Canned motor pumps from Kirloskar
By Edit Team | January 23, 2017 10:35 am SHARE
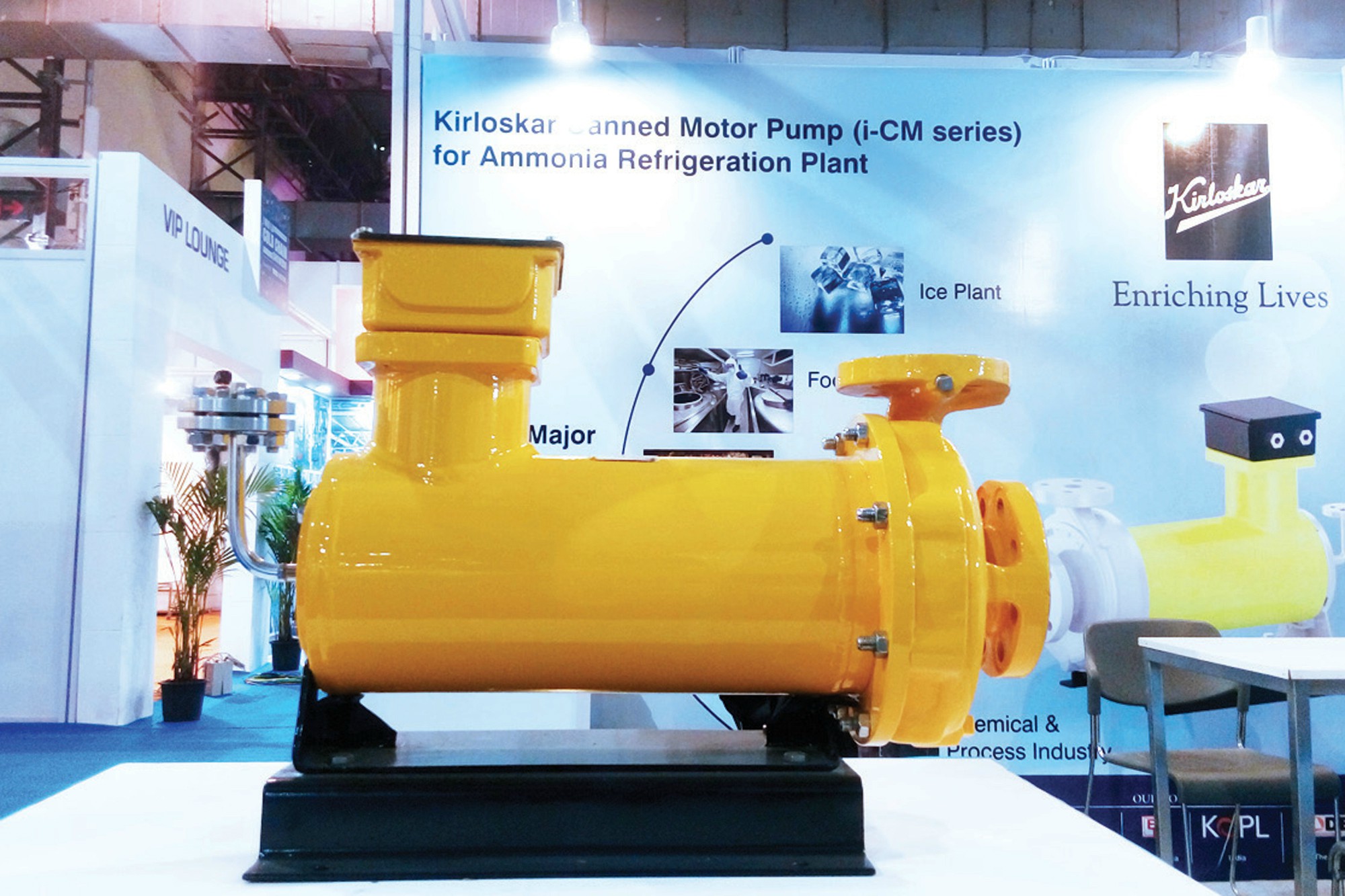
Kirloskar Brothers limited has launched Canned Motor Pump (i-CM)pump, categorised under i – CAN pumps series that cater to the refrigeration (cold storage), ice plants, chemical and process and windmill industries. i-CM pumps are mainly used for pumping hazardous fluids such as radioactive coolants, corrosive and noxious liquids (free of suspended solids and particles) and liquefied gases.
The compact, lightweight yet sturdy design of the pump along with less number of components ensures that it minimises assembly and dismantling time and occupies less space. The pump is hailed as a step-up from the conventional mechanical seal pump category, which requires heavy maintenance. It comes with innovative features, such as optimised stator and rotor design, apart from its compact size.
The pump has a body that is 80 per cent lighter than the conventional canned motor pump, and includes seamless stator band, off the shelf terminal box, three in one adapter plate, optimised bearings and sleeves, improved aesthetics and application base bearing wear monitoring system. Besides, it is also known to reduce assembly time by 50 per cent.
Product range
• Delivery Size: 32 to 50mm
• Capacity: 4 to 80 cubic metre/hr
• Head: Up to 60 meters
• Speed: 2,900 rpm
• Temperature: Up to 90 C (standard)
Design
The casting of the pump has an axial suction and top center line delivery with self-venting design. Smooth hydraulic passage ensures high efficiency. The delivery flanges and supporting feet are cast integral with the casting. The impeller is of enclosed type. Hydraulic balancing of impeller is achieved by balance holes depending upon magnitude of axial thrust. The impeller is statically and dynamically balanced.
The shaft is supported between the carbon graphite bush bearings. The critical speed of shaft is sufficiently above the operating speed. The shaft is critically machined and grounded to maintain concentricity. The motor and the pump share a common shaft. Replaceable wear rings are provided on casting and impeller. Thrust water is provided to absorb the axial thrust.
When viewed from suction-end, the direction of rotation is anti – clockwise. The mounting of the motor has been done on the same shaft where the pump has been installed. The attached motor comes with a 415V, 3Amp Ph/50 Hz supply.
Constructional Features:
• Seal-less and glandless design
• Eco-friendly
• Integral Motor design
• Ease installation
• Less space required for foundation
• Compact in construction and light in weight
• Integral adaptor plate
• Less number of parts
• Integral rear cover and rear bearing housing
• Good aesthetic design
• Stator band can be manufactured with the help of seamless pipe
• Quiet in operation
• Centerline delivery self- venting
• Back-pullout type design
• Flange drilling: ANSI class, 300 FF
• Auxiliary tapping: NPT
• Performance testing standard: ISO9906 Gr.2B
• Interchangeability of components
• Special alignment is not required due to mono- block construction
• No external lubrication is required for bearing
• Motor is protected from liquid with the help of the can provided on the Stator ID and Rotor OD
KBL also offers multiple ‘value added features’ including advance monitoring systems with pump controller that include-temperature indication, discharge/suction pressure indication, vibration and dry run indication.
Cookie Consent
We use cookies to personalize your experience. By continuing to visit this website you agree to our Terms & Conditions, Privacy Policy and Cookie Policy.