Improving shielding gas flow control in wire welding applications
By Staff Report | December 24, 2024 6:25 pm SHARE
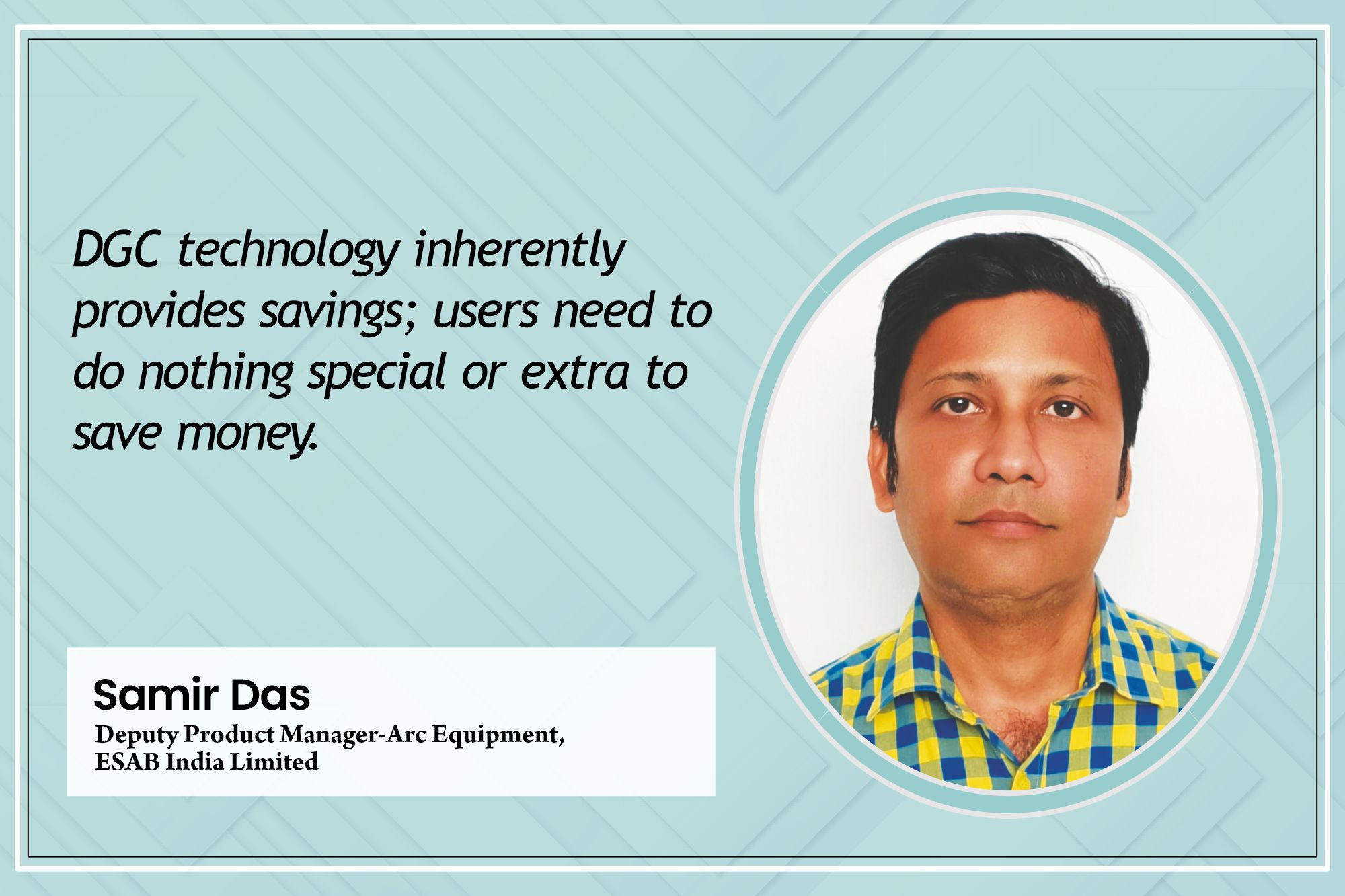
Incorporating Digital Gas Control (DGC) technology into premium wire feeders, like ESAB’s RobustFeed Edge, is a game-changer for fabricators. It cuts shielding gas waste, reduces costs, and eliminates common welding issues like porosity and inconsistent flow, ensuring cleaner, more cost-effective welds.
While shielding gas adds just a few cents to each meter of weld, who wouldn’t want to reduce shielding gas costs by up to 20 percent, or about €1,000 annually per machine? Who wouldn’t want to eliminate the downtime and hassle of swapping cylinders? Most importantly, who wouldn’t want to eliminate the root cause of porosity and the cost associated with weld defects? New digital gas control (DGC) technology is being incorporated in some of today’s premium wire feeders, such as ESAB’s RobustFeed Edge. DGC delivers peace of mind from using each litre of gas following weld procedure specifications. DGC provides precision, confidence, and savings that were not previously possible with flowmeters and standard wire feed units.
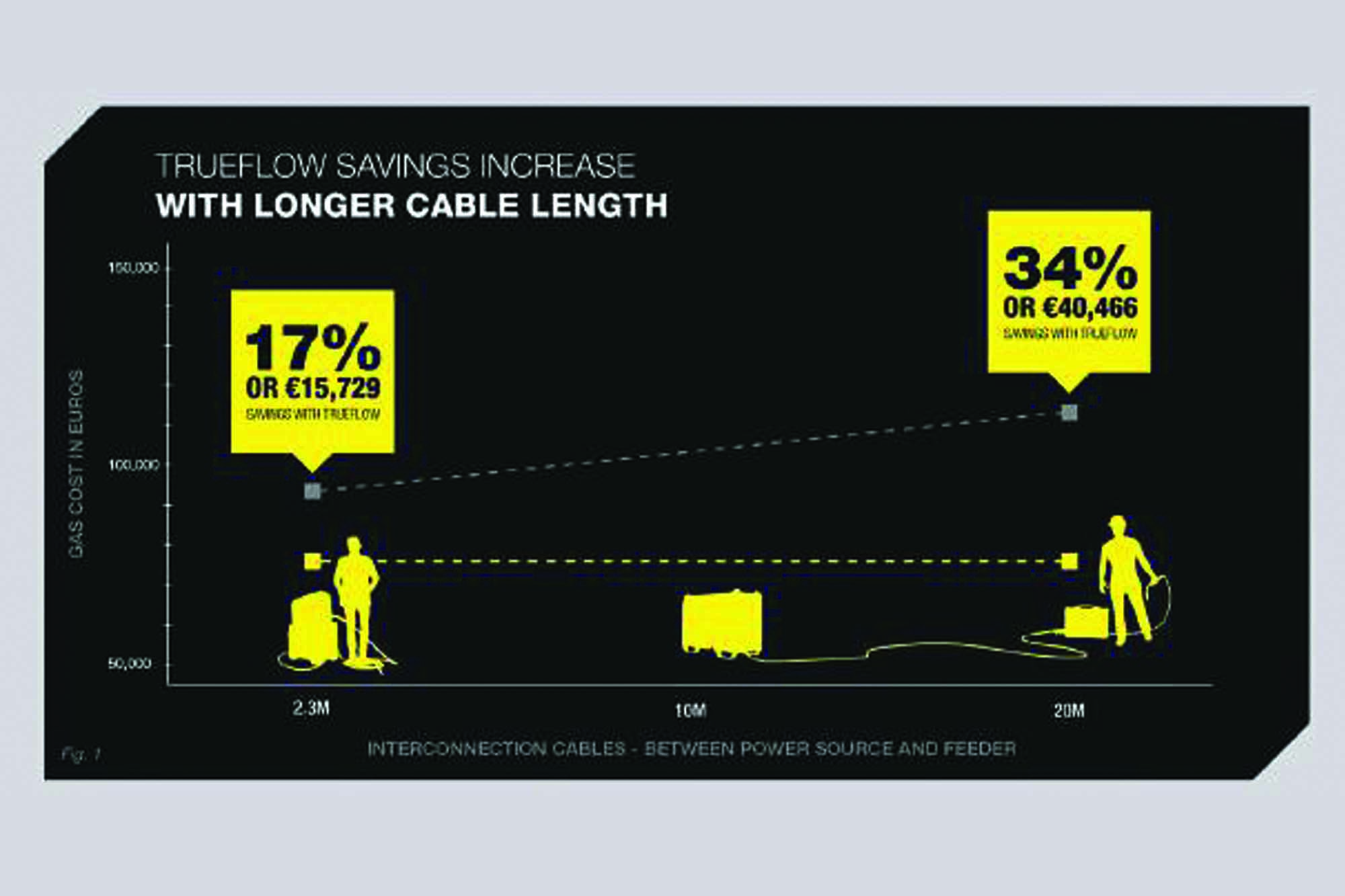
The surge at the arc starts.
To appreciate the benefits of DGC, start with one of the biggest problems it solves: gas surges. That “whooshing” sound at the arc start is the sound of losing money! A standard regulator and wire feeder can waste 1.8 litres per arc start. Conversely, DGC virtually eliminates waste. Further, the volume of over-pressurised gas is proportional to the length of the gas hose, so the DGC savings will be greater with longer interconnect cables (see Fig. 1, which shows the savings possible for a company operating ten welding machines over two shifts).
Hidden quality issues
While wasting gas is annoying, gas surges may also have a hidden cost: porosity at the weld’s start.
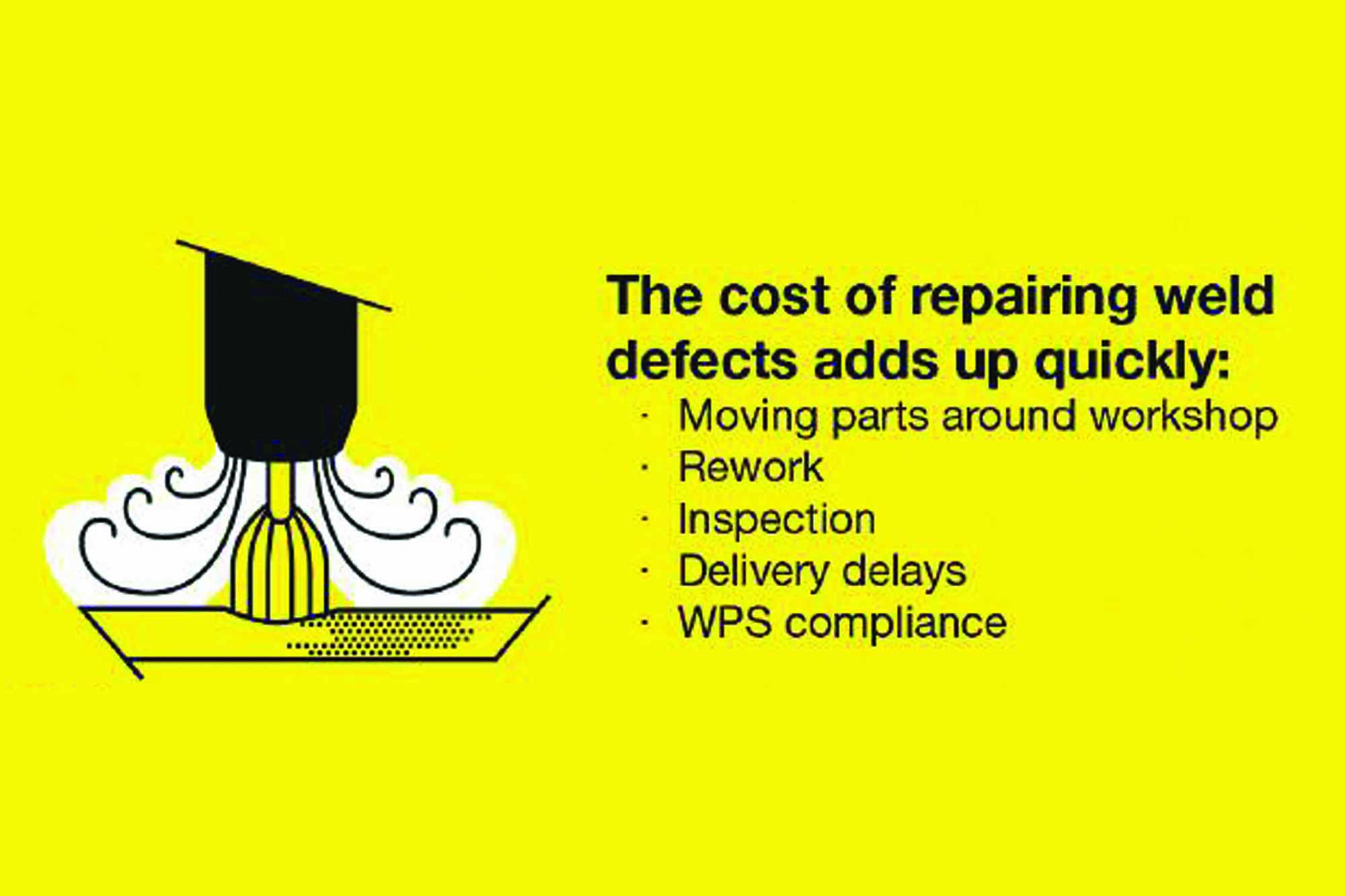
A gas surge during the arc starts creating turbulence that pulls air into the shielding gas flow.
Unfortunately, some operators mistakenly believe insufficient gas flow causes porosity, so they increase flow rates to a point where they compound contamination problems. In addition to porosity at the beginning of the weld, excess gas flow may cause random porosity along the weld seam.
A better design
Feeders with DGC use a proportional flow valve, unlike standard On/Off solenoid valves, enabling variable control. This system incorporates two sensors: a differential pressure sensor to regulate the gas flow rate in litres per minute and an absolute pressure sensor to determine the mass flow rate. Together, they ensure precise and rapid gas flow control, regardless of the gas type. Programmable RobustFeed Edge Quick Jobs buttons allow fabricators to set limits, preventing excessive or insufficient gas usage and leading to significant savings. Digital gas control quickly reaches and maintains the set flow rate, unlike standard systems that overshoot and take longer to stabilise. With shorter cables, it takes 2-3 seconds, and with a 40m cable, it can take up to 10 seconds. DGC also offers benefits like maintaining consistent flow despite low cylinder pressure or gas restrictions, eliminating calibration upon first use, and reducing downtime when changing torches or gas mixes.
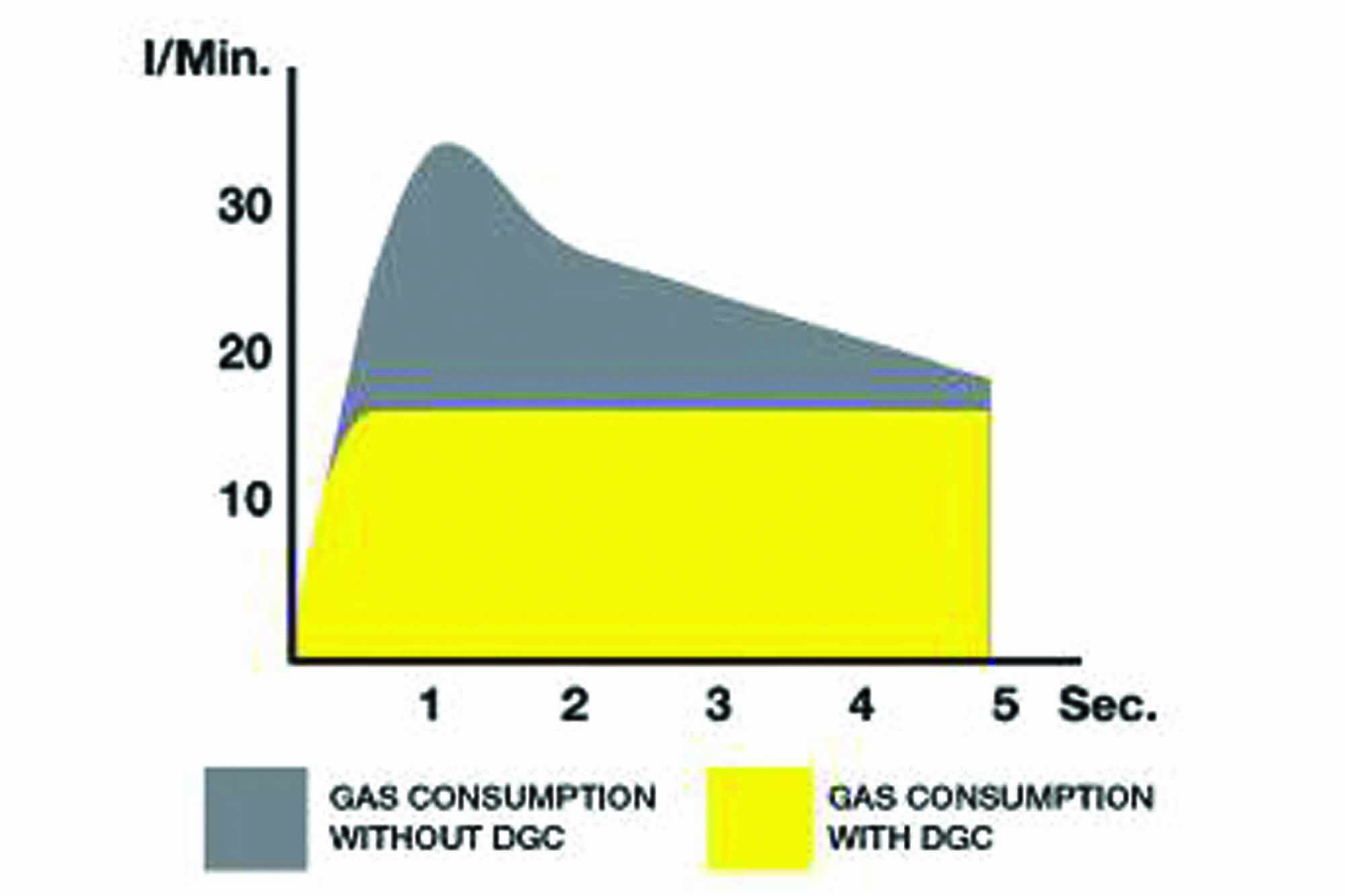
Accuracy made easy
Some systems with DGC set gas flow as part of a synergic line. To begin welding, the operator follows a few simple steps to ensure accuracy: select the wire type, diameter, and gas blend, then set gas flow on digital controls.
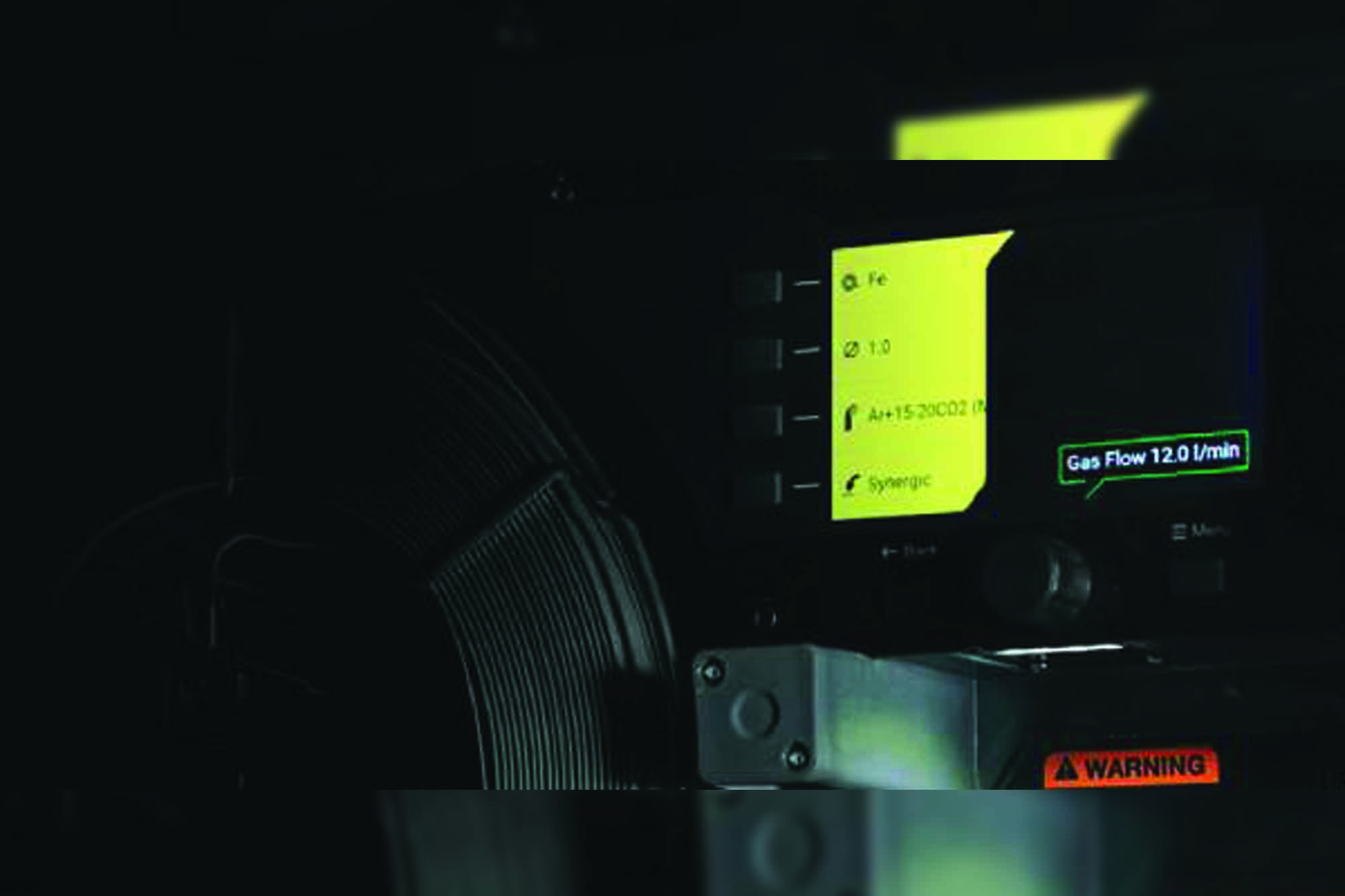
Inherent gas cost savings
DGC technology inherently provides savings. Users need to do nothing special or extra to save money. In addition to eliminating gas waste, DGC can eliminate 20 cylinder changes per station per year in a typical shop. To help fabricators calculate potential savings, ESAB created an online Gas Savings Calculator tool. For example, at a facility with ten welding systems working 16 hours per day, annual gas consumption with a standard system would be 552 cylinders (50 l cylinders) with 2.3 m cables, rising to 697 cylinders with 20 m cables. Conversely, consumption with DGC holds steady at 459 cylinders regardless of cable length, yielding an annual savings that ranges from 93 to 238 cylinders (Fig. 5). Reducing the number of cylinders used also reduces downtime associated with cylinder swap-outs, the possibility of a weld defect when gas runs out in the middle of a seam, spare cylinders in stock and rental charges and delivery frequency.
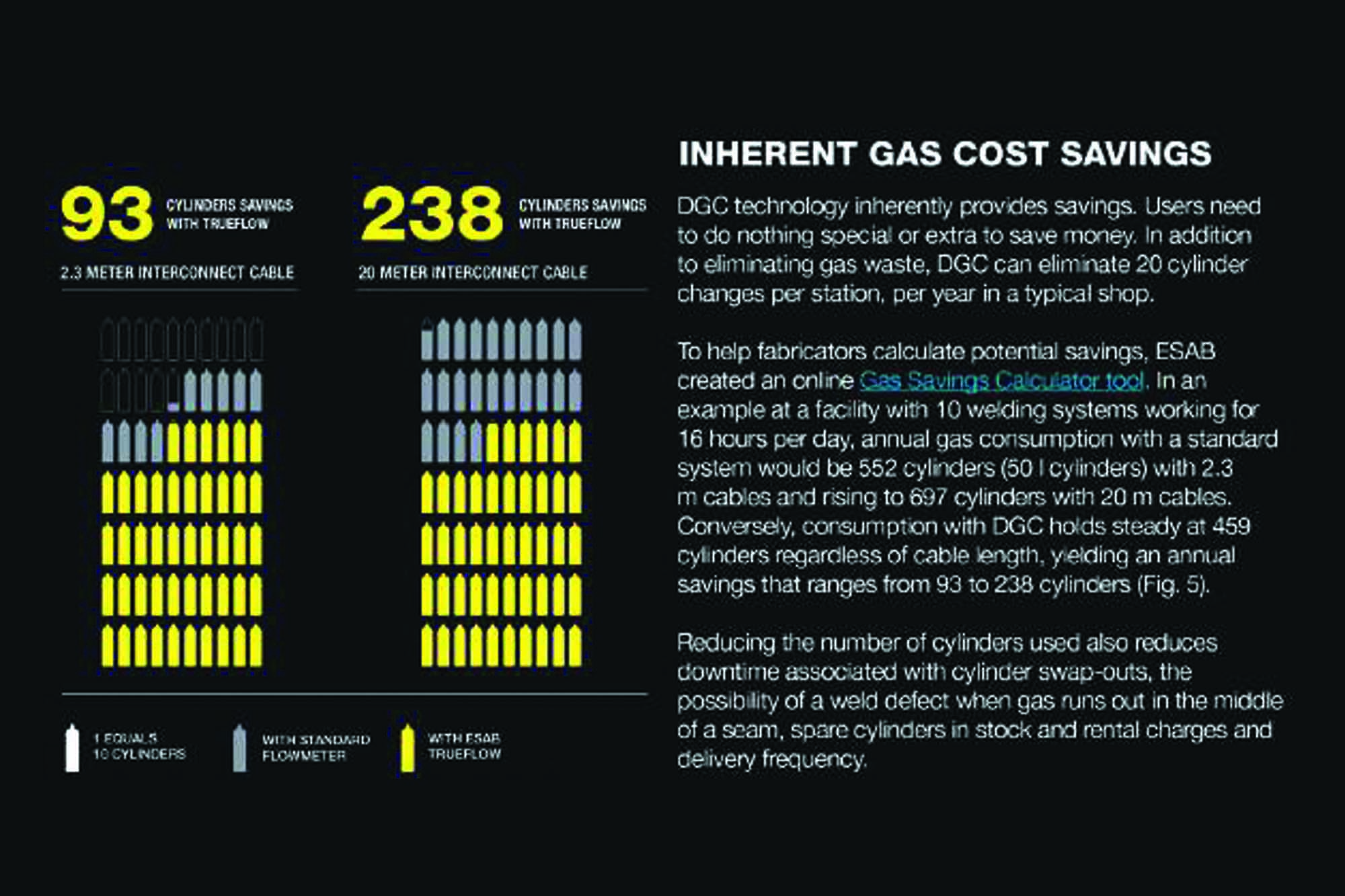
Quality control
DGC also adds protection that is not available with other systems. The system features an adjustable gas pre-flow time for carbon steel, typically set at 0.1 seconds. It quickly checks if the gas flow rate will reach the set value; if not, it prevents the arc from starting and displays an insufficient input pressure error. If the flow deviates significantly for a few seconds, it triggers a controlled weld termination using a programmed sequence like post-flow and crater fill, along with a warning. Sudden pressure loss, such as from a disconnected hose, causes immediate weld termination. The system also detects overpressure (above 7 bar), preventing arc start and displaying an over-pressure error.
Cookie Consent
We use cookies to personalize your experience. By continuing to visit this website you agree to our Terms & Conditions, Privacy Policy and Cookie Policy.