Fabrication market is transforming with infrastructure demand
By Admin | November 1, 2022 6:32 pm SHARE
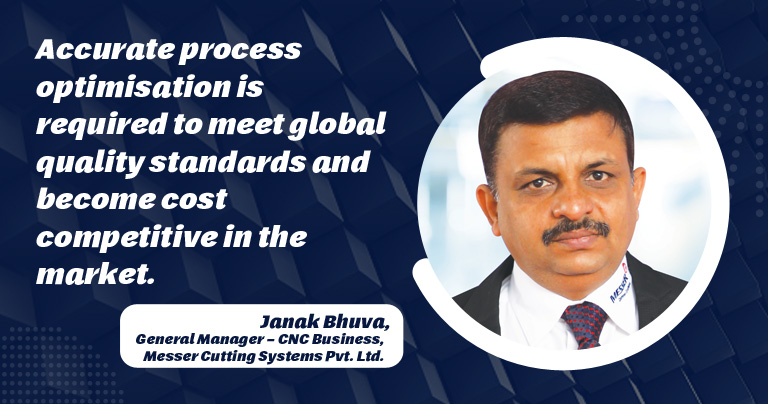
The market’s growth is expected to be aided by rising demand for machining and efficient fabrication techniques. Noting this, Janak Bhuva, General Manager – CNC Business, Messer Cutting Systems Pvt. Ltd., highlights that the growing demand is fuelled by programmed production techniques in the element fabrication sector, which assist in creating trustworthy fabrication amenities. The increasing demand for and supply of metal fabrication across numerous industries, such as automotive, aerospace, military, and manufacturing, is expected to boost the market growth. Increased advancements in sectors like computerisation and robotics are paving the way for new technologies and solutions to be implemented in the metal fabrication market. It is expected to rise in the next year due to increased demand for metal processing and machining in various growing economies worldwide.
Constant increase and utilisation for metal processing and machining
The Indian metal fabrication market is expected to grow at a CAGR of more than 5 percent between 2022 and 2027. It is considered one of the fastest-growing markets in the global metal processing industry. The main advantage of the metal fabrication industry in India is the availability of a workforce at a competitive cost. The Indian metal fabrication market is highly fragmented, with many small and medium-sized businesses and EPC firms present. The rising demand for goods and services across various sectors in India, combined with the fact that global manufacturing companies focus on diversifying their production by setting up low-cost plants in countries like China and India, is expected to drive the Indian manufacturing sector.
Factors behind the fast growth of the metal fabrication industry in India
Factors such as government-initiated infrastructure projects, modernisation of railway infrastructure and manufacturing facilities, development of metro networks in all major Indian cities, privatisation and modernisation of defence projects under the “Make in India” and “Atmanirbhar Bharat” initiatives are driving the metal fabrication industry in India. The big cluster of MSMEs present in India is actively supported by the government and acts as a driving force to boost the metal fabrication industry. As demand grows, the requirement for skilled labour and automation is also increasing. Optimisation of the fabrication process is essential to match the global standard in terms of quality and also to become price competitive on the world stage.
Thermal cutting processes in metal fabrication operations
Metal fabrication is one of the integral parts of industrial operations. It involves certain processes that are used to cut, shape, or mould metal structures into the final product. Any fabrication operation starts mainly with the cutting process. For the three primary metals, i.e., carbon steel, stainless steel, and aluminium, the cutting process will be carried out mainly by plasma, oxyfuel, laser, and water-jet processes. In India, the plasma, oxyfuel, and laser cutting processes drive the fabrication industries on a very large scale. The right application is vital and will give competitive advantages in industries. Engineering and manufacturing departments constantly look for an edge in the battle to reduce costs. If we talk about the application area for the thermal cutting process, the graph below will give you clear ideas for selecting the cutting process.
The oxyfuel process has limitations; there is no alternative for this process.
We Messer has introduced a unique torch, “ALFA”, to carry out this process in the most optimum way to reduce costs and improve cut quality to optimise this process and reduce operating costs. Additionally, this torch will reduce the operator’s skill required to carry out our oxyfuel process. Furthermore, automatic in-build ignition and an in-built height control system will also reduce gas consumption during operation and optimise the use of plates. Plasma cutting is the second most crucial process. This process has also improved its footprint in the fabrication industry over decades. This process started with air and oxygen plasma and is now upgraded to high-definition plasma, resulting in improved consumable life, cutting quality, and productivity.
Most fabrication industries are also engaged in edge preparation of the plate for welding surfaces. In this scenario, plasma cutting with an angle will be essential in providing optimum solutions. We, Messer, are pioneers in providing solutions for edge preparation in the fabrication industry. Our newly introduced, high-speed ELEMENT machine with a bevel tool is the perfect solution for this requirement. Our bevel machines are used successfully in the worldwide yellow goods, shipbuilding, windmill, and railway industries.
Laser cutting: Fiber laser cutting is the latest trend in the sheet metal industry. Every fabrication industry, particularly the thin sheet industry, wants to have this process due to its cost-effectiveness, cutting quality, and high productivity. Fabricators need to choose the right products for their application. Messer India offers very reliable and unique solutions in this process. Our flagship products, like Fiber Light and Fiber Blade machines, cater to these industries.
Advancements in technological tools used in metal fabrication
The metal working market uses a variety of ERP technologies and software. This facilitates data access and speeds up the decision-making process. Companies in the metal fabrication industry are benefiting from increased computer-aided manufacturing technologies, which are helping them improve operational efficiency and production.
Material handling process—An area for improvement in terms of thermal cutting machine duty efficiency
Plate/material handling also plays a vital role in the productivity of any fabrication unit. Processes like laser and plasma need huge material handling requirements to feed the machines and remove the cut parts. We are witnessing a major bottleneck in today’s fabrication industries due to inadequate material handling infrastructure in fabrication units. Even though cutting equipment is very reliable, fast, and can run continuously, its use is typically limited to 60 to 70 percent of the time due to in-feed and out-feed issues or a lack of proper material handling in units. Material handling is key for any fabrication unit to utilise world-class equipment optimally. And as always, Messer India is always at the forefront of visualising the fabrication industries’ requirements and coming up with solutions for material handling. We have recently launched a cost-effective material handling solution for the fabrication industry, particularly for the plasma and laser cutting processes.
Cookie Consent
We use cookies to personalize your experience. By continuing to visit this website you agree to our Terms & Conditions, Privacy Policy and Cookie Policy.