GFRP in infrastructure applications: From a layman’s perspective
By Staff Report | October 25, 2024 5:42 pm SHARE
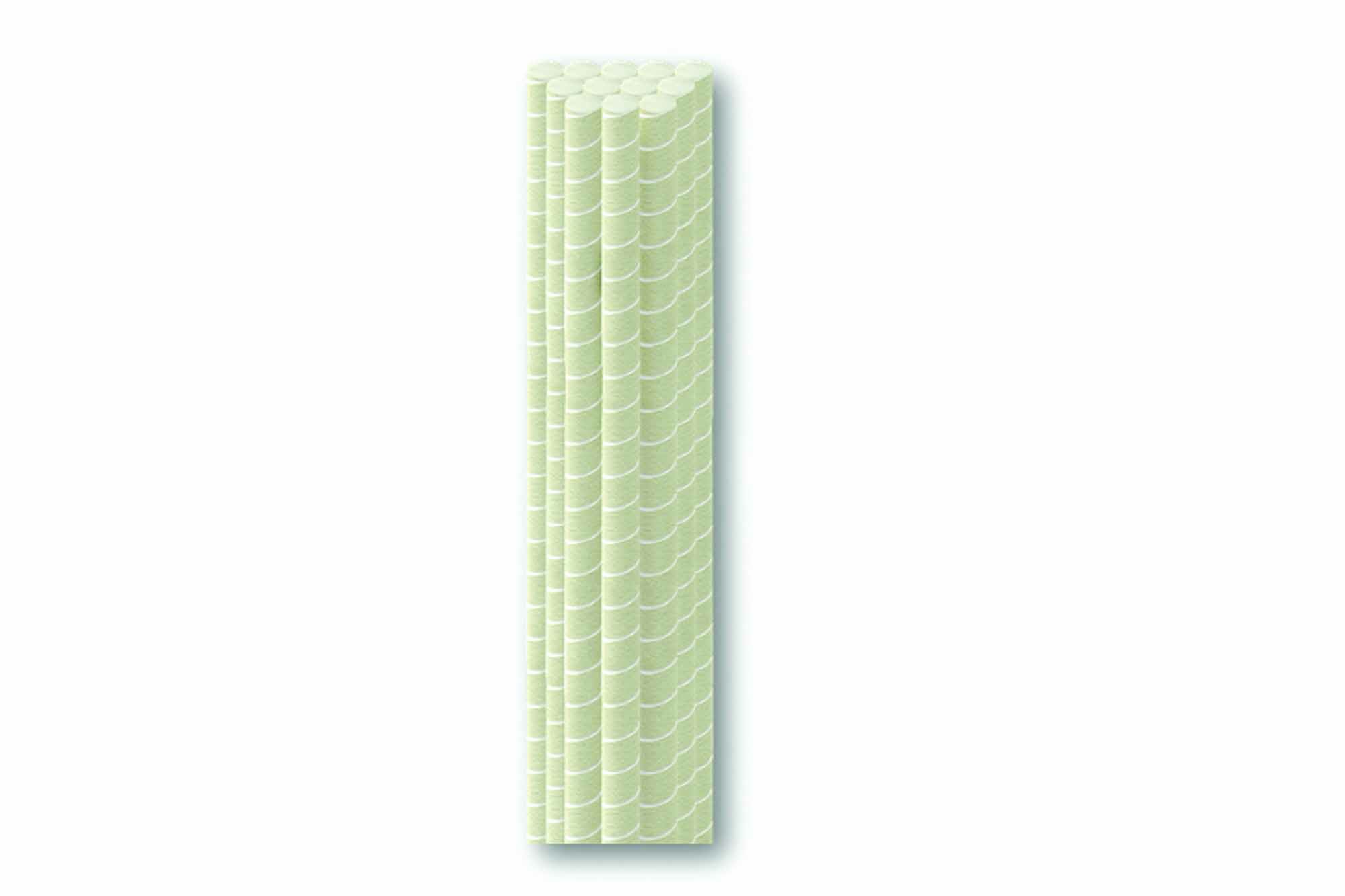
You may be surprised to learn that Glass Fiber Reinforced Polymer’s origins trace back to the 1930s, yet its potential in infrastructure is still unfolding. This article breaks down the basics of GFRP, examining its benefits like corrosion resistance and sustainability and why it may soon replace steel in various construction projects.
Fiber Reinforced Polymer (hereafter called FRP) has yet to be invented. A little digging in the history book shows that the roots were conceived in the late 30’s in the USA, and many experimental and demonstrative projects were conducted in the USA and Europe after that. The Japanese people introduced design guidelines for GFRP in 1996, which served as a good foundation for many upcoming versions of codes and guidelines. Although it has been used extensively now in applications such as storage tanks, wind turbine blades, boats, pipes, aircraft fuselage, etc., the commercial use of GFRP products for permanent usage in infrastructure projects is still “novice in the field” at least in developing economies like India. The applications mentioned above will see FRPs in various shapes and product forms, but for Infrastructure applications, we will mainly discuss solid round profiles like rebars, bolts, anchors, etc.
The composition
The FRP products are made of Fibers impregnated with polymeric Resins. The fibre determines the product’s strength, and Resin binds these fibre elements together, enabling the load transfer from one fibre element to another with the additional duty of protecting it. Various forms of FRPs exist based on which type of fibre is used, like Carbon, Aramid, Basalt, etc., but we will limit our discussions to Glass Fiber, which is used extensively in infrastructure projects.
On the other hand, choosing the right type of resin is extremely important as this will directly impact the mechanical and long-term properties of the GFRP system and the application under consideration. The basic option available with resins could be thermoplastic (reshaped using temperature cycles) or thermosetting (which generally does not change the shape when heated unless decomposed at high temperatures). Again, our area of interest is thermosetting resins only, examples of which are Epoxy, Polyesters, and Vinyl Ester (Most Preferred).
The most common and popular FRP manufacturing method is the pultrusion process, in which fibre filaments are pulled from the roving to undergo a resin bath and then cured in a heated die with necessary surface preparation (sand coating or surface deformations, etc.).
Key reasons why GFPR is arguably the best replacement for steel in infrastructure projects
The infrastructure industry has long relied on steel, a fundamental material known for its strength and versatility. However, as projects increasingly demand materials that offer high performance and sustainability, Glass Fiber Reinforced Polymer (GFRP) is emerging as a compelling alternative.
Corrosion resistance
One of steel’s major limitations is its susceptibility to corrosion, particularly in harsh environments such as coastal areas, underground, or chemical plants. Steel structures exposed to water, salt, and chemicals require regular maintenance to prevent rust, which leads to increased operational costs over time.
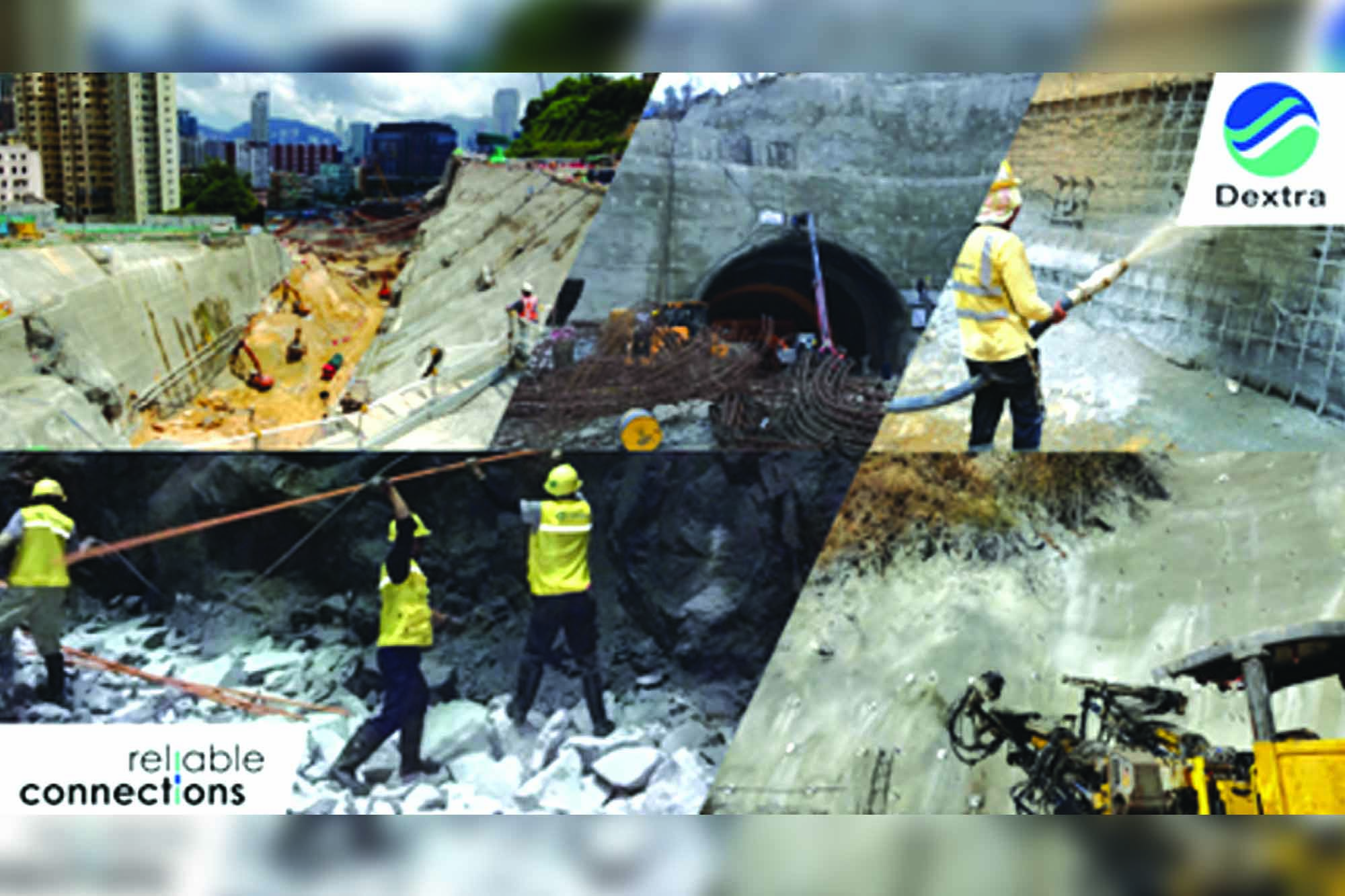
GFRP, on the other hand, is inherently corrosion-resistant. As a non-metallic composite material, it does not rust or degrade in aggressive environments, significantly reducing maintenance requirements. This property makes GFRP particularly useful in marine applications, chemical plants, water treatment facilities, and underground structures where corrosion is a persistent challenge.
High strength-to-weight ratio
Steel’s high density, while beneficial in terms of strength, is also a drawback when weight is a concern. Steel’s weight can impose limitations on design, increase transportation costs, and complicate installation processes.
GFRP, however, offers a superior strength-to-weight ratio. It is as strong as steel but significantly lighter, making it easier to transport, handle, and install. This property is crucial in applications like bridge decks, tunnels, and high-rise buildings, where reducing weight can also reduce structural loads, leading to overall cost savings in construction and engineering design.
Electrical and thermal insulation
Steel, a good conductor of electricity and heat, requires insulation in certain applications to prevent accidents or inefficiencies. In contrast, GFRP is a natural insulator. Its electrical non-conductivity makes it ideal for power plants, electrical substations, and other environments where electrical safety is paramount. Additionally, GFRP has low thermal conductivity, offering thermal insulation benefits, which are valuable in energy-efficient building designs and industries where temperature control is critical.
Durability and longevity
The inherent corrosion resistance and chemical inertness of GFRP contribute to its long service life, even in the most demanding environments. While steel structures need frequent maintenance and corrosion protection treatments, GFRP structures typically last longer without major intervention. This longevity makes GFRP a more cost-effective solution over the structure’s lifecycle.
Sustainability
Sustainability has become a priority for the infrastructure industry, with an increasing focus on reducing carbon footprints. Steel production is energy-intensive, contributing significantly to carbon emissions. GFRP, however, offers a more environmentally friendly alternative. Thanks to its lightweight properties, it requires less energy (~40%) and emits less carbon (~60%) during manufacturing and transportation. Additionally, GFRP’s longer service life reduces the need for frequent repairs and replacements, contributing to sustainable construction practices.
Another very interesting concept promoting sustainability is the SEA-SAND SEAWATER CONCRETE (SSC), which directly impacts the reduction of CO2 from the concrete itself. SSC is essentially a combination of GFRP Rebars—sea sand and Seawater—Recycled Concrete Aggregates. Dextra is a member of “ACI Committee 243—Seawater Concrete,” which is preparing a Guide to the Use of Seawater-Mixed Concrete.
Code & design guidelines
1. International
a. ACI 440.11.22 (Building Code Requirements for Structural Concrete Reinforced with GFRP Bars and Commentary)
b. Eurocode 2 (Annexure R for FRP rebars)
c. CSA S 806 (2021)
2. India
a. IS 18255:2023 (Methods of Test)
b. IS 18256:2023 (Technical Specifications)
c. IRC:137-2022 (Guidelines)
Indicative list of GFRP applications in infrastructure projects
1. Tunnels –
a. Permanent Rock bolts for NATM Tunnels
b. Rebar + MS Fiber in TBM reinforcement, Soft eye in TBM Tunnel
2. Roads & Bridges –
a. Rebar for the deck of the bridge
b. Soil nail for Sope stabilisation applications
c. Rebars replacing permanent steel works like trenches, anti-crash barriers, etc
3. Urban Rail –
a. Anchors for UG works
4. Marine Ports –
a. Rebars for Repair Work, Sea Walls, Flatwork applications
5. Miscellaneous projects such as Warehouses, Cold Storages, Industrial Slabs, Flood Channel etc
Contact:
Bhargav Jog,
Business Development Deputy General Manager, Dextra India
bjog@dextragroup.com
+91 9619906565
Cookie Consent
We use cookies to personalize your experience. By continuing to visit this website you agree to our Terms & Conditions, Privacy Policy and Cookie Policy.