Hose assembly cleanliness in mobile hydraulics
By Edit Team | September 21, 2016 6:06 am SHARE
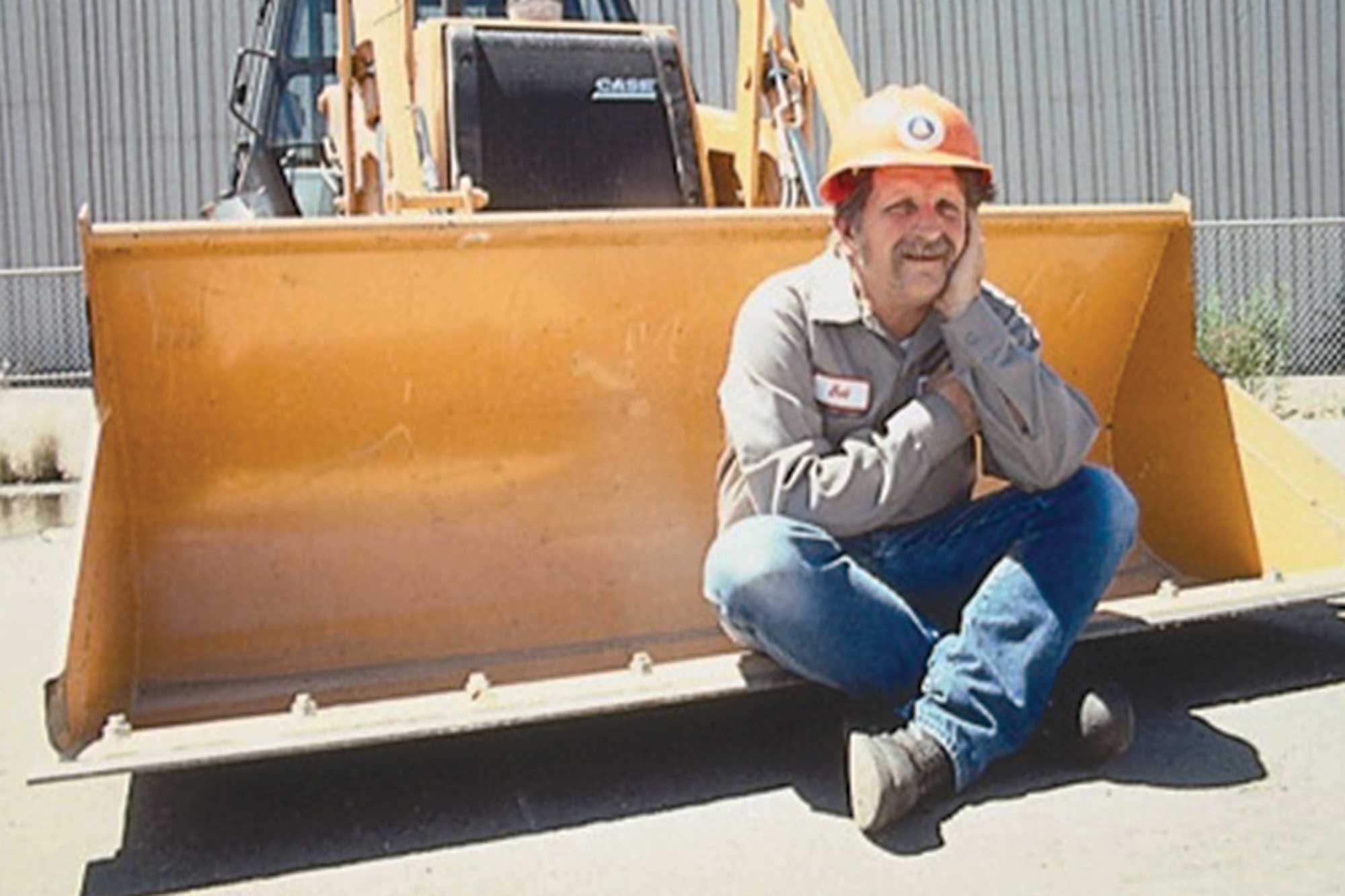
“Over 70% of all hydraulic system failures are the result of contaminated fluid.”
Hose assemblies are the life line of the various mobile equipment like Excavators and Backhoe Loaders and “clean” hose assemblies are critical to the performance of the hydraulic system in these machines.
How do contaminants adversely affect hydraulic systems?
Contaminants can adversely affect a hydraulic system by preventing the proper function of the system components. A gas contaminant such as air can cause pump cavitation. This cavitation can cause a loss of power, overheating, and noise issues. Water contamination can cause oxidation in the hydraulic oil that leads corrosion and sludge build-up. Solid particulate contamination, such as dirt, can cause a wide range of problems in a hydraulic system. This can include component wear, heat buildup and oil flow stoppage. Contaminant particle size can cause system damage relative to the size of the orifice or clearance of system components such as between a piston and cylinder wall, or filter porosity. The usual system clearances available in hydraulic systems show the importance of maintaining hydraulic cleanliness.
Visualise these clearances consider the size of some common objects:
Yeast Cell 1 Micron
Red Blood Cell 6 Microns
White Blood Cell 24 Microns
Human Hair 70 Microns
Grain of Table Salt 100 Microns
How do contaminants get into hydraulic systems?
There are many ways contaminants can get into hydraulic systems-during assembly, operation, maintenance and repairs. During assembly the contaminants can come from a number of sources including hydraulic reservoir, valves, pumps, hoses, tubes and hydraulic oil.
System components need to be cleaned before installation into a hydraulic system. Components can have material left over from the manufacturing process that can contaminate the hydraulic oil. For components such as hoses assemblies, the contamination gains access to the inside of the hose while cutting it to length with a saw or skiving the hose before assembly.
These processes generate clouds of dust particles that can flow into the open ends of the hose. Once cleaned the components need have any opening capped or plugged to prevent contamination during storage.
New oil should be filtered before adding it in to a hydraulic system. New hydraulic oil cleanliness can vary from container to container, so it is best to use a filter during the fill process to prevent contamination.
Minimizing contamination and its harmful effects
To minimize contamination and reduce the harmful effects it can have on a system, there are some steps to follow. Have an understanding of your hydraulic system and cleanliness requirements. By understanding the cleanliness requirements of the system you can set a target level to maximize system life. To select a target cleanliness level, review the system components for the most sensitive to contamination.
Most hydraulic component manufactures have guidelines to flow when it comes to hydraulic oil cleanliness. This may even affect the warranty coverage from the manufacturer.
Once the target is selected, develop a good maintenance program that includes hydraulic oil testing. The testing will provide information that can indicate the health of the system. If testing shows a foreign substance in the oil or a high particle count, then it is time for system repairs.
Confirmation cleanliness levels by testing
Despite efforts to totally remove all of the contaminant in a hydraulic hose system, some contamination remains even after the most robust cleaning or flushing techniques are applied. Contamination can be quantified to better understand the resulting cleanliness level of the hydraulic system. The customer may require a specified cleanliness level.
The International Standards Organisation (ISO) has established three principal methods to measure the contamination level within a component, circuit, or system.
ISO 4405 (Gravimetric Measurement)
ISO 4406 (Particle Size Distribution)
ISO 4407 (Maximum Particle Size Analysis
Usually a combination of the above testing methods is required to maintain the target cleanliness levels
Cookie Consent
We use cookies to personalize your experience. By continuing to visit this website you agree to our Terms & Conditions, Privacy Policy and Cookie Policy.