How to select a cone crusher
By Edit Team | August 25, 2021 4:10 pm SHARE
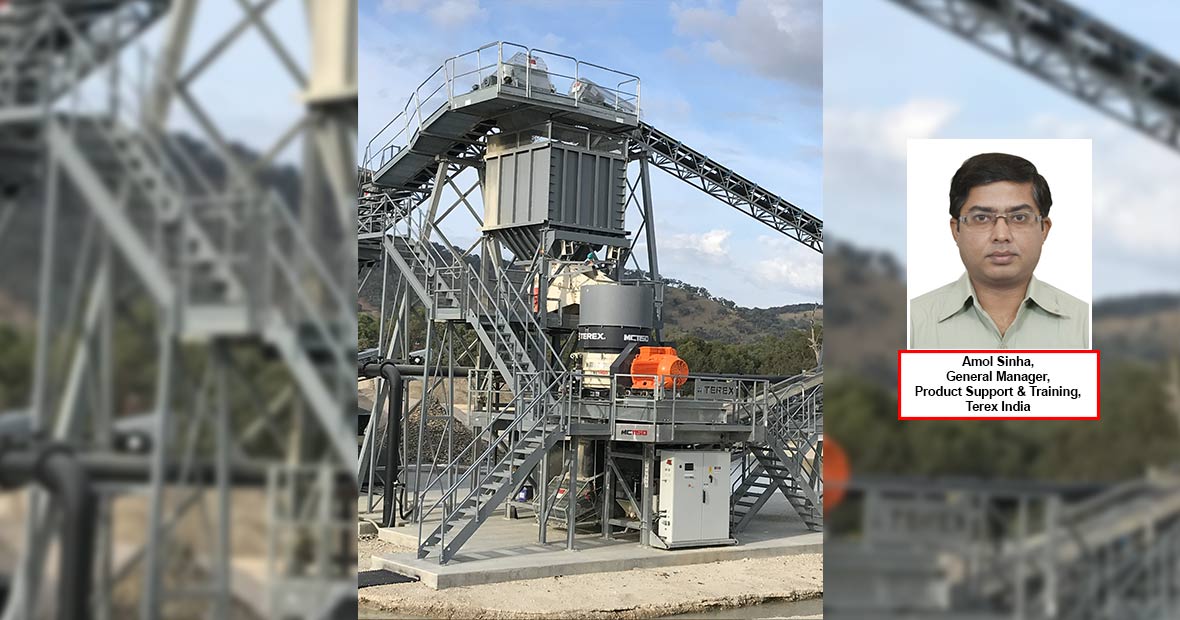
Quarries have numerous factors to consider when selecting cone crushers to create quality aggregate products.Successful application of a cone crusher within a crushing circuit is measured by the amount of material passing through the cone, the power draw of the machine, the size distribution of the products coming out of the circuit and the shape of the product. The goal is to efficiently and economically produce the target products, conforming with the required specifications.
The mechanical factors that affect the production rate and quality of the material processed by a cone crusher include:Cone head diameter, crushing chamber slope (angle), cone head stroke, gyrating speed, manganese liner profile, closed side setting (CSS), crushing force – monitored as operating pressure, applied power, and feed control.
In any crushing operation, physical characteristics of the material being processed affect the output product. The material characteristics that affect the crushing process include: abrasiveness, compressive strength, bulk density, friability, plasticity, feed gradation, and moisture content.
A measure of the size reduction achieved for a particular crusher application is the reduction ratio. A cone crusher in a secondary crushing application will typically work with a 3.5:1 to 5:1 reduction ratio. Tertiary cone crusher configurations typically work with a reduction ratio of 2.5:1 to 4:1.
Long stroke advantages
The newer, longer stroke, high powered machines of today will outperform the machines in common use 25 years ago. A large stroke provides a greater cross-sectional area for material to pass through the crushing chamber in a given amount of time. The result is that the longer the stroke, the greater the volume of material that can be processed through a given size machine.
Crusher speed
The influence of crusher speed, or gyrations of the cone head per minute, is not as well defined as stroke. Depending on the crushing stroke, the CSS and the crushing chamber profile, the effect of increased speed can either increase or decrease the production rate of the crusher. For any combination of these, a different ‘sweet spot’ in speed will produce maximum throughput for a given feed.
In general, a coarse crusher, such as a secondary cone in open circuit, should be run at the low end of the speed range. As the crushing becomes finer, an increase in speed has been found to be beneficial, especially when shape is a factor. Therefore, it is recommended that tertiary crushers that are operated in closed circuit and at the higher end of the speed range. It needs to be understood that the faster the crusher runs, the faster the manganese wears. The life of other mechanical components will also be reduced. Therefore, the optimum speed for any application is the slowest speed that produces the desired production rate, gradation and shape.
Limitations on CSS
Minimum closed side setting for any cone crusher is that setting just before the factory recommended limit of operating pressure is reached. This is the point at which the hydraulic relief system will act to open the CSS. Minimum CSS may be greater or smaller than published settings based on the conditions and crushing characteristics of the material being processed. Generally, clay or other plastic material in the crusher feed must be eliminated to prevent the formation of compacted material or ‘pancakes’, which are non-crushable and will cause activation of the tramp iron relief system.
Producing quality product
The breakage of rock in a compression crusher can result in a percentage of flat or elongated product. However, most construction specification rock products require a cubical product. The cubicity of the cone crusher product can be improved with the proper circuit design, screen selection and crusher operating parameters.
Guide for crushing circuit design
In any crushing circuit, it is good common sense to get the material to the product piles as quick as possible. This will reduce the wear and tear on the equipment and can lead to increased efficiency and capacity of the circuit because the finished product is not taking up room on the screens, conveyors, and in the crushers.
The size of the raw feed or blasted material and the specification of the final products will dictate the number of crushing stages and screens required. If there is also a shape specification, additional controls and crushing stages may be required. A low reduction ratio application may be able to get by with a jaw/cone/screen circuit (two-stage crushing). A higher reduction ratio application may require a jaw-screen/cone-screen/cone-circuit (three-stage crushing). A large reduction ratio application may require four or more stages of crushing.
The crusher breaks down the rock to a smaller size. The screen is the ‘cash register’ of the crushing circuit in that it determines the final gradation of each product pile. In general, it is good practice to oversize the screen to account for changes in environmental conditions that can affectthe overall performance of the crushing circuit.
Cone crusher types
Cone crushers can be categorised into three main design types. With floating bowl and screw bowl cone crushers the upper frame raises to open CSS or relieve crushing pressure. The third type – the spider-bearing cone crushers – incorporate a shaft supported by a hydraulic piston which controls CSS and crushing pressure. Each machine type has its own features and advantages and each is best suited to particular applications. Terex, through the TC cone, Cedarapids MVP, TG cone and JaquesGyracone, includes each of these main cone crusher types within its equipment range to ensure it can provide the best option across all crushing applications.
Expertise shared by:
Amol Sinha, General Manager, Product Support & Training, Terex India
Cookie Consent
We use cookies to personalize your experience. By continuing to visit this website you agree to our Terms & Conditions, Privacy Policy and Cookie Policy.