How to select equipment for underground mining
By Edit Team | November 25, 2017 5:39 am SHARE
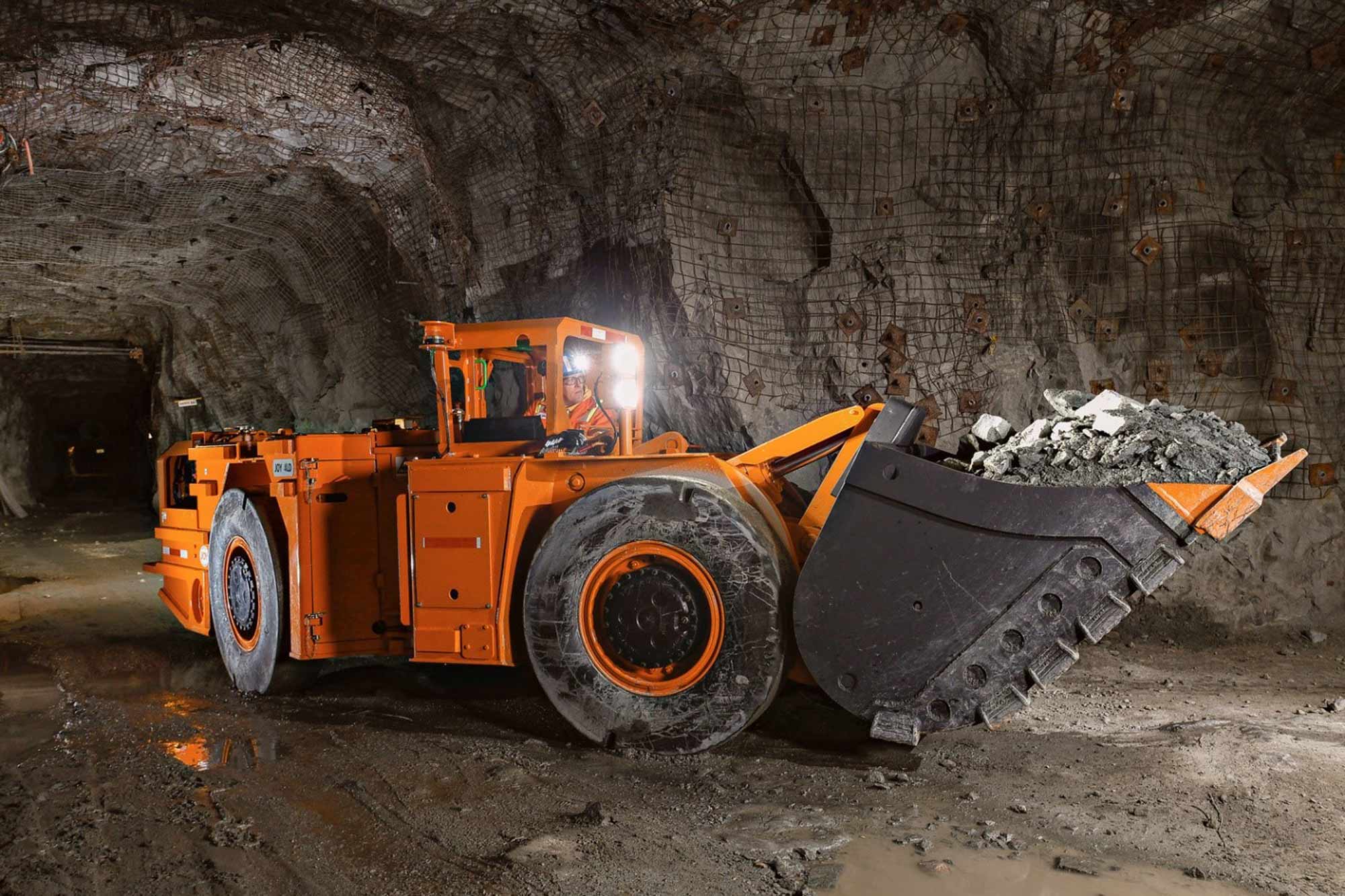
An in-depth report on how to select equipment for underground mining along with necessary solutions provided.
To meet the demand of coal in domestic market, Government of India (GoI) has set an ambitious target for the coal companies to produce one billion tonne of coal by 2020 from the present level of 655 million. Coal India Limited (CIL), a state-owned enterprise and the largest coal company in India, produced 554 million tonne coal in 2015-16, out of which 35 million tonne came from underground mines.
Selection of the equipment package for underground coal mines
While surface mining will continue to play dominant role to meet the production target, there is a persistent effort to enhance the underground production from its present level by introducing innovative technologies. “Continuous Miner (CM) technology is the only economically viable option to increase India’s underground coal production and meet the demand of coal in a safe and productive mining environment,” says Prasenjit Maity, Senior Sales Manager, Komatsu Mining Corp. Group, Joy Global (India) Ltd.
Underground coal mining varies greatly based on geo-mining conditions and the application for each coal seam. “From planning to operation of the equipment, a deep understanding of each mine’s specific needs and customisation of both equipment and systems are required,” Maity adds.
Selection of right equipment package for underground coal mining depends on the following factors:
Geo-mining conditions of the coal block
• Status of the various seams – developed or virgin
• Seam thickness – low, medium or high seam
• Compressive strength of coal – to select proper cutting drum with required power
• Depth of the seam
• Gradient – steep gradient will limit the movement of tyre mounted equipment
• Degree of gassiness
• Immediate roof – UCS test result required to determine bolting requirement
• Floor conditions – slake durability test result required to select the right equipment to withstand the ground pressure of the equipment
• Incubation period
• Mineable reserve – reserved should cover the life of the equipment
• Whether ‘caving’ is possible – caving preferred as stowing will be bottleneck for high production
• Existing gallery and pillar size – minimum 5m roadway width is required for smooth manoeuvrability of the equipment
• Geological disturbances, e.g. faults, dyke etc.
Infrastructure of the mine
• Coal evacuation capacity of conveyor belt – should be able to handle peak production
• Incline size – minimum 3m x 4m clear rectangular cross-section is required
• Man riding system – should have appropriate Man riding system to enhance the efficiency of the workmen.
• Surface and underground bunker capacity – total storage capacity should be one day’s production
• Electric power
• Water supply – filtration plant
• Skilled manpower
• Workshop facility
• Store facility
DGMS approval
Based on detailed information of the mine and the requirements of the customer, a suitable equipment package is selected to achieve the target annual production. However, the production potential may vary depending on the Go-No-Go matrix of the above mentioned parameters.
Main challenge lies with bringing ‘ore’ to the surface
It is very important and crucial in selection of material handling equipment especially in underground mining applications. “In underground mining the main challenge lies with the bringing of ore to the surface. It is typically based on the mine production targets and mining methods,” says V. Manoj Kumar, Assistant Vice President – PMG, Bevcon Wayors Pvt Ltd.
“The initial capital cost calculations, annual operating costs and equipment replacement considerations play a significant role in establishing an accurate forecast of the net-present-value of the mining operation,” he adds.
The mining industry is extremely capital-intensive, especially when implementing bigger equipment with larger capacities to increase production rate. However, low commodity prices have forced companies to discover innovative methods and equipment in order to decrease their overall capital costs by improving equipment productivity. One way to accomplish this is to utilise equipment more effectively and efficiently.
A holistic approach for selecting the vertical haulage system
The innovative and new age method of bringing ore to the surface is by continuous vertical haulage. Bevcon in technical collaboration with M/s. Dos Santos Intl. USA, who are world’s foremost authority on high angle conveyor applications and design of sandwich belt type high angle conveyors technology introduce to Indian mining industry.
Kumar informs, “These vertical haulage systems (as HAC) are capable of elevating ore from greater depths ranging from 400 metres to the surface at 3,000 tonnes per hour.”
With an ambitious targets set by ministry of mining in India year on year, these new and innovative equipment adds greater value to the production.
Sizer technology: Compact and efficient way of comminution
The MMD group of companies is a global specialist in the processing and reducing of natural and manufactured minerals using Sizer technology. Subhajit Chaudhuri, Vice President-Sales & Projects, MMD Heavy Machinery (India) Pvt Ltd, says, “The equipment selection process for an underground mine has an extremely wide scope as there are a myriad of parameters to consider when incorporating mobile and stationary equipment in combination with loaders, crushing equipment and trucks in hard or soft rock mining applications.”
He adds, “In equipment selection factors, there are a range of factors that must be taken into consideration pertaining to each piece of mobile equipment that are:
• Purpose and objective of each equipment
• Different types of each equipment
• Crushing equipment size (the size should be compact) and capacity
• Operating cycle time
• Turning radius or working radius
• Health and safety considerations
Sizer technology is the latest innovation in the crushing industry providing a compact and efficient way of comminution, both in underground and open pit operations. Currently MMD process over 80 different materials in more than 70 countries worldwide for primary, secondary or tertiary crushing operations.
Solutions for underground mining
Rijubrata Das, Sales Manager, Komatsu Mining Corp. Group, Joy Global (India) Ltd outlines the latest offering for underground coal mines.
• Continuous miner 12CM27: efficient equipment for extraction of 5m thick coal seams in a single slice.
• Entry driver 12ED30 – high speed mechanised drivage of longwall gate road development, capable of simultaneous coal cutting and roof bolting.
• Roadheader EBZ260 – for incline drivage of coal mine.
• Low height roof bolter, RR-II – suitable for 1.3m to 2.5m extraction height.
• Battery hauler BH20 – cable free battery-operated coal hauler of 20 tonne capacity.
Underground hardrock mining
Thanks to the April acquisition of Joy Global Inc., Komatsu now has the full portfolio of Joy, P&H, and Montabert hard rock mining products as part of its offerings. The extensive Joy product suite of hard rock equipment includes hydraulic jumbo drills, in-the-hole production drills, loaders and trucks.
The brand’s heavy-duty drilling jumbos for mining and tunneling use Montabert HC series drifters and Intelsense drilling controls. The Joy NV-1, Vein Runner II, Drift Runner, and Ramp Runner series of drills suit narrow vein, standard size to large mine or tunnel cross-sections. The articulated chassis and telescopic feed help to manoeuvre and position the machine in narrow drifts.
The largest size, which can fit within a given cross-section, defines the ideal size of underground LHD (loaders) and LPDT (trucks). The extensive line of Joy loaders, with a wide variety of rated load capacities, is ideal for narrow vein and standard drive applications. Joy underground trucks are designed for ground-level maintenance with no climbing.
In the past year, several enhanced Joy underground hard rock products were launched, including the 16TD truck, 4LD loader and the new line of hybrid underground loaders featuring proprietary Switched Reluctance (SR) Hybrid Drive technology to significantly reduce fuel consumption and enable faster acceleration.
Das informs, “The 16TD truck is based on the popular DT-1804 model, which has been a stalwart unit in the product line for many years. The 16TD takes that reliable model and builds on it to include: lower hood lines for improved visibility, a digital operator display, shorter turning radius, ground level maintenance and faster speed ramps.” Similarly, the 4LD loader is a comprehensive re-design of the LT-350 loader. He added, “The new machine features increased carrying capacity and z-bar link improvement; better operator comfort or safety due to the ROPS or FOPS enclosed cab with climate control and upgraded controls; and increased ease of maintenance.”
Komatsu will continue to invest in and promote the Joy, Montabert and P&H brands. Through integration, the company plans to continue expanding its capabilities in underground hard rock mining and other areas.
Innovative conveying systems and equipment
Bevcon Wayors provides concept to commissioning solutions and execute turnkey or EPC projects for all material handling applications for all sectors and establish itself as a reliable brand in bulk material handling industry.
Value innovation is life line for Bevcon. They always strive to bring best technologies to India with most cost optimised manner. Bevcon executes project with blend of latest technology with conventional systems in most optimised manner which will enhance the operations reliability. Kumar from Bevcon Wayors, claims, “Bevcon core strength lies in use of Innovative Conveying Systems and Equipment which caters present day demands of Indian mining sector.”
Kumar further opines, the company’s highly competent technical team supported by technology partners from the US and Europe are in position of supplying the innovative equipment like:
Sandwich belt high angle conveyor
For vertical conveying application which is revolutionary concept; Bevcon’s technology tie-up with M/s. Dos Santos intl. USA, who are world’s foremost authority on high angle conveyor applications and design of sandwich belt type high angle conveyors for Open Pit Mine (In-pit Crushing Conveying), which is breakthrough concept of conveying any mineral from pit bottom to the surface by totally eliminating use of conventional trucks. It also minimises the environmental degradation; flexibility of conveying profiles makes it one of the unique materials handling equipment of current generation and brings down the operational cost drastically and enhances productivity by retaining product quality. Its unique concept ever tried in Indian mining industry. These high angle conveyors are not new at all, but have not found wide use in IPCC systems where they can realise the greatest advantage.
Overland pipe conveyor
Overland Pipe Conveyor is a modern and environmentally friendly transporting system for all kind of bulk materials by overcomes numerous challenges associated with conventional conveyor systems. Pipe Conveyors have best capabilities of transferring materials between two points, managing both horizontal and vertical curves as well as high inclinations which are difficult in case of trough conveyors. It eliminates multiple transfer points and exposure of material to atmosphere. Pipe Conveyor not only protects the conveyed material against external influences such as climatic conditions, it also avoids material loss and spillage and thus, protects the environment.
Overland troughed conveyor
Overland troughed belt conveyors are designed to carry high tonnage loads over long distances. Bevcon’s long distance conveyor design ensures lowest power consumption per ton of conveying. Overland belt Conveyors have been proven to be an efficient method of transporting bulk material over long distances and costs are often lower than with truck transportation.
Stockyard system
Bevcon brings the vast experience of their technology partner M/s. FMK, Poland, in design and development of wide range of stockyard equipment like stacker, reclaimer, stacker cum reclaimers, full & semi-portal scrapper reclaimer, Side Scraper and belt conveyor system for maximizing the space utilisation to meet the expectations of project.
Bulk receipt feeders
To facilitate easy handling of bulk material unloading from trucks without civil works of ground hoppers.
Reclaim feeders
For faster reclamation of minerals at mines and ports.
Idlers and pulleys
Be’RolleX manufactures Idlers and Pulleys to meet high capacity and high speed applications.
As the industry becomes increasingly aware of the need for ‘Sustainable Mining’, the ecological benefits derived from the elimination of dust and reduction of harmful greenhouse emissions caused by truck and shovel methods are self-evident. MMD’s innovative technology is at the forefront of this revolution,” informs Chaudhuri from MMD Heavy Machinery.
MMD IPSC systems
MMD IPSC systems are a cost-effective and safer alternative to discontinuous material haulage by dump trucks; reducing operating costs, improving safety, and reducing CO2 emissions, dust, and noise pollution. Employing either fully mobile, semi mobile or static Sizer units in conjunction with conveyors, IPSC efficiently processes and transports material out of the mine.
For the ultimate in cost savings, environmental mining and portability, fully mobile Sizer units (fully mobile IPSC) enable the use of efficient conveyor haulage directly from the mine face. They move frequently to work directly with the excavator, whilst sizing and delivering conveyable material onto the conveyor haulage system, eliminating trucks and their associated costs, safety risks and environmental impact. “MMD has, throughout its existence, developed purpose designed mobile units to suit any mining method and material. The whole range of Sizers can be incorporated into a wide range of transport options available to suit the duties and throughput required,” says Chaudhuri.
MMD Atlas transporter
The MMD Atlas transporter is the latest technology from MMD, enabling heavy semi-mobile structures to be relocated in a safe and controlled manner. A single transporter can serve many units and structures around the mine. A range of MMD transporters are available from 200T to 750T carrying capacities.
The design of the transporter has been optimised to fit within compact dimensions and low height. This provides the ideal foundation for lifting large heavy structures.
“Utilising over 80 sensors the MMD transporter has the unique capability to monitor and maintain the payloads centre of gravity automatically while travelling over different terrain and gradients. Inline and cross gradients of up to 10 per cent can be accommodated for, providing uncompromised portability. “For safe operation the transporter is controlled by a fully featured wireless unit which provides live feedback and maximum control while travelling, lifting or slewing,” adds Chaudhuri.
Cookie Consent
We use cookies to personalize your experience. By continuing to visit this website you agree to our Terms & Conditions, Privacy Policy and Cookie Policy.