Efficient re-utilisation of trenched material in construction projects
By Edit Team | August 12, 2022 6:55 pm SHARE
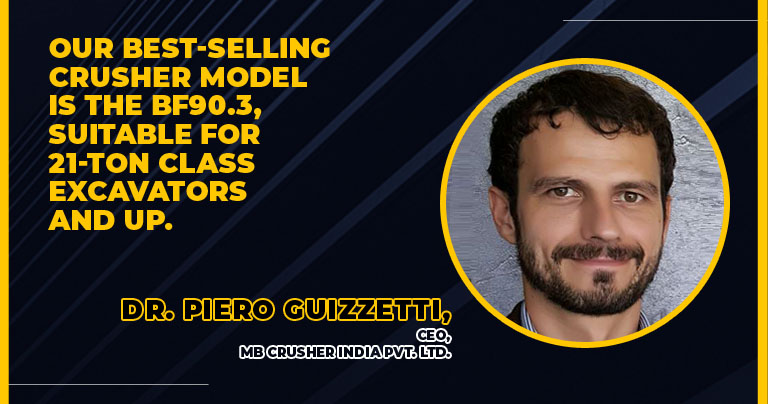
Dr. Piero Guizzetti, CEO of MB Crusher India Pvt. Ltd., illustrates the value of raising crushing productivity at the project location.
What are the ongoing trends in the crushing and screening/sand washing market in the Indian infrastructure business?
India is the world’s 2nd largest aggregate consumer. With the government of India’s continued emphasis on infrastructure development, aggregate demand will continue to grow steadily and significantly in the medium term. The aggregate industry is very fragmented in India and is mostly dominated by local players and small captive players who own small quarries and low-capacity plants. We see M-sand demand as particularly strong owing to the ban on natural sand mining in several states of India.
Wherever raw material is available, the market increasingly appreciates at-site screening. Our on-site mobile screening solutions, the MB-S and MB-LS series, are witnessing this firsthand. For pipeline projects, trenched material can be promptly and efficiently re-utilised for backfilling purposes.
Which stone/rock crushers are mainly deployed at project sites to ensure high productivity? What are the key highlights of your crushing and screening equipment?
Our best-selling crusher model is the BF90.3, suitable for 21-ton class excavators and up. Once attached, it immediately turns the base machine into a crushing unit, with no additional operating cost and/or auxiliaries required. It is an ideal mobile solution that can be moved from site to site with relative ease for the applications and project sizes where we find the greatest pertinence. And meeting productivity requirements with critical savings vis-à-vis procurement from own mines and/or third-party suppliers.
What innovations are happening in your organisation to add capacity and reliability to your equipment?
We at MB invest heavily in R&D. On the back of 10 years’ worth of data specific to India, thanks to our direct presence in the country, we have enhanced our bucket crushers to suit better the particular characteristics of Indian stone and materials and operations. We have also further enhanced the weight distribution of our machines. Thereby ensuring an even better experience for the operator and zero impact on the base machine. We have been able to do this thanks to our leadership in the market, both internationally and in India.
Can you talk about your current ongoing projects? Which equipment have you deployed for speedy project completion?
Recently, we deputed our Crusher Bucket BF90.3 at 16,700 feet above sea level in the northern mountainous region of India to undertake a road construction job. Considering the geographical location covered in severe snow for the majority of the year, installing any other traditional solutions was not possible as there was no proper connectivity to the grid. The project was considerably behind schedule. Upon installing MB Crusher Bucket BF90.3 on their excavator, the client could make up for lost time and meet the project timeline.
Cookie Consent
We use cookies to personalize your experience. By continuing to visit this website you agree to our Terms & Conditions, Privacy Policy and Cookie Policy.