Double Duty: Sarens enlists two Terex AC 700 cranes for a heavy tandem lift
By Edit Team | August 19, 2016 5:55 am SHARE
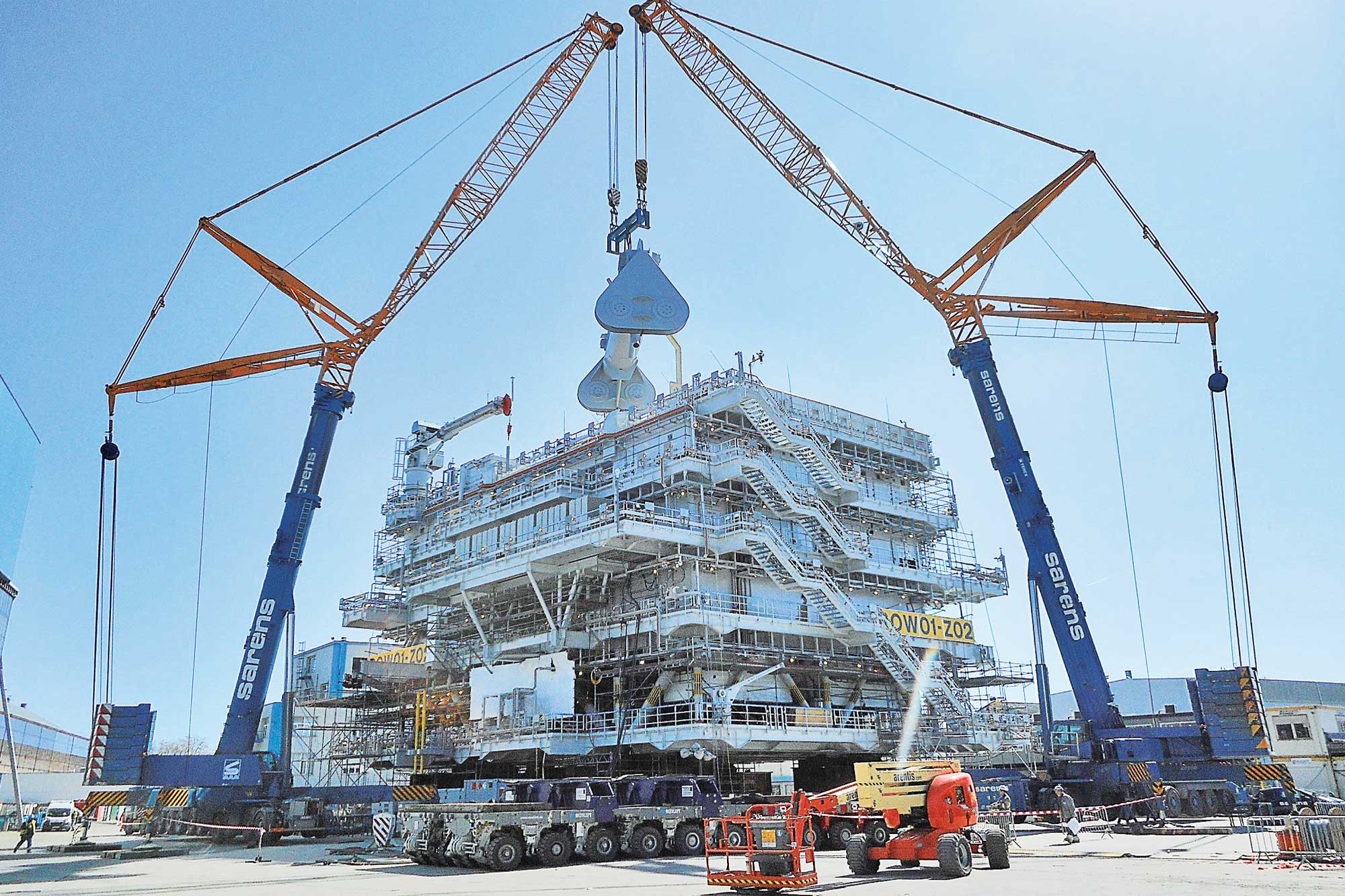
Recently, international steel construction company, Iemants, constructed an offshore oil module for Fabricom at the company’s Hoboken facility in Antwerp, Belgium. These massive modules, critical for the oil and gas production process, range in sizes reaching 25-metre high, 30-metre wide and 40-metre long and weigh up to 2,200 tonnes. Even with a full complement of equipment at Iemants’ disposal, occasionally during module construction it is necessary to bring in heavy lifting specialists to safely pick especially heavy pieces and place them on to the module platform.
When the time came to lift and mount on top of the module a large spreader bar used to perform offshore lifting, Iemants worked with its lifting partner, The Sarens Group, to develop the most cost-effective and efficient lifting solution.
The Right Cranes
The spreader bar measured 13.5 metres long, 5 metres wide, and 6 metres high and weighed 145 tonne. It had to be lifted from ground level to a placement height of 32 metres, and the crane would have to work at a maximum 24-metre radius during the lift. “We considered a number of options from using a single crawler crane to performing a tandem lift using two all terrain cranes,” says Erik Van der Elst, Key Account Manager for Sarens.
The advantage of the single crane option would have been that it required only one crane and crew to be mobilised. However, a crawler crane would require multiple days and more than 20 loads to transport the crane components necessary to configure it to meet 145-tlift capacity at a 24-metre radius. “It would need at least 10 days to complete the entire project from mobilisation to completing the lift with the single crane option,” says Van der Elst. This was too long and costly for the module lift project.
Sarens’ project managers focused on a more efficient, dual crane option, using the 700-tonne capacity class Terex AC 700 all terrain crane. To meet required lifting capacity and working radius, while minimising loads to improve mobilisation efficiency, planners went with a 20.5-metre main boom option, using a 4-metre variable adapter to connect the 30-metre luffing fly jib to the telescopic boom. “In this configuration, each AC 700 crane offers 86.5-tonne capacity at the 24-metre radius, ample capacity to safely lift the 145-tonne spreader bar,” says Michael Klein, Product Marketing Manager for Terex and Demag All Terrain Cranes.
Even though this option required two cranes to be mobilised, it offered significant time and money savings. The nine-axle AC 700 all terrain crane is quickly driven to the jobsite with its complete 60-metre main telescoping boom installed, while meeting 12-tonne per-axle load limits to reduce the number of loads required for transport.
Even using the two cranes, this option would cut the number of loads approximately in half compared to mobilising a crawler crane. “We calculated a week’s time savings by using the two Terex all terrain cranes, which represented significant labour and cost savings for our customer,” explains Van der Elst. This is critical for the construction of an oil module in a depressed oil price market.
Cookie Consent
We use cookies to personalize your experience. By continuing to visit this website you agree to our Terms & Conditions, Privacy Policy and Cookie Policy.