How to deal with safety aspects of tanks and tank farms
By Edit Team | April 14, 2016 8:57 am SHARE
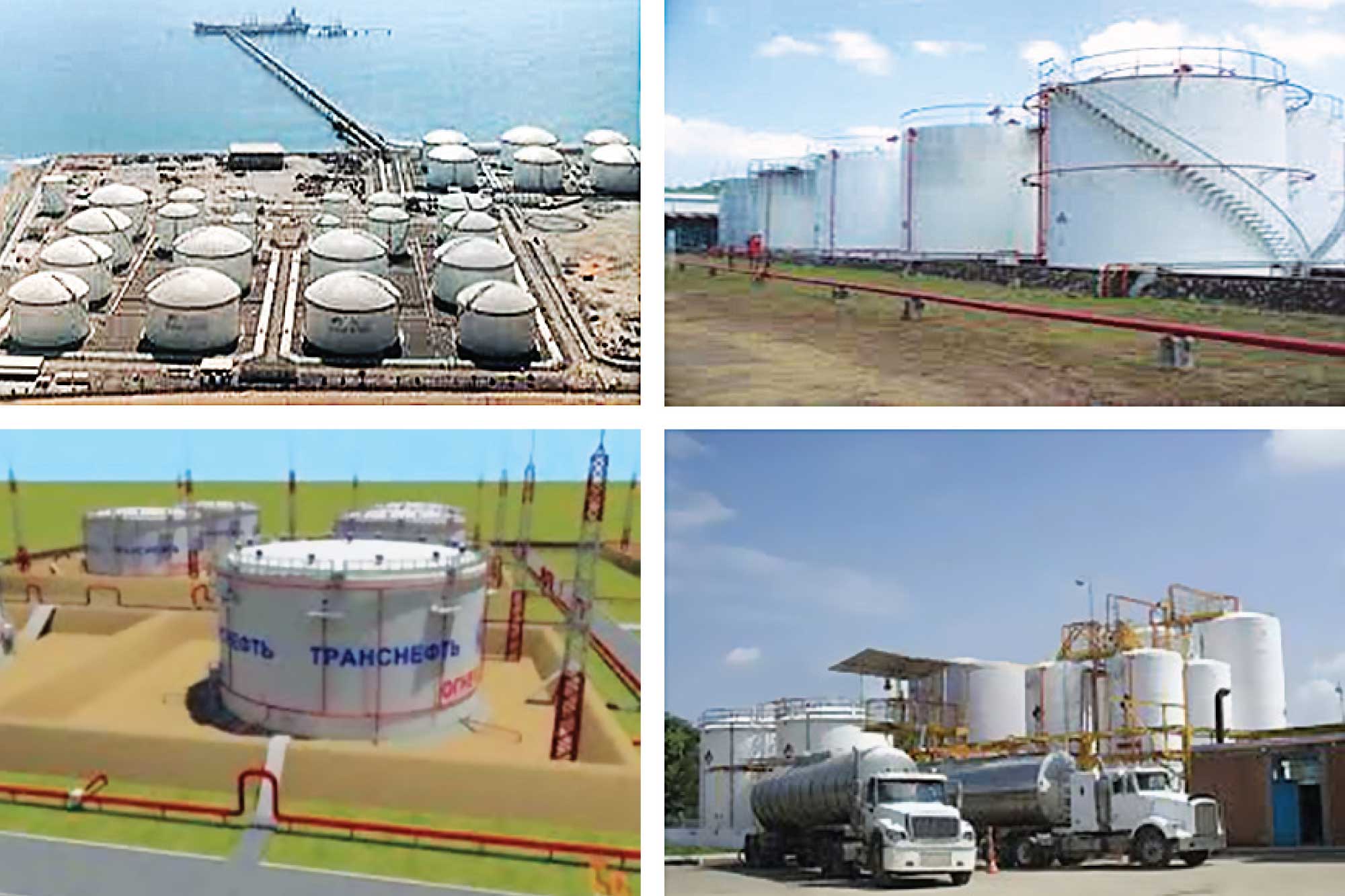
This article deals with different safety aspects of tanks and farms, and talks about general safety aspects of tanks like storage hazard, tank – layout and containment criteria, venting
Storage tanks are one of the most common equipment used for the storage of petroleum products, fuel oil, alcohol, acids and a host of different chemicals. Large quantities of chemicals are often stored in tanks either at process plants or storage terminals. Preventing losses in storage tanks is extremely important. However, this aspect is often neglected. The main reason behind this is the design simplicity which does not result in malfunctioning like reactors, compressors, pumps or other process equipment. In most cases the storage tanks are installed at one corner of the plant. Hence, regular safety inspections are not given due importance.
Loss of containment from storage of toxic chemicals can have serious consequences. The hazard due to release of toxic chemicals was realised at Bhopal, which was the worst disaster in the chemical industry. Although the incidents of toxic gas release with large scale consequences are considered to be rare, stringent preventive measures must be taken to avoid them.
Losses due to fires/explosions in storage tanks constitute a major portion of the losses suffered by the industry. Most of such incidents result in financial loss rather than loss of life and tend to make relatively little impact on the public. However, disasters at Feyzine,
The importance of safety in tank – farm operation takes precedence over all other activities because:
• The quantity involved is several thousand tons of flammable or toxic chemicals.
• A fire in tank farm can lead to large scale property damage and considerable down time.
• Explosion, fire or major spillage in a tank – farm can also damage the surrounding resulting in ecological imbalance and contamination of ground water.
• Possibility of personal injuries and fatalities cannot be ruled out.
Need and purpose of storage
With the liberalisation policy of the government and ‘Make In India’ there has been a phenomenal growth, and will further growth of chemical, petrochemical, fertiliser, petroleum and pharmaceutical industries in India. There has also been an increasing demand from the user industries for providing infrastructure, internal transport and handling facilities on the Indian Ports who are carrying out major expansion of their cargo handling operations.
Chemicals like LNG, Ammonia, LPG and Propylene are imported, transferred to storages at or near the port areas before these are transported to desired destinations. Additionally, user industries also need to store raw materials, intermediates and finished products in bulk quantities at their premises to meet the production needs and provide smooth in and out flow of chemicals.
Storage practices include:
• Liquid at atmospheric pressure and temperature (atmospheric storage)
• Liquefied gas under pressure and at atmospheric temperature (pressure storage)
• Liquefied gas under pressure and at low temperature (refrigerated/semi-refrigerated storage)
• Liquefied gas at atmospheric pressure and at low temperature (fully refrigerated storage)
• Gas under pressure.
Storage hazards
The hazards in the storage depend on the material and type of storage. Rarely, a tank fails catastrophically due to metallurgical or mechanical defects. The tank may get over-pressurised due to overfilling, too rapid filling and under-pressurised by too rapid emptying.
Often the release occurs due to leaks from associated equipment like pumps, pipe work or fittings. Common causes include crack, pinhole full bore rupture, failure at a flange, gasket or valve. Release of contents may also occur in various ways like physical over-pressurisation causing the tank to burst, ignition of a flammable mixture, reaction due to contamination / impurity. Fire in storage tank such as pool fire, jet flames or external can lead to its failure.
Natural events, which can cause loss of containment, include heavy wind, storm, flood, earthquake and tsunami or lightning. Arson or sabotage is other initiating events.
Storage layout
The separation of storage tanks from adjacent facilities is largely based on the classification of the materials, secondary containment, hazardous area classification and fire protection arrangements. The separation distance for the storage tanks has to be as per the Petroleum Act, 1934 and the rules made there under. Also, the drawings of storage facility are to be approved from the office of Petroleum Explosive Safety Organisation – Nagpur, before any construction.
Secondary containment
Storage tanks are normally provided with a bund/dyke and with/without a pit/sump to retain spilled liquid. Bunds may be constructed of such a material that will not be affected by heat or flame. This could be earth, concrete, or brick. In general, bunds are provided for atmospheric storage tanks and for fully refrigerated storage tanks containing liquefied gas or for acid or alkali storage but not for pressure or semi-refrigerated storage of liquefied gas. Such a provision retains the spilled liquid so that it can be dealt with in a controlled manner.
The sizing of the dyke and other stipulations like distance from other installations and constructional features shall be as per OISD-Standard 118 (Revision-I, July 1995) issued by Oil Industry Safety Directorate (OISD) of Ministry of Petroleum and Natural Gas, Government of India, IS: 456-2000 Code of Practice for Plain and Reinforced Concrete for RCC dyke-wall, IS: 1905-1987 code of Practice for Structural use of Un-reinforced Masonry for masonry dyke wall.
Venting and relief
Since atmospheric tanks can withstand pressure / vacuum only to a little extent, it is essential that atmospheric vents are maintained free of obstructions. Blockage can occur due to debris, icing up, solid formation, polymerisation etc. A pressure / vacuum (PV) valve, also called as a breather valve or conservation vent, has two vent valves – a pressure valves which open to let vapour out and a vacuum valve which opens to let air in. A fixed roof tank tends to breathe frequently leading to appreciable loss of vapour through the vent. A Breather valve is effective in reducing this loss.
Flame arrestor is however not considered essential in conjunction with a PV valve because flame speed is less than vent velocity. Open vents with a flame arresting device may be used in place of PV valves on tanks in which oil, having flash point below 100 F (37.78 C), is stored and on tanks containing petroleum products where the storage temperature is more than the flash-point.
Flame arrestors fitted on tank vents may get blocked. Therefore the use of flame arrestors is sometimes discouraged if the maintenance of a high standard is not practicable to ensure the required venting capacity.
Authored by
Anil Choumal, Managing Director
QuEST Management Solutions, Bharuch
Email: anilchoumal@yahoo.co.in, quest.bharuch@gmail.com
Cookie Consent
We use cookies to personalize your experience. By continuing to visit this website you agree to our Terms & Conditions, Privacy Policy and Cookie Policy.