Green alternative to river sand
By Edit Team | August 16, 2019 8:08 am SHARE
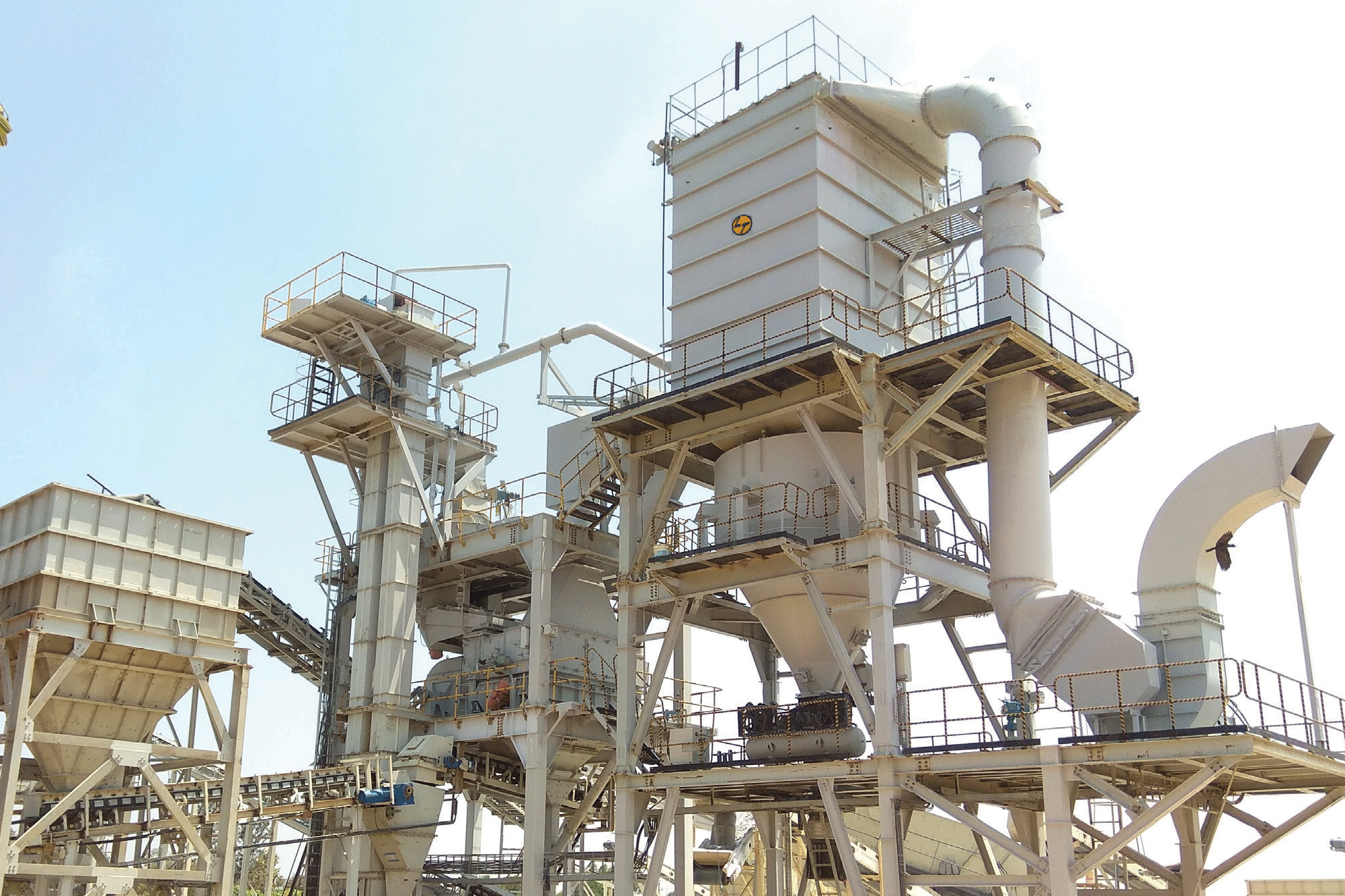
The complexity of modern-day concrete constructions coupled with the shortage of river sand has led to emergence of many manufactured sand alternatives.
A developing economy where construction, mining and manufacturing industries form the foundation of the economy can be immensely benefitted if a true green alternative to river sand is available. The conservation of energy, water and natural resources through usage of effective alternative means is the key for any growing economy, more so when sand is the second most consumed natural resource in the world, after water.
Strong legislation and its implementation against rampant river sand extraction is obvious to save rivers and natural ground water recharge process. The complexity of modern-day concrete constructions coupled with the shortage of river sand has led to emergence of many manufactured sand (or M-Sand) alternatives. The next important step for authorities is to ensure the industry uses proper manufactured sand without any compromises on quality and without destroying any other scarce natural resource.
It has been established that particle shape (rounded/equi-dimensional) uniform gradation of different fraction sand and cleanliness (being free from excess ultra-fines, silt and clay content) – are three key parameters for accepting quality sand for the construction industry for various applications like concreting, plastering, brickwork etc. Any compromise on any of these three parameters can lead to compromising on construction process or quality or both. A lot of research has been undertaken by the industry and reputed institutes to devise solutions which can manufacture such sand that meets all desired parameters (shape, gradation and cleanliness) and be a true alternative to river sand.
In the early nineties, the construction industry started using quarry dust (0-5mm aggregates) as M-Sand. These were often jaw plus cone dust and were hence flaky, elongated with poor gradation and high on silt/ultra-fine content. Introduction of VSI (vertical shaft impactor) in early 2000s improved the shape a little as shaping was of aggregates and not sand, but excess ultra-fines generation became a new headache for such M-Sand. This led to various types of water washing and classification systems to reduce excess fines. The washed M-sand however became too coarse and also led to loss of good fractions. Besides, the washing process created wastage of the most valuable natural resource – water.
The need of the hour was a process to manufacture sand for sand’s sake, and not just as utilisation of wastage. Somewhere in Japan, an advanced and fully automated sand manufacturing process was innovated by the world leaders in sand manufacturing technology – Kemco, Japan. They devised and patented a process which could address all three quality aspects of sand with precision without involving water and yet produce precise sand fit for purpose, i.e. engineered sand.
These e7 sand plants are versatile, efficient and non-polluting. e7 sand plants utilise controlled air for controlled removal of unwanted material, precise crushing and shaping of stones to engineer sand of desired fineness modulus fit for a given design mix. The plant mimics the natural flow of river in a vertically designed installation (one equipment above another), thus also reducing overall footprints.
Concretes or plasters made with e7 engineered sand have been tested across applications and the results are far superior than conventional M-sands (or washed sand) and on certain parameters even better than river sands too. Concrete with e7 engineered sand possesses higher strength (compressive and flexure) when compared to conventional m-sand and is even better than river sand. Concrete or mortars with e7 engineered sand exhibit much better workability and flow-ability, coverage when compared to conventional M-sand. e7 engineered sand concrete and river sand concrete exhibit similar stress-strain behaviour. It has also been established that by using e7 engineered M-sand the cement consumption is at least 10 per cent lesser for the same level of strength in concrete. Particle interlocking in concrete is better with e7 engineered sand for its rough texture compared to smooth surface of river sand particles. The quality consistency gives e7 engineered sand higher mileage over river sand, too.
L&T joined hands with Kemco of Japan to bring this technology to India. Within last few years, there are many such plants, which are mushrooming in all major cities like Mumbai, Delhi, Chennai, Bangalore, Pune, Coimbatore, Nashik, etc. and benefitting both the industry and the environment.
For more details, contact:
BN Arora,
Sr Deputy General Manager – Marketing,
Larsen & Toubro Limited
Email: bn.arora@lntecc.com
Cookie Consent
We use cookies to personalize your experience. By continuing to visit this website you agree to our Terms & Conditions, Privacy Policy and Cookie Policy.