Global paint market: Decorative coatings take the lead
By Edit Team | July 12, 2023 4:48 pm SHARE
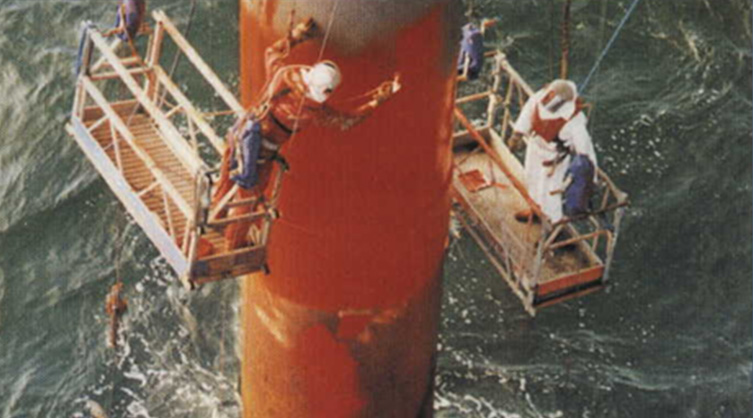
This article overviews paint coatings, focusing on decorative and industrial applications. It emphasises the need to consider substrate, location, and specific requirements when choosing a decorative coatings.
The paint coating is an easily accessible technique for protecting materials, aiming to ensure aesthetics and prevent corrosion. This technique can be broadly categorised into two types: decorative coatings and industrial coatings. Decorative coatings primarily enhance the appearance of a surface, making it attractive and colourful. In some cases, they also provide increased strength and durability.
A thorough approach involving selection, preparation, and application is necessary for decorative coatings to ensure long-term satisfaction. For instance, the distinct requirements of interior walls and external surfaces of buildings necessitate different considerations. Indoor surfaces may require waterproofing, a glossy finish, and anti-graffiti protection. At the same time, exterior walls and roofs benefit from long-lasting paint coatings, anti- fungal properties, UV light resistance, hydrophobicity, anti-dust pickup, and the ability to change colours quickly.
When selecting a decorative finish, several criteria should be taken into account. Merely considering colour is not the most optimal approach. The choice of paint should be based on the substrate, which could be concrete, steel, plastic, or wood. Additionally, it is essential to determine whether the application is for an interior or exterior wall, considering the specific location within the building, such as the main drawing room, bedroom, kitchen, or bathroom. Each area may require different options in terms of colour, atmosphere, and durability, as bathrooms and kitchens typically have more humid environments than other walls.
The market for decorative paint
Globally, the decorative paint market holds a significantly larger share than the industrial sector. According to a 2018 industry analysis, decorative paint accounted for approximately 68 percent of the USD 158 billion paint market overall. Recent surveys suggest that this proportion has increased and ranges between 75 and 78 percent.
In 2018, the global coatings market reached a substantial USD 158 billion. Within this market, decorative coatings claimed a majority share of 68 percent, while industrial coatings accounted for the remaining 32 percent. The industrial coating sector can be further categorised into various segments. Transportation, including the automotive industry, represented 19 percent of the market, while the general industry, which involves painting steel structures across multiple sectors, held a 16 percent share. Maintenance coating, which includes coatings suitable for surfaces exposed to moisture and wet conditions, occupied a 14 percent share. Powder coating and automobile refinishing each captured 9 percent of the market. The marine sector, primarily comprising naval constructions, ships, jetties, and offshore structures, contributed 5 percent. Coil coating, which directly applies paints on thin steel foils, accounted for 5 percent of the market. The packaging industry had a smaller market share of approximately 3 percent. Recent market research estimates indicate that the global paint market has grown to USD 184 billion, with a compound annual growth rate (CAGR) of 4.6 percent. Consequently, similar changes can be anticipated in other industrial sectors as well.
The selection of industrial paints begins by considering the type of resin used as the binder, which includes alkyd, acrylic, polyester, epoxy, and polyurethane- based resins. Each resin category offers numerous formulations to meet the functional requirements of specific industrial challenges. Paint coatings are classified as either conventional or high-performance based on the modifications they undergo. High- performance coatings encompass paint systems capable of achieving significant coating thicknesses. These coatings are fortified with unique pigments like mica iron oxide (MIO), glass flakes, and fibres. They can withstand harsh conditions with high humidity levels, providing increased strength and prolonged endurance. One popular example is the isophthalic ester-based polyester glass-flake coating, known for its quick-drying, toughness (due to glass flakes), and increased thickness (due to low solvent content). These coatings are commonly used in corrosive splash zones of offshore constructions in the C5M environment. Another high- performance coating is the underwater coating, created using a basic epoxy and an amine hardener with multiple amine groups like cycloaliphatic amine, utilising water repellence during application.
The carbon-to-fluorine (C-F) bond is the foundation for high-performance coatings capable of withstanding strongly acidic, alkaline, or sewage- related environments. Fluoro-polymer- based resins are essential for creating coatings that can endure highly acidic conditions. PVDF coatings offer the maximum corrosion resistance. PVDF- coated Aluminum-Composite Panel (ACP) facades, with a thin 25-micron layer, safeguard multi-story structures from UV rays and acid rain, lasting over 20 years. A high-performance coating can withstand all acids and be applied to acid and alkali storage tanks by carefully selecting and blending epoxy resin with nanoparticles. Small nanoparticles dispersed in a two-pack epoxy system provided excellent acid resistance for battery pit areas in ships and submarines, withstanding temperatures up to 250°C and resisting all acids. The silicon-oxygen (Si-O) bond is an effective method for creating high- performance coatings, especially for applications involving high temperatures. Silicon-based paints exhibit temperature resistance starting from 300°C and above. However, coatings formulated with poly-siloxane can withstand temperatures up to 650°C.
Durability is crucial when selecting industrial coatings, as many applications require corrosion protection for several years or even decades. To understand what contributes to enhanced coating longevity, we need to examine the coating system, which includes surface preparation, primer application, intermediate coat, and final top coat. The combination of these factors and the appropriate thickness determines the paint’s longevity.
The longevity of a painted structure is influenced by the composite coating, which includes a zinc-based primer providing cathodic protection. An intermediate epoxy coat is a barrier against moisture and contaminants like chlorides, carbon dioxide, and sulphur dioxide. The top polyurethane layer shields the intermediate epoxy coat from environmental elements such as UV rays, rain, and snow. Refer to Figure 2 for a schematic representation of this coating system.
Paint coatings have become integral to our everyday lives, serving multiple purposes. They protect our valuable resources and industrial infrastructure and enhance the aesthetic appeal of our homes, offices, and public buildings by adding a glossy, colourful touch. Decorative paint is prominent in the coating industry, as it caters to professional and personal settings, including commercial spaces and durable consumer goods. Within the industrial market, different categories exist, each with specific needs and requirements. For instance, with its extensive scope, the automotive industry demands corrosion protection and decorative elements. However, achieving successful industrial application of new research and innovative formulations is incredibly challenging. Consequently, various new terminologies have emerged in the realm of industrial paints. This article aims to provide fundamental recommendations that offer a comprehensive understanding of the diverse paint finishes available.
Expertise shared by Prof. A.S. Khanna, Retd. IIT Bombay, Chairman SSPC India.
Cookie Consent
We use cookies to personalize your experience. By continuing to visit this website you agree to our Terms & Conditions, Privacy Policy and Cookie Policy.