Delivering excellence in warehouse construction
By Edit Team | March 13, 2024 3:11 pm SHARE
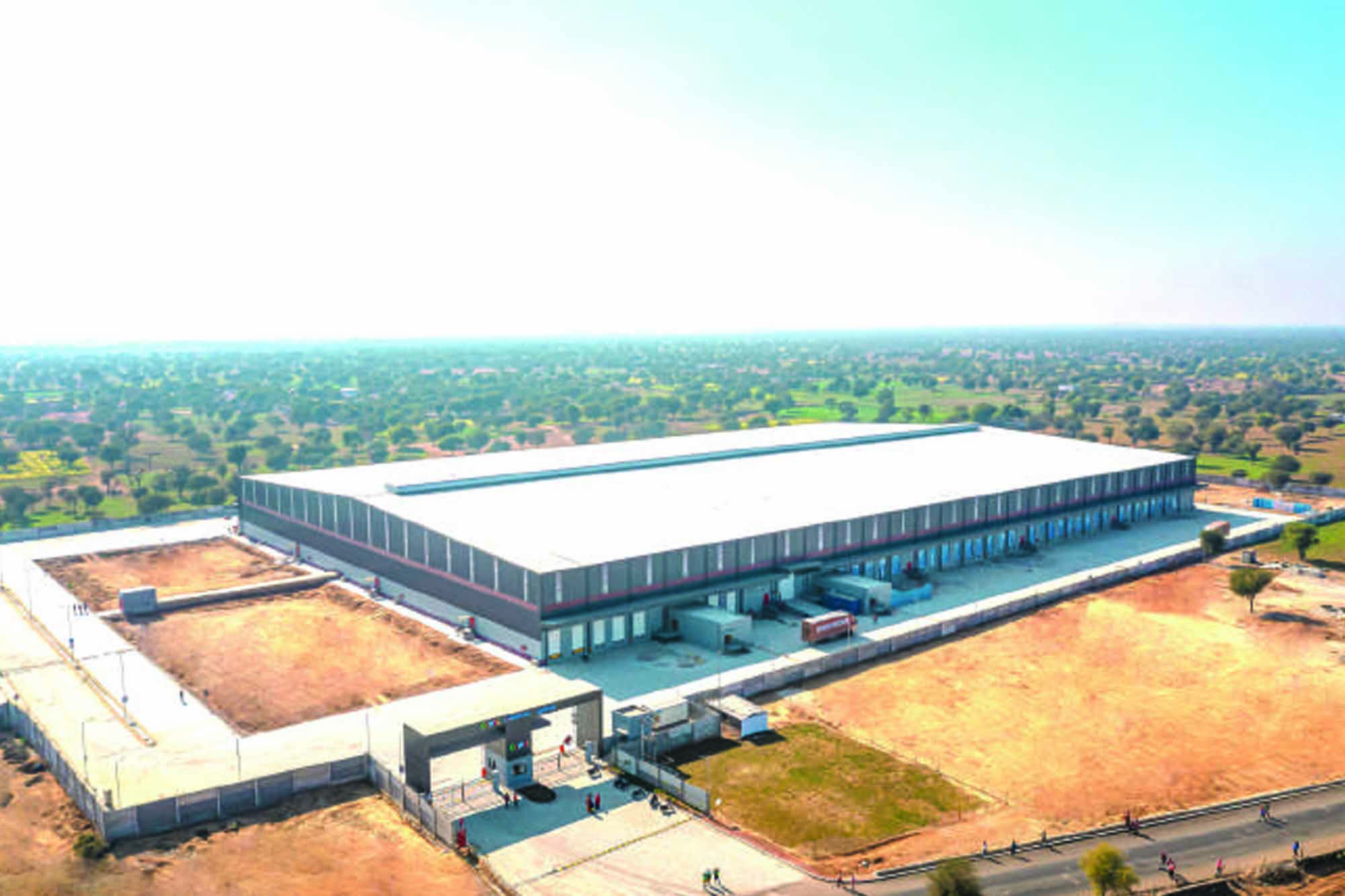
Nahar Industrial Enterprises Ltd. envisioned a warehouse in Jaipur, Rajasthan, that would be tall and change industry standards. They joined together with Everest Industries and sought to establish a reliable and innovative warehouse.
One of the major projects that Everest completed effectively was the construction of a warehouse for Nahar Industrial Enterprises Ltd. This structure is a shining example of a meticulously planned, expertly designed warehouse. Situated to function as a crucial distribution hub, the establishment has been designated for use by the leading e-commerce company in India.
One of the nation’s top producers of textiles, Nahar Industrial Enterprises Ltd., has a diverse range of businesses under its umbrella. The company has shown strategic awareness by developing a warehouse for its business arm focusing on warehouses.
Geometry
The Warehouse has an area of over 3.5 lakh sq. ft. The width of the building is more than 130 m, and it requires large unobstructed spaces for the movement of forklifts to transport goods. Everest designed a multi-span frame with optimum column spacing to achieve the layout requirements. Jack Portals and Jack beams were provided to reduce interior columns for unhindered space required for material movement inside the building.
Architectural features
The building has a mezzanine area along its length. The flooring was provided using concrete over the deck sheet to bear human and material loads. Shear studs were provided for non-composite joists in lighter sections.
The customer was very particular about leakage. Hence, Everest decided to use the latest SS470 Standing Seam roofing profile, the latest addition to its product offerings. The leakproof roof was provided in the building for water tightness and longer roof life. Appropriate rainfall Intensity data was collected, and adequate water drainage systems were designed to offer seamless working for the structure’s end user.
Roof monitors and S-type louvres were provided to ensure ventilation as per the users’ required air changes.
uniqueness
The building’s end wall will expand in the future, which requires careful design of the end wall columns and secondary systems, including wall cladding. The customer wants the wall cladding and columns removed to pave the way for expansion and create more space. The building’s length is more than 200 m, so designing the structure to handle thermal expansion was necessary.
The building had to be designed to house an array of pipe racks, sprinkler systems, and cable trays. Adequate design precautions were taken to ensure the desired locations were provided with Brackets or slotted holes to allow the suspension of the supports of these structures.
Challenges
The building had two important aspects that remain the concern of all customers—economical solutions without preceding the requirements of designs, material specifications, and construction time. Since the project had a very short timeline, the design and release of the drawings had to take place on a very tight schedule. The material dispatch had to follow the erection sequence, which required accurate planning.
Everest used two Standing Seam roll formers to ensure roof sheets were laid in record timelines and strictly adhered to safety practices. Any error would have cost the company its plans to commence operations on time.
Conclusion
The economy and timeline were key points. The Everest Industries team maturely handled the situation by conducting multiple meetings and monitoring day-by-day progress as desired, thus resulting in the expected positive outcome for all project stakeholders.
Cookie Consent
We use cookies to personalize your experience. By continuing to visit this website you agree to our Terms & Conditions, Privacy Policy and Cookie Policy.