Evaluation of Aeration System in Effluent and STPs
By Edit Team | September 19, 2016 10:42 am SHARE
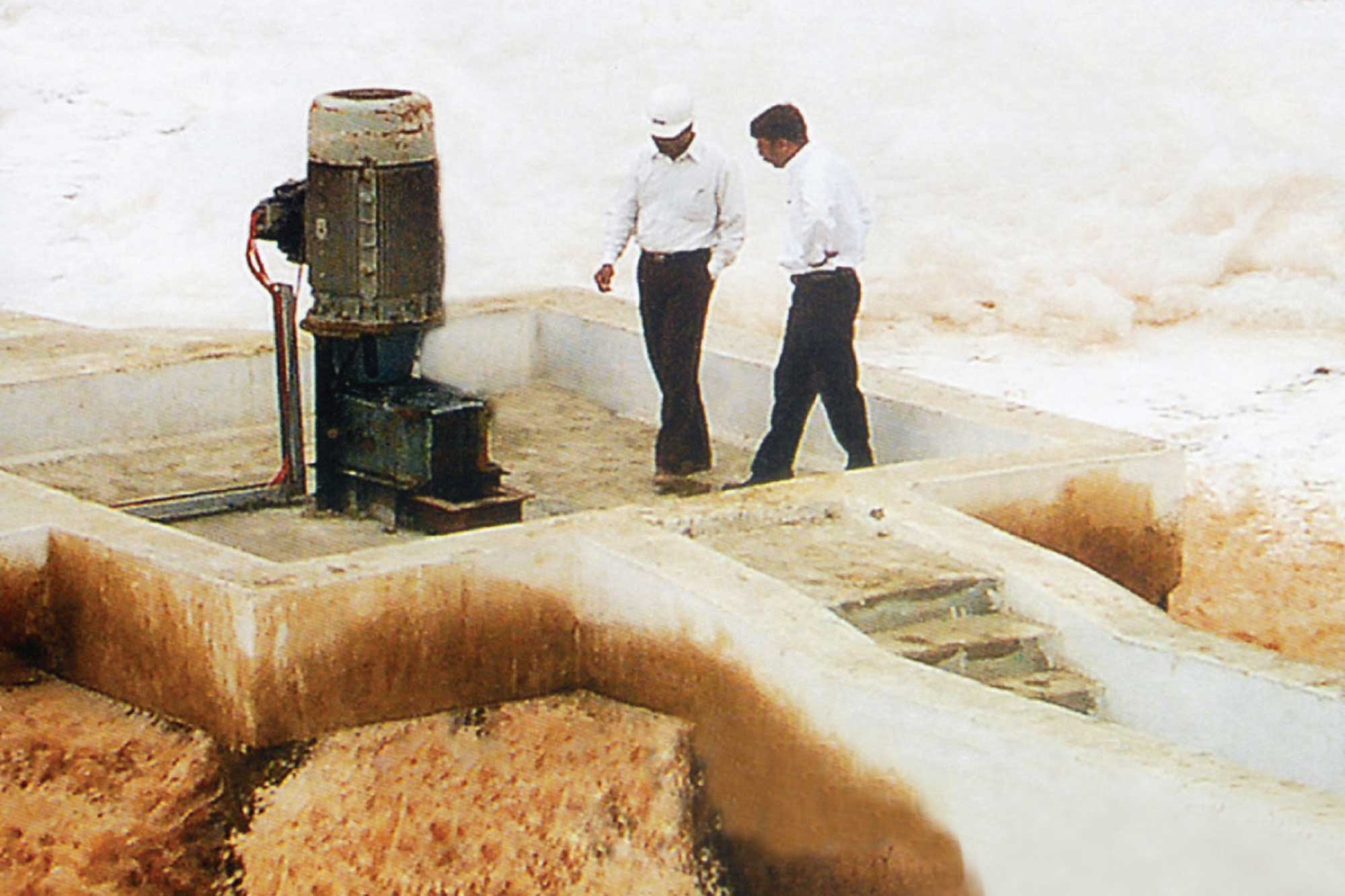
Evaluating Aeration System, that includes a total performance and cost of operation analysis is critical. The components of this analysis should include an evaluation of the initial capital cost of system installation, all operating and energy costs, and projected maintenance costs. Also included should be an analysis of how well the systems perform the four basic functions required of all Aerators:
• Provide sufficient Oxygen Transfer to promote biological treatment.
• Provide sufficient mixing to ensure homogeneity of mixed liquor suspended solids and to prevent solids settling.
• Respond to varying process conditions to maximize energy efficiency.
• Provide reliable service, without costly maintenance and downtime, and without reduction in oxygen transfer capability.
Why Mechanical Aerators fail
Even though there is NO Economical solution of Mechanical Aerators to achieve output results in Effluent / Sewage Treatment Plant with Low maintenance, minimum operation cost and long life of 10 – 15 years in Aeration System, it consumes more energy OR it fails in achieving output results after a period of time.
Will the same 20 HP Aerator Impeller work in the Aeration Tank depth of 3 mtrs/ 3.5 mtrs./ 4.0 mtrs/ 4.5 mtrs/ 5 mtrs SWD ?
The simple answer to the question is NO, because every Aerator impeller has its own design having its own influence zone, capacity to cater particular depth and size of the Aeration Tank. One knowingly has to over design the Energy required if the Aeration tank depth is more than 2.5 mtrs. In Aeration System, even though the requirement to achieve the output results is of 20 HP Energy. They always consider MIXING EFFICIENCY of Aerator, as there is NO solution OR Provision in the mechanism they have to recommend and install Higher HP Aerators ( say e.g. 30 HP ).
When the aeration tank depth is more than 2.5 mtrs. The water pressure increases and the Aerator Impeller is not able and it does not have the capacity to break the water pressure and to lift the settled sludge from the bottom floor level ( as it has its own limitations ) and cannot keep the sludge in suspension. As the sludge is settled at the Bottom Floor Level of Aeration Tank it creates septic conditions hence, the Dissolved Oxygen in the aeration tank is reduced and the results are not achieved.
It is very simple to understand that solubility of the Oxygen will be less due to Missing of Mixing Criteria which is equally important in any Aeration System, Results cannot be achieved.
Calculating the Energy required in Aeration System is very EASY as per the formula, but it is very difficult to conclude that the calculated energy will offer the desired results in Aeration System, even though more energy consuming Aerators are installed. This is because, the experts are not confident for the Oxygen Transfer Efficiency of the Aerators as the manufacturers are not able to show the witness test of Oxygen Transfer efficiency of aerators which is required and also it is the moral responsibility of any manufacturer to check the oxygen transfer efficiency of the aerator before committing the efficiency of the aerator.
Let’s take an example to have a more clear idea. Say, suppose the requirement is of 28 Kg of O2/ Hr and if the Oxygen Transfer Efficiency of the Aerator considered as 1 Kg of O2 or HP or HR at field conditions, the Aerator HP required will be 28 HP say 30 HP.
In the same way if the manufacturers or experts are confident regarding achievement of Oxygen Transfer Efficiency of the Aerator is 1.4 Kg of O2/ HP/HR at field conditions then the Aerator HP required will be 28 ÷ 1.4 = 20 HP. So saving of 10 HP i.e. 7.5 KW / hr. can be achieved.
Hence, form the above information, one can conclude that due to missing of mixing efficiency in higher depths of aeration tank and oxygen transfer efficiency, considering low oxygen transfer efficiency at field conditions the aerators consuming high energy aerators are installed even the requirement is of low energy consuming aerators.
Recently, environ got an opportunity to replace 12 nos. Of 50hp existing aerators installed with 12 nos. Of 30hp enviroin energy efficient aerators at m/s. Star paper mills ltd. – Saharanpur (u.P.).
Here is the case study as to how a huge amount will be saved every year after installing 12 nos. Of 30hp environ energy efficient aerators m/s. Star paper mills ltd., That will save 240hp i.E. 180Kw in their aeration system.
Case study
At M/s. Star Paper Mills, the Parameters of the Effluent are as:
Effluent Inlet Flow: 12000 – 15000M3/day.
Inlet BOD: 280 – 320ppm.
Inlet COD: 600 – 700ppm.
TDS of Effluent: 1800 – 2000ppm.
Aeration Tank Size: 40M x 104M x 4.5M SWD.
Existing Aerators installed: 12 Nos. of 50HP –Fixed Type.
Electrical charges: ` 5/- per unit.
Now, calculation of Aerator HP required at M/s. Star Paper Mills:
Flow: 15000M3/day x Inlet COD 700ppm ÷ 1000 = 10500 kg. of COD /day.
Now, to reduce 1 kg. of COD, 1 kg. of O2 is required i.e. 10500 kg. of O2 required per day ÷ 24 hrs =437.5 kg. of O2 required per hour.
The Oxygen Transfer Efficient of ENVIRON Energy Efficient Aerators is 1.4 kg. of O2 per HP/HR at FIELD CONDITIONS. So, HP required will be 437.5 kg. of O2 ÷ 1.4 kg. of O2/HP/HR Oxygen Transfer Efficiency of ENVIRON Energy Efficient Aerators = Total 312.5HP required per hour ÷ 12 Nos. Aerators = 26.04HP Say Total 12 Nos. of 30HP Aerators are required.
So, saving will be 12 Nos. of 50HP Aerators Existing i.e. 600HP – 12 Nos. of 30HP Aerators proposed i.e. 360HP = 240HP i.e. 180KW Saving. Now, the Electrical Unit charges are ` 5/- per unit x 180KW Saving = ` 900/- Saving per hour x 24 hours = ` 21,600/- Saving per day x 365 days = ` 78,84,000/- Saving per year.
Working of environ energy efficient aerator
The Top Impeller is having very high Oxygen Transfer Efficiency and the Bottom Impeller is provided for rigorous Mixing.
By providing the additional impeller, vortex is created at the bottom, which breaks the pressure of the effluent and does not allow the sludge to settle at the bottom floor level of the aeration tank and keeps the sludge in suspension.
It is very simple to understand that, due to rigorous and thorough mixing, the solubility of the oxygen is more. So, oxygen transfer efficiency is increased with less energy consumption compared to other aeration system. Hence, energy saving.
Environ Engineering Company – Vadodara are the manufacturers of effluent / sewage treatment plant machineries like: fixed and floating type slow speed energy efficient aerators from 2 hp to 150 hp ratings, centre drive clarifiers, clariflocculators, high rated solid contact clarifiers (HRSCC), thickners from 2-metre diameter to 25-metre diameter, mixers, agitators, stirrers, flocculators from 0.5 hp to 40 hp ratings, api oil separators etc.
Cookie Consent
We use cookies to personalize your experience. By continuing to visit this website you agree to our Terms & Conditions, Privacy Policy and Cookie Policy.