BONDERITE® Solution is a one-stop process for all metal surface treatment
By Admin | August 12, 2022 5:38 pm SHARE
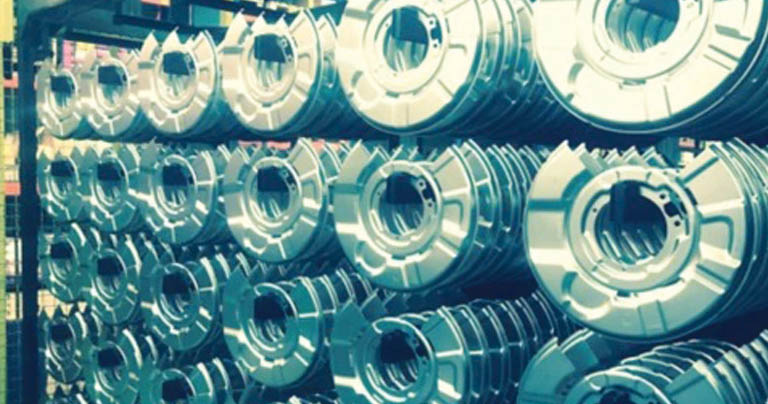
Bonderite’s extensive portfolio includes cutting-edge nickel free, chromium-free, and zinc-free processes for virtually any metal substrate.
and improve sustainability through the use of advanced new alloy sand multi-metal materials.
Faced with tighter regulatory requirements and growing consumer awareness of improved fuel efficiency and reduced emissions, automotive manufacturers are increasingly shifting away from traditional steel sheet or galvanised alloys and toward mixed and very light metals that offer significant weight savings. Benseler-Group, a tier-1 supplier to many European automakers, opened a new plant in Germany in 2016dedicated to cathode dip coating (CDC) of automotive body parts and structural components. With a coating capacity of1,000 square metres of metal surface per hour, the plant relieson a number of Henkel-engineered processes to address major cost, performance, and sustainability issues in metal pre-treatment.
Aluminium components are deoxidised and chromium free converted using Bonderite M-NT 2040, a revolutionry phosphate-free Henkel technology focused on multi-metal and light metal substrates. A special tri-cationic zinc phosphating treatment is applied to the steel parts before immersion Henkel Adhesive Technologies, a global leader in metal surface treatment processes, provides adiverse range of Bonderite solutions to OEM sand suppliers looking to reduce weight coating. Both techniques serve to activate the substrate and prepare it for subsequent priming and corrosion protection. Bonderite’s extensive portfolio includes cutting-edge nickel free, chromium-free, and zinc-free processes for virtually any metal substrate. This provides customers with a “total solutions” package of coating chemistry and expertise throughout the entire value chain, prior to, during, and after pre-treatment. Bonderite M-NT 160/161 for magnesium/zirconium and M-NT 400 for aluminium/titanium are two of the most recent developments. In addition to M-NT Tec Talis, anew M-ZN Two-Step Process for steel or galvanised steel with aluminium is now available. Henkel’s unique position as a surface treatment specialist for light metals has been reinforced with the development of Bonderite M-NT 160/161. Not only can the advanced process be used in the conversion step of magnesium/aluminium hybrid substrates, but it is also the only solution in the world that can provide magnesium parts ready for painting by the end of the same day. Depending on the size and complexity of the components, successful conversion can take between15 and 180 seconds. The non-chromate process forms a layeron the substrate at ambient temperatures ranging from 15to 30 °C, improving paint adhesion while providing enhanced corrosion protection. Customers with large metal surface treatment operation scan also benefit from Henkel’s unique Line guard process control equipment, which comes in modular hardware and software configurations. Line guard incorporates cutting edge PLC, sensor, and HMI technology that has been adapted and seamlessly integrated to provide a total system solution tailored to each customer’s specific requirements, from chemical pre-treatment and pumps to automated process data acquisition and comprehensive documentation. When combined with Henkel’s global capabilities, this results in a very cost-effective “one face to the customer” strategy. Suppliers such as Be n seler-Group can benefit from this comprehensive offering and gain a competitive edge in surface treatment as they capitalise on the light weight opportunities opened up by new alloys and multi-metal materials in the automotive and other critical industries.
n For more details, visit, https://www.henkel-adhesives.com/
Cookie Consent
We use cookies to personalize your experience. By continuing to visit this website you agree to our Terms & Conditions, Privacy Policy and Cookie Policy.