Caterpillar boosts wheel loaders efficiency with Production Measurement system
By Edit Team | November 8, 2017 5:36 am SHARE
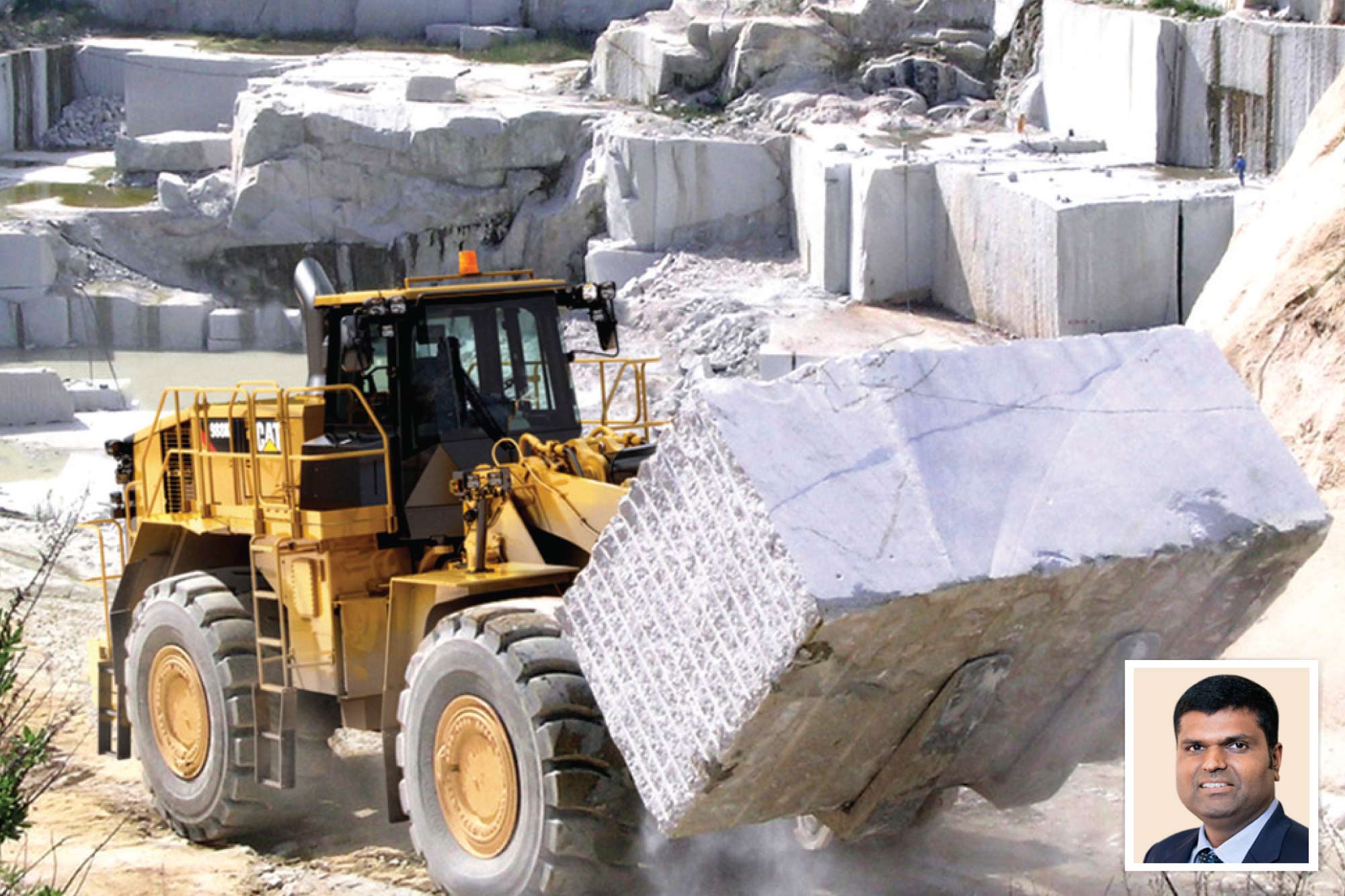
Cat Production Measurement System for Large Wheel Loaders – yet another efficiency boosting technology from Caterpillar.
Andy Dhanaraj, Director – Sales, Global Construction & Infrastructure Division, Caterpillar India.
Caterpillar has been at the forefront of developing breakthrough technologies and product innovation in heavy engineering machinery and equipment which are used in a range of sectors including construction, mining, transportation and energy for several decades now. The seriousness and dedication with which the company pursues its R&D efforts can be gauged from the fact that it invests more than $2 billion annually in these activities alone.
Historically Caterpillar has been credited with developing number of breakthrough technologies and products in all the industry segments it operates. From autonomous off highway trucks to excavators that can carry out even some of the most difficult tasks in the extreme hostile geographic and climatic areas, all these machines are equipped with advanced digital software features. These features help improve production levels by several notches. Cat Connect, the innovative, intelligent suite of hardware, software and dealer services to boost efficiency, improve safety and save costs, is another example of breakthrough technologies and innovative products and technological solutions from Caterpillar Inc.
Cat Production Measurement for 986K, 988K, 990K & 994K Wheel Loaders
Among the new innovative and breakthrough technology Caterpillar provides its customers in various parts of the world an integrated Cat Production Measurement system for 986K, 988K, 990K and 994K Large Wheel Loaders.
“Cat Production Measurement is a productivity enhancing Cat Connect PAYLOAD technology that helps operators consistently deliver payloads with world-class weighing precision, in line with the leading payload scale specialists,” informs Andy Dhanaraj, Director – Sales, Global Construction & Infrastructure Division, Caterpillar India. He adds, it pairs the functionality of an on-board Payload Weighing Scale with production monitoring features such as cycle count and cycle timer; as well as Key Performance Indicators including tonnes/litre (tonnes/gallon) of fuel consumed, tonnes/hour and tonnes/cycle.
When used with Cat Connect LINK technologies, site manager scan access PAYLOAD data through the online VisionLink user interface or Vital Information Management Systems (VIMS) PC software to get accurate, reliable, data about the performance and productivity of their machine. Data can be used to help customers make timely, fact-based decisions about their fleet and more effectively manage their job sites.
Applications
Cat Production Measurement for Large Wheel Loaders is ideal for the following applications:
• Materials producers: Mining, quarry and aggregates, sand and gravel, cement and asphalt plants.
• Metals industries: Mills, smelters and scrap processors.
On-the-go payload weighing maximizes productivity
Cat Production Measurement allows operators to weigh bucket loads “on-the-go” during loading operations. Payloads are weighed as the bucket is raised during lift – eliminating the need to interrupt the loading cycle, thus improving efficiency and productivity. “Cat Production Measurement helps operators hit target payload the first time, eliminating under loading and overloading that require return trips to the stockpile; resulting in lost productivity and higher fuel usage,” Andy says.
The Cat Production Measurement technology-enabled properly loaded trucks reduce safety concerns, cost of excessive wear on equipment and haul roads and overload fines for customers.
Fully integrated display with intuitive user interface
Cat Production Measurement is integrated into the loader’s standard multifunction touchscreen display, located within easy reach of the operator’s fingertips and viewable at a glance. No additional display is required giving the operator a full view of the work area with no additional cab clutter. The graphical user interface is easy to use and navigate; and even works while wearing gloves.
Transfer-on-weigh, low-lift weigh and tip-off
Bucket payload weight is “transferred” or added to the displayed truck payload total during weighing instead of waiting until bucket dump. This gives the operator a preview of how much payload will go in the truck before dumping. No need to manually calculate whether they have enough or too much in the bucket to finish off the truck load. This gives them a chance to tip-off excess material before physically dumping the entire load into the truck that is almost at target weight.
Once the system detects a complete bucket dump, only then is the bucket payload committed” to the actual truck payload total in memory.
Two advanced operating modes expand system usability
Low Lift Weighing mode allows the operator to see a quick estimate of bucket payload weight before raising to full height. This speeds truck and hopper loading cycles when only an estimated weight is required.
• Get an estimated weight down low without raising the bucket up through the entire weigh range.
• Ideal for stockpile applications and loading hoppers from ramps where only an approximate weight is needed.
Two Tip-Off modes (on the 988K and 990K only) help the operator quickly adjust the last bucket load during the final pass. The operator can dump material from the bucket and view transferred weight in real-time, which eliminates the need for a lower and re-weigh cycle and shortens loading times.
• Tip-off at Pile: Helps operator make small adjustments at the pile before heading to the truck.
• Tip-off at Truck: Ideal when sequential trucks need the same material type or when distributing the load evenly between axles.
For more details, visit www.caterpillar.com
Cookie Consent
We use cookies to personalize your experience. By continuing to visit this website you agree to our Terms & Conditions, Privacy Policy and Cookie Policy.