygiene. This is an important buying element for our customers because it affects their viability. In generators, we employ similar base automobile engines built to function at higher RPMs (2600-2800) and on a continuous duty cycle (24×7). During the life of a generator, customers pay around 82 percent on fuel, 10 percent on maintenance, and 8 percent on capital expenditures. The customer is interested in the total cost of ownership (TCO) rather than the initial capital expenditure.
Our gensets have best-in-class fuel economy and deliver higher block loads to handle demanding applications like mining and construction.
Given the increasing focus on sustainability, how does Ashok Leyland ensure its CPCB4+ Diesel Gensets reduce carbon footprints while maintaining high-performance levels?
Since April ’20, we’ve been developing engines that fulfil vehicle BS VI standards, which are more difficult than CPCB4+. We have gone through the necessary learning curve and have grown in maturity over time.
Implementing CPCB4+ rules will reduce carbon footprints. This becomes more critical as the TIV for the Indian domestic market for gensets ranging from 15 to 250 kVA is approximately 140k, and the overall operational DG set population will exceed 1200k.
In the CPCB4+ range, using our learning curve on BS VI and CEV IV, we cut carbon emissions in line with the legislation while increasing fuel efficiency, improving block loading capability, and increasing service duration, which would translate into better returns for our customers.
Your gensets range from 15 kVA to 250 kVA. Could you explain the specific needs and applications of different industries served by this power range, particularly in the construction and mining sectors?
We serve a wide range of end-user segments with our gensets, including Manufacturing, Process Industries, Banks & BFSI, Hospitals & Clinics, Horeca, IT/ITeS, Education, Reality- Commercial & Residential, Fuel Distribution, Logistics & Warehousing, Infrastructure, Construction & Mining, and Government, including Railways and Defence. Each user segment has its unique duty cycle and loading pattern, which ranges from 40 percent to 110 percent loading and 150 to 6500 hours per year of running hours.
Our engines are intended to handle a wide range of applications. They are the first choice of customers in construction and mining because of their increased block loading, improved fuel efficiency, and longer service life. Our brand is well-known in the construction and mining industries because of our vehicle offerings, particularly haulage and tippers.
Could you explain how your non-emission and emission-compliant engines (CEV-IV, TREM-IV) are designed to enhance productivity and reduce operational costs in industrial applications?
On the industrial side, we provide a wide range of products from 1.5 Ltr to 8 Ltr, 35 hp to 360 hp in non-emission and emission-compliant engines (CEV-IV, TREM-IV). We specialise in industrial applications such as construction, agriculture, mining, compressors, rigs, excavators, and other machinery. We are a top choice among proprietary equipment manufacturers for bespoke engines.
To meet customer expectations in the Industrial segment, we provide best-in-class fuel efficiency, best-in-class packaging tailored to the application, best-in-class engine construction materials, best-in-class power-to-weight ratio, emission compliance, and a nationwide after-sales network.
For construction and mining projects where uptime is critical, how do Ashok Leyland gensets ensure minimal downtime? What after-sales support and services are offered to guarantee this?
We have over 220 touchpoints to ensure uptime at the customer’s end, supported by service managers stationed at our state-level offices. We provide a maximum SLA of 4 hours for reporting and 24 hours for resolution.
With the genset industry shifting towards digitalisation and remote monitoring, is Ashok Leyland incorporating any smart technologies into your gensets for better operational control and predictive maintenance?
We are in sync with the digital wave and are well-prepared for such projects. We have in-house telematics to handle such requirements. As automotive players, we were exposed to telematics and remote monitoring systems. Furthermore, with CPCB4+, remote monitoring is required from 56 kW onwards. These devices are useful for managing preventative maintenance and ensuring uptime.
For more information, visit: https://www.ashokleyland.com/
Cookie Consent
We use cookies to personalize your experience. By continuing to visit this website you agree to our Terms & Conditions, Privacy Policy and Cookie Policy.