Cold Galvanising Process
By Edit Team | February 29, 2016 12:25 pm SHARE
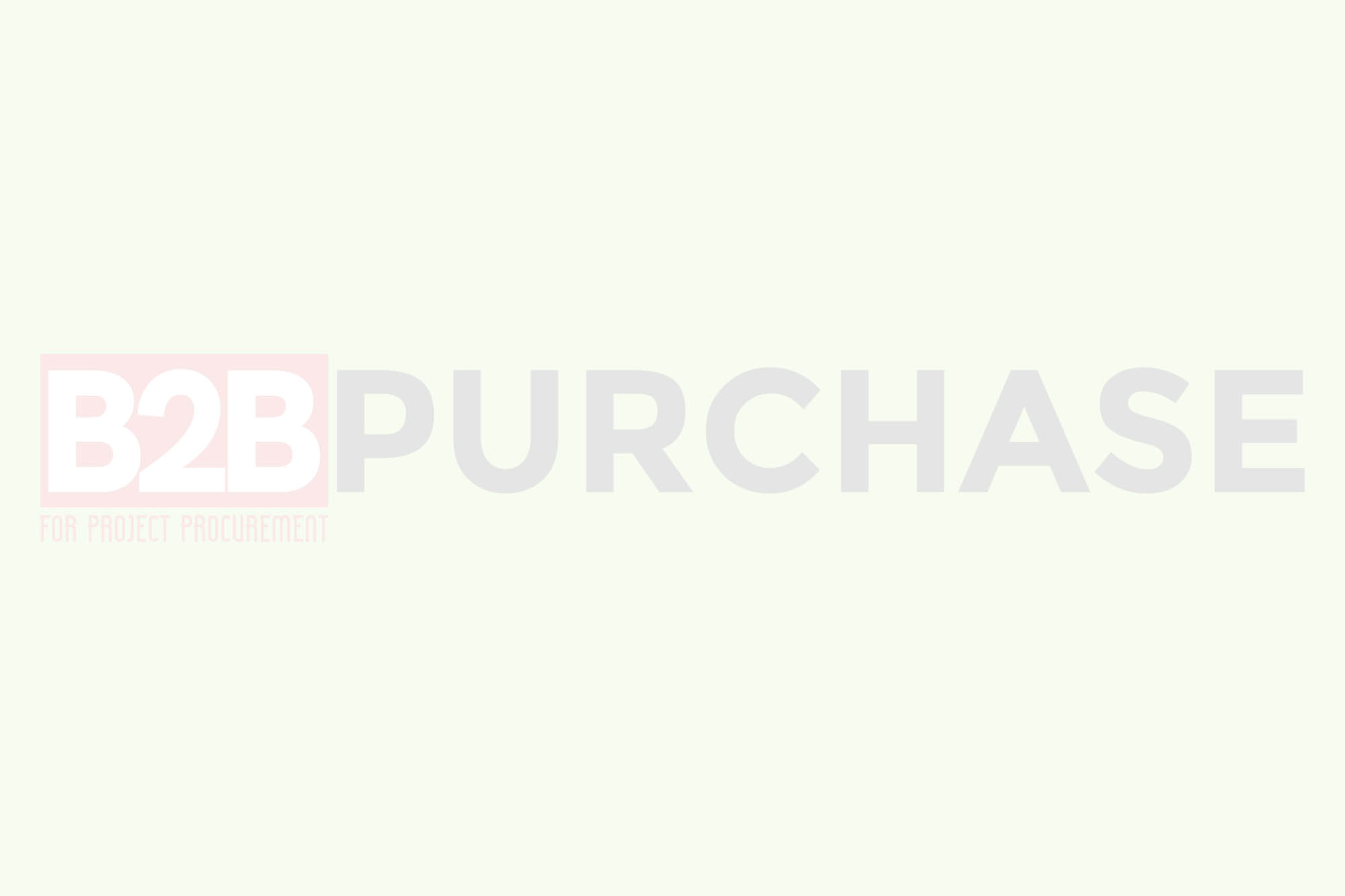
Cold galvanising process for repairs or touch up for scratched, damaged & rusted GI fabrications
1.How does galvanising protect steel from corrosion?
Zinc metal used in the galvanising process provides an impervious barrier between the steel substrate and corrosive elements in the atmosphere. It does not allow moisture and corrosive chlorides and sulfides to attack the steel. Zinc is more importantly anodic to steel. This means it will corrode before the steel, until the zinc is entirely consumed.
2.How does the cost of hot-dip galvanising compare to other corrosion protection systems, such as paints?
When compared with paint systems, hot-dip galvanising after fabrication has comparable initial application costs. In fact, the lower life-cycle costs of a hot-dip galvanised project makes galvanising the smart choice for future.
3. How long can I expect my galvanised steel project to last in service?
Hot-dip galvanised steel resists corrosion in numerous environments extremely well. It is not uncommon for galvanised steel to last more than 70 years under certain conditions.
5. Does the galvanised steel coating of zinc resist abrasion?
The three inter-metallic layers that formed by Fusion Bonding between IRON and ZINC metals during the hot-dip galvanising process are all harder than the substrate steel and have excellent abrasion resistance.
6. What causes wet storage stain and how can it be prevented?
Zinc on newly galvanised steel is very reactive and wants to form zinc oxide and zinc hydroxide corrosion products on exposure to air, UV radiation and moisture and water vapours in the atmosphere. This eventually becomes the stable zinc carbonate. When galvanised steel is tightly stacked or stored in wet boxes that don’t allow for free flowing air, the zinc forms excessive layers of zinc hydroxide, otherwise known as wet storage stain. Most wet storage stain can be easily removed with a cleaner or nylon brush. To prevent wet storage stain, store galvanised steel indoors or block it so that there is ample free flowing air between each galvanised article.
7. Why do galvanised steel appearances differ from project to project and galvaniser to galvaniser and is there any difference in the corrosion protection offered by the different appearing coatings?
The steel chemistry is the primary determinant of galvanised coating thickness and appearance. Continuously cast steel produced by the steel companies has a wide variety of chemistries, thus the different coating appearances. There are several different additives galvanisers may put in their zinc kettle to enhance the coating appearance by making it shiny, spangled or matte gray. The appearance of the coating (matte gray, shiny, spangled) does nothing to change the corrosion protection of the zinc coating.
8. What are the specs governing hot-dip galvanised steel?
Structural steel (plate, wide-flange beams, angles, channels, pipe, tubing) are galvanised to ASTM A 123/A 123M. Fasteners and small parts that fit into a centrifuging basket are galvanised to ASTM A 153/A 153M. Reinforcing steel is galvanised to ASTM A 767/A 767M. IS 2629 – 1966 IS 4759 – 1968 BS 729 – 1971 ASTM A-780 A 446 – 71.
9. Is galvanising more expensive than paint?
Depending on the product mix, square feet per ton, and condition of the steel surface, galvanising is often less expensive on an initial cost basis. However the lifetime costs should be considered when making a project decision on the corrosion prevention system to utilise. And, with galvanising, the life-cycle cost, i.e. the cost per year to maintain, is almost always less than any conventional painting system. Paint systems require maintenance, partial repainting and full repainting several times over a 30-year project life. The costs can be staggering, making the decision to paint a costly one in the long run.
10. How long will hot-dip galvanising protect my steel from corrosion?
The corrosion rate of zinc and how long it will provide protection is a function of the coating thickness and the amount of corrosive elements in the atmosphere. For example, in rural settings where there is less automotive or truck exhaust and plant emissions, galvanised steel can easily last for 100 – 150 years without maintenance. In industrial, humid, saline and marine locations, air contains significantly more aggressive corrosion elements such as chlorides and sulfides. Galvanised steel fabrications may last for 50 – 100 years in those cases.
11.Where are galvanised steel products used?
Mild steel used in all kinds of structural fabrications (angles, channels, wide-flange beams, I-beams, H-beams, grating, expanded metal, corrugated sheets, wire, cables, plate, castings, tubing, pipe, bolts and nuts) The industries that utilise hot-dip galvanised steel range from infra and EPC projects, water and wastewater treatment plants architectural steel structures (canopies, facades, exposed structural steel, lentils, reinforcing steel for concrete decks, exposed structural steel columns and barriers, pulp and paper plants (structural steel, walkways, handrail), motor housings, electrical cabinets, frames, heat exchanger coils): transmission towers, distribution poles, substations, wind turbine poles, signal antennas, and towers, rail transportation (poles, switchgear, miscellaneous hardware), chemical or petrochemical plants, off-shore constructions, pipeline hardware steel buildings, storage tanks, walkways) SILOS, tank farms, chemical and steam pipelines, fence poles, boats, trailers, stadiums, arenas, road crash guards, racetrack fences) pre-engineered metal buildings and almost every mild steel fabrications.
12. Can I paint right over the galvanised coating? If so, what procedure should be followed?
Galvanised coatings can be easily and effectively painted, not only for aesthetics but also to extend the structure’s service life. The age and extent of weathering of the galvanised coating dictate the extent of surface preparation required to produce a quality paint system over galvanised steel. ASTM D 6386, practices for preparation of Zinc (Hot-Dip Galvanised) coated iron and steel product and hardware surfaces for painting, should be referred for suggested surface preparation methods for galvanised coatings of varying ages.
13. What is “white rust” and how can it be avoided?
“White rust” is the term mistakenly applied to wet storage stain, which actually is a milder corrosion product than white rust. Wet storage stain can be avoided by properly stacking freshly galvanised articles, avoiding unprotected exposure to wet or humid climates, or by using a surface passivation treatment (Dip in very dilute Dichromate Solution) after galvanising. Wet storage stain typically weathers away once the part is in service. White rust is most commonly associated with galvanised cooling towers structures and marine, off-shore fabrications.)
14. What is “COLD Galvanising “?
There is no such thing as cold galvanising. The term is often used in reference to painting the mild steel fabrication or damaged galvanised structure or object with 99 per cent pure zinc-rich paint. Galvanising by definition means a metallurgical reaction between zinc and iron to create a metallic bond between zinc and steel of approximately 3600 psi strength. There is no such reaction when zinc-rich paints are applied and the bond strength is only several hundred psi. Application of zinc rich paints will completely seal the exposed, scratched, welded, damaged surface (resulting from removal of zinc layer on mild steel. Such damaged surfaces are virgin and are much more prone to atmospheric corrosion. Corrosion and rusting are a sub-surface phenomenon and will propagate under the galvanised zinc coating layer. Hence it is customary and mandatory to coat such areas with cold galvanising zinc rich paints.
Promtech Consultancy Group, through their manufacturing unit Innovative Coating Industries: MIDC, Pimpri Pune 7767982244, offer Zinc Metal Sprays , Zinc Bright Sprays , Zinkote 20 GP per cent Premium Zinc Rich Paints : Ex Stock from Pune and Thane.
This article is authored by Prof.Pradeep Vaidya, Technical and Marketing Director, Promtech Consultancy Group.
For Complete details on Galvanising Process and Zinc Rich Paints and Sprays www.promtechaerosol.com
919820181738 ,02225883265 puvpromtech@gmail.com
SONIA Vaidya 9819813015 soniavaidya30@gmail.com
Cookie Consent
We use cookies to personalize your experience. By continuing to visit this website you agree to our Terms & Conditions, Privacy Policy and Cookie Policy.