IN THE EYE OF THE TIGer
By Edit Team | March 15, 2018 12:07 pm SHARE
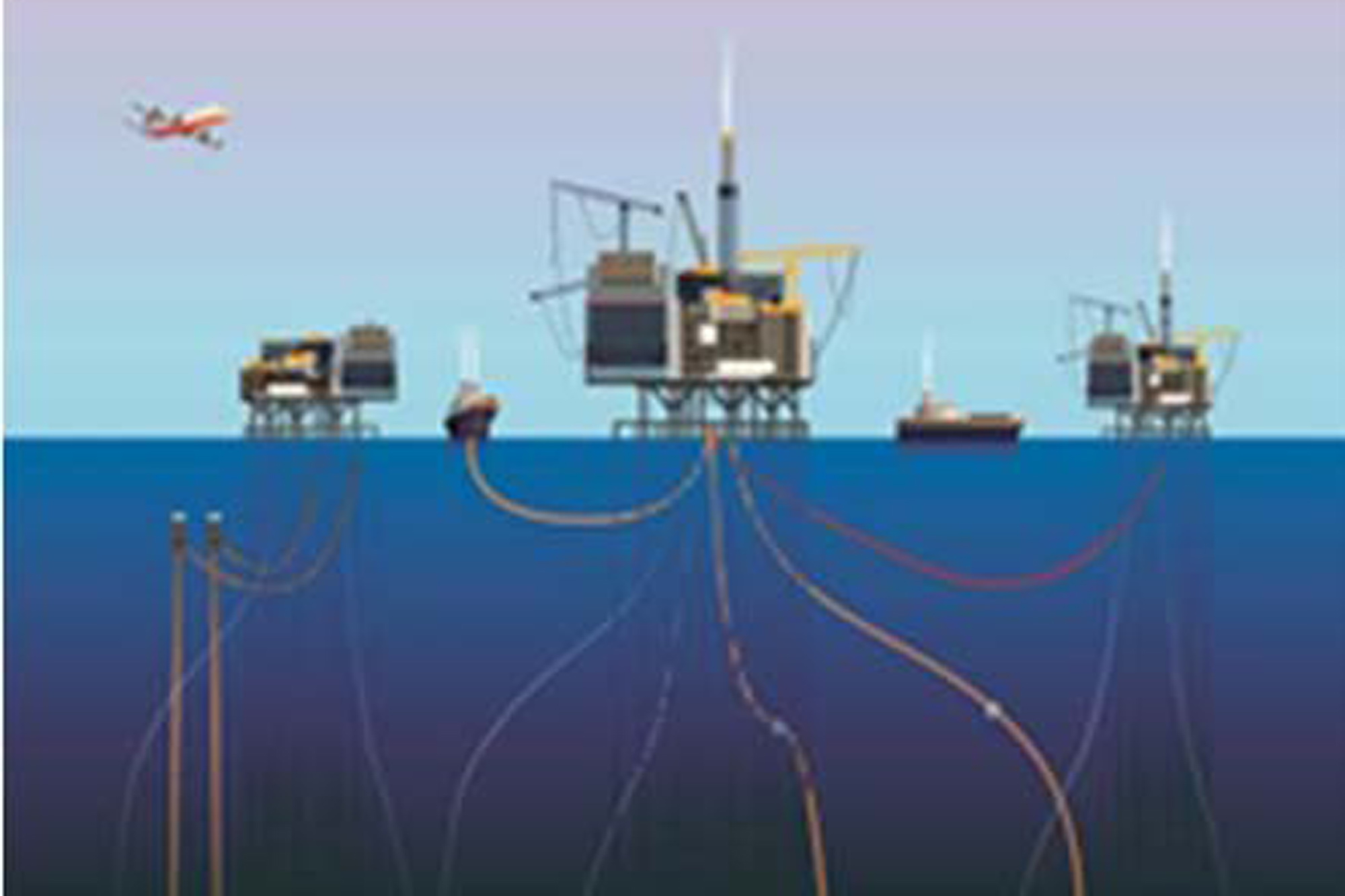
TIGer-weld overlay cladding of advanced metallurgical quality
The safe production and transport of oil and gas is highly dependent on reliable pipelines. There are several million miles of onshore and offshore pipelines currently in use worldwide.
Offshore pipelines and their constraints
Production lines are used to transport production fluids from subsea wells and manifolds to offshore processing facilities, loading buoys, and S2B (subsea to beach). These production fluids are still unprocessed and are usually composed of hydrocarbons from gas and condensates, crude oil, water and solid impurities in varying proportions. Where the pipes close to connect with the subsea wells, the pipes often have to carry crude oil which is of a very high pressure and temperature.
Export lines (or pipelines) are used to convey gas or oil after its separation from the other products found in production fluids. The operating environment of pipelines is moderate when compared to the environment within which production lines have to work. The conveyed fluid is the same temperature as the surrounding water and the pressure is low to medium. Therefore, it is essential that the basic material chosen for an offshore pipeline is collapse resistant.
Whilst design regulations for pipelines are less stringent than those for production lines, there is a growing demand for higher quality pipelines due to the immense environmental damage which leaks or failures of tubular structures can cause.
Due to the declining productivity of existing wells, operators are forced to extend their exploration activities into deeper offshore waters. Consequently, ever more production lines, with improved mechanical strength, will be necessary.
The subsea tieback system is the preferred solution, where possible. This involves the production lines of recently completed wells being connected to existing installations. This is a good way to overcome the ever more significant offset between production facilities and related wells. It can help to reduce costs considerably. Reel-laying of pipes is a fast and cost-effective way to establish the necessary connections. The additional strain caused by the laying procedure can only be absorbed by pipes of an adequate quality.
Another major concern is making sure that production lines are corrosion resistant. If the concentration of chloride, carbon dioxide or sulphur ions exceeds a certain level, the high strength low alloy C-Mn steel can corrode at a rate of about 0.2mm per year. Corrosion Resistant Alloys (CRA) such as austenitic and martensitic stainless steel and nickel-base and titanium-base alloys can withstand the strain of the corrosive chemicals.
Corrosion resistant alloy clad pipe
To combine the strength of low-alloyed Carbon steel with the corrosion resistance of CRAs, the inside of C-Mn steel pipes is covered with a layer of a suitable corrosion resistant alloy. Excellent bonding between the parent metal of the outer pipe and the deposited layer inside can be achieved if overlay cladding is applied. CRA clad steel pipes are characterised by the firm metallurgical bond between the host pipe and the inner CRA layer. It meets the highest quality standards.
The TIG weld overlay cladding process is becoming ever more popular for the manufacturing of CRA clad steel pipes. It is known for providing a smooth and regular surface with only small variations in thickness. The layer has “zero defects”, no pores, no lack of fusion and particularly low dilution rates.
Conventional GTAW/ TIG welding (Tungsten Inert Gas) is characterised by the creation of an electric arc between a refractory metal (alloyed tungsten) electrode and the workpiece in an atmosphere filled with inert gas. The electrode withstands the high temperature of the arc and directs it towards the fusion zone. The impact of the electrons causes the fusion of the parent metal, forming the weld pool which is shielded by the inert gas flow. In the case of cold-wire TIG cladding the energy required to melt the added wire comes from the electric arc, so the melting rates that can be achieved are quite limited. In case of the Hot Wire TIG process, the wire is preheated by the Joule effect of a separate current which is provided by an additional power source. Hot Wire TIG cladding allows increased melting rates and advanced productivity without compromising the reliability of the process or the quality of the deposited layers.
Using the TIGer technology to clad pipes
The process of TIG welding (particularly TIG Hot Wire cladding applications) has been made yet more efficient thanks to a recent development, known as TIGer technology. It is based on a new torch design. Whilst a common TIG torch has one single tungsten electrode, the distinct TIGer torch is equipped with two electrodes. Each electrode is supplied with current by its own power source. The position of the electrodes (with the tips next to each other) means that a single bi-cathodic arc is generated.
The low arc pressure of the TIGer arc, combined with high welding intensity allows extremely fast welding speeds to be reached (over 1000mm/min). Furthermore, high deposition rates of 6 kg/h or more per TIGer torch can be achieved, with only a low dilution rate between the deposited alloy and the substrate material. The dilution rates are less than 10 per cent for the first layer and 2 per cent for each of the following layers. If only one layer is deposited, it is possible to adjust the welding parameters to limit the dilution at 6 per cent.
It is possible to optimise the thickness of each layer to within a range of 1 to 3 mm, this meets all known codes and standards. Consequently, only the exact quantity of corrosion resistant alloy material need be added, which creates significant cost savings, considering the cost of CRA filler products.
Suitable cladding equipment for the TIGer technology
Optimised industrial TWIN TIGer (double torch) solutions are available for the internal cladding of C-Mn steel pipes with an inner diameter of minimum 5-inch and standard lengths of 6- or 12-metre.
The pipe which is going to be cladded in a horizontal position (1G) is carried by several pipe supports. The rotary motion of the pipe is generated by a hollow shaft rotator, which is mounted in the vertical position and is adjustable to the appropriate workpiece diameter.
The technical challenge for such equipment is to guide the torches precisely and reliably through the inside of the pipe (despite its small ID and the high temperatures, which is the result of the cladding operation itself).
The system is based on a 12-metre long frame with two horizontally aligned steel ropes, carrying the welding lance, the two ropes are passed through the pipe to be cladded and tightened with strong forces.
Two TIGer torches with Hot Wire supply are mounted, one behind the other on the welding lance. The lance itself slides along the ropes. The cladding sequence starts at the rear end of the pipe.
During the cladding operation, the lance is pulled through the pipe, thus creating the longitudinal movement of the torches. The two torches rotate in the shape of a helix along the inside and are able to cover the whole internal surface area. The requested deposition of two weld layers can be created by one single movement along the pipe (TWIN TIGer torch).
Two synchronised Polysoude PC 600-3 Hot Wire TIGer power sources automatically control the longitudinal movement of the lance, the rotation of the pipe and the intrinsic displacement of the torches each with intendant Arc Voltage Control. Except for the welding speed, all welding parameters of each TIGer torch can be adjusted independently, so the dilution of each CRA layer can be minimised and the specified thickness of the deposition will be followed exactly.
As the sequence of a cladding operation is entirely controlled by the equipment, there is no need for an operator to intervene. The TIGer torches are fitted with integrated high-resolution colour cameras, so the process can be followed on video monitors. For quality assurance, all important cladding parameters are continuously monitored and recorded by the data acquisition system.
Conclusion
TIGer overlay cladding technology is an advantageous way to satisfy the increasing demand for metallurgical bond CRA clad steel pipe. It is of a suitable quality for production lines and the crude oil exploration. 100 per cent defect-free CRA depositions, reasonable investments, increased efficiency and high flexibility are the reasons why companies have chosen and are successfully using Polysoude’s unique cladding technology in their production processes.
For more details, visit www.polysoude.com
Cookie Consent
We use cookies to personalize your experience. By continuing to visit this website you agree to our Terms & Conditions, Privacy Policy and Cookie Policy.