How to enhance mining equipment reliability
By Edit Team | February 27, 2017 9:50 am SHARE
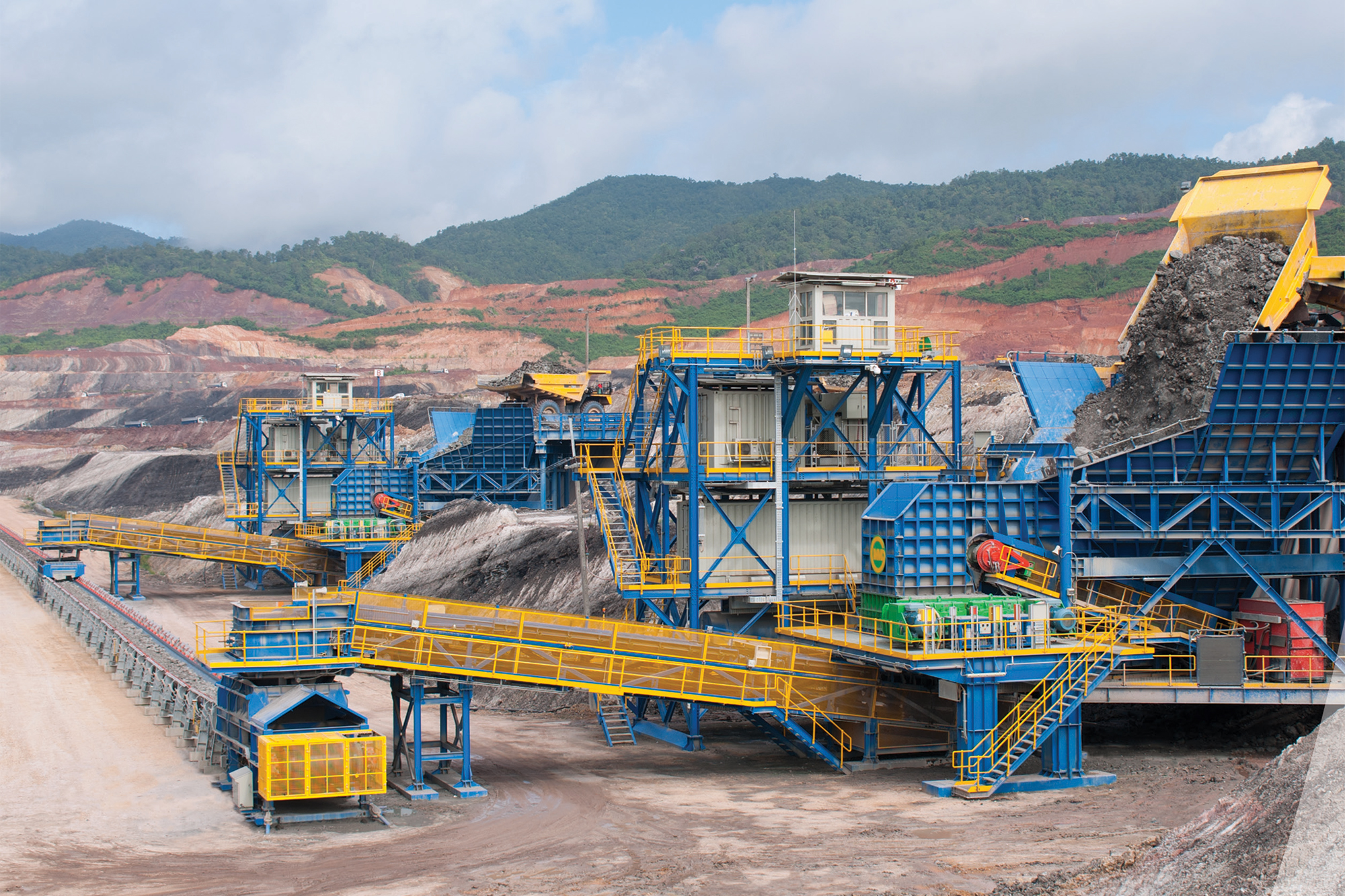
For any production plant or process equipment, reliability is a critical aspect. Mining industry is not an exception. Experts take us through how we can enhance the reliability of mining equipment.
Global mining is changing rapidly: rising costs, environmental pressures and health and safety have called time on traditional truck and shovel methods. As the industry becomes increasingly aware of the need for ‘Sustainable Mining’, the ecological benefits derived from the elimination of dust and reduction of harmful greenhouse emissions caused by truck and shovel methods are self-evident.
For the ultimate in cost savings, environmental mining and portability, fully mobile Sizer units ( fully mobile IPSC) enable the use of efficient conveyor haulage directly from the mine face. “Sizers move frequently to work directly with the excavator, whilst sizing and delivering conveyable material onto the conveyor haulage system, eliminating trucks and their associated costs, safety risks and environmental impact. MMD has, throughout its existence, developed purpose designed mobile units to suit any mining method and material. The whole range of Sizers can be incorporated into a wide range of transport options available to suit the duties and throughput required,” says Subhajit Chaudhuri, Vice President – Sales & Projects, MMD Heavy Machinery India Pvt Ltd.
He further adds, “The Sizer unit reduces material in preparation for efficient conveyor haulage out of the mine. As the mining face progresses these units are relocated occasionally to minimise the truck haulage distance.” Semi mobile sizer units leverage the flexibility of truck haulage together with the efficiency of conveyor haulage. This provides the ideal efficient solution for many mining scenarios where mining flexibility is vital, such as selective mining (blending), heavily faulted seams or irregular shaped ore bodies. “Semi-Mobile units are constructed in easy-to-assemble modules that can be relocated closer to the mine face by the MMD Atlas Transporter. Through the use of the well established components such as the twin shaft Sizer and heavy duty apron plate feeder, MMD Semi Mobile units deliver the reliability and robustness required for IPSC operations,” informs Chaudhuri.
MMD Sizing Technology
Speaking about the Sizing technology by MMD, Chaudhuri says, “The basic concept of the MMD Sizer, is the use of two rotors with large teeth, on small diameter shafts, driven at a low speed by a direct high torque drive system. This design produces three major principles which all interact when breaking materials using Sizer Technology.”
The unique principles are; The Three Stage Breaking Action, The Rotating Screen Effect, and The Deep Scroll Tooth Pattern. The interlaced toothed rotor design allows free flowing undersize material to pass through the continuously changing gaps generated by the relatively slow moving shafts. The deep scroll conveys the larger material to one end of the machine and helps to spread the feed across the full length of the rotors. This feature can be used to reject oversize material from the machine. With large teeth and small shaft diameters the material is gripped and broken in shear rather than compression force resulting in much lower energy consumption. Absorbed power is 55 per cent on installed power. Deep scroll tooth pattern which acts as a rotating screen allowing already undersize material to pass without any further size degradation or power usage. MMD Sizer technology produces the minimum fines.
Sharing about the successful operation, Chaudhuri says, “MMD has more than 4500 successful installations worldwide with over 80 different minerals worldwide. We have more than 350 pleased customers with repetitive orders.”
He concludes saying, “Breaker bar option defines the final product size resulting in three dimensional sizing of material. This also eliminates the possibility of any slabby material in the final product.”
Selective mining – an upcoming alternative
Ramesh Palagiri, Managing Director and CEO, Wirtgen India says, “Surface miners extract primary resources in a selective operation, achieving high degrees of purity and maximizing exploitation of the deposits. Selective mining considerably reduces equipment, labour and time requirements as well as overburden volumes. With our machine technology, we also constantly endeavour to keep environmental pollution as low as possible.”
A tremendous advantage of selective mining is that the vibration less mining operation without drilling and blasting is accompanied by low levels of dust and noise. The low environmental impact also permits maximum exploitation of the deposit right up to the edge of residential areas. The selective mining of high-quality materials requires considerably less space than conventional mining methods.
Speaking about the surface miner introduced by Writgen, Palagiri says, “A WIRTGEN surface miner is a perfect example of this philosophy: it impresses with its environmentally friendly technology as it cuts, crushes and loads rock in a single operation. Our fuel-efficient, intelligently controlled engines comply with the strictest exhaust emission standards, thus making our Surface Miners very reliable.”
High pressure hoses and couplings
Gates India is a leading name in fluid power product and services for mining equipment. The company offers a wide range of high pressure hoses and couplings for the mining and construction industry for their variety of applications. These hoses are certified by US MSHA for fire resistance and conform to international standards SAE, EN and BCS.In the recent times, it is observed that hydraulics is becoming more compact with increasing requirements in high temperature and pressure. Many applications call for compact and flexible hoses with pressure impulse life beyond standards. Gates team too is very positive about the innovations that have taken place in this area. On contacted Gates shared that there is an increased awareness and demand from the users for right product, service, and ability to track and monitor these assets for better performance in the field leading to reduced downtime and environmentally leak free performance. Gates as one of the global leaders is providing jaw dropping performance with excellent solutions. Its range of Mega Sys hoses, Ilok Mining couplings, and Sentry Hose management system are towards meeting these requirements.
Why Gates India?
Gates claims that as a company it designs the products, validates them and manufactures to meet the customer expectations of quality and reliability in very arduous conditions. Gates has a long track record of innovating products and services meeting specific application requirements by actively collaborating with the customers. A country wide team of application engineers support the customers in optimal product selection, VE/ VA studies, routing and installation study helping them to improve the uptime of the equipment and reduce the total cost of ownership. All this, collectively shapes in making Gates India a stand out from the other competitors when it comes to hose manufacture.
Conclusion
Thus, techniques like sizing, selective mining and reducing the down time will help in enhancing the reliability of the mining equipment. Implementation of these techniques will definitely boost the production.
Cookie Consent
We use cookies to personalize your experience. By continuing to visit this website you agree to our Terms & Conditions, Privacy Policy and Cookie Policy.