Automation and robotics process with alternate fuel will drive the welding market
By Edit Team | October 31, 2022 6:29 pm SHARE
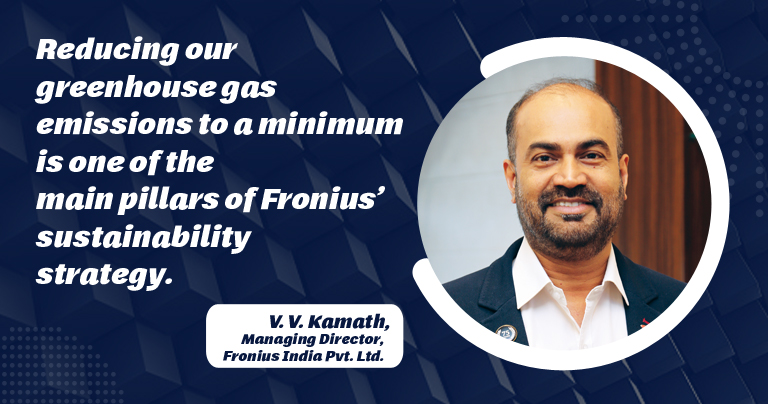
V V Kamath, Managing Director, Fronius India Pvt. Ltd., is optimistic about achieving its decarbonisation goals by switching from fossil fuels to clean energy sources such as solar energy, geothermal energy, and biomass, as well as by reducing our energy consumption.
Sustainability in welding
Welding technologies can be sustainable because they contribute to the production of new components using 3D printing, metal additive manufacturing, or Directed Energy Deposition (DED-Arc). CMT-Cold Metal transfer welding technology is widely used for this AM process for manufacturing near-net shape components. Using this, we can save the base materials through the welding process, in which we can recycle the old and waste materials.
Changes in the procurement of welding equipment and technologies
Manual welding is shifting towards automation and robotics, and we, at Fronius, are already geared up for the shift. Our welding power sources can be used for manual, SPM, or robotic applications as such, with minimal hardware and support peripherals. Also, there is a shift towards Industry 4.0, and all our welding machines are Industry 4.0 ready and enabled for data documentation.
Unique features that enable cutting-edge services to clients
Fronius has innovative advanced technologies like Cold Metal Transfer (CMT), TWIN wire intelligent welding technologies, Laser Hybrid welding (LHW), and I-Wave Multi Process Welding power sources that have unique advantages over the available conventional welding technologies.
CMT technology is the patented process used for joining and cladding. Aluminium can be joined to coated steel or weld sheets of 0.5 mm in thickness by CMT. The deposition rates with TWIN wire can reach up to 24 kg/hr. With LHW, the plates can be joined with a low heat input at very high welding speeds of 4m/min, with minimum edge preparation on the plates/sheets to be joined. I-Wave multipurpose machines have various welding processes, viz., MMAW/GMAW/ GTAW and CMT welding processes in one power source. We are committed to long-term innovations and creative solutions, which is why we have a strong, skilled research team of 780 employees in Austria. We have 1366 active patents and are still counting! All these strengths are the reflection of our extraordinary systems.
Robustness tests of our products: every detail of the new product is tested, errors are resolved, and the software is tweaked to make the final product ready.
Sustainability is a driver for innovation. The development of sustainable products and services is an important part of our sustainability strategy. Some of the key factors in reducing the environmental footprint of our product development process are:
- A long service life
- Efficiency and effectiveness
- The ease of repair and recyclability of the products
- Material and energy efficiency in manufacturing
- Use of sustainable components and recycled materials.
Managing and reducing waste
We have a carbon-neutral headquarters, and the following are the areas where we are reducing waste.
Reducing our greenhouse gas emissions to a minimum is one of the main pillars of Fronius’ sustainability strategy. Decarbonisation at our production sites in Austria will be achieved by 2023. On the one hand, we will achieve this ambitious goal on the other hand by switching from fossil fuels to clean energy such as solar energy, geothermal energy, and biomass, and on the other hand by reducing our energy consumption. Our product packaging ensures “No Land Fillings”. We use recyclable and bio-degradable packaging materials and strictly avoid plastic wherever we can.
Cookie Consent
We use cookies to personalize your experience. By continuing to visit this website you agree to our Terms & Conditions, Privacy Policy and Cookie Policy.