FAQ: Ideal painting process for steel fabrications
By Edit Team | April 14, 2016 9:26 am SHARE
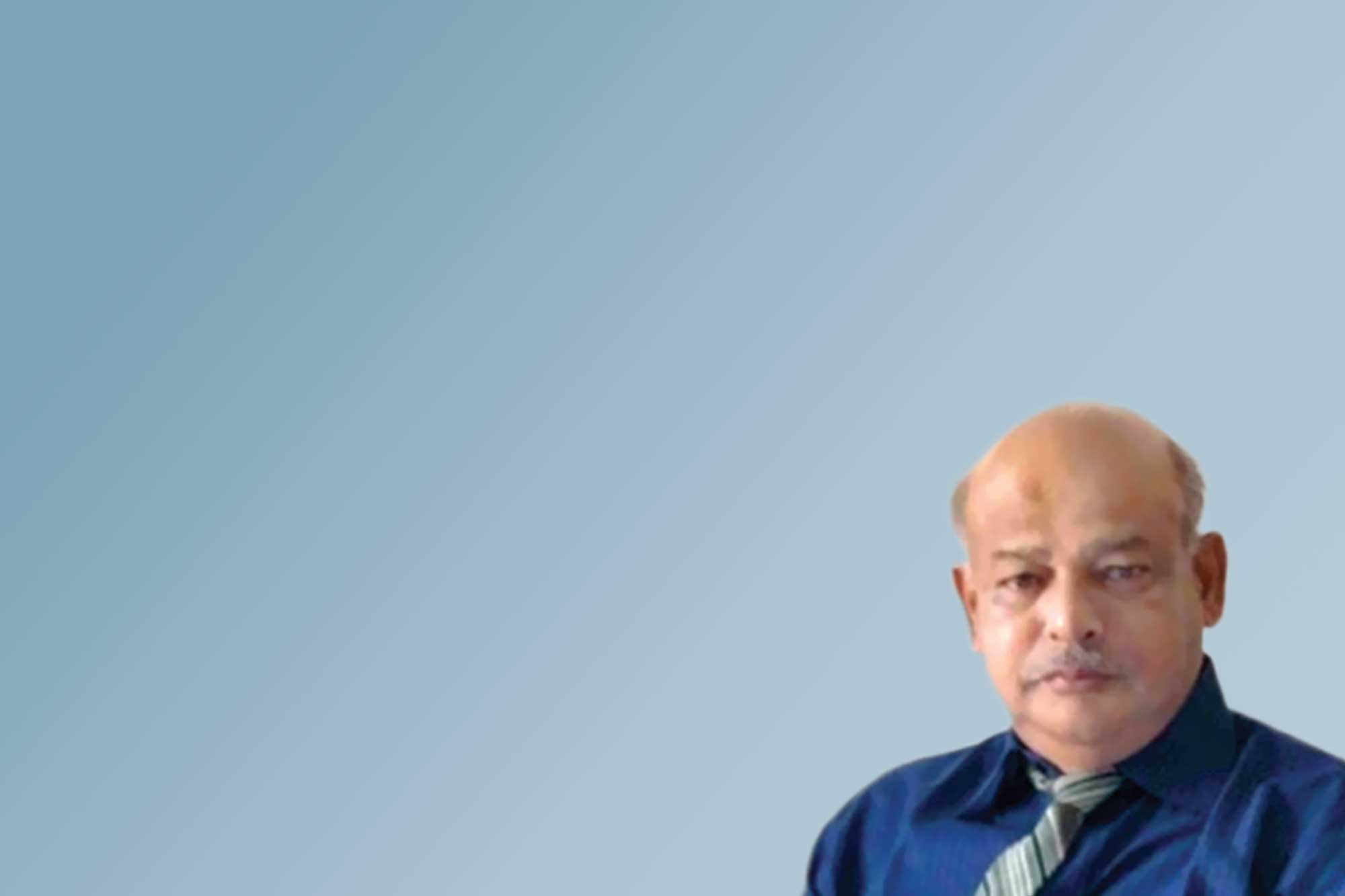
Selecting the ideal painting system for structural steel fabrications and galvanised steel fabrication is a daunting task for Maintenance Managers and Chief Engineers. It becomes all the more critical when the steel fabrications and the machineries or equipment have to be installed in the harsh working atmospheres such as coastal areas, highly humid areas, nearly salty and saline atmosphere, areas with steam, water vapour, and chemical fumes, places with high operating temperature. For getting the optimum results from a painting system in terms of long equipment life, high anti-corrosion and the aesthetics, MS paints offered by Pune-based Innovative Coating Industries can be used.
Frequently asked questions on MS paints:
For which types of steel fabrications and the industries sectors this painting process is recommended?
It is recommended for painting and repainting of MS and GI structures, fabrications, PEBs, metal buildings, off-shore platforms construction, all rusted and non–rusted steel fabrications, solar power plants, HVAC plants, ready mix plants factory trusses, support structures, tank farms, chimneys, steam, water, chemicals and petro-solvents pipelines, columns, I-beams, bridges, dams, transmission towers, telecom signal towers, EOT cranes, formworks and scaffoldings, AC ducts etc.
Which products should be selected?
What are the basic chemical antirust properties such products must have? The product selected must be safe for workmen, low fuming, non-toxic and readily available. These products must have min 12 months of shelf life and the metal cleaners shall be water based (non flammable). Premium grade anti-corrosion products from Innovative Coating Industries are quite useful in this purpose. The products offer excellent corrosion protection to mild steel fabrications from atmospheric rusting, oxidation and surface chipping corrosion. These chemicals and the paint coatings must have excellent adhesion to the metal or substrate as per recommended Indian standard specifications.
What is the process sequence to be followed?
The exact sequence to be followed is: pre-cleaning, derusting (surface rust removal), and painting.
Pre-cleaning: Complete removal of oil and grease, surface rust must be ensured. This can be carried out by chemical cleaning, solvent cleaning, sand blasting, sand papering, grinding, mechanical cleaning or any other means. Shot blasting, sand blasting, grit blasting are the best methods for surface cleaning.
Total removal of residual water, cleaning of even traces of acidic cleaners, all foreign matters, dust, dirt from the cleaned surface must be ensured. These traces of impurities can cause hydrogen embrittlement in the microscopic pores of the metallic surface. These impurities promote sub-surface corrosion after some duration. Trapped hydrogen will try to escape to atmosphere and will rupture the finished paint however it may be thick and strong. The opened up areas of paint coating or film on steel now provide nucleus for further rusting.
Derusting: Chemical derusting for all corroded mild steel fabrications and structural steel is easily accomplished by use of RUSTOGEL 1406 offered by Innovative. These cleaners are based on phosphoric acid, solvent, wetting agents and foaming agents. Phosphoric acid is a rust preventive acid. Being in gel format, the chemical is quite useful for derusting and cleaning and maintenance of all heavy steel fabrications in vertical and horizontal positions.
Painting: Innovative’s recommended products are ZINKOTE 20 GP ZINKOTE 20 Premium. Zinkote GP is manufactured using 99 per cent pure zinc dust rich paint for highest corrosion resistance. Coverage: 2 sq.m. zinc contents in DFT is 88 to 92 per cent. Zinc deposit coating: 20-25 microns offers highest anti-corrosion properties over a long period. Conforms to ASTM A 780.
ZINKOTE 20 Premium is manufactured using 99 per cent pure zinc flakes rich paint for highest corrosion resistance. Coverage: 2 sq.m. zinc contents in DFT 88 to 92 per cent. Zinc deposit per spray coating: 20-25 microns. Maximum two coats are recommended. Conforms to ASTM A 780.
Is zinc rich paint for cold galvanising available in ready-to-use aerosol spray format for on-site use? Yes. Zinc rich paint is also offered as Zinc Metal Spray (light grey finish) and Zinc Bright Spray (silver bright finish) in 500 ml self spray aerosol spray cans.
What are the advantages of using aerosol sprays?
Zinc metal spray (light grey finish) and zinc bright spray (silver bright finish) offered in 500 ml self spray aerosol spray cans are most convenient for on-site use, offer very uniform zinc coating film. The aerosol cans are extremely user friendly, are used at work sites, quite handy light weight for using at greater heights.
Contact
Pradeep Vaidya, CEO, Innovative Coating Industries,
MIDC, PuneThane: B-7 / 701, Vedant Complex,
Vartak Nagar Naka, Thane (West) – 400 606
Mobile: +91-9820181738
Email: puvpromtech@gmail.com
Sonia Vaidya,
Tech Mktg Executive, Thane
Tele: +91-22-25883265, 9819813015
Email: soniavaidya30@gmail.com
Cookie Consent
We use cookies to personalize your experience. By continuing to visit this website you agree to our Terms & Conditions, Privacy Policy and Cookie Policy.