Green mining: Balancing demand and sustainability
By Staff Report | February 11, 2025 7:39 pm SHARE
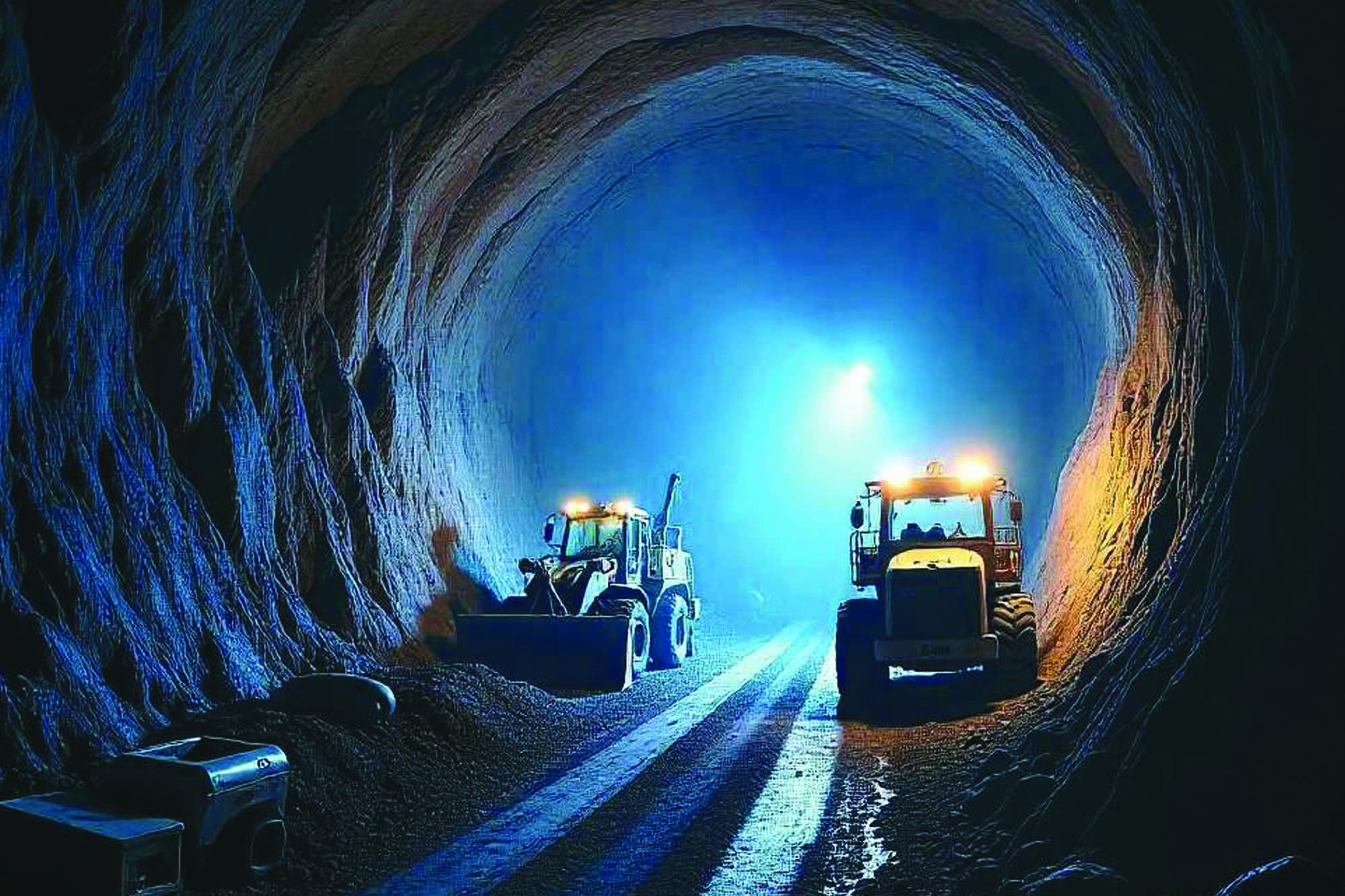
As demand for metals and minerals escalates, new circular economy practices and groundbreaking technology are helping reshape mining operations in India to enhance resource efficiency, reduce waste, and mitigate long-term environmental impacts.
The Indian mining industry nowadays faces a dual challenge. Maintaining its essential role in the domestic economy while transforming to meet sustainability goals. The increasing demand for raw materials, including metals, minerals, and fossil fuels, has led to more aggressive mining methods with significant environmental and economic consequences. However, the rise of circular economy principles and cutting-edge innovations in geological engineering and mining technology are reshaping the landscape. These innovations offer promising solutions to enhance sustainability and efficiency, mitigating the long-term impacts of mining activities.
State of the mining sector today
The global mining sector continues to evolve under rising demand for minerals driven by the renewable energy transition, electric vehicle boom, and infrastructure growth. In 2022, the global mining market was valued at approximately $1.64 trillion and is projected to reach $2.41 trillion by 2030, growing at a CAGR of 5.5%. As the demand for critical minerals like lithium, cobalt, and copper skyrockets, mining operations are under immense pressure to meet production targets and adopt responsible environmental practices.
In India, one of the world’s largest mining markets, the sector contributes about 2.5 percent to the national GDP. The government has been actively encouraging the mining industry’s modernisation, with significant policy shifts to foster sustainable practices. In the 2024 Union Budget, the Indian government allocated substantial funds to develop and modernise the mining sector, enhancing productivity through digital tools, research and development, and infrastructure upgrades. These investments are expected to help the industry transition towards greener and more sustainable mining practices, focusing on recycling, waste reduction, and adopting advanced technologies.
In response to the environmental challenges the mining industry faces, the concept of a circular economy has emerged as a crucial solution. Unlike the traditional linear model of “take-make-dispose,” a circular economy focuses on reusing, recycling, and reducing materials, aiming to extend the life cycle of resources and minimise waste. In the mining context, this translates to recovering valuable metals and minerals from waste, reprocessing tailings, and improving the efficiency of material recovery processes.
Recycling and waste reduction
Anubhav Chandra, National Sales Manager at Ashar Locker India Private Limited, underscores the importance of screening media in supporting the circular economy in mining: “Our screening media are designed for effective material separation and classification, which is essential in recycling operations. Our screens can handle a wide range of materials, including metals, plastics, and building debris, ensuring that valuable resources are recovered and reintroduced into the manufacturing cycle. This decreases the requirement for fresh resources while also minimising trash.”
Chandra’s insights align with the growing trend of incorporating recycling processes in mining operations. Screening technologies are pivotal in extracting valuable materials from slag, tailings, and mining byproducts. Often considered a waste product, tailings contain residual metals and other recoverable resources. According to Chandra, Ashar Locker’s screening systems are used in traditional recycling efforts and in reprocessing tailings to recover additional valuable materials, significantly reducing environmental impact.
Recycling and processing mining waste, including metals, plastics, and other materials, helps mining companies reduce their reliance on virgin raw materials. This is crucial as the world moves towards a more resource-conscious economy. Moreover, recovering metals from tailings can reduce pressure on mining sites and mitigate the environmental footprint of large-scale mining operations.
Slag processing and sustainable practices
Samar Pal, Divisional Head of the Mining Division at Liebherr India Private Limited, highlights how modern mining equipment contributes to waste reduction and material recovery. “We help to reduce waste and improve resource recovery through innovative design and modern technology. Precise digging and loading technologies prevent over-digging and material contamination, ensuring that high-grade ore is efficiently separated from waste. The equipment’s fuel-efficient engines and electric drive choices reduce energy consumption and greenhouse gas emissions, promoting environmentally friendly operations,” says Pal.
The slag processing industry is another area where circular economy principles can be applied. Slag, a byproduct of steel production, is often used in road construction, agriculture, and cement production. Liebherr’s equipment is critical in improving the recovery rate of valuable materials from slag and reducing waste that would otherwise be disposed of in landfills.
In line with this, technologies that enhance resource recovery and reduce energy consumption are essential in driving sustainable mining practices. By implementing these technologies, mining companies can significantly reduce their operations’ environmental footprint while improving efficiency and profitability.
Water conservation and energy use
Water conservation and energy efficiency are vital components of sustainable mining operations. VG Sakthikumar, Chairman and Managing Director of Schwing Stetter India, said, “Our mining machines use precision-controlled excavation and efficient material handling systems to maximise material recovery while minimising resource waste. In addition, we provide energy-efficient engines and hybrid systems that reduce fuel consumption and pollutants. Our sludge pumps for wastewater treatment and C&D waste recycling technologies are critical for sustainable mining practices.”
Sakthikumar’s company’s focus on energy-efficient engines and hybrid systems plays an integral role in reducing fuel consumption and greenhouse gas emissions. Additionally, the company’s sludge pumps help treat wastewater and recycle construction and demolition (C&D) waste, contributing to water conservation efforts. Mining companies increasingly need to integrate water-saving technologies to minimise operational water usage, especially in water-scarce regions. Innovations like water-efficient slurry systems and waste treatment technologies are leading the charge in water conservation.
Geological challenges in mining
While the push towards sustainability is significant, the mining industry faces immense geological challenges impacting safety and productivity. Prof. Arnold Dix, President of the International Tunneling & Underground Space Association, discusses these challenges and the importance of innovative approaches: “One of the most difficult challenges is rock instability. Rock can be weak in some formations, such as those in the Himalayas. Tunnels in seismic zones must be designed using materials and techniques that allow movement absorption rather than inflexible resistance to geological shifts. Water ingress is another key concern since high-pressure water inflows can destabilise tunnel constructions.”
Tunnelling and underground mining are subject to unpredictable geological conditions. As Prof. Dix explains, tunnels in seismic zones, like the Himalayas, require specialised designs to accommodate geological shifts. Similarly, high-pressure water inflows can destabilise tunnel constructions, posing risks to safety and project timelines. In response to these challenges, modern engineering practices rely on advanced geotechnical analysis, controlled drainage systems, and continuous monitoring to mitigate risks and ensure structural integrity.
Advancements in geological engineering
Recent advancements in geological engineering have revolutionised how mining companies approach geological risks. Real-time geotechnical monitoring systems, for example, have become integral to mining operations. These systems track key parameters such as rock stability, air quality, and structural integrity, offering early warnings that allow companies to take preventive action before problems arise.
For example, Vermeer’s surface mining equipment includes onboard diagnostics and real-time performance monitoring features. Tarique Salman, Regional Sales Manager at Vermeer, says, “Onboard Vermeer TEC Plus helps guarantee that our surface miners run at peak efficiency. SmartTEC performance software supports operators in adjusting machine settings to increase machine performance while monitoring and recording that performance for future analysis by the machine owner or fleet manager.”
This technology enables real-time diagnostics, alerting operators to potential issues and minimising downtime. Mining companies can maximise productivity and improve operational safety by enhancing efficiency and reducing the risk of equipment failure, particularly in challenging geological environments.
Meeting safety and regulatory demands
Safety remains a critical concern in the mining industry. As mining operations often occur in hazardous environments, ensuring the safety of workers is paramount. Various companies, including Liebherr and Schwing Stetter, have implemented advanced safety features such as fatigue monitoring systems, proximity detection sensors, and operator assistance technologies.
Liebherr’s equipment integrates fatigue monitoring systems with automated support features, such as autonomous haulage solutions, to reduce human error and improve operational safety. Schwing Stetter’s mining machines are equipped with operator assistance systems, automatic emergency braking, and rollover protection, ensuring worker safety in hazardous conditions.
In India, where mining safety regulations are evolving, the government is strengthening safety norms enforcement. Prof. Dix notes, “Stronger regulatory oversight and enforcement are required to ensure compliance with current safety laws. A risk-based inspection strategy prioritising high-hazard sites could enhance overall safety standards.”
A technologically-driven future for mining
The mining industry stands at a crossroads. As the demand for minerals continues to rise, so does the need for sustainable practices that minimise environmental damage, reduce waste, and promote resource efficiency. The integration of circular economy principles, such as recycling, resource recovery, and waste reduction, is critical for sustainability and presents economic opportunities for mining companies.
Simultaneously, innovations in geological engineering, such as real-time monitoring systems, advanced tunnelling techniques, and precision excavation, are transforming how mining companies approach geological risks. As the industry continues to evolve, the collaboration between technology, safety protocols, and sustainability efforts will define the future of mining operations.
With key players like Ashar Locker, Liebherr, Schwing Stetter, and Vermeer leading the charge in technological innovation and sustainability, the mining sector is poised to overcome its challenges and embrace a more circular and sustainable future. The 2024 Union Budget’s focus on modernising the mining industry aligns with these global efforts, offering hope for a cleaner, more efficient, and more resilient mining industry. The way forward is clear: through innovation, collaboration, and a commitment to sustainability, the mining industry can thrive while minimising its impact on the planet.
Cookie Consent
We use cookies to personalize your experience. By continuing to visit this website you agree to our Terms & Conditions, Privacy Policy and Cookie Policy.