High-tensile fasteners for superior strength and durability
By Staff Report | October 25, 2024 7:21 pm SHARE
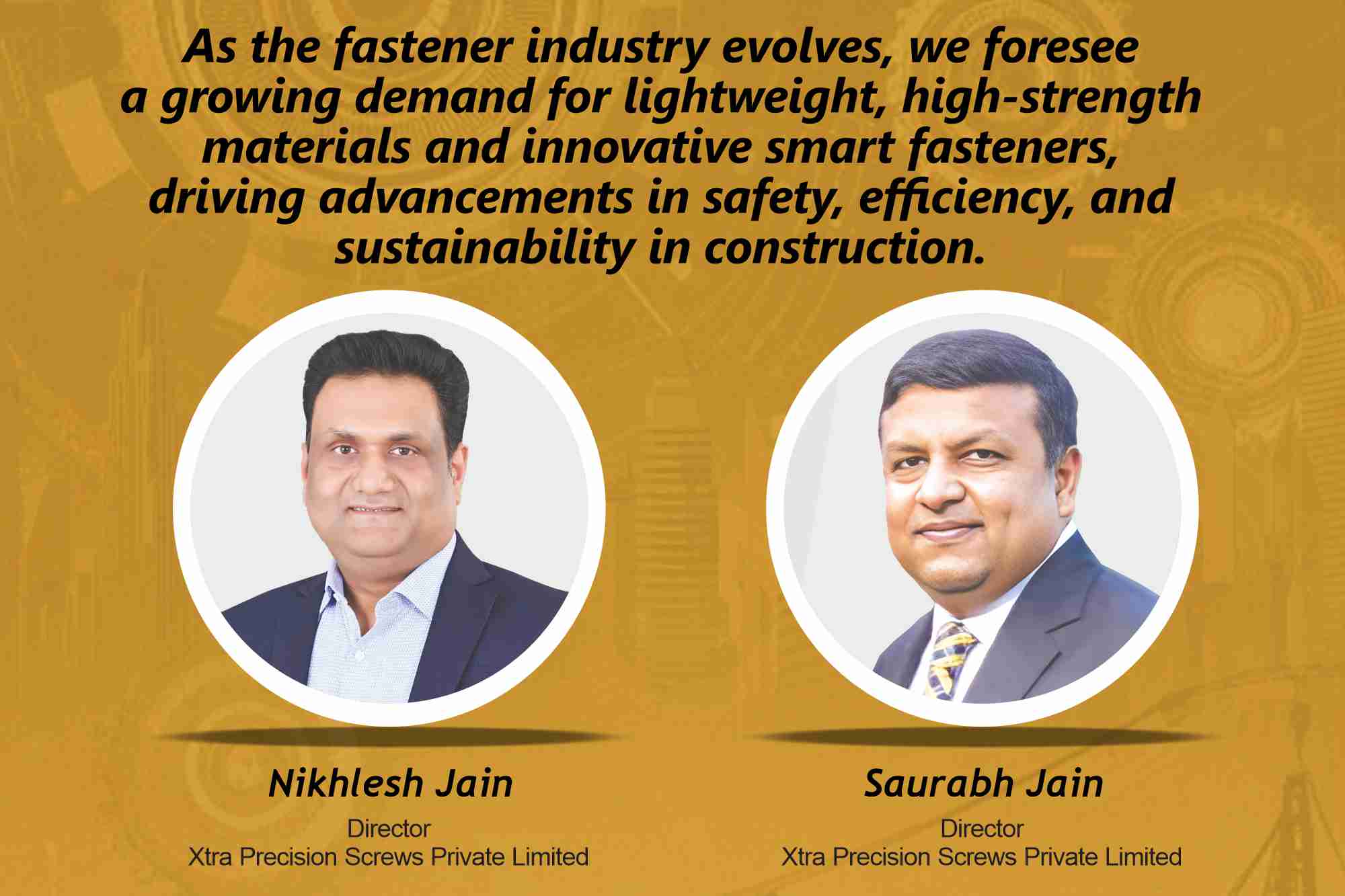
Xtra Precision Screws provides high-tensile, long-lasting fasteners that meet international requirements. They specialise in construction solutions and provide custom goods while researching innovations such as smart fasteners and sustainable methods for future infrastructure projects.
Can you provide detailed specifications for your high-tensile fasteners, including tensile strength ratings and material compositions?
At Xtra Precision Screws, we manufacture high-tensile fasteners that meet rigorous industry standards like ISO, IS, DIN, GB, ANSI and BS. Our fasteners are available in various grades with tensile strength grades 8.8, 10.9 and 12.9, depending on the specific product. We use premium materials, including boron steel and alloy steel, treated with heat and surface treatments for enhanced durability and performance.
What are the key advantages of your most popular products, such as Socket Head Cap Screws and Hex Head Bolts, in construction applications?
Our Socket Head Cap Screws and Hex Head Bolts are designed for demanding various applications, offering several key advantages. Both products provide exceptional tensile strength and fatigue resistance, making them ideal for heavy-load bearing structures. The Socket Head Cap Screws offer a compact design for use in tight spaces without compromising strength, while Hex Head Bolts ensure ease of installation and removal with standard tools. Additionally, they are made from high-grade materials and undergo strict quality control to ensure long-term durability and corrosion resistance, even in harsh environments.
Do you offer custom fasteners tailored to specific project requirements? If so, what factors do you consider during the customisation process?
Yes, we offer custom fasteners tailored to meet specific project requirements. During the customisation process, we consider several factors, including the required tensile strength, material selection, corrosion resistance, environmental conditions, and specific dimensional requirements. We also evaluate the application’s load-bearing needs and any industry-specific standards or certifications. Our engineering team works closely with clients to ensure the fasteners are optimised for performance, durability, and safety in their intended use.
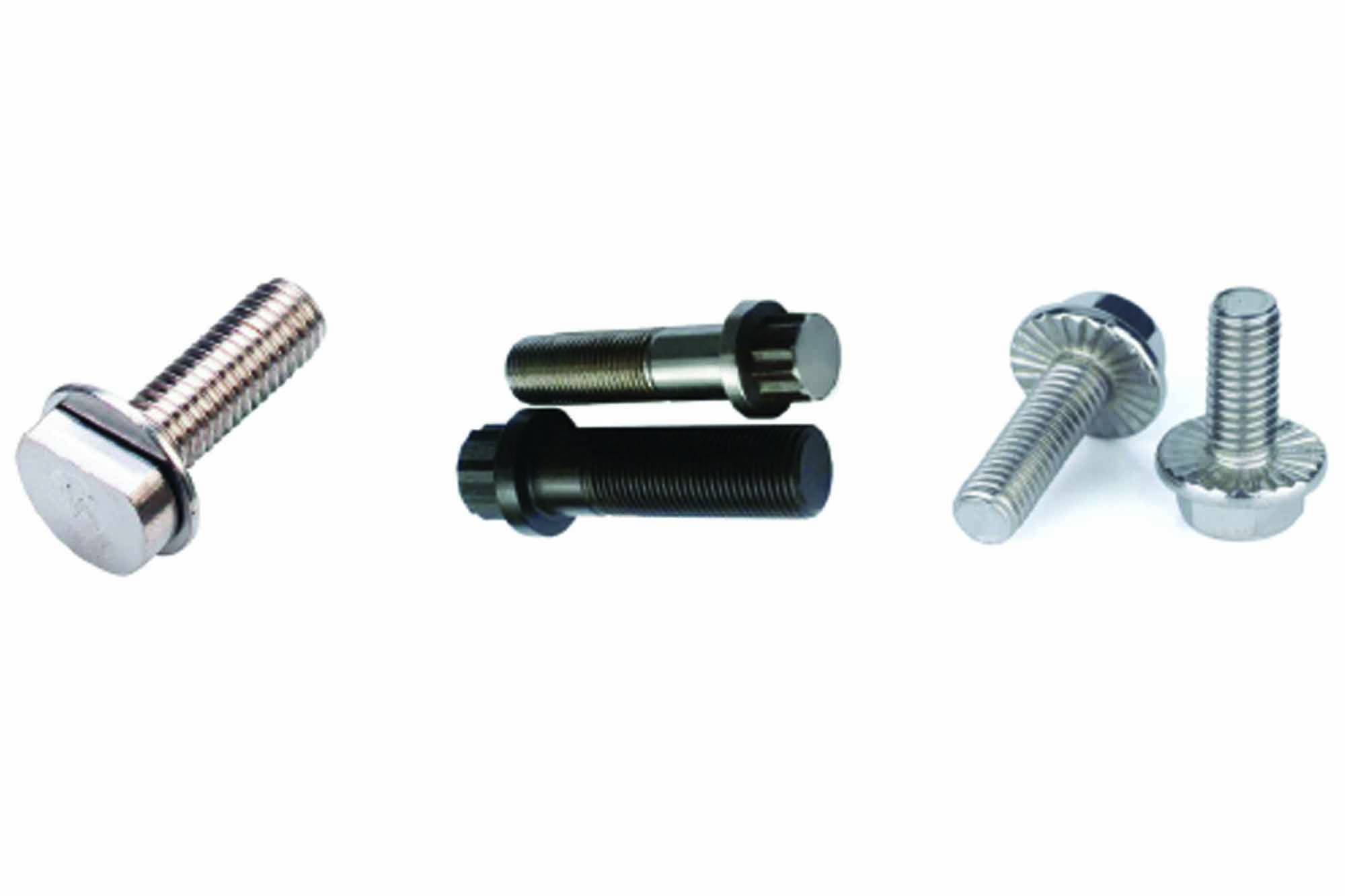
How do your fasteners align with industry standards like GB, ISO, and DIN? Can you discuss the importance of compliance in your product offerings?
Our fasteners are manufactured to meet and exceed industry standards such as GB, ISO, and DIN. These standards ensure consistency, reliability, and safety in construction and industrial applications. Compliance with these standards is crucial as it guarantees that our products meet global quality benchmarks, offering optimal performance, durability, and compatibility across various projects. By adhering to these standards, we help our clients meet regulatory requirements and ensure the longevity and safety of their structures.
What surface treatment options do you provide for your fasteners, and how do these treatments enhance performance in harsh environments?
We offer a range of surface treatments for our fasteners, including zinc plating, hot-dip galvanising, black oxide, zinc aluminium flake, dacro and geomet coatings. These treatments enhance the fasteners’ resistance to corrosion, wear, and environmental factors such as moisture, chemicals, and extreme temperatures. In harsh environments, these protective layers extend the lifespan of the fasteners and ensure their strength and integrity, providing long-lasting performance in demanding conditions.
How do your fasteners perform under different load conditions, and what testing has been done to validate their reliability?
Our fasteners are engineered to perform exceptionally under various load conditions, including static, dynamic, and cyclic loads. To validate their reliability, we conduct rigorous testing such as tensile strength tests, fatigue testing, and hardness evaluations. Additionally, our fasteners are subjected to environmental simulations to ensure they maintain their integrity in extreme conditions. These tests guarantee that our products meet high safety and performance standards, offering consistent reliability in demanding applications.
Can you describe the key stages in your manufacturing process that ensure high quality and durability in your fasteners?
Quality and durability are ensured through several key stages in our manufacturing process. It begins with selecting high-grade raw materials, followed by precision forging on advanced high-speed bolt formers to achieve accurate dimensions. Heat treatment is then done in a state-of-the-art continuous furnace to achieve required tensile strength and hardness. Next, surface treatments are added to improve corrosion resistance and durability. Finally, each batch undergoes rigorous quality control checks, including tensile testing, dimensional inspection, and surface analysis, to ensure the fasteners meet our strict performance standards.
What emerging trends in the fastener industry do you foresee impacting construction and infrastructure in the next few years?
In the coming years, we foresee several emerging trends impacting the fastener industry, particularly in construction, infrastructure, EV segment and robotics. These include the increasing use of lightweight, high-strength materials to improve efficiency in large-scale projects, as well as the growing demand for corrosion-resistant coatings in extreme environments. Additionally, advances in smart fasteners, which incorporate sensors to monitor load and stress in real-time, are expected to enhance safety and maintenance in critical structures. Sustainability is also gaining prominence, with more emphasis on eco-friendly manufacturing processes and materials.
For more information, visit: https://xpsindia.com/
Cookie Consent
We use cookies to personalize your experience. By continuing to visit this website you agree to our Terms & Conditions, Privacy Policy and Cookie Policy.