FAQ: Challenges in powder coating
By Edit Team | July 4, 2017 10:39 am SHARE
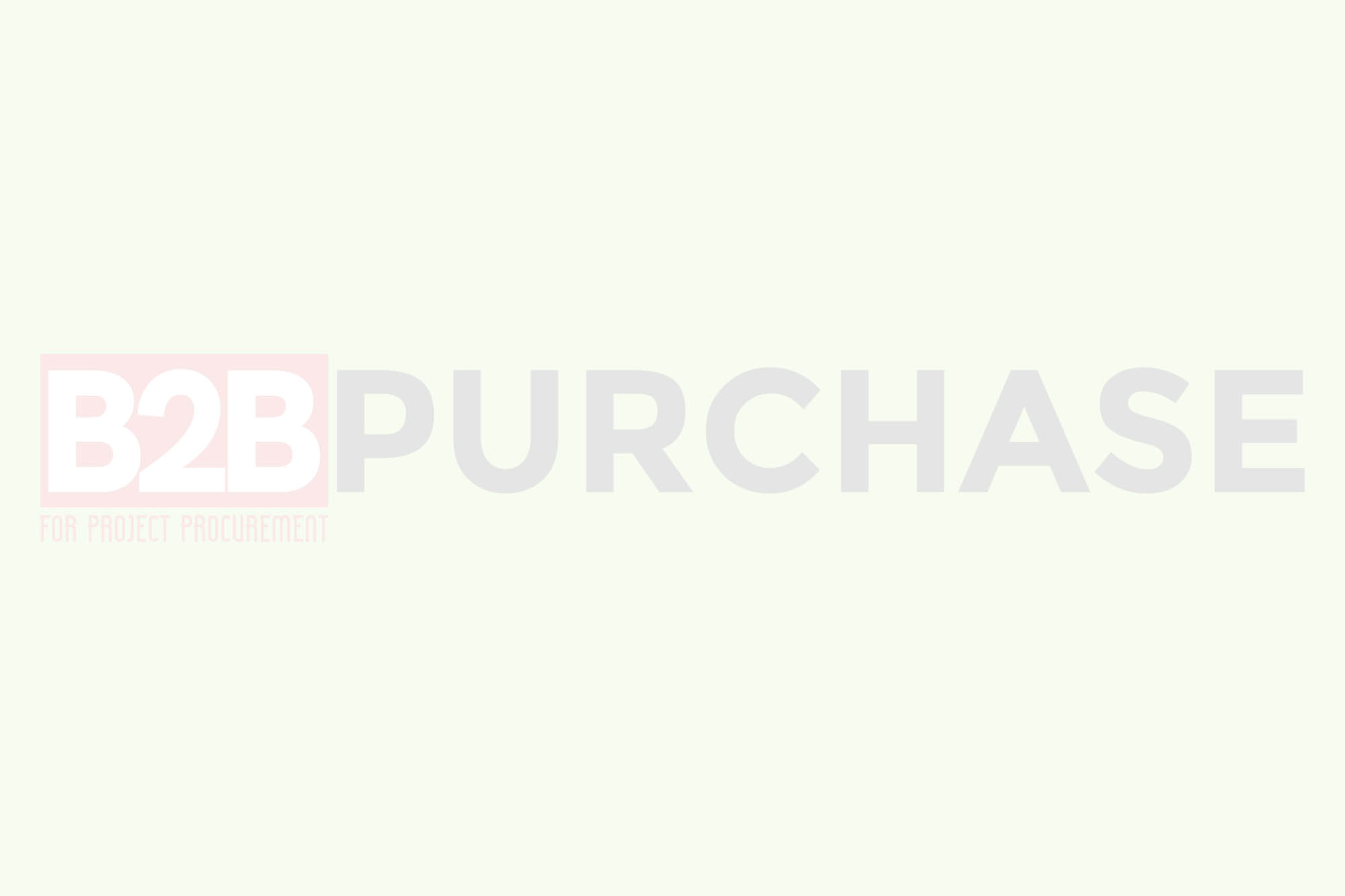
Pradeep Vaidya, CEO of Innovative Coating Industries explains the process of powder coating.
Pradeep Vaidya, CEO, Innovative Coating Industries
In the procedure of powder coating the powder that is used for the process is a mixture of finely ground particles of pigment and resin, which is sprayed onto a surface to be coated by corona or tribo charging technique.
Frequently Asked Question (FAQs)
What is powder coating process?
Powder coating is an advanced method of applying a decorative and protective finish to a wide range of materials. The powder used for the process is a mixture of finely ground particles of pigment and resin, which is sprayed onto a surface to be coated by corona or tribo charging technique. Charged powder particles adhere to the electrically grounded surfaces until heated and fused into a smooth coating in a curing oven. The result is a uniform, durable, high-quality and attractive finish.
Why is pretreatment required for powder coatings?
Powder coatings can provide improved performance over liquids when applied to a properly pretreated part. As powder does not have solvents, you need to make sure the washer does a good cleaning job. Iron phosphate is the most frequently encountered pretreatment used with powder coatings. However, if the highest level of performance is required, zinc phosphate will work admirably with powder as well. Proper prior preparation prevents poor powder performance.
What is the best cleaner for powder coating?
Base metal of the work piece, soil being removed, bath temperature, contact time, oil removal capabilities, environmental considerations, etc. must be taken into account when deciding. The bottom line is that you need to get your parts clean, safely, so the steps following in the pretreatment process will function properly.
Why, at times, powder doesn’t adhere to a part?
Many factors affect powder deposition on a part. However, there are some more common reasons for poor powder transfer efficiency. With corona-charging systems, a poorly grounded part is the most common cause of low transfer efficiency. Insufficient charging is caused by several factors including powder formulation is not suitable for tribo-charging applications.
Why are inside corners or channels sometimes difficult to coat?
Difficulty experienced when coating recessed areas is called as “Faraday cage effect”. It is due to the fact that an electric field always goes to the nearest grounded surface and is strongest around sharp edges. Electric field from the gun concentrates on the edges and does not penetrate into deep corners, compromising powder deposition.
What are the air humidity and temperature requirements in a powder coating operation?
Ideal ambient conditions are temperatures between 15 to 27 C with 40 to 60 per cent humidity. Temperature and humidity of the compressed air are even more important. Here, for corona-charging systems, the pressure dew point of the compressed air should not exceed 3 C @ 100 psi line pressure.
How do I get good powder coverage into Faraday areas?
Faraday cage effect defines a condition that occurs when parts are coated that have recesses, inside corners, channels, or protrusions on their surfaces. The Faraday cage is the area of the part where the external electrical field does not penetrate. Powder coating of recessed areas is often complicated. For the successful coating of Faraday areas, the following conditions must be met:
• Powder has to be well charged,
• Airflow must be sufficient to deliver the powder inside a recess but not excessive to preclude powder deposition
• The external electric field must be controlled to reduce the “push” for powder particles to deposit on the edges of a Faraday cage.
Are there powders for interior or exterior use?
One of the most important considerations in defining the end use performance is weather ability. Outdoor exposure results in absorption of ultraviolet energy, which can attack the organic binder and result in gloss loss and colour change. Due to a tendency to chalk, epoxies and epoxy containing hybrids are generally not recommended for outdoor use when aesthetics is a primary concern. Polyesters and acrylics on the other hand provide excellent UV light stability and typically find use in architectural, automotive, lawn and garden as well as outdoor furniture markets.
Contact:
Pradeep Vaidya, CEO,
Innovative Coating Industries
MIDC, Pune
Thane: B-7/701,
Vedant Complex, Vartak Nagar Naka,
Thane (West) – 400606
Mobile: 09820181738
Email: puvpromtech@gmail.com
Sonia Vaidya, Tech Mktg Executive, Thane
Tele: +91-22-25883265, 9819813015
Email:soniavaidya30@gmail.com
Cookie Consent
We use cookies to personalize your experience. By continuing to visit this website you agree to our Terms & Conditions, Privacy Policy and Cookie Policy.