Cloos’ AC MIG/MAG power source improves efficiency in welding
By Staff Report | December 27, 2024 5:59 pm SHARE
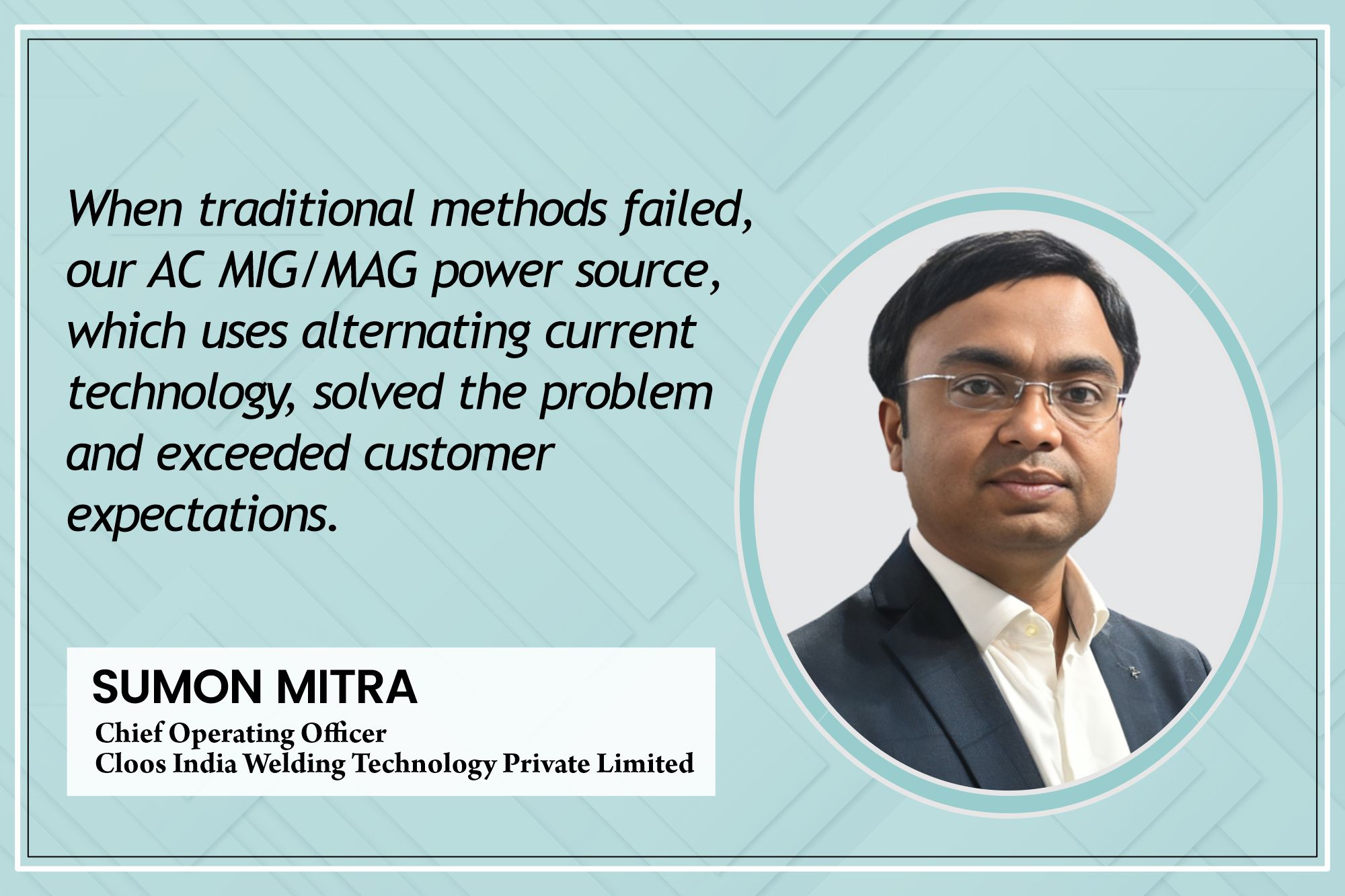
As India’s industries evolve, Cloos leads the way to automation with sophisticated solutions such as QIROX robots, QINEO welding systems, and Mix Weld technology, which boost productivity, efficiency, and manufacturing quality.
How has the demand for automated welding systems evolved in India, and how are your solutions addressing this shift?
Welding is Cloos’ primary competence, and it serves as the foundation for everything else we do. Building on this foundation, we offer comprehensive automation solutions adapted to our customers’ requirements. Our strategy includes examining and determining the best welding technology for each client, devising an appropriate automation solution, and successfully implementing it.
Our staff assures a smooth deployment at the customer’s site and provides full training to their employees. We focus on selling things and providing solutions, necessitating a professional and committed workforce.
In today’s market, there is a considerable disparity between having labour and having the necessary skills. The scarcity of trained labour has increased the demand for automation. Unlike 5 to 10 years ago, when automation was predominantly used in heavy sectors, even small-scale shop floors are increasingly looking for automation to overcome the issues caused by a shortage of trained welders.
We provide a wide range of high-end welding products and solutions suitable for heavy-duty and specialised applications to address this expanding demand.
How do cobots complement traditional welding, and which industries benefit most?
Our cobot and robot applications are available as complete turnkey solutions. When customers contact us with their needs, we assess their manufacturing process. We determine whether companies engage in continuous batch manufacturing of 2, 5, or 10 different product variants throughout the year or if they produce smaller batches with frequently changing designs and no stable data due to varying consumer demands. Cobots provide a substantial advantage in circumstances involving frequent design modifications and smaller batch quantities because of their quick and easy programming capabilities.
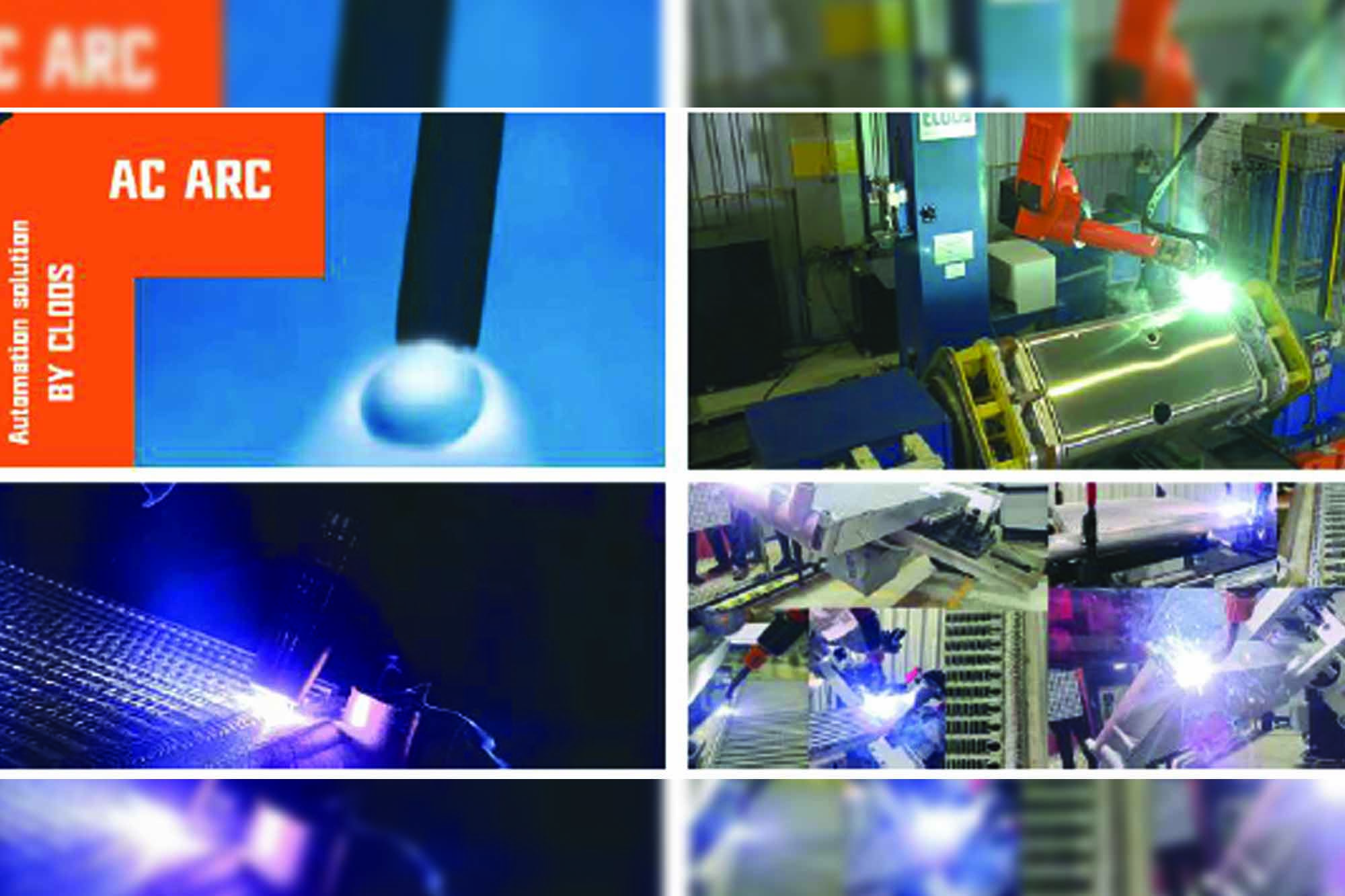
Based on these discussions and research, we advise our customers on choosing a robot or a cobot package. In the case of cobots, we offer advanced functionality like online seam tracking without needing external laser cameras. This is made possible by an inbuilt system, a hallmark of Cloos technology, which is well-known worldwide. This built-in capacity in our cobots provides a significant benefit, solving a critical gap that many of our clients confront.
How does Cloos ensure Industry 4.0 compatibility, and how do software, sensors, and connectivity enhance welding efficiency and quality?
Industry 4.0 necessitates technology capable of collecting and transferring data, condensing it into a single interface from which the complete system’s data can be easily accessed. In our offerings, QIROX denotes our robotic system, QINEO, our welding system, and QNEC, the entire process, including welding data and database integration.
When we offer a system, all our hardware, including built-in sensors, is Industry 4.0 ready. Customers can choose between using our Cloos C-Gate Industry 4.0 software or integrating it with their existing systems.
With Cloos C-Gate, customers can easily access all system data on their mobile devices anytime and anywhere. The program also ensures quality control; for example, if a welder changes a parameter over the predetermined limit, an alert is promptly transmitted to the appropriate authority’s mobile device.
We supply the essential data via OPC protocols for customers using Industry 4.0 software, allowing for smooth integration. Our solutions, which include hardware and software, are intended to meet our customers’ demands, requirements, and preferences.
What new welding technologies have been introduced to aid automotive components manufacturers?
The welding process is the strength and heart of any robotic welding system. While robots, peripheral devices, and other automation components are necessary, the key focus when discussing solutions with customers is understanding the welding difficulties that must be solved and delivering the appropriate product based on the Welding Procedure Specification (WPS).
At Cloos, we pride ourselves on providing diverse, innovative welding methods adapted to specific requirements, whether thin-sheet or heavy-duty welding. We offer precise current and voltage control and are pioneers in tandem welding technology. This enables us to achieve continuous deposition rates of 20-30 kg per hour, positioning us as industry leaders.
We excel at thin-sheet welding, with travel speeds of up to 4.5 meters per minute on sheets as thin as 1 mm. We have completed tough projects in the increasing aluminium industry, particularly in heat exchanger and battery manufacture. One example is a heat exchanger product where a customer failed to get appropriate penetration using traditional approaches. We launched our revolutionary AC MIG/ MAG power source, which employs alternating current technology. The outcomes exceeded expectations, and the customer met the needed quality for the first time, establishing us as a global issue solver in this field. We’ve already supplied two systems to this client, and more enquiries are flowing in from comparable businesses.
Furthermore, our new and proven welding processes for highest productivity and quality overcomes the issues of partial welding in businesses that work with huge, immovable goods. This technology enables a seamless transition between pulse and non-pulse modes, allowing for effective welding without the need to rotate objects horizontally. These technologies, particularly AC technology and new and proven welding processes for highest productivity and quality, reflect the most recent advances in welding techniques that we provide to our customers, assisting them in overcoming even the most difficult obstacles.
How do training initiatives support workforce skill development in India, and how does education drive automated welding adoption?
Training and skill development are crucial components of our methodology, as they enable the customer’s team to efficiently manage the system once we have deployed and verified the solution.
Operating a robotic system necessitates specialised expertise, yet our solutions are intended to be extremely user-friendly. All operations are controlled by a single teach pendant, eliminating the need to access the power source or other components separately. Welding parameters, online seam tracking, and other controls are all available and displayed on a single screen, simplifying operation.
We provide training in two methods to guarantee that operations run smoothly. When we deliver a system, we begin by teaching the customer on-site. Second, we provide further training at our technical centre in Pune. This facility invites clients, college students, and institutional trainees, allowing us to exchange information and expertise. This method is critical for running the systems and making sound decisions concerning robotic welding solutions.
Our training programs are intended to educate customers and prospective users on the essential considerations when selecting the best robotic welding system. This is critical to the successful implementation of automation programs. Frequently, we encounter trainees—whether customers or engineers—who realise during the training that their prior automation decisions were incorrect owing to a lack of understanding about relevant technologies and alternatives. Our programs provide them with the knowledge they need to make sound decisions.
As a result, our training benefits both present users of robotic systems and those considering automation, allowing them to select the best solutions for their needs.
For more information, visit:https://www.cloos.de/de-en/
Cookie Consent
We use cookies to personalize your experience. By continuing to visit this website you agree to our Terms & Conditions, Privacy Policy and Cookie Policy.