Effective grouting solutions to arrest heavy water leakages in below-grade structures
By Edit Team | February 22, 2023 6:28 pm SHARE
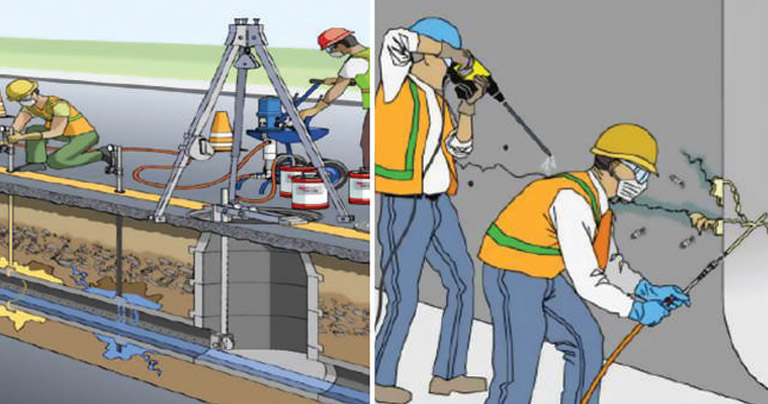
Nowadays most of the large commercial/residential building structures and infrastructure projects such as Road & Rail tunnels, UG Metro Rails, Mining tunnels, Dams, Hydro Power projects, etc., involve huge underground constructions. During construction, design modifications and adaptations of these structures are common, and civil engineers & project managers often encounter challenging issues and hazards on account of poor geology and groundwater constraints. Water flow under the ground is mostly unpredictable, abrupt, and destructive, which can have catastrophic consequences for structural integrity and longevity. Moreover, such Projects are always expensive to build and need continual and high standards of maintenance.
Generally, the water channels and water flow under the ground are difficult to predict especially in tunnels for rail/ road/ UG metro or mining. Water ingress in a tunnel or deep basement can have catastrophic consequences for structural integrity and durability. Once water finds its way into our workplace (shaft, gallery, tunnel, etc.), it seems to be very complicated to stop it. As soon as we plugged one leak, the water will find another gap, and a new leak will appear in a formerly dry point.
Amongst the various options, grouting is the most frequently used defense against water ingress in tunnels and is a remedial option to improve the mechanical and sealing properties of soil and rocks. This has created a demand for high-performance grouting materials.
However, it is possible to use a wide range of techniques and products to control water ingress into underground structures and mining works. There are many products available for waterproofing, consolidation, sealing, bolting, crack and joint repairing, bonding, and cavity filling. Although, the selection of the right grouting techniques, materials, and suitable equipment is of utmost importance for the successful and permanent arresting of leakages.
Generally, the following factors should be considered while deciding on grouting in below-grade structures subjected to substantial water leakages and for consolidation of rocks/ soil.
Permeability or porosity of the concrete/rock mass or soil
Crack width
Substrate or crack movement
Dry/ Moist/ Wet
Water Pressure and Flow Rate (amount of water infiltration)
Injection Method and availability of materials & equipment
Mechanical Properties
Ambient Temperature, etc.
Polyurethane injection grouts have become very popular over the last couple of decades and are considered to be the most effective solution to inhibit heavy water leakages in below-grade or water-retaining structures. Polyurethane grouting involves the injection of expanding polyurethane to cut off water flow through joints or cracks and to fill voids beneath or behind the subsurface of the excavated area. The grout is injected with high pressure through a pre-drilled hole, which then expands to fill the crack or void. Polyurethane grouts can be used for both leaks sealing against high water flow and ground consolidation.
PU grouting is performed to improve the physical and mechanical properties of rock, soil, or building materials in construction. In PU injections, the components polyol and isocyanate react to form a high-strength adhesive. The main property of polyurethane is its versatility, and it can be found in different formulations having different properties either in liquid or in a hardened phase, such as viscosity, thixotropy, foaming reaction, and mechanical strength. Generally, water-reactive polyurethane is (with or without the addition of a catalyst) injected into the ground and cured with the water in the ground yielding a lightweight foam.
Polyurethane grouts are designed to react with water and expand in place, forming a tight, impermeable, elastomeric seal that immediately stops the flow of water. Polyurethane seals in three ways: First, it forms a chemical bond with concrete surface areas; second, it builds a mechanical anchor by entering the pores and voids; and third, by expanding, it forms a compression seal within the crack, joint, or void to act as a water stop.
Many different polyurethanes are available, but all can be classified as hydrophobic, hydrophilic, or multi-component based on their reaction with water, elongation, and mechanical properties. Unexpected water ingress during tunneling usually escalates project costs and leads to important delays. In such cases, appropriate injection systems based on dual and single-component polyurethane forms and or resins are generally used. Most of the time, only foaming PU injections can temporarily stop water ingress, but it is never a permanent solution. While Pure Resin injections can form a permanent seal, they can’t cut off or stop the heavy water flow. Therefore, 2 component resins are usually administered after injecting foam to achieve lasting and permanent sealing. Internationally, it has become common practice and standard to inject foam first, followed by the injection of resin to achieve a permanent seal, although it may require separate drilling of holes, separate packers, and the use of different injection pumps, which is a time-consuming, costly, and tedious process.
Resins are fascinating compounds both in the field of structural renovation as well as in new construction. Some of their most important uses apply to anchor, sealing, cavity filling, rock stabilization, and crack injection. There are many different resins for injection, each suitable for specific circumstances and conditions. There is no single resin that will suit all conditions. Appropriately engineered resin injection can transform weak sands to the consistency of sandstone and water-bearing gravel to a solid conglomerate. If the incorrect resin is chosen, it may result in a performance that does not meet the requirements.
Presently, a new generation of Dual Performance Combination PU injections (Foam and Resin in a single product) has been introduced, which provides a very effective solution. Such injections offer dual characteristics and performance, i.e., in the presence of water, they will foam up to curb water leakages, and the same material when injected further cures as a solid resin which permanently seals leakages/cracks while in the absence of water, they will cure to the solid resin. Two different categories of such injections are available – one for permanent and elastic sealing, while the other for permanent and structural sealing with high mechanical properties like epoxy injections. Such grouts can also be used for structural repairs even in low temperatures.
Therefore, it requires experience and intricate knowledge from various fields like geology, hydrogeology, structural geology, rock and soil mechanics, geotechnics, mining, underground constructions, construction of foundations, structural stability, defects of constructions and their repair, the chemistry of the grouting material, grouting technique (pumps, packers), etc. Grouting technologies represent an effective technology for solving various kinds of problems in mining, construction, and geotechnics practice.
ECMAS PU INJECTION GROUT SOLUTIONS: ECMAS offers a wide range of very effective PU injection grouting solutions in India with unique properties.
- Produced in India under the Make in India initiative, in technical collaboration with a Netherlands-based company ensuring the Best of Technology, Quicker Service with a shorter delivery time
- All our PU Injection products are MDI based, i.e., TDI, Solvent, and Phthalate free products
- Wide range of solutions to meet specific project site challenges (Foam, Resin, Dual Performance, and Gel series)
In-house R&D to ensure high quality, tailormade the solutions
Product Name | Brief Description |
ECMAGROUT PU FOAM INJECTION SERIES | |
ECMAGROUT PU F 200 | 1 Component PU Foam Injection to Stop Heavy Water Leakages |
ECMAGROUT PU F 240 | 2 Component PU Foam Injection to Stop Heavy Water Leakages |
ECMAGROUT PU RESIN INJECTION SERIES | |
ECMAGROUT PU R 420 | 2 Component PU Resin Injection for Permanent & Elastic Sealing, can accommodate movements |
ECMAGROUT PU R 440 | 2 Component PU Resin Injection for Permanent & Structural Sealing (high mechanical properties) |
ECMAGROUT COMBINATION INJECTION (DUAL PERFORMANCE: FOAM + RESIN IN SINGLE PRODUCT) SERIES | |
ECMAGROUT PU M 620 | 2 Component, 2 in 1 Product (Foam & Resin in a single product) to stop water leakages and for Permanent & Elastic Sealing, can accommodate movements |
ECMAGROUT PU M 640 | 2 Component, 2 in 1 Product (Foam & Resin in a single product) to stop water leakages and for Permanent & Structural Sealing (high mechanical properties) |
ECMAGROUT PU GEL INJECTION SERIES | |
ECMAGROUT PU G 800 | 1 Component, Water-reactive, Hydrophilic, PU Gel Injection System |
ECMAGROUT PU G 820 | 2 Component, Water-reactive, Hydrophilic, PU Gel Injection System |
ECMAGROUT ACRYLATE GEL INJECTION SERIES | |
ECMAGROUT MA G 900 | Hydrophilic, Water-reactive, Methacrylate injection system |
Please contact the ECMAS team for more details on PU Injection solutions offered by ECMAS Construction Chemicals India Pvt. Ltd.
Rajeev Gupta
(Business Head – Construction Systems BU)
ECMAS Construction Chemicals Pvt. Ltd.
Mobile: +91 9811426707, 9350102219
e-mail: rajeev.gupta@ecmas.co.in
web: www.ecmas.in, www.ecmas.com
Cookie Consent
We use cookies to personalize your experience. By continuing to visit this website you agree to our Terms & Conditions, Privacy Policy and Cookie Policy.